TECHNOLOGY
Laser Cutting vs. Traditional Methods: 6 Reasons to Make the Switch
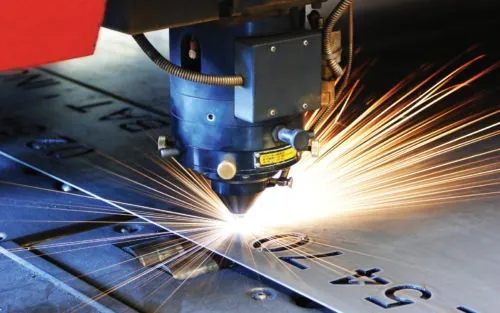
Introduction
As manufacturing evolves, the debate between laser cutting and traditional cutting methods continues. While traditional tools like saws and knives have their place, laser cutting offers compelling advantages that make it a superior choice for many applications. This article will explore six key reasons why making the switch to laser cutting is beneficial.
1. Precision and Accuracy
Traditional Methods: Conventional cutting tools often struggle with precision, especially when dealing with complex shapes or fine details. The accuracy of cuts can be inconsistent, leading to potential errors and material waste.
Laser Cutting: The laser cutter excels in precision, offering accuracy down to +/- 0.1 mm. This level of precision allows for the creation of intricate designs with minimal errors, making it ideal for industries requiring high accuracy.
2. Versatility in Materials
Traditional Methods: Traditional cutting tools are often limited in the types of materials they can handle. For example, certain metals or composite materials may require specific tools, limiting flexibility.
Laser Cutting: Laser cutters are incredibly versatile, capable of cutting a wide range of materials including metals, plastics, wood, and textiles. This versatility allows manufacturers to work with multiple materials using a single machine, streamlining the production process.
3. Speed and Efficiency
Traditional Methods: Conventional cutting processes can be time-consuming, often requiring multiple steps and manual adjustments. This slows down production and increases labor costs.
Laser Cutting: The laser engraver operates at a high speed and can be fully automated, drastically reducing production times. The ability to quickly switch between different tasks without the need for tool changes further enhances efficiency.
4. Minimal Material Waste
Traditional Methods: The lack of precision in traditional cutting methods often leads to material waste, which can be costly over time. In addition, the wear and tear on tools can affect cut quality.
Laser Cutting: With laser cutting, the high precision of the cuts minimizes material waste. The process also reduces the need for secondary finishing, further conserving materials and reducing overall costs.
5. Cost-Effectiveness
Traditional Methods: Traditional cutting methods can be labor-intensive and inefficient, leading to higher operational costs. The need for regular maintenance and replacement of tools also adds to the expense.
Laser Cutting: Despite the initial investment, laser cutting proves to be more cost-effective in the long run. The efficiency, precision, and reduced labor requirements translate to lower operational costs and a faster return on investment.
6. Environmental Impact
Traditional Methods: Conventional cutting methods often involve significant energy consumption and generate a considerable amount of waste, contributing to environmental concerns.
Laser Cutting: Laser cutting is an environmentally friendly option, consuming less energy and producing less waste. The precision of laser cuts also means fewer rejected parts and less material waste, aligning with sustainable manufacturing practices.
Conclusion
Switching from traditional cutting methods to laser cutting offers numerous advantages, from enhanced precision and material versatility to greater cost-effectiveness and environmental benefits. For businesses looking to improve their manufacturing processes, laser cutting is a compelling option worth considering.
TECHNOLOGY
Fixing the Spankbang Origin DNS Error
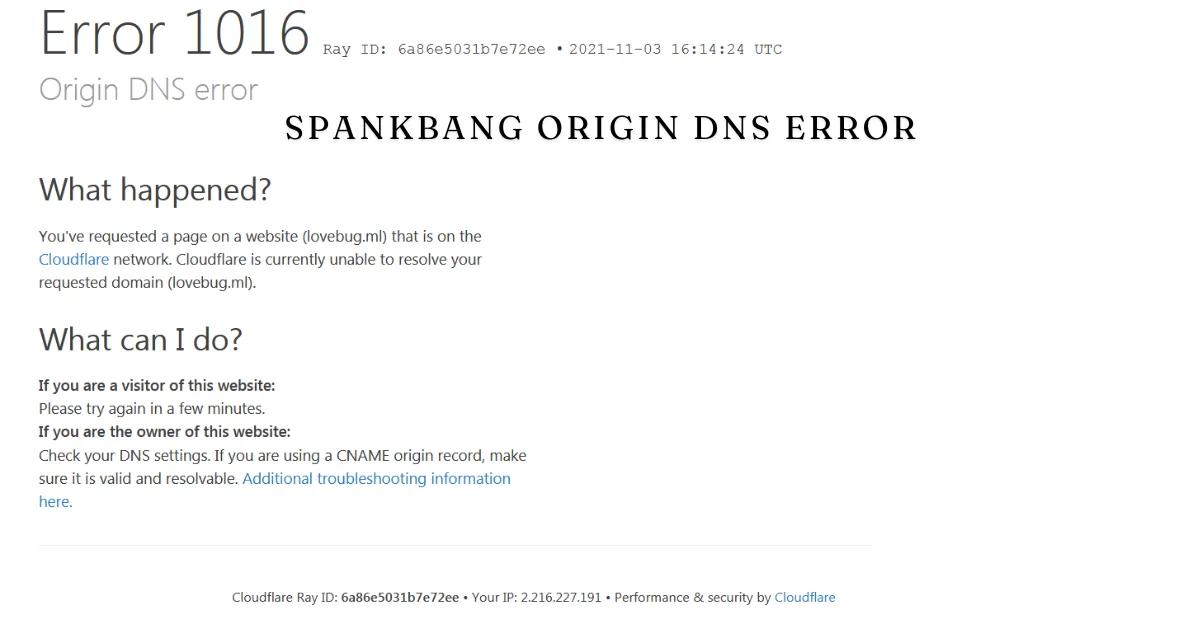
Introduction to spankbang origin dns error
Are you tired of running into the Spankbang Origin DNS error? If you’ve found yourself frustrated while trying to access your favorite content on Spankbang, you’re not alone. This pesky error can put a serious damper on your browsing experience. But don’t worry—understanding this issue is the first step towards fixing it. Let’s dive into what causes the Spankbang Origin DNS error and explore practical solutions to get you back online in no time!
Understanding the Spankbang Origin DNS Error
The Spankbang Origin DNS error can be frustrating for users trying to access the site. It typically occurs when the domain name system fails to resolve the website’s address, preventing your browser from locating it.
When you type in a URL, your device needs a reliable connection to translate that web address into an IP address. If there’s any disruption or misconfiguration in this process, you’ll encounter the dreaded DNS error.
This issue may arise from various sources, such as problems with your internet service provider or incorrect settings on your local device. In some cases, it could even be due to server-side issues with Spankbang itself.
Understanding this error is essential for troubleshooting effectively. Knowing what triggers it will help you take appropriate steps toward resolution and regain access quickly without unnecessary hassle.
Causes of the Error
Several factors can lead to the Spankbang origin DNS error. One common cause is an issue with your internet connection. If your network is unstable, it might disrupt the ability to resolve domain names.
Another potential culprit is incorrect DNS server settings on your device. Using outdated or unreliable DNS servers can prevent you from accessing certain websites, including Spankbang.
Browser-related problems also play a significant role. Cached data and cookies may become corrupted over time, leading to unexpected errors during browsing sessions.
Sometimes the problem lies with the website itself. Server outages or maintenance activities on Spankbang’s end can trigger this error as well. Identifying these causes helps in troubleshooting effectively and restoring access quickly.
Troubleshooting Steps for the Spankbang Origin DNS Error
If you encounter the Spankbang origin DNS error, don’t panic. There are several straightforward steps to resolve it.
First, check your internet connection. A weak or unstable network can lead to such errors. Try restarting your router for a quick refresh.
Next, clear your browser cache and cookies. Over time, stored data can cause conflicts with website loading.
Consider changing your DNS settings as well. Switching to Google’s Public DNS (8.8.8.8 and 8.8.4.4) often resolves these issues effectively.
Additionally, disabling any active VPNs or proxies may help since they sometimes interfere with site access.
Try accessing the site using a different browser or device to rule out specific software problems on your current setup. Each step brings you closer to enjoying uninterrupted browsing on Spankbang.
Alternative Methods to Access Spankbang
If you’re facing the spankbang origin dns error, alternative access methods can provide relief. One of the simplest solutions is to use a VPN. This tool not only masks your IP address but also helps bypass geographical restrictions.
Another option is using a proxy server. By routing your connection through a different server, you might avoid DNS-related issues entirely.
If these options don’t suit you, consider accessing Spankbang via its mobile app. Often, apps have fewer issues compared to web browsers.
Try using different web browsers or clearing your current browser’s cache and cookies before reconnecting to the site. These small tweaks may just lead you back to enjoying your favorite content without interruptions.
Preventing Future Occurrences of the Error
To prevent the Spankbang origin DNS error from reoccurring, start by keeping your browser updated. Regular updates often include fixes for bugs that might lead to such issues.
Consider using a reliable DNS provider. Services like Google Public DNS or Cloudflare can enhance browsing stability and speed. Changing your DNS settings is typically straightforward and can yield significant benefits.
Clearing your cache regularly also helps in maintaining smooth access to sites like Spankbang. A cluttered cache may cause outdated information to interfere with website loading.
Additionally, employ a VPN service if you encounter frequent connectivity problems. A VPN not only secures your connection but can help bypass regional restrictions that sometimes trigger DNS errors.
Ensure your internet connection remains stable. Periodic drops can lead to frustrating issues, including the dreaded error message popping up when you least expect it.
Importance of Fixing the Error for Smooth Browsing Experience
Addressing the Spankbang origin DNS error is crucial for maintaining a seamless browsing experience. When this issue arises, it can disrupt your access to content that you enjoy or need.
A smooth connection ensures that you spend less time troubleshooting and more time indulging in your favorite videos. Frustration mounts when errors prevent quick access, so resolving these issues promptly enhances user satisfaction.
Moreover, fixing this error prevents potential security risks associated with unreliable connections. Staying connected securely allows users to browse without worrying about data leaks or exposure to harmful sites.
Keeping your network settings in check also contributes positively to overall internet performance. A reliable connection means faster load times and uninterrupted streaming—an essential aspect of modern online entertainment.
Conclusion
Experiencing the spankbang origin dns error can be frustrating. It disrupts your access to content you enjoy and can leave you feeling stuck. By understanding what causes this issue, you’re better equipped to address it effectively.
Taking the proper troubleshooting steps is essential for resolving the DNS error efficiently. Whether it’s flushing your DNS cache or adjusting network settings, these solutions are practical and straightforward.
If all else fails, alternative methods such as using a VPN or trying different browsers offer additional avenues to explore Spankbang without hindrance. These options ensure that your experience remains uninterrupted.
Preventing future occurrences of this error is also crucial. Regularly updating your browser and maintaining an optimal internet connection help keep issues at bay.
A smooth browsing experience significantly enhances enjoyment while accessing websites like Spankbang. Fixing errors promptly leads to fewer disruptions and more consistent access to content you love.
With these insights in mind, navigating around the spankbang origin dns error becomes much easier, allowing for a seamless online journey.
ALSO READ: someboringsite.com: A Purely Simple Experience
FAQs
What is “spankbang origin dns error”?
The “spankbang origin DNS error” is a connection issue where your browser can’t resolve Spankbang’s domain name, preventing access to the site. It’s usually caused by DNS misconfigurations, server outages, or internet connectivity problems.
How can I fix the Spankbang DNS error quickly?
Start by restarting your router and clearing your browser’s cache. If that doesn’t work, try switching to Google DNS (8.8.8.8) or Cloudflare DNS (1.1.1.1).
Does using a VPN solve the Spankbang DNS error?
Yes, a VPN often bypasses DNS errors by routing your connection through a different server, especially if the issue is related to regional blocks or ISP restrictions.
Can browser settings trigger the DNS error on Spankbang?
Absolutely. Outdated browsers, corrupted cache, or incompatible extensions can all contribute to DNS resolution issues when trying to access Spankbang.
Is there a way to prevent the DNS error from happening again?
Regularly update your browser, use a stable DNS service, and maintain a strong internet connection. These steps help minimize future DNS-related disruptions.
TECHNOLOGY
Why Concierge-Level Support in Virtual Data Rooms Matters for High-Stakes Transactions
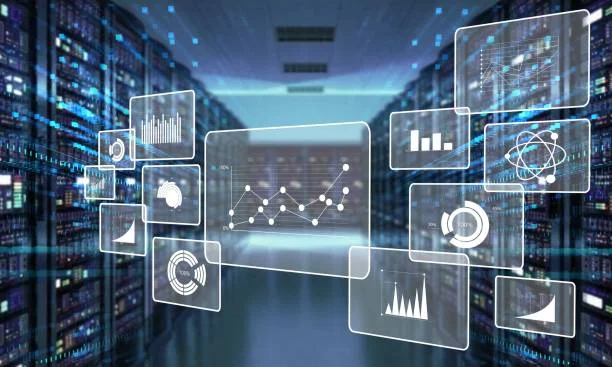
Whether navigating a complex merger, launching a capital raise with multiple LPs, or managing a cross-border acquisition, the outcome often depends on how well the execution is managed. In time-sensitive deals, delays can cost more than just money—they can erode trust, derail momentum, and put the entire transaction at risk for Concierge-Level Support.
That’s why more dealmakers are turning to virtual data room (VDR) platforms that offer not just speed and security, but also enterprise-level concierge support. This white-glove service extends beyond traditional tech support, giving deal teams access to dedicated experts who help set up, configure, and manage VDR workspaces with precision.
What Is Enterprise Concierge Support in a VDR?
Concierge support goes far beyond responding to service tickets. It’s about having a hands-on team available to assist with all aspects of your data room, including:
- Workspace setup and onboarding
- File uploads, conversions, and folder structure organization
- User and permission management
- Security configuration and compliance guidance
- Q&A workflows and approval hierarchies
- Customized training for internal and external stakeholders
For high-value, high-complexity transactions, concierge support provides the infrastructure and expertise required to move fast without sacrificing accuracy or control.
Why Basic Support Isn’t Enough for Enterprise Deals
In large transactions, multiple stakeholders need access at different levels—legal teams, analysts, auditors, investors, and compliance officers. Each participant has unique requirements and permissions. Coordinating that complexity with a slow support desk or self-service tools is a recipe for confusion.
Many VDR providers still rely on:
- Email-only support queues
- Business-hours-only availability
- Limited onboarding help
- Little to no experience with regulated or sensitive transactions
By contrast, concierge-level VDR services offer real-time responsiveness and strategic guidance to ensure your workspace is optimized for speed and precision.
How Concierge Support Enhances the Deal Lifecycle
Here’s how expert VDR support directly improves outcomes at every stage of the transaction process:
1. Rapid Launch with Reduced Risk
A strong start can make all the difference. Instead of spending days or weeks configuring a workspace, concierge teams can handle setup on your behalf:
- Custom folder structures built to match your workflow
- Pre-assigned permission tiers for each stakeholder group
- Bulk file uploading and document import support
This gets your data room live quickly and minimizes the chance of permission errors that could expose confidential documents to the wrong eyes.
2. On-Demand Help When It Matters Most
During the peak of diligence, deal teams can’t afford to wait for answers. Whether it’s resolving an access issue, tagging documents for review, or troubleshooting file visibility, real-time support ensures your progress doesn’t stall.
Concierge support includes:
- Live response via phone or email
- Specialists trained in private equity, M&A, and cross-border deal complexity
- 24/7 availability when transactions require round-the-clock attention
When critical moments arise, immediate solutions can be the difference between closing and losing a deal.
3. Elevated Stakeholder Experience
For many investors and buyers, your data room is their first impression of your organization. A smooth, intuitive interface—and quick access to the right documents—speaks volumes about your professionalism.
With concierge support:
- Stakeholders are guided through onboarding
- Access challenges are handled proactively
- Corporate branding can be applied for a seamless experience
- FAQ and navigation aids can be built in to reduce confusion
These touches improve trust and help keep participants focused on the deal, not the platform.
4. Support for Security and Regulatory Compliance
Complex transactions often involve regulated data—financial disclosures, personal information, health records, and more. Maintaining compliance with data protection laws (like GDPR or HIPAA) is non-negotiable.
Concierge support teams can help:
- Configure user permissions aligned with compliance best practices
- Set up audit trails and activity tracking
- Apply security settings like dynamic watermarking and access expiration
This reduces the risk of non-compliance and ensures sensitive data stays protected throughout the deal.
Measurable ROI From Expert VDR Support
Concierge-level support isn’t just a value-add—it can directly impact the speed and success of your transaction. Benefits include:
- Faster onboarding and setup
- Fewer technical errors or stakeholder complaints
- Higher investor or acquirer engagement
- Smoother close processes and better buyer experiences
- Greater confidence in compliance and document control
Every saved hour, reduced error, or avoided delay compounds over the life of a high-value deal.
What Sets Leading Concierge Support Apart
Not all VDR support is created equal. The most effective concierge services provide:
- Dedicated account managers with experience in your industry
- Tailored onboarding for each new workspace
- Proactive assistance during critical transaction stages
- Integrated guidance on permissions, structure, and legal compliance
- Rapid-response help desks staffed by professionals—not generic agents
This type of support is designed for speed, accuracy, and reliability—exactly what’s required in the pressure-filled environment of modern dealmaking.
The Case for Concierge VDR Support in Strategic Transactions
When deals involve multiple parties, sensitive data, and tight timelines, execution matters more than ever. A virtual data room with concierge support provides the tools and expertise to move faster, collaborate more effectively, and protect your most valuable information at every stage.
From quick setup to ongoing assistance and compliance peace of mind, enterprise concierge support can transform a standard data room into a fully managed, strategic advantage.
Explore the featured posts and gain top strategies to enhance your business today.
TECHNOLOGY
Cursed-Memes.com Technology: Impact on Digital Culture
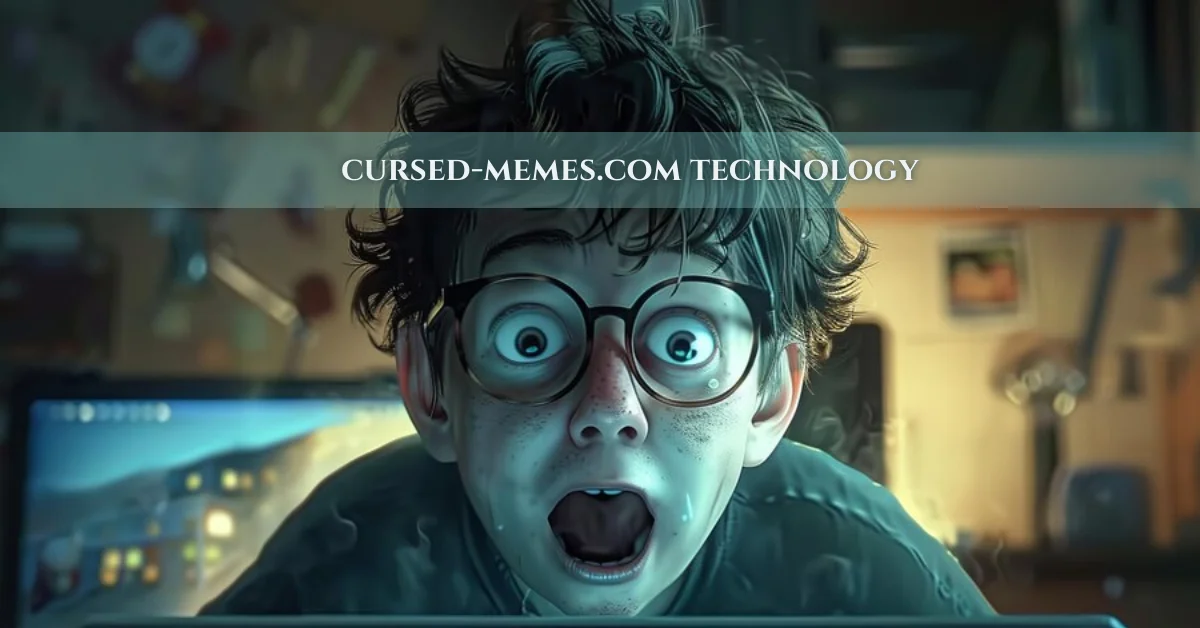
Introduction to cursed-memes.com technology
Welcome to the wild world of internet memes, where humor and absurdity collide! One platform that’s taken this phenomenon to new heights is cursed-memes.com technology. This innovative approach has transformed how we engage with digital culture, pushing boundaries and reshaping our online experiences. Memes have become more than just fleeting images; they’re now powerful tools for communication, social commentary, and entertainment. As we dive into the realm of cursed memes, you’ll discover what sets them apart from their traditional counterparts and explore their far-reaching impact on popular culture. Buckle up—it’s going to be an enlightening ride through the meme-verse!
The Rise of Memes in Digital Culture
Memes have transformed the landscape of digital culture. They serve as a universal language, bridging gaps between diverse communities.
Originating from simple images with text, memes quickly evolved into intricate forms of expression. Social media platforms fueled their rapid spread, allowing anyone to create and share. As a result, memes became an integral part of online communication.
The rise of internet humor has changed how we engage with content. Memes often reflect societal trends and cultural references in real-time—making them both timely and relatable.
With their ability to provoke thought or laughter, they capture fleeting moments in our collective consciousness. This phenomenon showcases creativity while fostering connections among users worldwide.
In today’s digital arena, memes are more than just entertainment; they’re statements that resonate deeply within various subcultures.
How Cursed-Memes.com is Different from Traditional Memes?
Cursed-memes.com technology takes meme creation to a whole new level. Unlike traditional memes that often rely on humor or relatable content, cursed memes dive into the bizarre and absurd.
These digital artifacts often incorporate distorted visuals and dark humor. They challenge our understanding of what’s funny by blending surreal elements with unexpected contexts. This creates a unique experience for viewers who find joy in decoding the madness.
The format encourages creativity, inviting users to remix existing images in unconventional ways. Traditional memes typically follow established formats; cursed memes thrive on breaking those molds.
Moreover, the community surrounding cursed-memes.com embraces an ironic detachment from mainstream culture. This fosters a space where niche interests can flourish without boundaries, setting it apart from conventional meme platforms that cater to broader audiences.
ALSO READ: lotterygamedevelopers.com: Create Your Dream Lottery Game
The Impact of Cursed-Memes.com on Popular Culture
Cursed-memes.com technology has shifted the landscape of popular culture dramatically. It introduces a new layer of humor that combines absurdity with relatable experiences. This unique blend captivates audiences, drawing them into an alternate reality where nothing is off-limits.
Social media platforms buzz with these cursed memes, often going viral overnight. They capture moments and emotions in ways traditional formats cannot achieve. The surreal nature creates shared laughter and confusion among users.
Moreover, brands have started to tap into this phenomenon. Marketing strategies now incorporate elements of cursed memes to resonate with younger audiences who appreciate unconventional humor.
As creators push boundaries, the cultural dialogue evolves too. Cursed memes challenge societal norms while encouraging creativity in expression—something that’s becoming increasingly valuable in today’s digital age.
Controversies Surrounding cursed-memes.com technology
Cursed-memes.com technology has sparked significant debate in online communities. Critics argue that its content often crosses the line into inappropriate or offensive territory. The edgy nature of cursed memes can lead to misunderstandings, especially for those unfamiliar with meme culture.
Some believe these memes perpetuate negativity and desensitize users to serious issues. They worry about the potential harm to mental health, particularly among younger audiences who may struggle to differentiate satire from reality.
On the other hand, advocates defend cursed-memes.com as a creative outlet. They contend it allows individuals to process dark humor during tough times. This dichotomy creates an ongoing conversation about boundaries in digital expression.
Additionally, copyright concerns have emerged as creators navigate ownership within this chaotic landscape of remixed media. Artists often find their work repurposed without credit, igniting disputes over intellectual property rights in an ever-evolving meme ecosystem.
ALSO READ: Pikruos: Your Partner in Business Technology Solutions
Future of Cursed-Memes.com and the Evolution of Memes
The future of cursed-memes.com technology is poised to shape the next wave of digital expression. As meme culture continues to evolve, we can expect even more bizarre and unpredictable content.
Emerging technologies like artificial intelligence will play a significant role in this transformation. AI can generate memes at an unprecedented scale, pushing boundaries that challenge traditional humor.
Social media platforms are also adapting. They’re integrating algorithms that prioritize unique and edgy content, making cursed memes more visible than ever before.
As creators experiment with new formats—think video loops or interactive elements—the line between consumed content and creator will blur further.
The interconnectedness of global cultures online ensures that these cursed creations will resonate worldwide, sparking conversations around shared experiences infused with dark humor. This evolution promises not just entertainment but a deeper commentary on modern life itself.
Conclusion: Embracing the cursed-memes.com technology Phenomenon
The rise of cursed-memes.com technology marks a significant shift in how we interact with digital content. This platform has opened up new avenues for creativity, allowing users to explore humor that pushes boundaries and challenges societal norms. As memes continue to evolve, those rooted in the concept of “cursedness” invite us to reflect on our collective experiences and reactions.
Cursed memes have created their own niche within the digital culture landscape. They not only entertain but also provoke thought and discussion about what is acceptable in humor today. With this unique blend of absurdity and relatability, cursed-memes.com stands out as a beacon for those who enjoy the unconventional.
As we move forward, it’s clear that platforms like cursed-memes.com will shape future trends in meme culture. Whether you love them or hate them, these memes are here to stay. Embracing this phenomenon can lead to richer conversations about art, expression, and even societal issues through the lens of humor.
Engaging with cursed-memes.com technology invites everyone into a broader dialogue about creativity online—one filled with unexpected twists and endless possibilities. The journey into this peculiar world promises excitement for both creators and consumers alike.
ALSO READ: Emometre: Decoding Human Emotions
FAQs
What is “cursed-memes.com technology”?
Cursed-memes.com technology refers to an innovative approach to meme creation that emphasizes absurdity and dark humor, transforming traditional memes into unique digital expressions that challenge societal norms.
How do cursed memes differ from traditional memes?
Cursed memes utilize bizarre visuals and surreal humor, often breaking established formats and pushing creative boundaries, unlike traditional memes that usually rely on relatable content.
What impact have cursed memes had on popular culture?
Cursed memes have reshaped online humor and communication, going viral on social media, influencing marketing strategies, and fostering new dialogues around creativity and societal norms.
Are there any controversies surrounding cursed-memes.com technology?
Yes, critics argue that cursed memes can be offensive or inappropriate, while advocates see them as creative outlets that allow individuals to cope with darker themes, sparking debates about humor boundaries.
What does the future hold for cursed-memes.com technology?
The future of cursed-memes.com technology is likely to feature more bizarre content driven by emerging technologies like AI, alongside evolving social media algorithms that prioritize edgy and unique expressions.
- GENERAL1 month ago
5 Factors That Affect Tattoo Removal Success
- ENTERTAINMENT2 months ago
Exploring the Kristen Archives: A Treasure Trove of Erotica and More
- LIFESTYLE6 months ago
The Disciplinary Wives Club: Spanking for Love, Not Punishment
- TECHNOLOGY6 months ago
Blog Arcy Art: Where Architecture Meets Art
- ENTERTAINMENT7 months ago
The Ultimate Guide to Shillong Teer Hit Number: How to Predict Your Next Win
- LIFESTYLE1 week ago
Who Is Sandra Orlow?
- LIFESTYLE3 months ago
Berniece Julien: The Private Life of Tyson Beckford’s Partner
- Uncategorized12 months ago
Conrad Fisher Transformation: From Top Student to Troubled Soul