AUTOMOTIVE
Installation Guide for FPV Drone Motors: Tips and Procedures
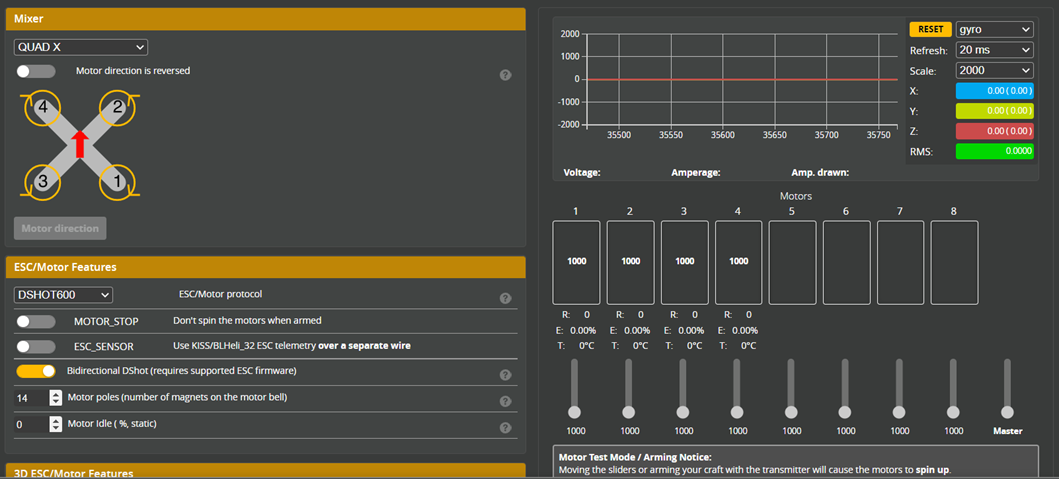
1. Introduction
FPV (First Person View) drones are beloved by drone enthusiasts for their agility, speed, and ability to offer an engaging perspective during flight. Installing motors on an FPV drone is a crucial phase to ensure optimal performance and safety during flight. In this guide, we will explore the basic details of installing drone motor on FPV drones, including ESC/motor compatibility, motor mounting, cable routing, measuring cables to fit desired lengths, and troubleshooting common issues.
2. ESC/Motor Compatibility
Before starting the motor installation process, it’s essential to ensure that the Electronic Speed Controllers (ESCs) are compatible with the motors you intend to use. ESCs regulate the speed and direction of motor rotation and must be capable of handling the current required for motor operation. Therefore, it’s necessary to ensure that the ESCs support the current and voltage required by the motors, in addition to being compatible with the drone’s flight controller firmware.
3. Motor Mounting
3.1. Motor Attachment
Use appropriate screws and nuts to secure the motors to the drone frame. Ensure that the motors are securely fastened to prevent unwanted movements during flight and that the screws do not touch or are close to the stators (this could cause motor overheating issues).
3.2. Use of Insulating Gaskets and Racewiring
To reduce vibrations and protect electronic components, it is advisable to use insulating gaskets between the motors and the drone frame. Racewiring can also be used if the motor cables are too short or if you want to facilitate motor replacement in the future.
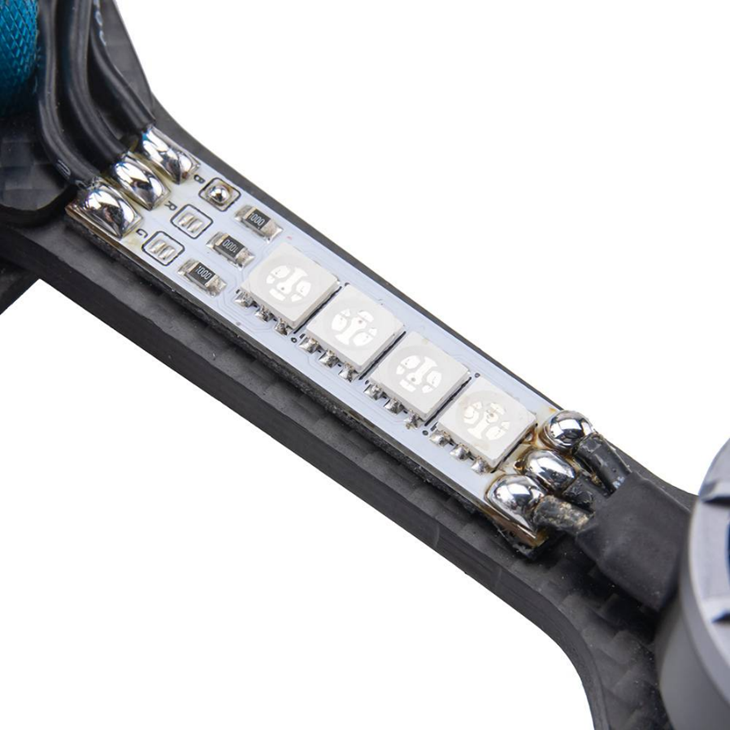
3.3. Cable Routing
3.3.1. Planning Cable Routing
Before connecting the motor cables to the ESCs, plan the cable routing to ensure a neat and safe installation. Avoid cable crossings or tangles that could interfere with motor movements or other drone components. It’s also possible to route the cables internally between the Flight Controller (FC) and ESC (in the case of a stack), which helps to have a cleaner build visually and allows leaving the motor cables longer; however, leaving internal cables may cause vibrations.
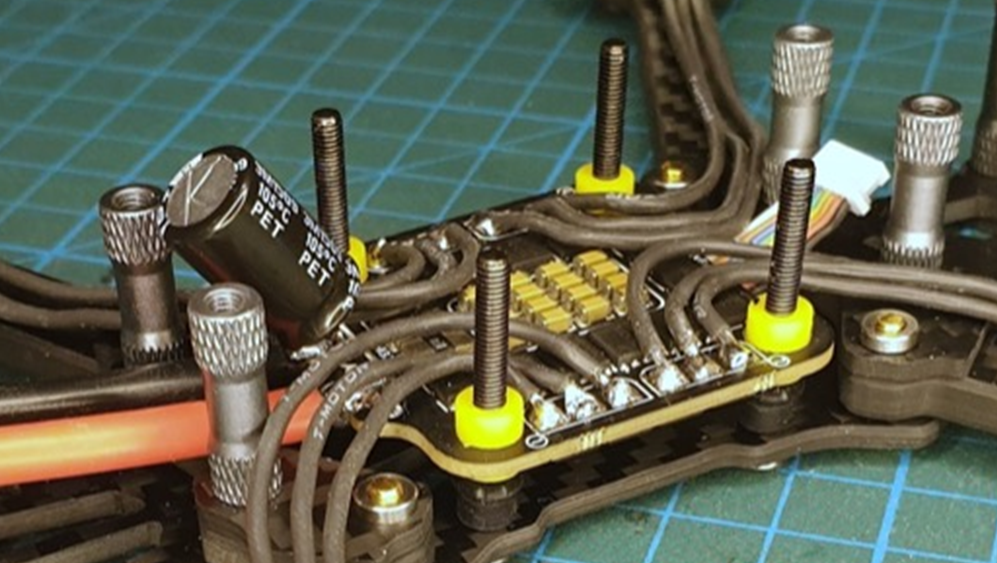
3.3.2. Use of Cable Protections and Fastening
To prevent leaving the cables loose, it is necessary to protect and secure them on the arm; for this purpose, there are several solutions: hard plastic tubing (not recommended because they break at the first crash), electrical tape, zip ties, cloth tape (the best in experience), etc.
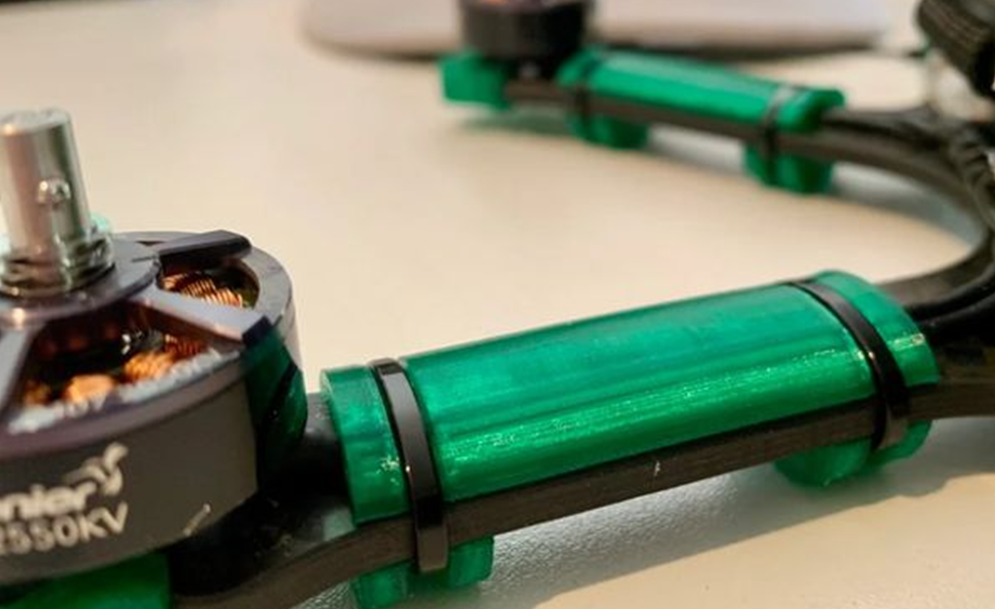
3.4. Measuring Cables
3.4.1. Determine Cable Length Measure
The distance between the motors and ESCs to determine the length of cables needed. It is advisable to leave an additional margin to allow for movements and adjustments during installation. Pay attention to the frame type; the length of cables may vary depending on the arm.
3.4.2. Cable Cutting Once
The desired cable length is determined, carefully cut them using pliers or scissors designed for electrical cables, strip the ends, and pre-solder them.
3.4.3. Cable Soldering Connect
The motor cables to the ESCs using the appropriate soldering technique. Ensure that the connections are solid, secure, and that the solder does not contact adjacent pads or other ESC components to avoid false contacts, disconnections during flight, or short circuits.
By carefully following these steps and considering component compatibility, mounting motors on an FPV drone can be a rewarding process that improves the performance and stability of your drone during flight. Always remember to perform a thorough pre-flight check to ensure that all components are properly installed and functioning as expected; now let’s move on to motor configuration.
4. Motor Configuration
Configuring motors on an FPV drone is a crucial step to ensure optimal performance and a good flying experience. Using a flight configurator, such as Betaflight, Cleanflight, or Kiss, you can customize various parameters to tailor your drone’s behavior to your flying preferences. Below are the various steps to configure motors with our flight configurator.
4.1. Connection and Preparation
Before starting, make sure your drone is connected to the computer via a USB cable and that the flight configurator is open and correctly configured to communicate with the drone. Also, ensure that the propellers have been removed, and the drone’s battery is disconnected to avoid accidents.
4.2. Access to the Motor tab
Once connected, open the flight configurator and go to the section dedicated to motors. This section will allow you to adjust the parameters of individual motors according to your needs; this is where we will begin our configuration.
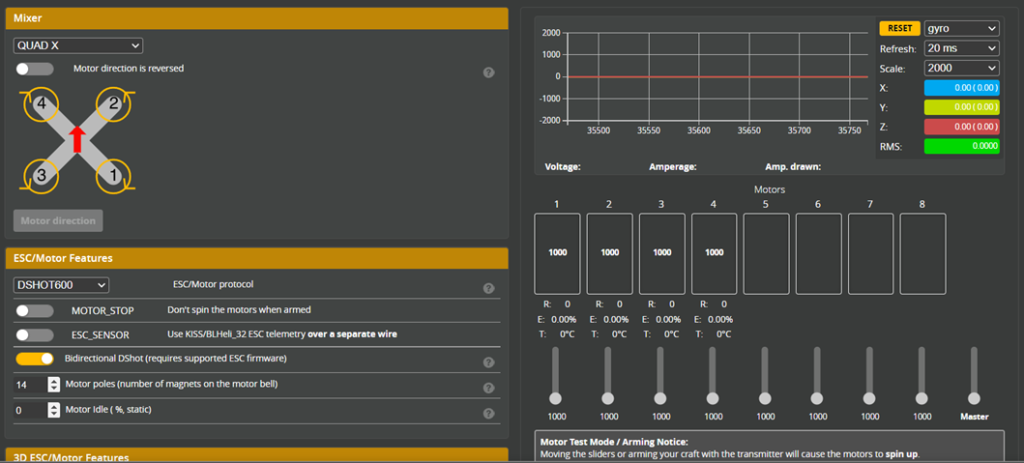
4.3. Checking Motor Order and Rotation Direction
Ensure that your drone’s motors are connected to the correct pins on your flight control board. Otherwise, the motors may spin in the wrong direction or not respond correctly to inputs. Check that the motor order is correct or change it through the configurator. Once it is confirmed that the order is correct, check the rotation direction (prop-in/prop-out) and that all motors respect the correct direction.
4.4. Motor Settings
Now is the time to adjust the motor settings. These settings include maximum motor speed, communication protocol, and other advanced options. Make sure you have your motor and ESC manuals handy to correctly configure the settings. For example, on a blheli_s ESC, it is recommended to download the Bluejay firmware.
4.5. Motor Testing
After setting the motor parameters, it is advisable to perform a test to ensure that all motors spin in the correct direction and respond uniformly to throttle inputs (WARNING: remove the propellers as previously stated). You can do this using the flight configurator, which will allow you to individually activate each motor.
4.6. Fine Tuning and Flight Test
Once the motor configuration is complete, it is advisable to perform some flight tests to verify that the drone behaves as desired. If necessary, further adjustments can be made to the motor parameters to improve performance or adapt the drone’s behavior to your flying preferences through PID tuning.
4.7. Safety Considerations
Before taking off, always make sure to perform a thorough check of your drone to ensure that all components are securely fastened and that there are no obvious damages. Always respect local regulations and fly in designated areas to avoid accidents and hazards to yourself and others.
We have seen how to mount and solder the motors, how to configure them; now let’s see the most common issues we may encounter.
5. Resolving Common Issues During FPV Drone Motor Installation
As we have seen, installing motors on an FPV drone is a crucial part of building a quadcopter. However, some issues may arise during this process. Let’s see what the most common challenges are and how to address them:
5.1. Vibrations and Abnormal Oscillations
- Possible Causes: Vibrations can be caused by unbalanced motors, damaged propellers, or incorrect motor mounting on the frame.
- Solutions: Balance the motors using a prop balancer. Check that the propellers are not damaged and securely mount the motors on the frame, using insulating gaskets if necessary.
5.2. Excessive Heat on Motors
- Possible Causes: Excessive current through the motors, poor airflow, screws too long and therefore too close to the stator, incorrect PID settings, incorrect ESC firmware, can cause overheating.
- Solutions: Check that the ESCs are calibrated correctly and that the current supplied to the motors is adequate. Ensure that the airflow around the motors is sufficient , avoiding obstructions in the drone frame, recheck the screws, and finally, if the problem persists, review the PID settings.
5.3. Cable Connection Problems
- Possible Causes: Damaged cables, loose connections, or faulty solder joints can cause connection problems.
- Solutions: Inspect the cables carefully for any damage. Ensure that the connections are securely connected and that the solder joints are of good quality; also recheck the cable bends in case they have been forced and may have broken internally.
5.4. Motors Not Starting or Not Responding Correctly
- Possible Causes: Incorrect ESC configuration, power issues, motor or ESC damage, incorrect ESC-motor connections and/or ESC/FC connections can cause motor malfunction.
- Solutions: Check the ESC configuration and reprogram them if necessary. Check that the power supply is correct and that there are no interruptions in the electrical circuits. Inspect the motors for any physical damage. Recheck the connector that connects FC to ESC (in some stacks, it is necessary to pay attention to which connector is inserted into the ESC and which connector is inserted into the FC, having a different min order).
5.5. Strange Noises During Motor Operation
- Possible Causes: Some abnormal noises may indicate mechanical damage to the motors; in other cases, there may be abnormal noises due to incorrect PID settings, misaligned bells, dirty motors, or incorrect configuration.
- Solutions: Visually inspect the motors for any signs of damage or wear. Recheck the PID settings, motor, and ESC configuration, give the motors a clean.
5.6. ESC/Motor Compatibility Issues
- Possible Causes: ESCs may not be suitable for the motors in use or may not be compatible with the flight controller firmware.
- Solutions: Check the compatibility of ESCs and motors using technical specifications and manufacturer recommendations. Update the flight controller firmware if necessary.
Addressing these issues requires patience and attention to detail. With proper diagnosis and the right solutions, most problems that may arise during the installation of motors on an FPV drone can be successfully resolved. If problems persist, consult online resources (social media communities can also be a great source of help) or seek assistance from industry experts for additional support.
AUTOMOTIVE
The Smart Way to Compare Car Shipping Quotes Online in Minutes
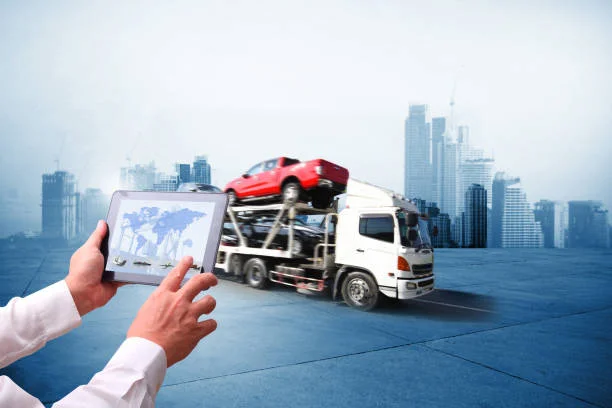
The hardest part about writing a post on how to find the best way to ship a car would be titling it! Learning to compare car shipping quotes online can save you a lot of money and time, given the many options available.
To help make your experience as smooth and efficient as possible, this guide provides a few tips and tricks to hopefully streamline the process for you and make getting car shipping quotes online easier.
Understanding Car Shipping Basics
Before contacting a transport company, it is important to understand the basics of car shipping. Most providers offer two main options: open transport and enclosed transport. Open carriers are generally more affordable, while enclosed carriers offer greater protection for high-value or delicate vehicles. Knowing the difference helps you make a more informed and confident decision based on your needs and budget.
Defining Your Needs
The most important step is identifying requirements. Take into account the distance a vehicle is travelling, what kind of vehicle it is, and how soon you want it delivered. When you have an idea about what you need, it will be easy and accurate to compare.
Researching Reliable Companies
It is very important to choose a reliable company. Online reviews and ratings help us understand previous customers’ experiences. Find firms that have excellent feedback. It is also a good practice to verify proper licensing and insurance coverage.
Using Online Tools for Quotes
So, instead of going to the physical markets, consumers can get quotes very easily online, and the online platform gives them all the necessary information for making the right choice. The consumer goes to many websites, fills out information, and receives multiple quotes, usually within a few minutes. They provide a hassle-free means of comparing various options without millions of calls or endless emails.
Comparing Prices and Services
Price is undoubtedly an important factor, but it should not be the only one. Look at what is included with each quote—what insurance they provide, the time frame for delivery, and other fees. When you know everything about each of the offers, you can make a better decision.
Looking at Customer Support
Customer support is an important aspect of shipping. Companies that communicate well and are quick to respond are more likely to be reliable. You can tell a lot about how much a company cares about customer satisfaction by how it responds to questions and problems.
Evaluating Insurance Options
Insurance is a vital component when shipping cars. Make sure the coverage provided meets your personal needs. While the call is pretty basic, some companies will have really good plans. Knowing the terms and conditions of insurance policies is essential to help you in the future.
Reading Fine Print
Because there are no unpleasant surprises, reviewing terms and conditions saves you from the trouble. So be mindful of cancellation policies, extra fees, and delivery and pickup terms. This will help you avoid any miscommunication and make the transaction smooth.
Seeking Recommendations
Personal recommendations can be invaluable. You can get tips or advice from friends, family, or coworkers with experience using car shipping services. When it is your own experience, it gives a clear context and almost every time it shows something special that is not readily shown by the research on the internet.
Utilizing Social Media
Social media is a handy medium that, arguably, creates a demand for information. Numerous businesses are perpetually present in these spaces and frequently interact with customers. You can get a hint about how reliable they are and how well they will serve you by observing how a company interacts with people on social media.
Timing Your Booking
Timing can influence shipping costs. As a general rule, better prices come with early bookings and higher rates with last-minute arrangements. Seasonal demand can also influence pricing and availability.
Reviewing Multiple Quotes
Compare several quotes that will help you gather some perspective. Do not be tempted to settle on the first acceptable option you come across. Comparing numerous places gives you a sense of equilibrium and brings to the forefront the best offer.
Making an Informed Decision
Once you have everything you need, it becomes a simple case of making the right choice. Just make sure to weigh the pros and cons, whether it be the price, service, insurance, or the company’s reputation. The result of a passive take is mutually beneficial.
Conclusion
Getting online car shipping quotes to compare is a little more complicated than it should be. By identifying individual needs, studying companies, and using online tools, it will be a piece of cake. However, with some strategic thinking and proper planning, the right solution to your shipping needs is entirely attainable and profitable.
AUTOMOTIVE
Stay Cool in Every Season: Expert Air Conditioning Repair Services in Orange County
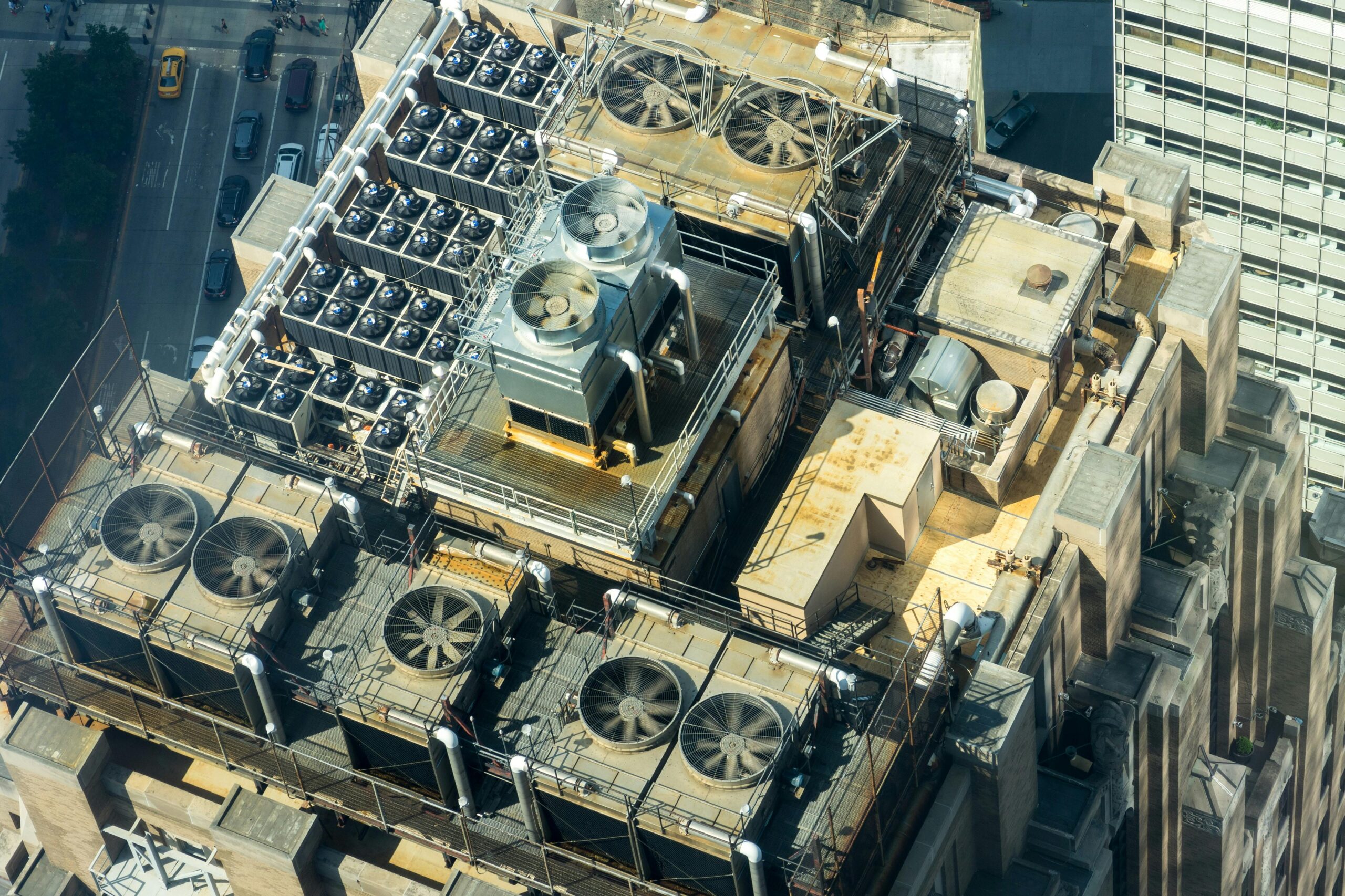
Living in Orange County means enjoying warm weather almost all year long. But with that comes the need for a working air conditioning system. Whether it’s summer or a mild winter day, having cool air inside your home or business is important. A broken or weak AC can quickly become a problem, especially during a heatwave. That’s why reliable air conditioning repair services are essential.
With many homes and businesses depending on AC systems, the demand for professional help keeps growing. When your system fails, you want fast, effective, and affordable solutions. That’s exactly what trusted HVAC companies in the area provide through expert services in air conditioning Orange County residents rely on.
Why Quick AC Repairs Matter
When an AC system is not working properly, it can affect your comfort, health, and energy bills. Small issues can turn into big problems if they are ignored. A faulty compressor, leaking refrigerant, or clogged filters are common problems that can reduce the cooling ability of your system. These issues not only affect temperature but also reduce indoor air quality.
Quick repair services help stop these problems from getting worse. Expert technicians can find the problem fast and fix it right the first time. This means you stay comfortable and safe, and your system lasts longer.
What to Expect from a Professional AC Repair Service
Professional air conditioning repair companies in Orange County offer a full range of services. From emergency repairs to regular maintenance, they can handle every part of your HVAC system. Here’s what you can expect when working with a skilled HVAC team:
- Fast response times
- Honest pricing with no hidden charges
- Certified and trained technicians
- Repairs for all major AC brands and models
- Warranty on parts and labor
These services are designed to give you peace of mind and make sure your cooling system works when you need it most.
Signs You Need Air Conditioning Repair
Not sure if your system needs repair? There are some clear signs that your air conditioner is not working well. If you notice any of the following issues, it might be time to call in the pros for air conditioning repair Orange County residents trust:
Weak Airflow
If the airflow coming out of your vents is weak, it may be a sign of a clogged filter, duct problem, or compressor issue. This means your AC has to work harder, which can lead to higher energy bills.
Warm Air
When the air coming out of your AC is not cool, it could be due to a low refrigerant level or a problem with the compressor. Warm air from your vents is a major sign that something is wrong.
Strange Noises
Loud banging, grinding, or rattling noises coming from your AC are not normal. These sounds often mean there is a loose part or motor problem that needs immediate attention.
High Humidity Levels
An efficient AC should help control humidity. If your home feels damp or sticky, it could be because your air conditioner isn’t doing its job correctly.
Why Choose Local Experts in Orange County
Choosing a local HVAC company in Orange County has many advantages. Local technicians understand the weather patterns and know what systems work best in the area. They are also more likely to offer quick response times and personalized services. Many trusted companies offer free estimates, competitive prices, and regular service packages.
A company like GoTech HVAC, based in Orange County, provides expert air conditioning repair and maintenance. They are licensed, experienced, and available seven days a week. Their team uses quality tools and parts, ensuring long-lasting results.
Benefits of Regular Maintenance
To avoid sudden breakdowns, regular AC maintenance is key. Well-maintained systems run better, last longer, and use less energy. During a maintenance visit, technicians will:
- Inspect and clean filters
- Check refrigerant levels
- Inspect electrical connections
- Clean the evaporator and condenser coils
- Test the system for performance
These checks help spot small problems before they become serious. Regular maintenance is a smart investment that saves time and money.
Conclusion
Air conditioning is more than just a luxury in Orange County—it’s a necessity. Whether your system needs a small fix or a full repair, working with experienced HVAC professionals ensures you stay cool, safe, and comfortable. From regular maintenance to emergency repairs, trusted companies like GoTech HVAC are ready to help.
Investing in timely air conditioning repair services is the best way to extend the life of your system, save money, and enjoy peace of mind throughout the year. Don’t wait until your system breaks down. Stay ahead of the heat and keep your indoor spaces cool in every season.
AUTOMOTIVE
The Secrets to Prolonging Your Vehicle’s Lifespan Through Proper Maintenance
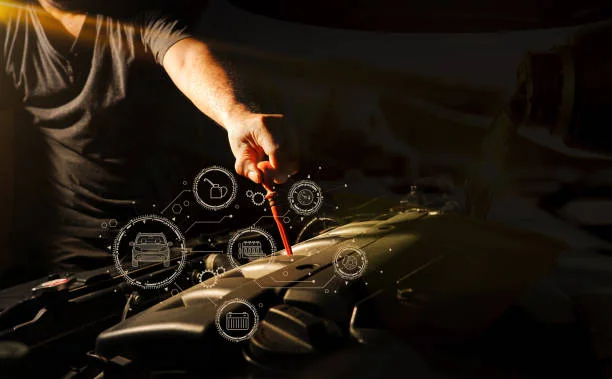
Key Takeaways:
- Regular maintenance is crucial for vehicle longevity.
- Oil changes and tire rotations are simple tasks that yield significant benefits.
- Understanding warning signs can prevent costly repairs.
- Trusted maintenance centers can ensure quality service and reliability.
Understanding the Basics of Vehicle Maintenance
Grasping the fundamentals of car upkeep is crucial for ensuring your vehicle operates efficiently and prolongs its life. Regular tasks such as checking engine oil levels, monitoring tire pressure, and replacing air filters improve performance and help prevent more costly repairs. Following your vehicle manufacturer’s maintenance schedule ensures that critical components like the brakes, battery, and transmission are inspected and serviced at the proper intervals. Even simple actions like washing your car and cleaning the interior can protect paint, upholstery, and resale value.
Regarding more complex or scheduled maintenance tasks, it’s wise to rely on certified professionals who understand your vehicle’s make and model requirements. Searching for a Honda service center near me can be a practical first step in finding qualified technicians and proper diagnostic tools tailored to your vehicle. Utilizing a reputable service center helps ensure your car is maintained to the highest standard and retains its reliability over time. This approach promotes safety and enhances long-term performance and fuel efficiency.
Oil Changes: The Lifeblood of Your Engine
Routine oil changes are crucial for keeping your vehicle’s engine in good condition. They lubricate moving components, minimize friction, and assist in heat dissipation. Oil can degrade and become debris-contracted as time passes, resulting in greater wear, overheating, or even engine failure. It’s essential to adhere to the oil change schedule specified in your vehicle’s manual, particularly if you frequently drive under demanding conditions. Maintaining consistent oil changes benefits your engine’s health and enhances its efficiency, ultimately leading to improved fuel economy over time.
Continue your journey: This related article is worth your time.
Tire Maintenance: Safety and Efficiency
Tire maintenance ensures vehicle safety, fuel efficiency, and overall performance. Regularly checking tire pressure, tread depth, and alignment can help prevent blowouts and improve traction in various driving conditions. Uneven wear or underinflated tires can reduce fuel economy and increase the risk of accidents, making routine inspections essential. For vehicle owners seeking professional assistance, places like Honda dealerships in GA often provide tire services that follow manufacturer guidelines and use proper equipment. Whether handling tire rotations, balancing, or replacements, staying proactive with tire care supports a smoother, safer, and more economical driving experience.
Understanding Warning Lights and Dashboard Alerts
Contemporary cars have sensors and alert lights that communicate with the driver. Understanding what these lights mean can prevent minor issues from escalating into costly repairs. For example, a check engine light could signal anything from a loose gas cap to a more serious engine problem.
A prompt response to dashboard alerts can mitigate the effects of a problem before it becomes severe. Regularly reviewing your vehicle’s manual to familiarize yourself with these indicators can empower you to take timely action and identify when a professional assessment is necessary.
The Importance of Preventive Maintenance
Preventive maintenance is a forward-thinking strategy that can result in considerable savings throughout your vehicle’s lifespan. Routine tune-ups, which involve monitoring fluid levels, examining belts and hoses, and verifying that all parts are functioning correctly, may initially appear to be an unnecessary expense. Nevertheless, by avoiding major breakdowns and extending the useful life of parts, these tune-ups can minimize the chances of incurring costly repairs later on.
In addition to savings on repair costs, well-maintained vehicles are often more fuel-efficient, which can result in lower ongoing costs. Preventive maintenance is about having the foresight to address minor issues before they become problems that eat into your budget.
Seasonal Maintenance Tips
Every season presents distinct challenges for maintaining vehicles. In the summer, high temperatures can cause motor oils to thin and batteries to be stressed, while winter requires extra attention to antifreeze levels and tire conditions. Preparing your vehicle for each season is about more than just reacting to weather changes; it’s about anticipating them.
Simple tasks like switching to winter tires, checking antifreeze levels, and ensuring the heater and defroster work properly can make a huge difference in how your vehicle handles cold weather. Similarly, ensuring optimal air conditioning performance and tire conditions for the hotter months can keep you comfortable and safe.
Selecting a Reliable Maintenance Center
Choosing the right service center to perform vehicle maintenance is crucial. Reliable centers with certified technicians provide high expertise and service quality, which helps reinforce peace of mind. Look for service centers that have strong reviews and reputation in your area. A skilled center should additionally provide transparent pricing and an in-depth account of the services completed and their importance.
Regular visits to a trusted center ensure you receive professional evaluations and services that uphold your vehicle’s performance and safety standards. Established relationships at a reliable workshop can also lead to better service experiences as the technicians become familiar with your vehicle’s history and specific needs.
Let your love for learning blossom—step into a world of ideas on Crispme.
- GENERAL1 month ago
5 Factors That Affect Tattoo Removal Success
- ENTERTAINMENT2 months ago
Exploring the Kristen Archives: A Treasure Trove of Erotica and More
- LIFESTYLE6 months ago
The Disciplinary Wives Club: Spanking for Love, Not Punishment
- TECHNOLOGY6 months ago
Blog Arcy Art: Where Architecture Meets Art
- ENTERTAINMENT7 months ago
The Ultimate Guide to Shillong Teer Hit Number: How to Predict Your Next Win
- LIFESTYLE1 week ago
Who Is Sandra Orlow?
- LIFESTYLE3 months ago
Berniece Julien: The Private Life of Tyson Beckford’s Partner
- Uncategorized12 months ago
Conrad Fisher Transformation: From Top Student to Troubled Soul