TECHNOLOGY
Best Practices for Welding Thermoplastics with Hot Wedge Welders
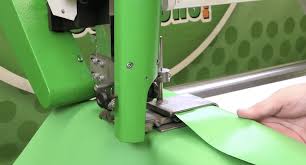
Introduction: When it comes to working with thermoplastics, precision is key—and hot wedge welders offer one of the most effective solutions for creating strong, reliable bonds. Whether you’re installing geomembranes, sealing industrial liners, or tackling other projects, mastering the use of hot wedge welding machines can save you time, reduce material waste, and ensure high-quality results.
In this guide, we’ll explore the best practices for welding thermoplastics using hot wedge welders, offering practical tips and real-world examples to help you elevate your craftsmanship.
1. Understand Your Materials Not all thermoplastics are created equal, and each material comes with its own set of characteristics. For example, polyethylene (PE) and polyvinyl chloride (PVC) have different melting points and welding behaviors. Before starting a project:
- Check the material specifications for compatibility with hot wedge welding.
- Perform test welds to fine-tune your settings.
Example: Imagine you’re welding a high-density polyethylene (HDPE) liner for a landfill project. Using the wrong temperature could cause burns or weak seams. By understanding the material’s properties and testing beforehand, you can avoid costly mistakes.
2. Optimize Your Machine Settings Hot wedge welders allow you to adjust parameters like temperature, speed, and pressure. Finding the right balance is crucial:
- Temperature: Ensure it’s high enough to create a strong bond but not so high that it damages the material.
- Speed: Adjust the speed based on the material’s thickness; thicker materials typically require slower speeds.
- Pressure: Too much pressure can distort the material, while too little can lead to weak welds.
Pro Tip: Keep a log of successful machine settings for different materials and conditions. This can save you significant time on future projects.
3. Prioritize Cleanliness Dirt, moisture, and debris can compromise weld integrity. Always:
- Clean the material surfaces with an appropriate solvent before welding.
- Check the wedge for buildup and clean it regularly to maintain consistent performance.
Story: A contractor working on a pond liner noticed weak seams during a quality check. The culprit? Dust particles left on the material’s surface. A quick cleaning routine resolved the issue and prevented further delays.
4. Conduct Regular Equipment Maintenance Your hot wedge welder is only as good as its condition. To ensure optimal performance:
- Inspect the wedge for wear and tear.
- Check electrical components for loose connections.
- Lubricate moving parts as recommended by the manufacturer.
Example: During a roofing project, a technician avoided costly downtime by identifying a worn wedge heater during a routine inspection. Replacing it before failure kept the project on schedule.
5. Use Proper Welding Techniques Even with the best equipment, improper techniques can lead to poor results. Keep these tips in mind:
- Overlap material edges evenly to ensure strong seams.
- Maintain consistent movement to avoid uneven welds.
- Monitor weld temperatures using an infrared thermometer or built-in sensors.
Pro Tip: Practice on scrap material to refine your technique and troubleshoot potential issues.
6. Perform Quality Checks Never skip post-weld inspections. Use methods like:
- Peel Tests: Check the weld’s strength by peeling the layers apart.
- Air Pressure Tests: Ensure airtight seams by testing with an air pump and gauge.
- Visual Inspections: Look for discoloration, voids, or uneven edges.
Story: A team installing geomembranes for a reservoir avoided a major leak after detecting a small seam defect during a routine air pressure test. The quick repair saved them from expensive rework.
Conclusion: Mastering hot wedge welding takes practice, attention to detail, and a commitment to quality. By understanding your materials, optimizing machine settings, and following these best practices, you can achieve professional-grade results that stand the test of time. Whether you’re working on industrial projects or smaller-scale applications, these tips will help you maximize efficiency and minimize errors. Ready to take your welding skills to the next level? Put these insights into action today.
TECHNOLOGY
Why Concierge-Level Support in Virtual Data Rooms Matters for High-Stakes Transactions
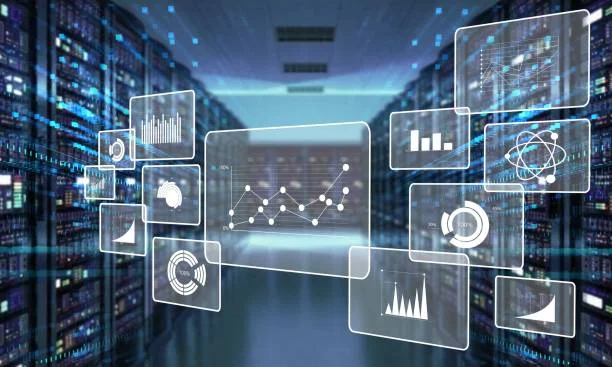
Whether navigating a complex merger, launching a capital raise with multiple LPs, or managing a cross-border acquisition, the outcome often depends on how well the execution is managed. In time-sensitive deals, delays can cost more than just money—they can erode trust, derail momentum, and put the entire transaction at risk for Concierge-Level Support.
That’s why more dealmakers are turning to virtual data room (VDR) platforms that offer not just speed and security, but also enterprise-level concierge support. This white-glove service extends beyond traditional tech support, giving deal teams access to dedicated experts who help set up, configure, and manage VDR workspaces with precision.
What Is Enterprise Concierge Support in a VDR?
Concierge support goes far beyond responding to service tickets. It’s about having a hands-on team available to assist with all aspects of your data room, including:
- Workspace setup and onboarding
- File uploads, conversions, and folder structure organization
- User and permission management
- Security configuration and compliance guidance
- Q&A workflows and approval hierarchies
- Customized training for internal and external stakeholders
For high-value, high-complexity transactions, concierge support provides the infrastructure and expertise required to move fast without sacrificing accuracy or control.
Why Basic Support Isn’t Enough for Enterprise Deals
In large transactions, multiple stakeholders need access at different levels—legal teams, analysts, auditors, investors, and compliance officers. Each participant has unique requirements and permissions. Coordinating that complexity with a slow support desk or self-service tools is a recipe for confusion.
Many VDR providers still rely on:
- Email-only support queues
- Business-hours-only availability
- Limited onboarding help
- Little to no experience with regulated or sensitive transactions
By contrast, concierge-level VDR services offer real-time responsiveness and strategic guidance to ensure your workspace is optimized for speed and precision.
How Concierge Support Enhances the Deal Lifecycle
Here’s how expert VDR support directly improves outcomes at every stage of the transaction process:
1. Rapid Launch with Reduced Risk
A strong start can make all the difference. Instead of spending days or weeks configuring a workspace, concierge teams can handle setup on your behalf:
- Custom folder structures built to match your workflow
- Pre-assigned permission tiers for each stakeholder group
- Bulk file uploading and document import support
This gets your data room live quickly and minimizes the chance of permission errors that could expose confidential documents to the wrong eyes.
2. On-Demand Help When It Matters Most
During the peak of diligence, deal teams can’t afford to wait for answers. Whether it’s resolving an access issue, tagging documents for review, or troubleshooting file visibility, real-time support ensures your progress doesn’t stall.
Concierge support includes:
- Live response via phone or email
- Specialists trained in private equity, M&A, and cross-border deal complexity
- 24/7 availability when transactions require round-the-clock attention
When critical moments arise, immediate solutions can be the difference between closing and losing a deal.
3. Elevated Stakeholder Experience
For many investors and buyers, your data room is their first impression of your organization. A smooth, intuitive interface—and quick access to the right documents—speaks volumes about your professionalism.
With concierge support:
- Stakeholders are guided through onboarding
- Access challenges are handled proactively
- Corporate branding can be applied for a seamless experience
- FAQ and navigation aids can be built in to reduce confusion
These touches improve trust and help keep participants focused on the deal, not the platform.
4. Support for Security and Regulatory Compliance
Complex transactions often involve regulated data—financial disclosures, personal information, health records, and more. Maintaining compliance with data protection laws (like GDPR or HIPAA) is non-negotiable.
Concierge support teams can help:
- Configure user permissions aligned with compliance best practices
- Set up audit trails and activity tracking
- Apply security settings like dynamic watermarking and access expiration
This reduces the risk of non-compliance and ensures sensitive data stays protected throughout the deal.
Measurable ROI From Expert VDR Support
Concierge-level support isn’t just a value-add—it can directly impact the speed and success of your transaction. Benefits include:
- Faster onboarding and setup
- Fewer technical errors or stakeholder complaints
- Higher investor or acquirer engagement
- Smoother close processes and better buyer experiences
- Greater confidence in compliance and document control
Every saved hour, reduced error, or avoided delay compounds over the life of a high-value deal.
What Sets Leading Concierge Support Apart
Not all VDR support is created equal. The most effective concierge services provide:
- Dedicated account managers with experience in your industry
- Tailored onboarding for each new workspace
- Proactive assistance during critical transaction stages
- Integrated guidance on permissions, structure, and legal compliance
- Rapid-response help desks staffed by professionals—not generic agents
This type of support is designed for speed, accuracy, and reliability—exactly what’s required in the pressure-filled environment of modern dealmaking.
The Case for Concierge VDR Support in Strategic Transactions
When deals involve multiple parties, sensitive data, and tight timelines, execution matters more than ever. A virtual data room with concierge support provides the tools and expertise to move faster, collaborate more effectively, and protect your most valuable information at every stage.
From quick setup to ongoing assistance and compliance peace of mind, enterprise concierge support can transform a standard data room into a fully managed, strategic advantage.
Explore the featured posts and gain top strategies to enhance your business today.
TECHNOLOGY
Cursed-Memes.com Technology: Impact on Digital Culture
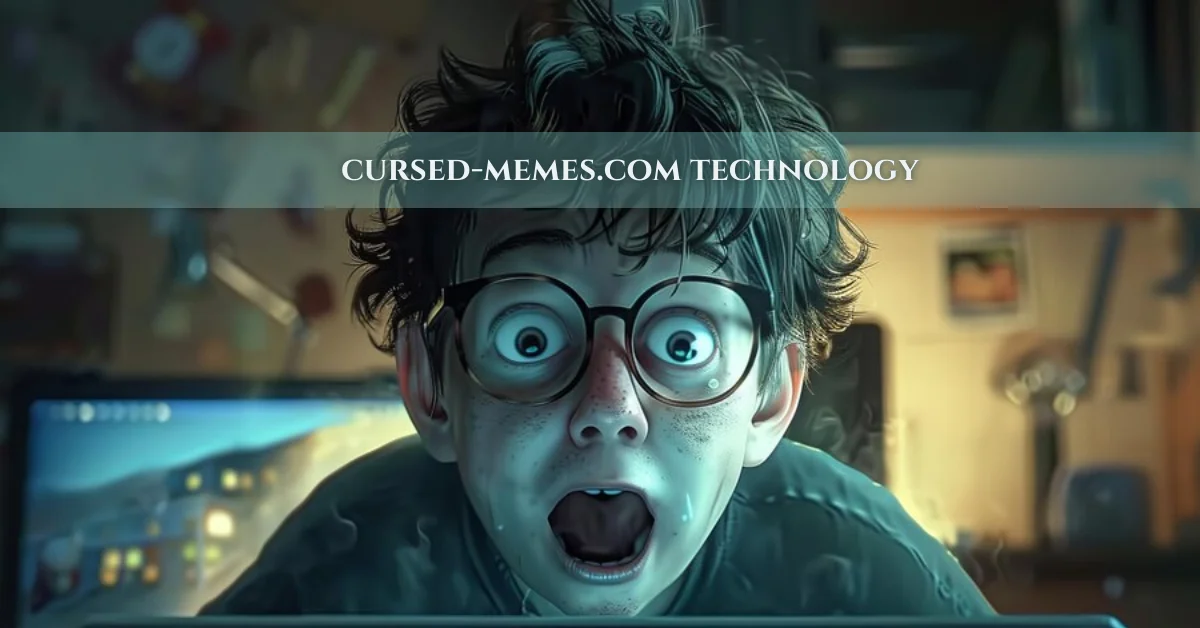
Introduction to cursed-memes.com technology
Welcome to the wild world of internet memes, where humor and absurdity collide! One platform that’s taken this phenomenon to new heights is cursed-memes.com technology. This innovative approach has transformed how we engage with digital culture, pushing boundaries and reshaping our online experiences. Memes have become more than just fleeting images; they’re now powerful tools for communication, social commentary, and entertainment. As we dive into the realm of cursed memes, you’ll discover what sets them apart from their traditional counterparts and explore their far-reaching impact on popular culture. Buckle up—it’s going to be an enlightening ride through the meme-verse!
The Rise of Memes in Digital Culture
Memes have transformed the landscape of digital culture. They serve as a universal language, bridging gaps between diverse communities.
Originating from simple images with text, memes quickly evolved into intricate forms of expression. Social media platforms fueled their rapid spread, allowing anyone to create and share. As a result, memes became an integral part of online communication.
The rise of internet humor has changed how we engage with content. Memes often reflect societal trends and cultural references in real-time—making them both timely and relatable.
With their ability to provoke thought or laughter, they capture fleeting moments in our collective consciousness. This phenomenon showcases creativity while fostering connections among users worldwide.
In today’s digital arena, memes are more than just entertainment; they’re statements that resonate deeply within various subcultures.
How Cursed-Memes.com is Different from Traditional Memes?
Cursed-memes.com technology takes meme creation to a whole new level. Unlike traditional memes that often rely on humor or relatable content, cursed memes dive into the bizarre and absurd.
These digital artifacts often incorporate distorted visuals and dark humor. They challenge our understanding of what’s funny by blending surreal elements with unexpected contexts. This creates a unique experience for viewers who find joy in decoding the madness.
The format encourages creativity, inviting users to remix existing images in unconventional ways. Traditional memes typically follow established formats; cursed memes thrive on breaking those molds.
Moreover, the community surrounding cursed-memes.com embraces an ironic detachment from mainstream culture. This fosters a space where niche interests can flourish without boundaries, setting it apart from conventional meme platforms that cater to broader audiences.
ALSO READ: lotterygamedevelopers.com: Create Your Dream Lottery Game
The Impact of Cursed-Memes.com on Popular Culture
Cursed-memes.com technology has shifted the landscape of popular culture dramatically. It introduces a new layer of humor that combines absurdity with relatable experiences. This unique blend captivates audiences, drawing them into an alternate reality where nothing is off-limits.
Social media platforms buzz with these cursed memes, often going viral overnight. They capture moments and emotions in ways traditional formats cannot achieve. The surreal nature creates shared laughter and confusion among users.
Moreover, brands have started to tap into this phenomenon. Marketing strategies now incorporate elements of cursed memes to resonate with younger audiences who appreciate unconventional humor.
As creators push boundaries, the cultural dialogue evolves too. Cursed memes challenge societal norms while encouraging creativity in expression—something that’s becoming increasingly valuable in today’s digital age.
Controversies Surrounding cursed-memes.com technology
Cursed-memes.com technology has sparked significant debate in online communities. Critics argue that its content often crosses the line into inappropriate or offensive territory. The edgy nature of cursed memes can lead to misunderstandings, especially for those unfamiliar with meme culture.
Some believe these memes perpetuate negativity and desensitize users to serious issues. They worry about the potential harm to mental health, particularly among younger audiences who may struggle to differentiate satire from reality.
On the other hand, advocates defend cursed-memes.com as a creative outlet. They contend it allows individuals to process dark humor during tough times. This dichotomy creates an ongoing conversation about boundaries in digital expression.
Additionally, copyright concerns have emerged as creators navigate ownership within this chaotic landscape of remixed media. Artists often find their work repurposed without credit, igniting disputes over intellectual property rights in an ever-evolving meme ecosystem.
ALSO READ: Pikruos: Your Partner in Business Technology Solutions
Future of Cursed-Memes.com and the Evolution of Memes
The future of cursed-memes.com technology is poised to shape the next wave of digital expression. As meme culture continues to evolve, we can expect even more bizarre and unpredictable content.
Emerging technologies like artificial intelligence will play a significant role in this transformation. AI can generate memes at an unprecedented scale, pushing boundaries that challenge traditional humor.
Social media platforms are also adapting. They’re integrating algorithms that prioritize unique and edgy content, making cursed memes more visible than ever before.
As creators experiment with new formats—think video loops or interactive elements—the line between consumed content and creator will blur further.
The interconnectedness of global cultures online ensures that these cursed creations will resonate worldwide, sparking conversations around shared experiences infused with dark humor. This evolution promises not just entertainment but a deeper commentary on modern life itself.
Conclusion: Embracing the cursed-memes.com technology Phenomenon
The rise of cursed-memes.com technology marks a significant shift in how we interact with digital content. This platform has opened up new avenues for creativity, allowing users to explore humor that pushes boundaries and challenges societal norms. As memes continue to evolve, those rooted in the concept of “cursedness” invite us to reflect on our collective experiences and reactions.
Cursed memes have created their own niche within the digital culture landscape. They not only entertain but also provoke thought and discussion about what is acceptable in humor today. With this unique blend of absurdity and relatability, cursed-memes.com stands out as a beacon for those who enjoy the unconventional.
As we move forward, it’s clear that platforms like cursed-memes.com will shape future trends in meme culture. Whether you love them or hate them, these memes are here to stay. Embracing this phenomenon can lead to richer conversations about art, expression, and even societal issues through the lens of humor.
Engaging with cursed-memes.com technology invites everyone into a broader dialogue about creativity online—one filled with unexpected twists and endless possibilities. The journey into this peculiar world promises excitement for both creators and consumers alike.
ALSO READ: Emometre: Decoding Human Emotions
FAQs
What is “cursed-memes.com technology”?
Cursed-memes.com technology refers to an innovative approach to meme creation that emphasizes absurdity and dark humor, transforming traditional memes into unique digital expressions that challenge societal norms.
How do cursed memes differ from traditional memes?
Cursed memes utilize bizarre visuals and surreal humor, often breaking established formats and pushing creative boundaries, unlike traditional memes that usually rely on relatable content.
What impact have cursed memes had on popular culture?
Cursed memes have reshaped online humor and communication, going viral on social media, influencing marketing strategies, and fostering new dialogues around creativity and societal norms.
Are there any controversies surrounding cursed-memes.com technology?
Yes, critics argue that cursed memes can be offensive or inappropriate, while advocates see them as creative outlets that allow individuals to cope with darker themes, sparking debates about humor boundaries.
What does the future hold for cursed-memes.com technology?
The future of cursed-memes.com technology is likely to feature more bizarre content driven by emerging technologies like AI, alongside evolving social media algorithms that prioritize edgy and unique expressions.
TECHNOLOGY
Decoding XVIF: Unveiling the Virtual Integration Framework
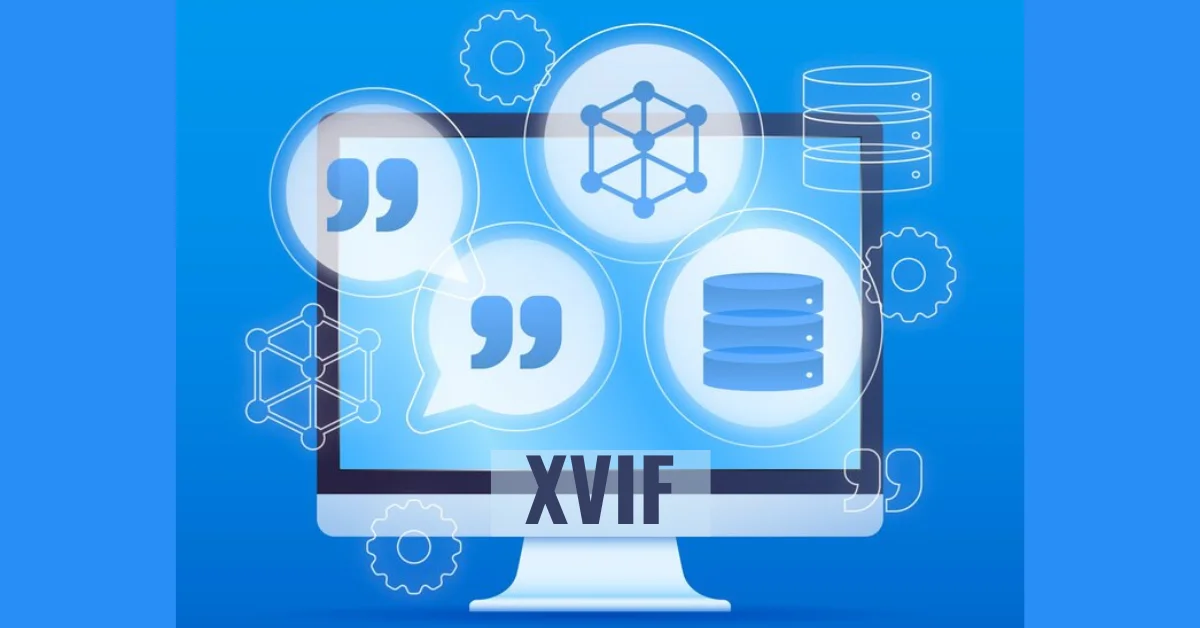
Breaking the Barrier Between Systems: What is XVIF?
In today’s hyperconnected world, integrating digital systems isn’t just a luxury—it’s a necessity. Businesses, developers, and organizations are constantly seeking ways to unify scattered data, streamline processes, and reduce friction between legacy and modern platforms. Enter XVIF, short for Virtual Integration Framework—a cutting-edge solution reshaping how systems talk to each other without the need for a complete overhaul.
Within the first wave of its adoption, xvif has already gained traction for its seamless, scalable, and future-ready approach to integration. But what makes this framework so special, and why should you be paying attention?
There’s plenty more where that came from—browse our other helpful content!
XVIF Explained: The Framework That Connects It All
At its heart, xvif is a modular and lightweight middleware layer that enables virtual integration between disparate systems—whether cloud-based, on-premises, or hybrid. Instead of rewriting legacy code or rebuilding existing systems, xvif allows organizations to overlay a “virtual mesh” that connects components through APIs, connectors, and intelligent data translation engines.
Think of it as a universal translator for your tech ecosystem—one that enables communication without forcing every component to speak the same language.
Why XVIF Is a Game-Changer
Unlike traditional integration methods that often require heavy investments in infrastructure and manpower, xvif offers a more agile and cost-effective alternative. Here’s what makes it stand out:
Low-Code Flexibility
XVIF’s intuitive interface and support for low-code development empower teams to build integrations faster—with fewer errors and shorter development cycles.
Real-Time Data Sync
With built-in support for event-driven architecture, xvif ensures systems remain updated in real-time, reducing lag, data duplication, and inconsistencies.
Future-Proof Scalability
Whether you’re a startup connecting three tools or an enterprise with hundreds of platforms, xvif’s scales without the need for extensive reconfiguration.
Plug-and-Play Connectivity
From CRMs and ERPs to IoT devices and AI modules, xvif comes equipped with a library of prebuilt connectors for faster onboarding.
Use Cases: Where XVIF Truly Shines
XVIF isn’t limited to one industry or function—its flexibility makes it a perfect fit across a broad range of scenarios:
Healthcare:
Integrate patient records, lab results, and billing systems across clinics and hospitals without compromising privacy or compliance.
Retail & E-commerce:
Connect POS systems, inventory tools, and customer data platforms to deliver seamless omnichannel experiences.
Enterprise IT:
Link HR, finance, operations, and customer service tools to build a unified, efficient digital workspace.
IoT & Smart Systems:
Bring together data from sensors, devices, and control centers in real-time—essential for automation and smart infrastructure.
Challenges and Considerations
While the xvif framework offers a robust set of tools, it’s not without its challenges:
- Learning Curve: Although user-friendly, some customization might require in-depth understanding of APIs and protocols.
- Security Measures: Since xvif deals with sensitive data transfers, robust encryption and access control mechanisms are critical.
- Vendor Lock-in Risk: Choosing the wrong version or vendor-locked implementation of xvif’s can make switching or scaling harder later.
However, many of these risks are mitigated by selecting open-source xvif’s implementations or enterprise solutions that follow modular, open standards.
XVIF Innovations: What’s New?
The world of xvif is constantly evolving, with recent innovations enhancing its capabilities even further:
- AI-Driven Mapping: Automating the mapping of data fields between systems using machine learning to reduce human error.
- No-Code Dashboards: Enabling business users to set up and monitor integrations without touching a single line of code.
- Edge Computing Support: Extending integration capabilities to edge devices, making xvif ideal for real-time analytics in remote or low-latency environments.
These advancements continue to position xvif as not just a connector, but a catalyst for digital transformation.
The Future of XVIF: What Lies Ahead?
The demand for system integration is only going to grow, especially with the rise of AI, big data, and decentralized platforms. Experts predict xvif will play a pivotal role in shaping the future of:
- Composable Enterprises where systems are assembled like Lego bricks.
- AI Orchestration where machine learning models talk to various data sources effortlessly.
- Decentralized Networks where virtual frameworks stitch together microservices spread across the globe.
XVIF’s adaptability and vision make it an essential tool in the evolving IT landscape.
Final Thoughts: Embracing the XVIF Era
As businesses move beyond isolated systems toward fully integrated digital ecosystems, xvif offers a clear path forward. It’s not about replacing what works—it’s about enhancing it with intelligence, agility, and scalability. For companies aiming to innovate without disruption, xvif’s is a powerful ally.
The journey toward digital cohesion doesn’t have to be messy or expensive. With xvif, it can be smart, seamless, and surprisingly smooth.
Loved this post? You’ll find even more just like it on our blog!
- GENERAL1 month ago
5 Factors That Affect Tattoo Removal Success
- ENTERTAINMENT2 months ago
Exploring the Kristen Archives: A Treasure Trove of Erotica and More
- LIFESTYLE6 months ago
The Disciplinary Wives Club: Spanking for Love, Not Punishment
- TECHNOLOGY5 months ago
Blog Arcy Art: Where Architecture Meets Art
- LIFESTYLE5 days ago
Who Is Sandra Orlow?
- ENTERTAINMENT7 months ago
The Ultimate Guide to Shillong Teer Hit Number: How to Predict Your Next Win
- LIFESTYLE3 months ago
Berniece Julien: The Private Life of Tyson Beckford’s Partner
- Uncategorized12 months ago
Conrad Fisher Transformation: From Top Student to Troubled Soul