Uncategorized
Common Problems and Solutions of Hand Stretch Film
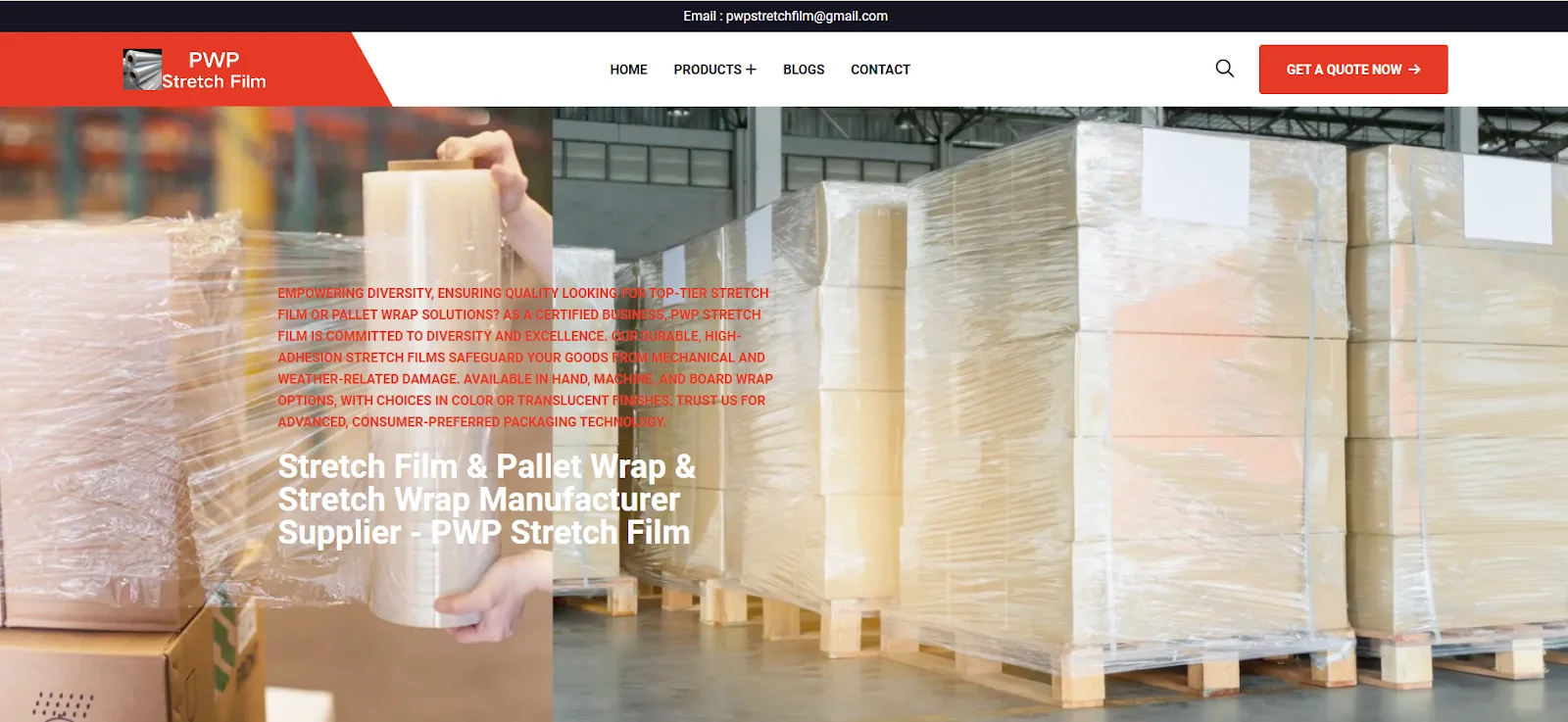
Hand stretch film is a widely used solution for securing goods during transportation and storage. However, businesses often encounter a few common issues with its use. Understanding the root causes of these problems and knowing how to address them can ensure more efficient packaging and reduce material waste. PWP Stretch Film, a trusted brand in the industry, offers high-quality solutions designed to mitigate these challenges. Here are some common problems with hand stretch film, along with their solutions, which PWP Stretch Film effectively addresses:
Film Breakage or Tearing
Problem: One of the most common issues with stretch film is breakage or tearing, which can occur during the wrapping process. This problem is typically caused by using film with insufficient strength for the load being wrapped. Film breakage can also be due to rough handling, high tension, or incorrect gauge choice.
Causes:
- Incorrect Gauge: Using a film with too low of a gauge for heavy or irregularly shaped loads can lead to breakage of Common problems.
- Sharp Edges: Items with sharp edges can puncture or tear the film.
- Excessive Tension: Stretching the film too tightly can cause it to snap.
Solution:
- Select the Right Gauge: Choose a stretch film with an appropriate gauge for the load. For lighter loads, an 80-gauge film may suffice, while heavier or more irregular loads may require a 90-110 gauge film.
- Use Blown Stretch Film: Blown stretch film is often more resistant to punctures and tears compared to cast film, making it a good option for handling sharp-edged or heavier items.
- Proper Handling: Ensure the film is dispensed correctly, and avoid over-stretching or applying excessive tension during the wrapping process of Common problems.
Difficulty in Handling
Problem: Operators may experience fatigue or difficulty handling the stretch film, especially when wrapping large or heavy pallets. This can lead to inconsistent application and reduce packaging efficiency.
Causes:
- Heavy Rolls: Larger rolls of stretch film, especially machine stretch film, can be cumbersome and difficult to manage manually.
- Low-quality Film: Poorly made or flimsy stretch films can be harder to apply, requiring more effort to achieve the same load retention of Common problems.
Solution:
- Pre-Stretched Films: Pre-stretched films are a great solution for reducing operator fatigue. These films are already stretched during manufacturing, which means less effort is required to apply them. They also offer consistent performance and help reduce material waste.
- Use a Film Dispenser: Hand stretch film dispensers can help operators apply film with more ease and precision. These devices provide better grip and control, reducing fatigue and improving wrapping consistency.
- Smaller Rolls: If your business does not require wrapping large pallets, consider opting for smaller rolls or narrower widths. They are easier to manage and can be more cost-effective for smaller operations.
Incorrect Stretch Ratio
Problem: An incorrect stretch ratio can lead to inefficiency in the wrapping process. If the stretch ratio is too low, more material will be used to secure a load than necessary, leading to wasted film. On the other hand, if the ratio is too high, the film may not provide adequate load retention, making the packaging less secure of Common problems.
Causes:
- Wrong Film Choice: Choosing a stretch film with an inappropriate stretch ratio for the product being wrapped can cause inefficiency. Films with a high stretch ratio (e.g., 250-300%) may be used for lighter loads, while heavier products require films with a lower stretch ratio.
- Inconsistent Application: If operators stretch the film too much or too little, it can affect the final load containment, leading to under-stretching or over-stretching.
Solution:
- Select the Right Stretch Ratio: The key to choosing the right stretch ratio is to consider the type of product being wrapped. For heavy-duty items or irregular shapes, a lower stretch ratio (150-200%) may be more suitable, as it offers greater control and better containment. For lighter loads, a higher stretch ratio (up to 300%) can maximize efficiency and reduce material use.
- Training for Operators: Proper training on how to handle the film and achieve the optimal stretch is essential. Ensure that operators are familiar with the ideal stretch ratio for the products they are wrapping to avoid excess material use or under-secured loads.
Environmental Concerns and Waste
Problem: Environmental impact and film waste are growing concerns in industries that use large amounts of stretch film. The non-biodegradable nature of plastic stretch films, as well as overuse of material, can contribute to environmental pollution and increase operational costs.
Causes:
- Excessive Material Use: Improper stretch ratios or film application techniques can result in overuse of stretch film.
- Non-Eco-friendly Film Options: Many stretch films are made from petroleum-based plastics, which are not biodegradable.
Solution:
- Eco-friendly Options: Look for suppliers that offer biodegradable stretch film or recycled films. Some VCI stretch film are made from recycled materials, making them an eco-friendly choice for businesses that need corrosion protection without compromising sustainability.
- Reduce Waste: Opt for films with higher stretch ratios to reduce the amount of material used per load. Pre-stretched films are also more efficient, as they provide maximum coverage with less material of Common problems.
- Film Optimization: Invest in stretch film dispensers that allow precise film application to minimize waste. Additionally, reevaluate your wrapping process to ensure you’re using the right amount of film for each type of load.
Uncategorized
Reimagining Home: The Diịhc Revolution
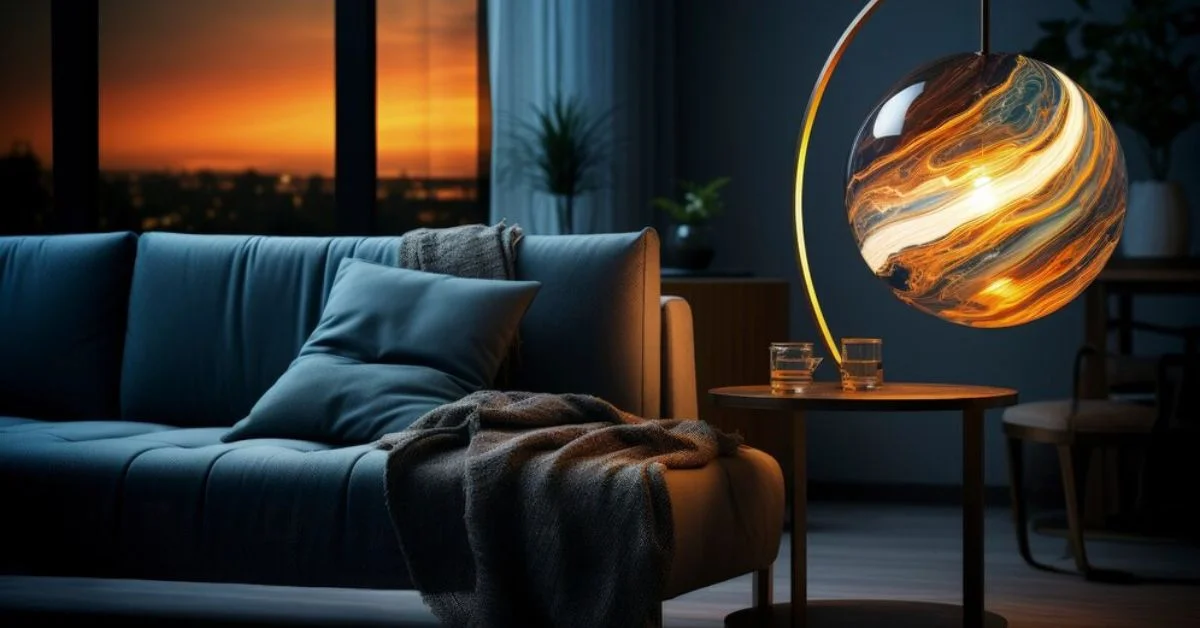
Introduction to the Diịhc (Decorative Intelligent Home Console)
In recent years, the world of home decor has experienced a significant paradigm shift with the introduction of the Diịhc (Decorative Intelligent Home Console). This innovative technology has revolutionized the way we perceive and interact with our living spaces, blending seamlessly with traditional decor while ushering in a new era of convenience and sophistication.
Traditional Home Decor vs. Diịhc Revolution
Incorporating Technology
Traditionally, home decor has been focused on aesthetics and functionality, with little emphasis on technological integration. However, the emergence of the Diịhc has transformed this landscape by seamlessly integrating cutting-edge technology into every aspect of home design.
Personalization and Adaptability
One of the most striking features of the Diịhc is its ability to personalize and adapt to the needs and preferences of individual homeowners. Through advanced AI algorithms, the Diịhc learns and anticipates user behavior, adjusting everything from lighting and temperature to music and ambiance to create the perfect atmosphere.
How Diịhc Has Changed Interior Design
Smart Furniture and Appliances
With the Diịhc, traditional furniture and appliances are transformed into intelligent, interconnected devices that communicate seamlessly with each other. From smart thermostats and lighting systems to automated blinds and entertainment centers, every aspect of the home becomes optimized for comfort and convenience.
Mood Lighting and Ambiance Control
Gone are the days of static lighting schemes. With the Diịhc, homeowners have unprecedented control over the ambiance of their living spaces. Whether they desire a cozy evening glow or a vibrant party atmosphere, the Diịhc can instantly adjust the lighting to suit any occasion.
ALSO READ: CORSETURI CRAZE: REVIVING CLASSIC ELEGANCE
The Impact of Diịhc on Lifestyle
Increased Convenience and Efficiency
One of the most immediate benefits of the Diịh,c is the enhanced convenience it brings to everyday life. With voice commands or simple gestures, homeowners can control various aspects of their home environment, eliminating the need for manual adjustments and streamlining daily routines.
Enhanced Comfort and Well-being
Beyond convenience, the Diịhc also contributes to enhanced comfort and well-being. By optimizing factors such as lighting, temperature, and air quality, it creates a harmonious environment that promotes relaxation and productivity, fostering a greater sense of overall well-being.
Challenges and Considerations with Diịh,c Integration
Privacy Concerns
As with any connected technology, privacy concerns are a significant consideration with the Diịhc. While its advanced AI capabilities offer unparalleled convenience, they also raise questions about data security and personal privacy, requiring careful safeguards to protect user information.
Maintenance and Upkeep
Additionally, the integration of complex technology into the home introduces new maintenance and upkeep challenges. Regular updates and troubleshooting may be necessary to ensure the Diịh,c continues to operate smoothly, requiring homeowners to stay vigilant and proactive in its care.
ALSO READ: FLOWERS IN EVERYDAY LIFE: SIMPLE PLEASURES THAT BRING HAPPINESS
Future Trends in Home Decor with Diịhc
Integration with Virtual Reality
Looking ahead, the integration of the Diịh,c with virtual reality presents exciting possibilities for the future of home decor. Imagine being able to virtually design and visualize your living space in real-time, experimenting with different layouts, colors, and styles before making any physical changes.
Sustainability and Eco-Friendly Features
Furthermore, future iterations of the Diịhc are likely to prioritize sustainability and eco-friendly features, aligning with growing consumer demand for environmentally conscious products. From energy-efficient appliances to sustainable materials, the Diịh,c will play a crucial role in creating more sustainable and eco-friendly homes.
Conclusion: Embracing the Future of Home Decor with Diịhc
In conclusion, the Diịhc represents a paradigm shift in the world of home decor, redefining our understanding of what it means to create a truly intelligent and interconnected living space. By seamlessly blending technology with traditional design principles, it offers unparalleled convenience, comfort, and customization, transforming the way we live and interact with our homes. As we continue to embrace the possibilities of this groundbreaking technology, the future of home decor has never looked brighter.
ALSO READ: TIPS TO HIRE LUX LIMO IN NEW YORK FOR YOUR BACHELORETTE CELEBRATION
FAQs
Can the Diịhc be integrated into existing homes, or is it only suitable for new construction?
The Diịhc can be seamlessly integrated into both existing homes and new construction projects, making it accessible to a wide range of homeowners.
How does the Diịhc prioritize user privacy and data security?
The Diịhc employs advanced encryption and authentication protocols to safeguard user data and ensure privacy protection at all times.
What happens if there’s a power outage? Does the Diịh,c lose its settings and preferences?
The Diịh,c features built-in backup systems to preserve settings and preferences in the event of a power outage, ensuring a seamless user experience.
Can multiple users customize their preferences on the same Diịhc console?
Yes, the Diịh,c supports multiple user profiles, allowing each member of the household to customize their preferences and settings independently.
Are there any ongoing subscription fees or additional costs associated with using the Diịhc?
No, once installed, the Diịh,c operates independently without any ongoing subscription fees or hidden costs, providing a hassle-free user experience.
Uncategorized
zf 6hp generation 2 solenoid diagram
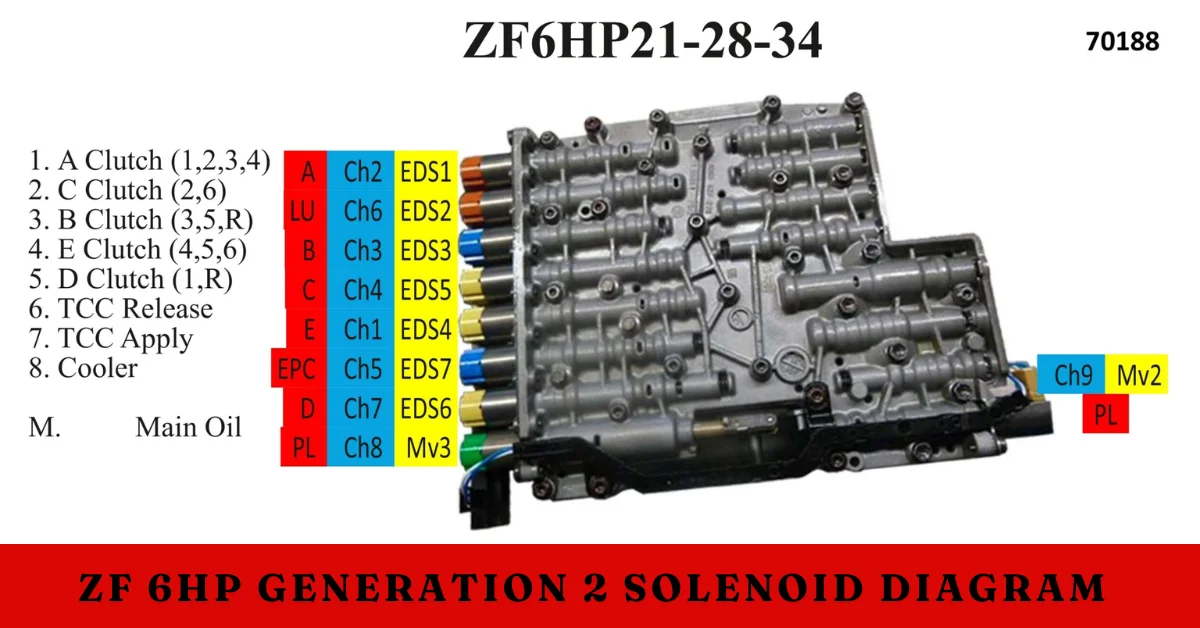
Welcome to the inner workings of the zf 6hp generation 2 solenoid diagram transmission system, where solenoids play a crucial role in ensuring smooth gear shifts and optimal performance. If you’ve ever wondered what lies beneath the surface of your vehicle’s transmission, buckle up as we dive into the intricate world of solenoid diagrams. Get ready to unravel the secrets behind this essential component and learn how to decode its language for a better understanding of your ZF 6HP Generation 2 transmission!
Explanation of solenoids and their role in the transmission
Solenoids are small but mighty components within the intricate system of a transmission. These electromechanical devices play a crucial role in controlling the flow of fluid and regulating gear shifts. When an electrical signal is sent to a solenoid, it acts as a valve, either allowing or blocking the passage of hydraulic fluid that influences different clutch packs and bands in the transmission. Essentially, solenoids serve as the traffic controllers of your vehicle’s gears, ensuring smooth transitions between them.
Without properly functioning solenoids, your zf 6hp generation 2 transmission may experience issues like harsh shifting, delayed engagement, or even slipping gears. Understanding how these solenoids work can help you diagnose problems early on and prevent costly repairs down the line. So next time you’re cruising down the road effortlessly changing gears, give thanks to these tiny yet powerful devices silently working behind the scenes!
Components of the zf 6hp generation 2 solenoid diagram
The components of the ZF 6HP Generation 2 solenoid diagram play a crucial role in the transmission system. Understanding these elements is key to ensuring smooth operation and optimal performance of your vehicle.
Within the diagram, you’ll find various solenoids, each responsible for specific functions within the transmission. These small but mighty devices control fluid flow, pressure, and gear engagement, allowing for seamless shifting between gears.
Additionally, the solenoid diagram also includes connectors and wiring that facilitate communication between the electronic control unit (ECU) and the solenoids themselves. This intricate network ensures precise coordination and timing during gear changes.
By familiarizing yourself with these components and their interplay within the system, you can better comprehend how your ZF 6HP Generation 2 transmission operates. This knowledge empowers you to identify potential issues early on and take proactive steps to maintain its efficiency over time.
Step-by-step guide on how to read the solenoid diagram
When it comes to understanding the zf 6hp generation 2 solenoid diagram, a step-by-step approach can make all the difference. Let’s dive into decoding this essential component of your transmission system.
Familiarize yourself with the layout of the diagram. Each solenoid is represented by a symbol that indicates its function within the transmission.
Next, identify each solenoid and its corresponding location on the diagram. This will help you pinpoint any issues or abnormalities when troubleshooting.
Pay attention to the connections between solenoids as they interact with one another to regulate fluid flow and gear shifting in your zf 6hp generation 2 transmission.
Utilize any key or legend provided on the diagram to interpret different symbols or markings that may indicate specific functions or characteristics of the solenoids.
By following these steps carefully, you’ll be better equipped to read and understand the zf 6hp generation 2 solenoid diagram effectively.
Common issues with solenoids in the zf 6hp generation 2 transmission
Solenoids in the zf 6hp generation 2 transmission can encounter common issues that may affect the smooth operation of your vehicle. One prevalent problem is solenoid failure, which can lead to shifting issues or even complete transmission failure. When a solenoid becomes faulty, it may cause erratic gear changes, slipping gears, or harsh shifts.
Another issue that can arise with solenoids is electrical connectivity problems. This can result from corroded connectors or damaged wiring harnesses, leading to poor signal transmission between the control unit and the solenoids. Additionally, debris buildup within the solenoid valves could restrict fluid flow and hinder proper functioning.
It’s crucial to address these common solenoid issues promptly to prevent further damage to your zf 6hp generation 2 transmission. Regular maintenance and inspection of the solenoids can help identify potential problems early on and ensure optimal performance of your vehicle’s transmission system.
Troubleshooting tips for solenoid problems
Facing solenoid problems in your zf 6hp generation 2 transmission can be frustrating, but fear not – there are troubleshooting tips to help you navigate these issues.
Ensure that all electrical connections to the solenoids are secure and free of corrosion. A loose connection could be the root cause of the problem.
Next, check for any damaged wiring leading to the solenoids. Frayed or broken wires can disrupt the communication between the transmission control module and the solenoids.
If everything looks intact on the outside, consider performing a diagnostic scan using specialized equipment to pinpoint any internal solenoid malfunctions accurately.
If you still encounter issues after troubleshooting, it may be best to consult with a professional mechanic who has experience working with zf transmissions for further assistance in resolving solenoid problems effectively.
Conclusion and final thoughts on maintaining your zf
Understanding the zf 6hp generation 2 solenoid diagram is crucial for maintaining your transmission’s optimal performance. By familiarizing yourself with the components and knowing how to read the diagram, you can troubleshoot any solenoid issues effectively. Remember to follow the steps outlined in this guide and keep up with regular maintenance to ensure your zf transmission operates smoothly for years to come. Take care of your vehicle, and it will take care of you on the road!
FAQs
What is a “ZF 6HP Generation 2 Solenoid Diagram”?
The ZF 6HP Generation 2 Solenoid Diagram illustrates the layout and function of solenoids within the transmission, crucial for smooth gear shifts and overall performance.
Why are solenoids important in the ZF 6HP Generation 2 transmission?
Solenoids act as valves controlling fluid flow, aiding in gear engagement and shifting. They ensure precise transmission operation, impacting overall vehicle performance.
How do I read the ZF 6HP Generation 2 solenoid diagram?
Start by familiarizing yourself with the diagram’s layout and symbols. Identify each solenoid’s function and location, using any provided legend for clarity on their roles in the transmission system.
What are common issues with solenoids in the ZF 6HP Generation 2 transmission?
Common issues include solenoid failure causing erratic shifts, electrical connectivity problems due to corrosion or wiring damage, and debris buildup affecting fluid flow and gear changes.
How can I troubleshoot solenoid problems in my ZF 6HP Generation 2 transmission?
Ensure secure electrical connections and inspect wiring for damage. Use diagnostic tools to pinpoint internal solenoid malfunctions accurately. For persistent issues, consult a qualified mechanic familiar with ZF transmissions.
Uncategorized
ultimate guide to new entertainment trends lumolog
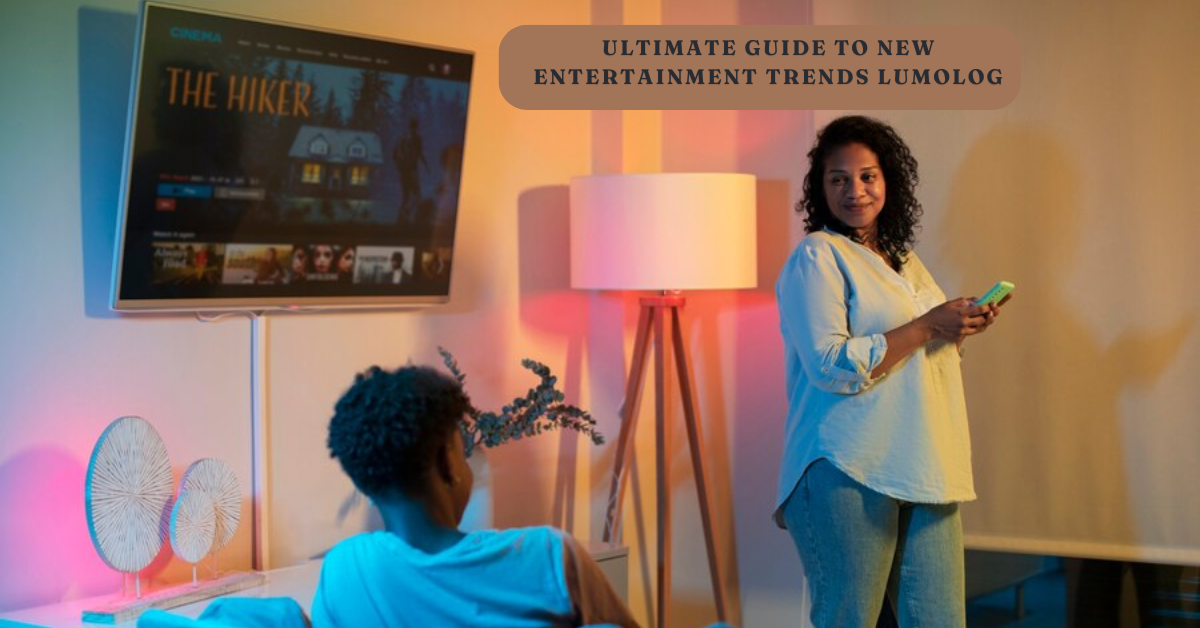
Welcome to the ultimate guide on the latest entertainment trends shaking up the industry: LumoLog! Get ready to dive into a world where virtual experiences, personalized interactions, and cutting-edge technology collide to redefine how we entertain ourselves. Join us as we explore the exciting evolution of entertainment in this digital age and discover how LumoLog is at the forefront of this thrilling transformation. Let’s embark on a journey together and uncover what lies ahead in the realm of new entertainment trends!
What Is LumoLog and its Benefits
LumoLog is a cutting-edge technology platform that revolutionizes the way we experience entertainment. By seamlessly blending virtual and physical elements, LumoLog creates immersive experiences unlike anything you’ve seen before.
One of the key benefits of LumoLog is its ability to transport users into new worlds through interactive storytelling and augmented reality. Imagine being able to step into your favorite movie or video game and become part of the action – that’s the power of LumoLog.
Furthermore, LumoLog enhances social interactions by allowing users to connect with friends and family in virtual spaces, fostering a sense of community even when physically apart. Whether attending a live concert together or exploring a digital museum, LumoLog brings people closer together through shared experiences.
LumoLog opens up endless possibilities for entertainment, offering unique and engaging ways to explore art, culture, gaming, and more. Get ready to dive into a world where imagination knows no bounds with LumoLog at your fingertips.
The Rise of Virtual Events and Experiences
With the world rapidly shifting towards digital experiences, virtual events have surged in popularity. People now have the opportunity to attend concerts, conferences, and even weddings from the comfort of their own homes.
Virtual reality technology allows participants to immerse themselves in a completely different environment, creating an unforgettable experience without leaving their living room. From interactive games to live streams of exclusive events, virtual platforms offer endless possibilities for entertainment.
Moreover, businesses are embracing virtual events as a cost-effective way to reach larger audiences while providing a unique and engaging experience. Attendees can network with others, participate in Q&A sessions, and explore virtual exhibits all within a few clicks.
The rise of virtual events has revolutionized how we connect with one another and consume entertainment. As technology continues to advance, the potential for innovative and immersive experiences is limitless.
The Influence of Social Media on Entertainment Trends
In today’s digital age, social media plays a pivotal role in shaping entertainment trends. Platforms like Instagram, TikTok, and Twitter have become powerful tools for creators to reach and engage with audiences on a global scale.
Through viral challenges, hashtag campaigns, and influencer collaborations, social media has the ability to catapult songs, movies, TV shows, and even niche hobbies into mainstream popularity within hours.
The instant feedback loop of likes, shares, comments fuels the hype around new releases and events. Fans feel more connected to their favorite artists or franchises through behind-the-scenes glimpses and interactive content shared on social platforms.
Moreover, social media algorithms constantly evolve to tailor personalized recommendations based on users’ interests and behaviors. This level of customization enhances the overall entertainment experience by delivering content that resonates with individual preferences.
As we move forward in this dynamic landscape where trends can emerge overnight and fizzle out just as quickly- staying attuned to the pulse of social media is essential for anyone looking to stay ahead in the ever-evolving world of entertainment.
The Power of Personalized and Interactive Experiences
Personalized and interactive experiences are revolutionizing the entertainment industry, offering audiences a new level of engagement and immersion. By tailoring content to individual preferences, creators can craft unique journeys for each participant, making them feel seen and valued.
Interactive elements allow users to actively participate in the narrative, blurring the lines between observer and protagonist. Whether it’s choosing their own adventure or controlling outcomes through real-time interactions, these experiences empower viewers to shape their own entertainment destiny.
From personalized recommendations on streaming platforms to immersive live events where spectators influence the storyline, customized experiences enhance enjoyment by catering to personal tastes and interests. Gone are the days of passive consumption – now audiences crave dynamic engagements that make them an integral part of the action.
As technology continues to advance, we can expect even more innovative ways for individuals to interact with entertainment content. The power of personalization lies in its ability to forge deeper connections between creators and consumers, fostering a sense of belonging and appreciation within this rapidly evolving landscape.
From Gaming to AR/VR: Exploring the Future of Entertainment
As we delve into the realm of entertainment, one cannot ignore the rapid evolution that gaming has undergone in recent years. From simple pixels on a screen to immersive worlds and interactive experiences, gaming has paved the way for what lies ahead.
Enter augmented reality (AR) and virtual reality (VR), two technologies reshaping how we engage with entertainment. AR overlays digital content onto our physical surroundings, while VR transports us to entirely new realms through headsets and sensory feedback.
The future of entertainment is undoubtedly intertwined with these emerging technologies. Imagine attending a concert from the comfort of your living room or exploring ancient ruins through a VR headset – the possibilities are endless.
From enhancing storytelling capabilities to revolutionizing education and training, AR/VR is poised to redefine how we consume content and interact with our environment. As we embrace this exciting shift, one thing remains clear: The future of entertainment is boundless and full of potential.
Incorporating LumoLog into Your Next Event or Experience
Planning your next event or experience and looking to add a touch of innovation and excitement? Look no further than LumoLog. By incorporating LumoLog into your upcoming gathering, you can elevate the entertainment factor and create unforgettable memories for your attendees.
Imagine immersing your guests in a virtual world where they can interact with each other in real-time, breaking down barriers and fostering connections like never before. With LumoLog, the possibilities are endless – from hosting virtual concerts to organizing interactive workshops that engage participants on a whole new level.
Whether you’re organizing a corporate event, launching a product, or simply throwing a party, integrating LumoLog technology can take your experience to the next level. The seamless blend of virtual reality elements with real-world interactions will leave everyone talking long after the event has ended.
So why stick to traditional event formats when you can harness the power of LumoLog to captivate your audience and create an immersive experience that sets you apart from the rest? Get ready to revolutionize your events with Lumolog!
Conclusion: Embracing the Evolution
As we navigate through the ever-evolving landscape of entertainment trends, LumoLog stands out as a catalyst for innovation and engagement. By embracing personalized experiences, virtual events, interactive content, and cutting-edge technologies like AR/VR, we are witnessing a transformation in how we consume entertainment.
The future of entertainment is bright with endless possibilities waiting to be explored. By incorporating LumoLog into your next event or experience, you can elevate it to new heights and create unforgettable memories for your audience.
So let’s embrace this evolution together. Let’s push the boundaries of creativity and imagination. Let’s ride the wave of new entertainment trends powered by LumoLog and shape the future of entertainment for generations to come. The time to revolutionize how we entertain is now – are you ready to join the journey?
FAQs
What is “Ultimate Guide to New Entertainment Trends LumoLog”?
The Ultimate Guide to New Entertainment Trends LumoLog explores cutting-edge technology blending virtual experiences and interactive storytelling to redefine entertainment.
How does LumoLog revolutionize entertainment?
LumoLog integrates virtual and physical elements to create immersive experiences, enhancing social interactions and offering new ways to explore art, culture, and gaming.
Why are virtual events gaining popularity?
Virtual events offer convenience and accessibility, allowing participants to attend from anywhere. They provide immersive experiences through virtual reality, revolutionizing how we connect and engage.
How does social media influence entertainment trends?
Social media platforms amplify entertainment trends through viral content and influencer collaborations, shaping global pop culture and enhancing fan engagement with personalized interactions.
What role do AR/VR technologies play in the future of entertainment?
AR/VR technologies transform entertainment by creating interactive environments and enhancing storytelling. They offer limitless possibilities, from virtual concerts to educational experiences.
- GENERAL2 months ago
5 Factors That Affect Tattoo Removal Success
- ENTERTAINMENT3 days ago
Exploring the Kristen Archives: A Treasure Trove of Erotica and More
- LIFESTYLE6 months ago
The Disciplinary Wives Club: Spanking for Love, Not Punishment
- TECHNOLOGY6 months ago
Blog Arcy Art: Where Architecture Meets Art
- ENTERTAINMENT8 months ago
The Ultimate Guide to Shillong Teer Hit Number: How to Predict Your Next Win
- LIFESTYLE2 weeks ago
Who Is Sandra Orlow?
- LIFESTYLE3 months ago
Berniece Julien: The Private Life of Tyson Beckford’s Partner
- Uncategorized1 year ago
Conrad Fisher Transformation: From Top Student to Troubled Soul