TECHNOLOGY
The Benefits of Custom Sheet Metal Fabrication for Industrial Applications
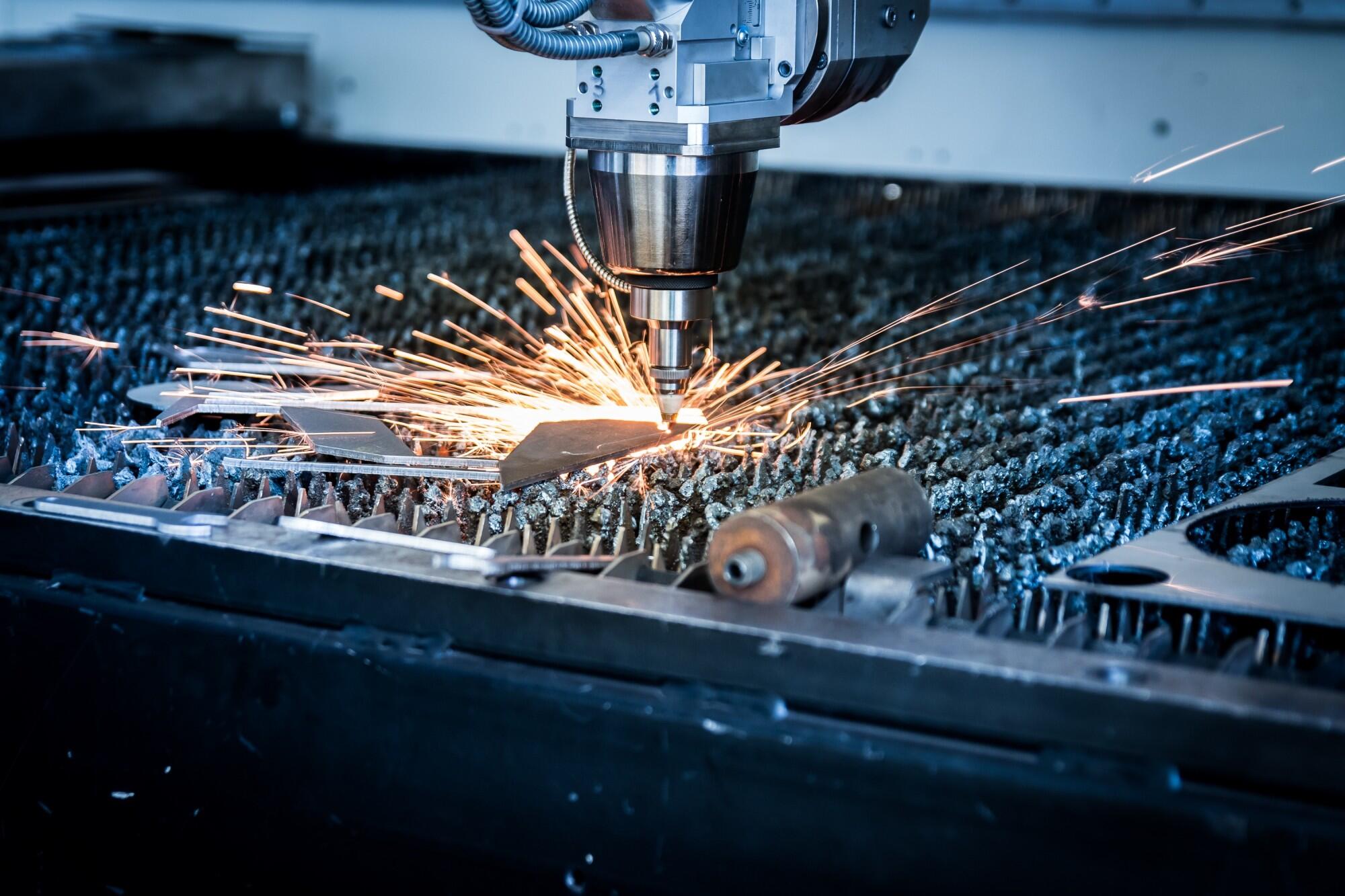
The success of industrial projects often depends on precision, durability, and efficiency – and that’s where custom sheet metal fabrication shines. Unlike standard parts, custom solutions are designed to meet unique requirements, ensuring components fit perfectly and perform reliably.
Custom sheet metal fabrication enhances the versatility of traditional sheet metal processes by tailoring designs to specific industrial needs. This level of customization is essential for industries like construction, manufacturing, and energy, where standard options often fall short.
By investing in custom sheet metal fabrication, businesses can enjoy precise, durable, and efficient solutions that improve performance and reduce errors.
In this blog post, we will look at the importance of custom sheet metal fabrication, its many benefits, and how it serves diverse industries with tailored solutions that stand up to real-world challenges. Let’s get started.
What Is Custom Sheet Metal Fabrication?
Essentially, custom sheet metal fabrication is the process of designing, cutting, shaping, and assembling sheet metal into specific parts or products according to precise specifications.
Unlike standard sheet metal fabrication, which typically uses pre-designed templates or mass-produced components, custom fabrication tailors the process to meet unique requirements for each project.
This method allows for greater flexibility in design, enabling businesses to create products that perfectly fit their industrial needs. Custom sheet metal fabrication can be used to produce a wide variety of items, including:
- Machine parts
- Structural components
- Enclosures
The materials used in custom fabrication vary, with common options including steel, aluminum, and copper, each chosen based on strength, durability, and corrosion resistance.
By utilizing advanced technologies like Computer-Aided Design (CAD) and CNC (Computer Numerical Control) machines, custom fabrication ensures precision and quality in every project, providing tailored solutions for industries like automotive, aerospace, construction, and electronics.
Core Benefits of Custom Sheet Metal Fabrication
Custom sheet metal fabrication offers a range of advantages that make it a popular choice for industrial applications. The ability to tailor designs precisely to meet specific needs ensures that products are both efficient and durable. Below, we’ll highlight some of the core benefits that make custom sheet metal fabrication a valuable solution for various industries.
Precision and Accuracy
Firstly, one of the main benefits of custom sheet metal fabrication is the precision it offers.
As mentioned above, with the use of advanced tools like CAD software and CNC machinery, fabricators can create highly accurate components that meet exact specifications. This ensures that parts fit perfectly and function as intended, reducing the risk of errors and costly reworks.
For industries like aerospace and electronics, where tight tolerances are critical, precision is essential to ensure reliability and performance.
Strength and Durability
Custom sheet metal fabrication allows businesses to select the most suitable materials for their products, which enhances the strength and durability of the final product. Materials such as steel, aluminum, and stainless steel offer exceptional resistance to:
- Wear
- Corrosion
- Stress
This makes custom-fabricated components ideal for harsh environments where durability is a must, such as in the construction, automotive, and manufacturing sectors.
Whether it’s structural supports or machine parts, custom fabrication can produce items that withstand the test of time.
Tailored Design Flexibility
Another significant advantage of custom fabrication is the flexibility it provides in design. Traditional mass production often limits the ability to modify designs to meet specific needs, but custom fabrication offers endless possibilities.
Manufacturers can customize the shape, size, and features of each part, ensuring that every component perfectly fits the required function. This is especially beneficial for industries that require specialized components or products that cannot be found through off-the-shelf solutions.
All in all, custom fabrication enables businesses to push the boundaries of innovation by creating unique, functional, and high-performing parts.
Cost Efficiency Over Time
While custom fabrication might involve a higher initial cost compared to mass-produced parts, it can save money in the long run. Custom-fabricated components are designed to be more efficient, reducing the likelihood of wasted materials or the need for frequent replacements.
Additionally, custom parts are often more robust and reliable, which leads to fewer repairs and maintenance costs. Over time, the durability and precision of custom sheet metal fabrication can lead to a significant reduction in the overall cost of ownership. This is particularly true for industries with high-volume or long-lasting production runs.
Speed and Efficiency in Production
Custom sheet metal fabrication also improves the speed and efficiency of production. With modern fabrication techniques, it is possible to streamline the manufacturing process, ensuring that parts are produced quickly and accurately.
This is particularly valuable in industries where time-sensitive projects are common, such as in automotive or electronics manufacturing. The ability to quickly produce high-quality, customized components reduces downtime and allows businesses to meet deadlines without compromising on quality.
Sectors That Benefit From Custom Sheet Metal Fabrication
As we’ve noted, custom sheet metal fabrication is used in a wide variety of industries due to its flexibility, durability, and precision. From automotive to construction, businesses across different sectors rely on custom metal fabrication to meet their specific needs. Let’s consider some of the key industries that benefit from custom sheet metal fabrication.
Manufacturing
Undoubtedly, manufacturing is one of the largest sectors that benefit from custom sheet metal fabrication. In this industry, companies often need components that are designed to exact specifications to improve production processes.
Custom fabrication allows manufacturers to create machine parts, tools, and equipment that fit their unique requirements. It also ensures high-quality, durable parts that withstand the heavy demands of a manufacturing environment.
Automotive and Aerospace
The automotive and aerospace industries both require custom sheet metal fabrication for creating parts that are both lightweight and strong. In the automotive sector, custom metal fabrication is used for making:
- Body panels
- Frames
- Structural components
In aerospace, it’s crucial for building parts that meet strict safety and performance standards. The ability to design precise, tailored components ensures that vehicles and aircraft operate efficiently and safely, reducing weight while maintaining strength.
Construction
Custom sheet metal fabrication is also essential in the construction and infrastructure sectors for creating structural components like:
- Beams
- Supports
- Cladding
These parts must be designed to withstand weather conditions and provide long-lasting support for buildings and infrastructure projects.
Custom fabrication offers the flexibility to create parts that fit unique designs and meet specific regulatory standards, ensuring both functionality and durability in construction.
Electronics and Electrical Equipment
Custom sheet metal fabrication plays an important role in the electronics industry, particularly for creating protective enclosures and housings for sensitive electronic equipment. These custom enclosures protect internal components from dust, moisture, and physical damage while allowing for ventilation and ease of access.
Fabricating enclosures to exact specifications ensures that products remain functional and safe. This is especially important for sensitive electrical equipment used, for example, in communication, medical devices, and consumer electronics.
Energy
Lastly, in the energy sector, custom sheet metal fabrication is used to create components for power plants, renewable energy systems, and machinery. Fabricated parts like heat exchangers, tanks, and piping systems must be able to handle:
- High pressures
- Temperatures
- Corrosive environments
Custom fabrication ensures that these parts meet the specific requirements for safety, efficiency, and durability. All of this is essential in power generation and energy infrastructure.
The Custom Sheet Metal Fabrication Process
The custom sheet metal fabrication process involves several key steps, each contributing to the creation of high-quality, precision parts. Here’s an overview of the basic steps involved in custom sheet metal fabrication.
Design and Planning
The first step in the custom sheet metal fabrication process is design. Using CAD software, engineers and designers create a detailed blueprint of the part or product. This design includes measurements, shapes, and any specific features needed for the final product.
Once the design is finalized, it is carefully reviewed to ensure it meets the desired specifications and functional requirements. Proper planning at this stage helps avoid errors later in the process.
Material Selection
The next step is choosing the appropriate material for the job. The choice of material depends on the desired strength, durability, and environmental conditions the part will be exposed to. Some of the common materials used in custom sheet metal fabrication include:
- Steel
- Aluminum
- Stainless steel
- Copper
Each material has its own properties, such as resistance to corrosion or weight, which is why selecting the right material is crucial for the performance and longevity of the final product.
Cutting
Then, once the design and material are set, the next step is cutting the sheet metal into the required shape. There are several cutting methods used in custom sheet metal fabrication, such as:
- Laser metal cutting
- Water jet cutting
- Punching
Laser cutting is particularly popular for its precision, while water jet cutting is often used for thicker materials. The cutting method chosen depends on the complexity of the design and the material being used.
Shaping and Bending
After the metal is cut into the desired shape, the next step is shaping and bending. This is typically done using a press brake machine, which uses controlled pressure to bend the metal into the required angle or shape.
Shaping and bending allow for the creation of components like brackets, panels, or frames that will later be assembled. This stage is crucial for creating parts that need to fit specific dimensions or angles.
Welding and Assembly
Welding is often necessary to join metal pieces together, creating larger or more complex structures. There are different welding techniques, including MIG (Metal Inert Gas) welding and TIG (Tungsten Inert Gas) welding.
Each of these techniques are suitable for different materials and applications. After welding, the parts may be further assembled, adding other components or features like fasteners or brackets.
Finishing
Once the metal parts are fabricated, they often require finishing to ensure they are smooth, clean, and ready for use. This may involve processes such as grinding, polishing, or sandblasting to remove sharp edges and improve the surface quality.
Additionally, parts may be coated or painted to protect them from corrosion and wear, ensuring they last longer in harsh environments.
Quality Control and Testing
Finally, before the final product is shipped or used, it undergoes a series of quality control checks and tests. This ensures that all dimensions, tolerances, and features meet the design specifications. Common tests include checking for:
- Material strength
- Functionality
- Finish quality
Ensuring the product meets quality standards is crucial, as it guarantees the product’s durability, reliability, and overall performance.
Cost Considerations in Custom Fabrication
Now, when planning for custom sheet metal fabrication, understanding the cost factors is key. The choice of material significantly affects costs, as metals like stainless steel or aluminum are priced based on their durability and properties. Complex designs or intricate features may also require advanced machinery and skilled labor, increasing expenses.
The size of the order impacts costs, as larger quantities typically lower the price per unit thanks to economies of scale. Additionally, processes like welding, finishing, and coating can add to the total cost.
While the initial expense may be higher, custom sheet metal fabrication offers long-term value through durability and precision.
Challenges in Custom Sheet Metal Fabrication
Finally, it’s important to note that custom sheet metal fabrication presents challenges such as:
- Material selection
- Achieving precision
- Managing costs
Choosing the wrong material can lead to performance issues or increased expenses, so it’s important to select metals suited to the application. Maintaining tight tolerances can also be difficult, especially with complex designs, but advanced machinery like CNC equipment ensures accuracy.
Another challenge is balancing cost and quality, and working with an experienced fabricator can help optimize processes and reduce waste. By addressing these challenges with careful planning and the right tools, businesses can achieve reliable, high-quality custom sheet metal products.
Guide to Custom Sheet Metal Projects
To sum up, custom sheet metal fabrication offers unmatched precision and flexibility for industrial applications. By investing in custom metal designs, businesses can create durable and efficient components tailored to their needs. While challenges exist, working with experienced fabricators ensures high-quality results.
The bottom line is that choosing custom sheet metal solutions provides long-term value, making it a smart choice for industries seeking reliability and performance. Like this blog post? Then check out our other articles on a range of topics.
TECHNOLOGY
Peúgo Decoded: Your Ultimate Guide
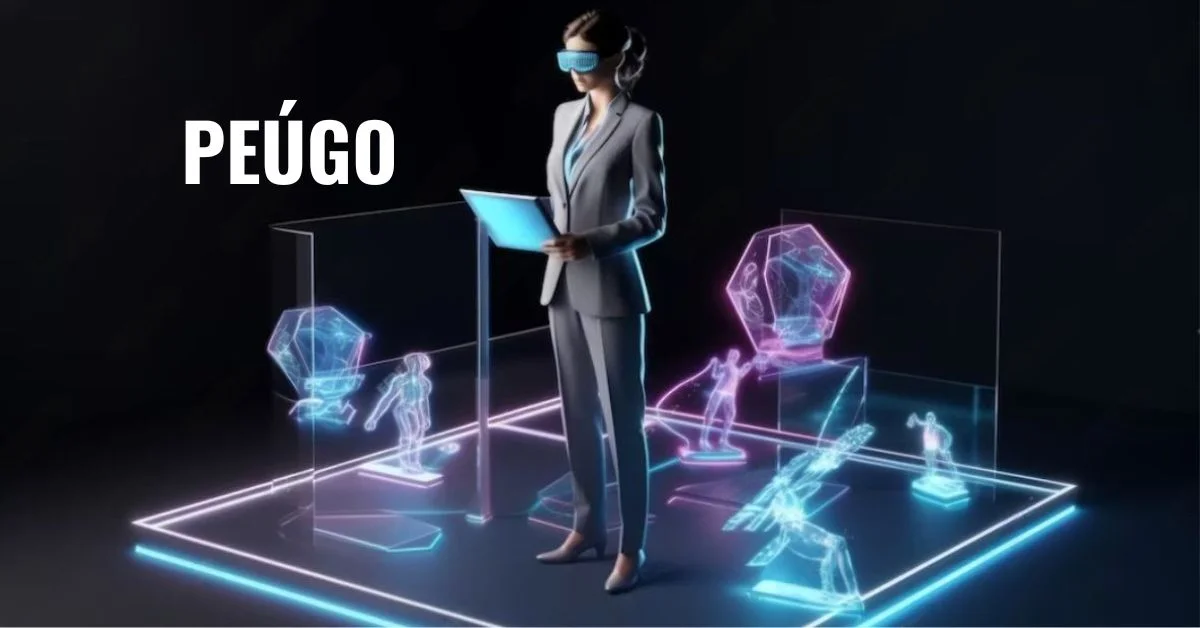
Introduction to Peúgo
In today’s rapidly evolving technological landscape, new innovations continue to emerge, revolutionizing the way we work and interact with digital platforms. Among these innovations is Peúgo, a cutting-edge solution that has been gaining significant traction in various industries. But what exactly is Peúgo, and why is it generating so much buzz? Let’s delve into the intricacies of this groundbreaking technology.
Origins and History
– Early Development
Peúgo traces its origins back to the early 21st century when a team of visionary developers set out to create a versatile and efficient solution to streamline digital processes.
– Evolution over Time
Since its inception, Peúgo has undergone significant evolution, incorporating advanced algorithms and functionalities to meet the ever-changing demands of modern businesses and consumers.
Understanding Peúgo: Definition and Concept
At its core, Peúgo can be defined as a comprehensive software platform designed to enhance productivity, efficiency, and collaboration within organizations. Its intuitive interface and robust features make it an indispensable tool for optimizing workflow management and achieving operational excellence.
ALSO READ: EVERYTHING ABOUT XATPES
Key Features and Characteristics
– Functionality
Peúgo boasts a wide array of features, including task automation, real-time analytics, and seamless integration with existing systems. Its user-friendly interface empowers users to accomplish tasks with ease, resulting in enhanced productivity and performance.
– Usability
One of the standout characteristics of Peúgo is its unparalleled usability. Whether you’re a seasoned professional or a novice user, navigating the platform is intuitive and straightforward, allowing for seamless adoption and implementation across organizations of all sizes.
ALSO READ: DECODING THE ENIGMA: U231748506 UNVEILED
Applications of Peúgo
– Industry Use Cases
From finance and healthcare to manufacturing and retail, Peúgo finds applications across a diverse range of industries. Its versatility and scalability make it a valuable asset for optimizing processes, driving innovation, and gaining a competitive edge in today’s digital landscape.
– Consumer Applications
In addition to its enterprise applications, Peú,go also caters to individual consumers, offering personalized solutions for managing tasks, organizing schedules, and enhancing overall productivity.
Advantages of Peúgo
– Efficiency
By automating repetitive tasks and streamlining workflows, Peú,go enables organizations to operate more efficiently, freeing up valuable time and resources that can be allocated to more strategic initiatives.
– Cost-effectiveness
The cost-effectiveness of Peú,go is another significant advantage, as it eliminates the need for multiple disparate solutions and reduces overhead costs associated with manual processes.
ALSO READ: BOLTBÓL: SHAPING THE FUTURE OF INNOVATION
Challenges and Limitations
– Technical Constraints
Despite its numerous benefits, Peúgo is not without its challenges. Technical constraints such as compatibility issues and system integration complexities may pose obstacles during implementation.
– Adoption Issues
Furthermore, widespread adoption of Peúgo may be hindered by resistance to change and the need for comprehensive training programs to familiarize users with its functionalities.
Peúgo vs. Competitors
– Comparative Analysis
In comparison to its competitors, Peú,go stands out for its intuitive interface, robust feature set, and scalability. Its ability to seamlessly integrate with existing systems gives it a competitive edge in the market.
ALSO READ: CRACKING THE CODE: A COMPREHENSIVE GUIDE TO 06SHJ06
Future Prospects and Trends
– Emerging Technologies
Looking ahead, the future of Peú,go is bright, with advancements in artificial intelligence and machine learning poised to further enhance its capabilities and drive innovation in the field of workflow management.
– Market Predictions
Analysts predict steady growth for the Peú,go market, fueled by increasing demand for digital transformation solutions and the growing emphasis on efficiency and productivity across industries.
ALSO READ: TECH DEMIS: NAVIGATING THE FUTURE OF TECHNOLOGY
Importance of Peúgo in Today’s Context
In conclusion, Peúgo represents a paradigm shift in the way organizations approach workflow management and productivity enhancement. Its versatility, usability, and cost-effectiveness make it an indispensable tool for businesses looking to stay ahead in today’s competitive landscape.
Conclusion
In summary, Peúgo offers a comprehensive solution for optimizing workflow management, enhancing productivity, and driving innovation across industries. With its user-friendly interface, advanced features, and promising future prospects, Peú,go is poised to revolutionize the way we work and collaborate in the digital age.
ALSO READ: QXEFV UNVEILED: THE ULTIMATE GUIDE
FAQs
What industries benefit the most from using Peúgo?
Industries across the board can benefit, but particularly those with complex workflow management needs such as finance, healthcare, manufacturing, and retail.
Is Peúgo suitable for small businesses?
Yes, Peúgo’s scalability makes it suitable for businesses of all sizes, including small and medium-sized enterprises (SMEs).
How does Peúgo contribute to sustainability?
Peú,go promotes sustainability by optimizing processes, reducing paper waste through digitalization, and minimizing resource consumption through efficient workflow management.
Can Peúgo be customized according to specific needs?
Absolutely, Peú,go offers customization options to tailor the platform to the unique requirements of different organizations and industries.
What sets Peú,go apart from similar solutions?
Peú,go stands out for its intuitive interface, robust feature set, seamless integration capabilities, and scalability, setting it apart from competitors in the market.
TECHNOLOGY
Everything About Geöe
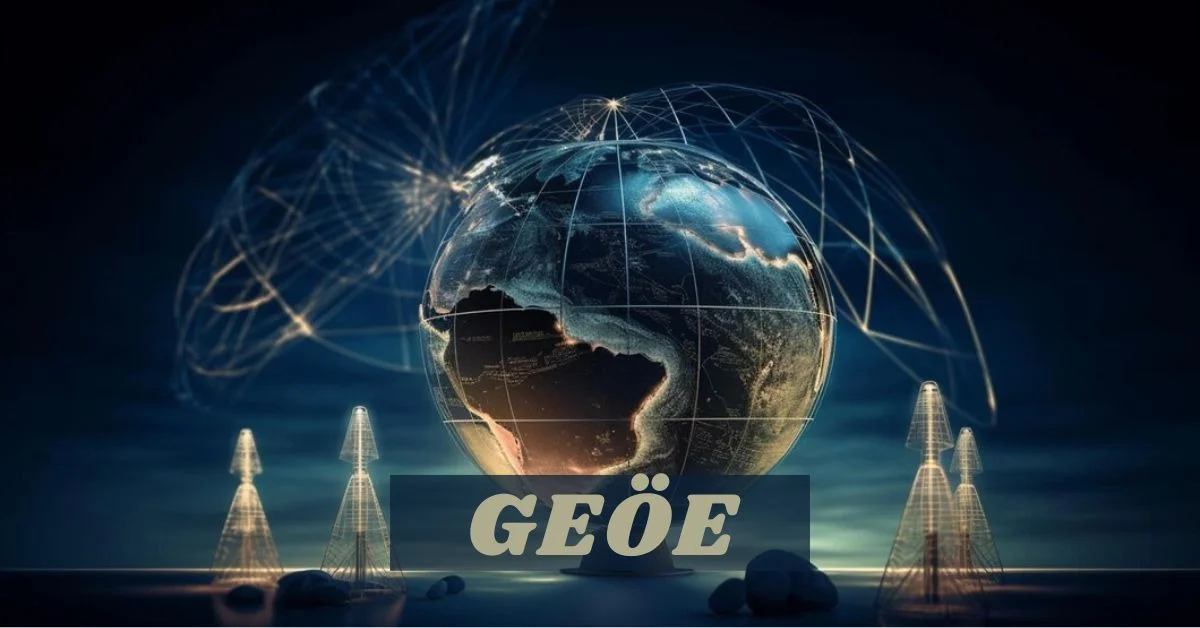
Introduction to Geöe
The world is constantly evolving, and with it comes a myriad of innovations that transform our daily lives. One such innovation that has recently captured the spotlight is Geöe. But what exactly is Geöe? Why should you care about it? Whether you’re a curious explorer or someone looking to harness new tools for personal growth, understanding Geöe can open up exciting possibilities. This blog post will dive deep into everything we need to know about this fascinating concept, from its origins to its practical applications in our everyday lives. Get ready to discover how embracing Geöe can enrich your experience and ignite your passions!
The History and Origin of Geöe
The origins of geöe are as intriguing as its modern applications. Rooted in ancient practices, this concept has evolved significantly over time. It is believed to have emerged from early human interactions with nature, where people sought balance and harmony.
Initially, geöe was used by indigenous cultures for various purposes including healing and spiritual connection. The term itself reflects a deeper understanding of the environment and our relationship with it.
As centuries passed, knowledge about geöe spread across continents, merging with different philosophies and traditions. This blend enriched its meaning and usage in diverse societies.
In more recent years, renewed interest in holistic living brought geöe back into the spotlight. Its principles resonate strongly today amidst growing awareness around sustainability and well-being.
Benefits of Using Geöe
Geöe offers a myriad of advantages that can enhance our daily lives. One of its primary benefits is promoting mental clarity. Users often report improved focus and reduced anxiety, leading to better decision-making.
Additionally, Geöe supports physical wellness. Incorporating it into your routine may boost energy levels, helping you tackle the day with vigor.
Another significant perk is the social aspect. Engaging with others who use Geöe fosters community connections and shared experiences, enriching your interactions.
Moreover, it’s versatile. Whether in cooking or as a part of wellness practices, Geöe adapts seamlessly to various lifestyles and preferences.
Using Geöe encourages sustainable choices. Many products associated with it prioritize eco-friendly methods, contributing positively to environmental health while enhancing personal well-being.
How to Use Geöe in Everyday Life?
Incorporating geöe into your daily routine is both easy and rewarding. Start by integrating it into your morning rituals. Whether it’s in your coffee or smoothie, a touch of geöe adds flavor and health benefits.
During meals, consider using geöe as a seasoning or garnish. It enhances dishes while providing nutritional perks that elevate standard recipes.
For those on the go, snack bars infused with geöe’s can be a game changer. They offer an energy boost without sacrificing taste.
You can also explore its use in skincare routines. Geöe-infused products may improve skin vitality and provide hydration.
Don’t overlook social gatherings. Share innovative drinks or appetizers featuring geöe to spark conversations among friends about its unique qualities and benefits.
Common Misconceptions about Geöe
Many people harbor misconceptions about geöe’s, often confusing it with other concepts. One common myth is that geöe’s is a passing trend. In reality, it’s rooted in deep cultural practices and offers lasting benefits.
Another misconception is that using geöe’s requires extensive knowledge or training. This isn’t true; anyone can incorporate it into their daily routine without needing specialized skills.
Some believe geöe’s only appeals to niche groups. However, its versatility makes it accessible and beneficial for everyone, regardless of background or lifestyle.
Additionally, there’s the idea that embracing geöe’s means abandoning traditional methods. On the contrary, it can complement existing practices rather than replace them entirely.
Many think incorporating geöe’s into life will yield immediate results. It’s essential to recognize that building habits takes time and patience for optimal outcomes.
The Future of Geöe and its Impact on Society
As we look ahead, the future of geöe’s holds immense promise. Its integration into various sectors is already reshaping how we interact with technology and each other.
Innovations in geöe’s could enhance communication channels, making them more intuitive and responsive to human needs. Think about personalized experiences powered by artificial intelligence—geöe’s can lead the way.
In education, geöe’s might revolutionize learning methods. Imagine classrooms where teaching materials adapt in real-time based on student engagement levels.
Moreover, its role in sustainability cannot be overlooked. Geöe’s principles may guide us towards smarter resource management and greener practices.
The social fabric will also change as communities harness the power of geöe’s for collaborative projects, fostering unity while tackling local challenges together.
With these advancements on the horizon, society stands at a fascinating crossroads filled with potential opportunities and transformations driven by geöe’s.
Conclusion: Embracing the Power of Geöe in Our Lives
Embracing the power of Geöe in our lives opens up a world of possibilities. With its rich history and unique benefits, it serves as a bridge connecting tradition with modernity. By incorporating Geöe’s into our daily routines, we not only improve our well-being but also foster a deeper understanding of ourselves and those around us.
As society continues to evolve, the relevance of Geöe’s becomes even more pronounced. It encourages mindfulness, nurtures creativity, and promotes healthier lifestyles—essential elements in today’s fast-paced environment. The misconceptions surrounding Geöe’s are gradually being dispelled as more people discover its true potential.
The future of Geöe looks bright as communities begin to embrace this powerful concept. Whether through individual practices or collective initiatives, its impact on wellness and community cohesion is undeniable. As you explore what Geöe’s has to offer, remember that it’s not just about adopting new habits; it’s about transforming how we live each day with intention and purpose.
Let’s continue exploring the depths of Geöe together while sharing insights that can enrich our lives for years to come.
ALSO READ: Lepbound: Discover the Path to Personal Growth and Freedom
FAQs
What is “Geöe”?
Geöe is a transformative concept rooted in ancient traditions, promoting mental clarity, physical wellness, and sustainable living in modern life.
How can I incorporate Geöe’s into my daily routine?
You can easily add Geöe’s to meals, beverages, skincare, and social activities to boost energy, enhance flavor, and foster wellness.
What are the common misconceptions about Geöe’s?
Many think Geöe’s is a fad or complicated, but it’s a versatile, accessible practice that complements traditional methods and benefits everyone.
What benefits does Geöe’s offer for mental and physical health?
Geöe’s supports improved focus, reduced anxiety, increased energy, and social connection through community engagement.
How will Geöe’s impact the future of society?
Geöe is expected to revolutionize education, technology, sustainability, and community collaboration by fostering smarter, greener, and more connected lifestyles.
TECHNOLOGY
Everything About XVIF: XML (Extensible Markup Language)
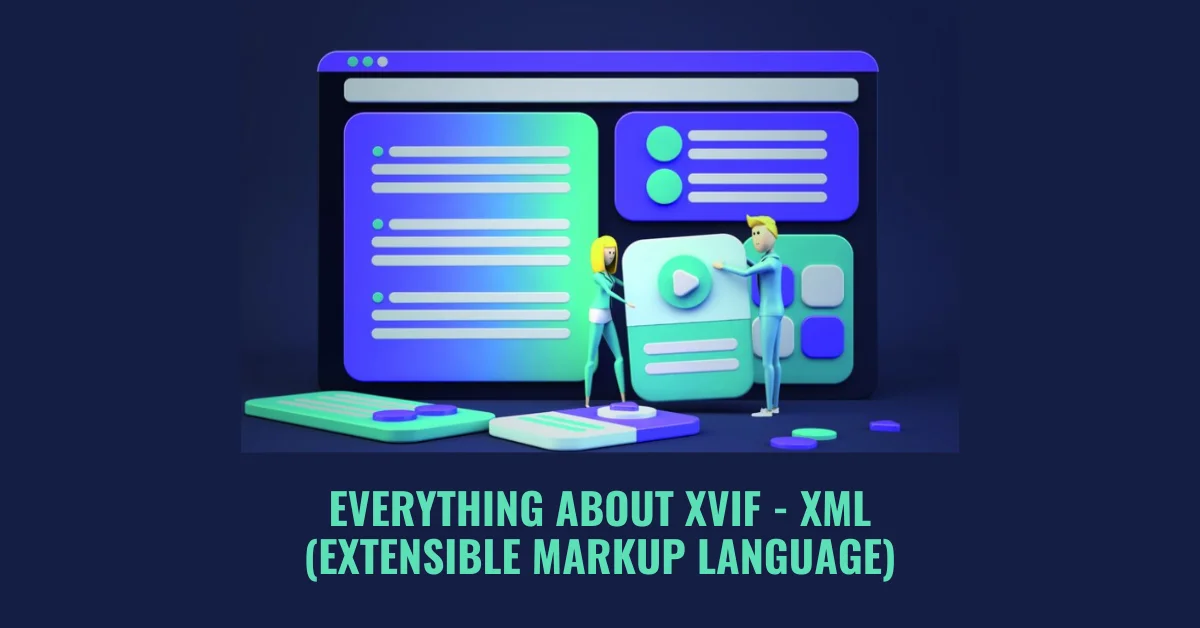
Introduction to XVIF
In the ever-evolving world of technology, data management and communication have taken center stage. Enter XVIF, an intriguing extension of XML that is reshaping how developers handle information. If you’ve ever wondered about the nuances and capabilities of this markup language, you’re in for a treat.
Think of XML as the backbone of data structure—versatile and powerful. Now imagine taking it a step further with XVIF, which introduces even more flexibility to your projects. Whether you’re building websites or managing databases, understanding XVIF could be your secret weapon in streamlining processes.
Join us as we explore everything there is to know about XVIF: from its history to its wide-ranging applications. Get ready to dive deep into a topic that’s essential for anyone looking to enhance their tech skills or optimize their workflows!
History and Evolution of XML
XML, or Extensible Markup Language, was born in the late 1990s. The World Wide Web Consortium (W3C) developed it to meet the growing need for a flexible format that could effectively manage data across diverse systems.
Before XML’s inception, SGML (Standard Generalized Markup Language) served as a markup standard. However, SGML was complex and not user-friendly for web applications. This limitation motivated developers to create XML as a simpler alternative.
The first official recommendation of XML came in 1998. It quickly gained traction because of its versatility and ease of use. Developers appreciated how XML separated data from presentation, allowing for seamless integration into various platforms.
As technology evolved, so did XML standards and specifications. From supporting different character encodings to enabling namespaces, these enhancements made it an essential tool in web development and beyond.
Advantages and Applications of XML
XML, or Extensible Markup Language, offers numerous advantages that make it a preferred choice in various fields. Its flexibility allows users to define their own tags and structure data according to specific needs. This adaptability is key for applications ranging from simple data storage to complex web services.
Another significant benefit is its platform independence. XML files can be created and accessed across different systems without compatibility issues. This ensures seamless communication between diverse software applications.
Additionally, XML enhances data sharing and interoperability. Its structured format makes it easy for machines and humans alike to process information efficiently.
In terms of applications, XML finds use in web development, where it serves as a backbone for APIs and configuration files. It’s also widely adopted in document management systems due to its capability of storing rich text alongside metadata.
Data integration projects often leverage XML because of its standardized approach to representing structured information across varied databases.
Key Features of XVIF
XVIF boasts several key features that set it apart in the realm of markup languages. Its extensibility is one of its standout attributes, allowing users to define custom tags suited for specific needs. This flexibility makes XVIF incredibly adaptable across various applications.
Another notable feature is its human-readable format. The structured nature of XML ensures that data can be easily understood and manipulated by both machines and people alike.
Additionally, XVIF supports a wide range of data types, which means it can handle everything from text to complex objects seamlessly.
Its hierarchical structure helps organize information efficiently, making data retrieval straightforward and intuitive. These characteristics enhance collaboration among developers and foster innovation within projects utilizing XVIF effectively.
How XVIF Differs from Other Markup Languages?
XVIF stands out among markup languages due to its flexibility and extensibility. Unlike HTML, which is rigid in structure, XVIF allows developers to create custom tags tailored to specific needs. This adaptability makes it a preferred choice for complex data representation.
Another distinct aspect of XVIF is its emphasis on self-describing data. Each element carries information about itself, enhancing clarity and reducing ambiguity. In contrast, traditional markup languages often require external documentation.
Furthermore, XVIF’s compatibility with various systems sets it apart. It can easily integrate with other technologies like JSON and APIs without much hassle. This seamless interoperability enriches the developer experience.
While many markup languages focus primarily on presentation or layout aspects, XVIF prioritizes data interchange and structured storage above all else. Its design philosophy aligns more closely with modern application requirements than conventional alternatives do.
Common Uses of XVIF: Web Development, Data Storage, and More
XVIF plays a significant role in web development. By allowing developers to create structured, easy-to-read documents, it enhances the clarity of data exchange between servers and clients.
In addition to web applications, XVIF is also favored for data storage solutions. Its hierarchical structure makes it ideal for organizing complex datasets while ensuring that information remains accessible and well-structured.
Moreover, XVIF supports interoperability across different systems. This capability allows various applications to communicate seamlessly with one another.
Another area where XVIF shines is mobile app development. It enables efficient data transmission between devices, making apps more responsive and user-friendly.
Industries such as finance and healthcare rely on XVIF for managing sensitive information securely while maintaining compliance with regulations. The versatility of this markup language continues to expand its reach across diverse fields.
Top Tools and Resources for Working with XVIF
When diving into XVIF, having the right tools can make all the difference. Text editors like Visual Studio Code and Notepad++ are excellent for writing and editing XML files. They support syntax highlighting, helping you catch errors quickly.
For validation purposes, consider using XML validators like W3C Validator or Xerces. These tools ensure your XVIF documents adhere to standard rules.
If you’re working with large datasets, programs such as Oxygen XML Editor offer robust features for navigating complex structures effortlessly.
Additionally, libraries like lxml in Python simplify parsing and manipulating XML data programmatically.
Don’t forget about online resources! Platforms such as Stack Overflow provide community support where you can ask questions or find solutions from experienced developers familiar with XVIF intricacies.
Conclusion
XML, or Extensible Markup Language, has become a fundamental technology in modern web and data management. XVIF enhances the capabilities of XML, allowing for even greater flexibility and efficiency in handling information.
Its history demonstrates how it evolved to meet the demands of various industries. The advantages of using XML are numerous—ranging from its versatility in data representation to its widespread application across different platforms.
Key features like self-descriptiveness and extensibility make XVIF stand apart from traditional markup languages. This adaptability is vital for developers looking to create complex applications without being constrained by predefined structures.
Common uses span web development, where it aids in structuring content dynamically, to data storage solutions that require organization over massive datasets. With an array of tools available for working with XVIF, both beginners and seasoned professionals can streamline their workflow effectively.
Understanding everything about XVIF opens doors to innovative practices in coding and data management. As technology continues to advance, mastering this language will remain essential for anyone looking to stay ahead in their field.
ALSO READ: Tex9.net Green IT: Leading Innovation for Sustainable Technology
FAQs
What is “Everything About XVIF”?
“Everything About XVIF” refers to a comprehensive overview of XVIF, an XML-based extension that enhances data structure, flexibility, and interoperability in tech applications.
How is XVIF different from standard XML?
While XML defines structure and tags, XVIF takes it further by allowing more extensible, self-describing data, optimized for integration with APIs, databases, and modern applications.
Why should developers consider using XVIF?
Developers benefit from XVIF’s customizable tags, readable format, and system compatibility, making it ideal for complex data processing, especially in web and mobile development.
Can XVIF be integrated with other technologies?
Yes, XVIF’s integrates seamlessly with technologies like JSON, REST APIs, and Python libraries, enabling efficient data exchange and automation across platforms.
Is XVIF suitable for beginners in web development?
Absolutely. XVIF builds on XML’s logic, making it accessible for beginners while offering powerful features that support advanced development as skills grow.
- GENERAL2 weeks ago
5 Factors That Affect Tattoo Removal Success
- ENTERTAINMENT3 weeks ago
Exploring the Kristen Archives: A Treasure Trove of Erotica and More
- TECHNOLOGY5 months ago
Blog Arcy Art: Where Architecture Meets Art
- LIFESTYLE2 months ago
Berniece Julien: The Private Life of Tyson Beckford’s Partner
- LIFESTYLE5 months ago
The Disciplinary Wives Club: Spanking for Love, Not Punishment
- LIFESTYLE2 days ago
Who Is Sandra Orlow?
- GENERAL7 months ago
Worldwide Elephant List: Complete Reserves and Map 2024
- ENTERTAINMENT3 weeks ago
Kiss KH: The Streaming Platform Redefining Digital Engagement and Cultural Currents