TECHNOLOGY
Basic Knowledge of PLC
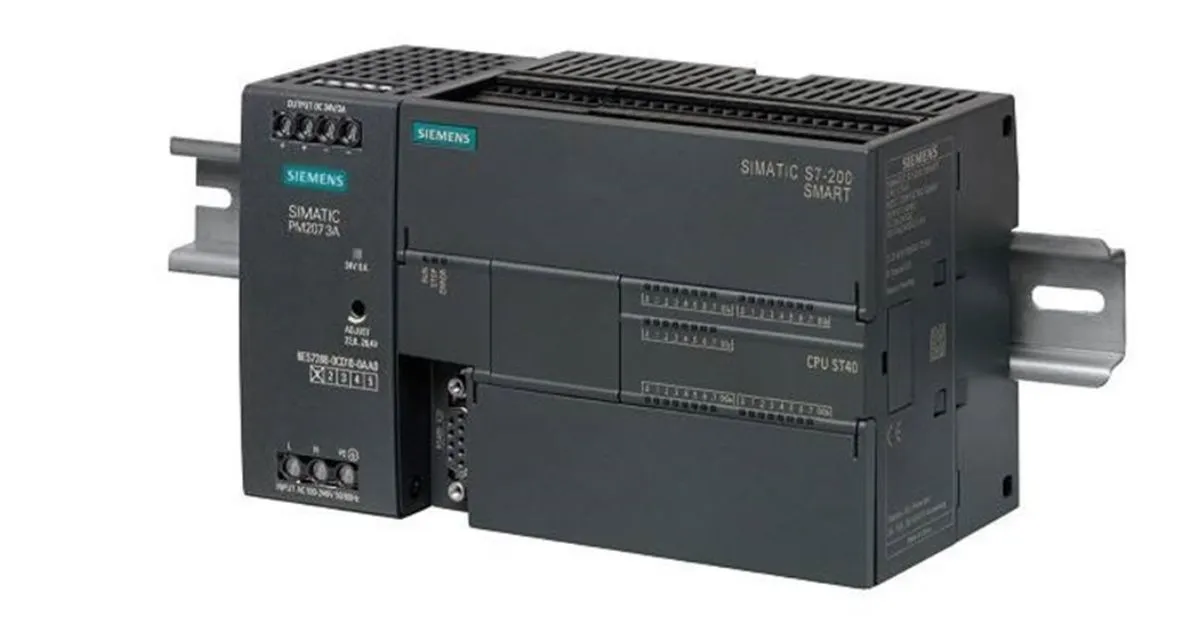
Programmable Logic Controller (PLC) is a new type of general-purpose industrial automatic control device that integrates computer technology, microelectronics technology, automatic control technology, digital technology, and communication network technology based on traditional sequential controllers. It is an important pillar of modern industrial control.
Applications of PLC:
PLC applications can generally be divided into the following five categories:
1. Sequential Control:
This is the most extensive field of PLC applications and the most suitable for PLC use. It replaces traditional relay sequential control. PLC is used in single machine control, multi-level group control, and production automatic line control.
2. Motion Control:
PLC manufacturers currently provide single-axis or multi-axis position control modules for stepper motors or servo motors. In most cases, the PLC sends data describing the target position to the control module, which outputs to move one or several axes to the target position. Each axis moves with appropriate speed and acceleration to ensure smooth motion.
3. Process Control:
PLC can control a large number of physical parameters, such as temperature, pressure, flow, liquid level, and speed.
4. Data Processing:
In mechanical processing, PLC is used as the main control and management system in CNC systems to complete a large amount of data processing work.
5. Communication Network:
PLC communication includes communication between the host and remote I/O, communication between multiple PLCs, and communication between PLC and other intelligent control devices (such as computers, inverters, CNC devices, etc.). PLC, together with other intelligent control devices, can form a distributed control system with centralized management and decentralized control.
Characteristics of PLC:
Programmability: PLC can perform various logical operations, timing control, and data processing functions through programming. Users can define PLC behavior by writing programs, making modifications, and adjustments as needed to meet different control requirements.
Reliability: PLC has high reliability and stability. They undergo rigorous testing and quality control and use reliable hardware designs and protective measures to handle harsh working environments and electrical interference.
Flexibility: PLC can be configured and expanded flexibly according to needs. Users can select appropriate input/output modules, communication modules, and function modules according to specific application requirements to meet different control needs.
Real-time Performance: PLC can process input signals in real time and respond quickly to output signals based on preset logic and programs, achieving real-time control and monitoring of the system.
Ease of Maintenance: PLC has good maintainability. They usually have self-diagnostic functions that can detect and report faults and provide corresponding troubleshooting and maintenance guidance. Moreover, PLC programming and parameter setting are relatively simple, making maintenance and modifications easier.
Scalability: PLC systems can be expanded and upgraded as needed. Users can add new modules or functions to meet system expansion requirements without large-scale hardware replacement.
Ease of Integration: PLC can be integrated with other devices and systems, such as sensors, actuators, and human-machine interfaces. Through appropriate communication interfaces and protocols, PLC can exchange data and communicate with upper-level computers, SCADA systems, and other control devices.
Overall, PLC has features such as programmability, reliability, flexibility, real-time performance, ease of maintenance, scalability, and ease of integration, making it widely used in the field of automation control.
Classification of PLC:
PLC is a product of the needs of modern production, and its classification must meet the requirements of modern production. Generally, PLC can be classified from three perspectives: control scale, performance, and structural characteristics.
Classification by Control Scale:
1. Small PLC:
Usually, the I/O points are less than 256, single CPU, 8-bit or 16-bit processor, with a user program memory capacity of less than 4KB, mainly for discrete control.
2. Medium PLC:
Generally, the I/O points are between 256 and 2048, dual or multi-CPU, with a user program memory capacity of 2-8KB or more. It has both discrete and analog control functions and stronger digital computation capabilities.
3. Large PLC:
Usually, the I/O points are more than 2048, dual or multi-CPU, 16-bit or 32-bit processor, with a user program memory capacity of 8-16KB or more.
Classification by Control Performance:
1. Low-end PLC:
This type of PLC has basic control functions and general computing power, slower working speed, can handle fewer input and output modules, and has fewer types of I/O modules.
2. Mid-range PLC:
This type of PLC has strong control functions and computing power. It can perform not only general logical operations but also more complex trigonometric, exponential, and PID calculations. It works faster and can handle more input and output modules, with a wider variety of I/O modules.
3. High-end PLC:
This type of PLC has powerful control functions and computing power. It can perform logical operations, trigonometric, exponential, PID, and complex matrix calculations. It works very fast and can handle a large number of input and output modules with comprehensive I/O module types.
Classification by Structure:
PLC can be divided into integral type and modular type based on structure.
1. Integral Type:
This is the most common and basic type of PLC. It consists of a central processor module, input module, output module, and communication module. The central processor executes programs, performs logical operations and control, the input module receives external signal input, the output module controls external device operations, and the communication module exchanges data with other devices.
2. Modular Type:
The modular PLC structure divides the PLC system’s components into several modules by function, such as CPU module, input module, output module, power supply module, etc. These modules can be inserted into a frame or baseboard to form a complete control system.
TECHNOLOGY
Unveiling the Mysteries of FTMÇ: Everything You Need to Know
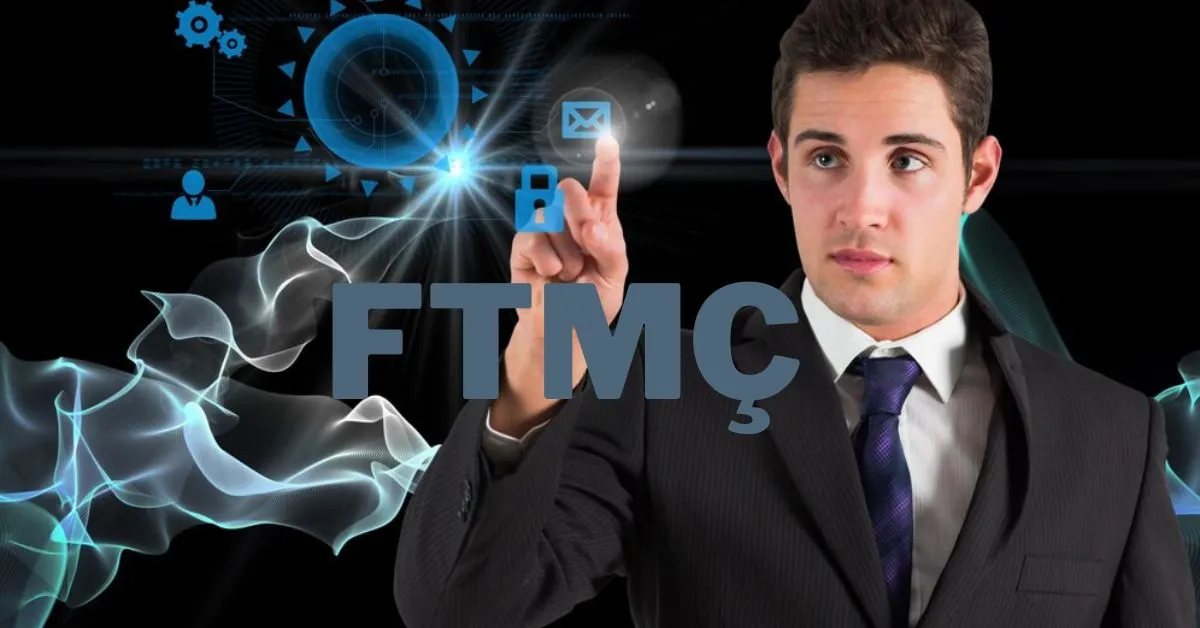
Introduction to Ftmç
In today’s fast-paced business landscape, the ability to harness data effectively can make or break an organization. Enter FTMÇ—a game-changer in the realm of data analysis and decision-making. This innovative tool is not just another software; it represents a paradigm shift for companies aiming to thrive amid intense competition. As businesses grapple with vast amounts of information, FTMÇ emerges as a solution tailored for modern challenges. It empowers organizations to turn raw data into actionable insights, paving the way for informed strategies and enhanced performance.
Imagine having a tool that transforms complex datasets into clear narratives, enabling teams to respond swiftly and accurately. With FTMÇ at your fingertips, this vision becomes reality. Let’s delve deeper into how FTMÇ is revolutionizing organizational success through smarter decision-making processes!
The Need for Better Data Analysis and Decision Making in Organizations
In today’s fast-paced business environment, organizations are inundated with data. This abundance can feel overwhelming. Many companies struggle to extract actionable insights from the mountains of information they collect.
Effective decision-making is crucial for growth and sustainability. When data analysis falls short, opportunities may be missed or miscalculated. Poor decisions based on incomplete or inaccurate data can lead to significant setbacks.
Moreover, competition is fierce. Organizations that harness their data effectively gain a distinct advantage in the marketplace. They make informed choices that propel them forward while others lag behind.
Investing in robust data analysis tools and strategies isn’t just an option—it’s a necessity for survival. Businesses must adapt to stay relevant and thrive amidst constant change in consumer behavior and market dynamics.
How Ftmç Works: An Overview of Its Features and Capabilities
Ftmç harnesses cutting-edge technology to streamline data analysis. Its intuitive interface allows users to easily navigate complex datasets. This makes it accessible for teams of all skill levels.
One standout feature is its real-time analytics capability. Users can visualize data trends as they unfold, enabling timely decision-making. The platform supports various data formats, ensuring compatibility with existing systems.
Collaboration tools enhance teamwork within organizations. Multiple stakeholders can access and manipulate shared datasets simultaneously, fostering a culture of transparency and inclusivity.
Advanced machine learning algorithms are integrated into Ftmç, providing predictive insights that guide strategic planning. Organizations can forecast outcomes based on historical patterns, minimizing risks associated with uncertainty.
Customization options further empower users by allowing tailored dashboards that highlight relevant metrics specific to their needs. Whether for finance, marketing, or operations, Ftmç adapts seamlessly to diverse organizational requirements.
ALSO READ: KÄNTÄJ: BRIDGING WORLDS THROUGH TRANSLATION
Real-Life Examples of Ftmç’s Impact on Organizational Success
Companies across various industries are harnessing FTMÇ to drive their success stories. A leading retail chain implemented the platform to analyze customer purchasing patterns. The insights gained allowed them to optimize inventory management, resulting in a 20% reduction in stockouts and improved sales.
In the healthcare sector, a hospital utilized FTMÇ for patient data analysis. By identifying trends in patient admissions and treatment outcomes, they enhanced service delivery and reduced waiting times by 30%.
An emerging tech startup leveraged FTMÇ’s predictive analytics capabilities to refine its product development strategy. This led to faster time-to-market for new features and an increase in user engagement by over 50%.
These examples highlight how organizations are not just collecting data but transforming it into actionable strategies with FTMÇ at the helm. Each story illustrates a unique journey toward operational excellence fueled by informed decision-making.
Benefits of Using Ftmç for Data Analysis and Decision Making
Using FTMÇ transforms how organizations approach data analysis and decision-making. One of its standout benefits is enhanced accuracy. With advanced algorithms, FTMÇ minimizes human error, ensuring decisions are based on reliable insights.
Speed is another significant advantage. Traditional methods can be slow and cumbersome. FTMÇ streamlines processes, allowing teams to access real-time data quickly. This agility enables quicker responses to market changes.
Collaboration becomes seamless with FTMÇ as well. Teams can easily share insights across departments, fostering a culture of informed decision-making throughout the organization.
Furthermore, the platform offers customizable dashboards tailored to specific needs and goals. This feature empowers users by presenting relevant information in an easily digestible format.
Leveraging predictive analytics helps organizations foresee trends and prepare strategically for future challenges or opportunities in their respective industries.
ALSO READ: DECODING ПРЕВОДСЧ: A COMPREHENSIVE GUIDE
Implementing Ftmç in Your Organization: Tips and Strategies for Success
Implementing FTMÇ requires a strategic approach for maximum impact. Start by identifying key stakeholders within your organization. Their buy-in is crucial for successful adoption.
Next, assess your existing data infrastructure. Understanding current capabilities will aid in tailoring FTMÇ to meet specific needs.
Training teams on how to use FTMÇ effectively is essential. Offer comprehensive workshops and resources that empower users to harness its full potential.
Encourage a culture of data-driven decision-making across all departments. Share success stories that highlight the benefits of using FTMÇ, fostering enthusiasm throughout the organization.
Regularly review performance metrics post-implementation. This ensures you can adapt strategies as needed and continuously improve processes based on user feedback and evolving needs.
Conclusion: Embracing the Future of Data Analysis with FTMÇ
The future of data analysis is here, and FTMÇ stands at the forefront. Organizations that recognize the importance of effective decision-making will benefit immensely from adopting this innovative tool. Embracing FTMÇ means harnessing advanced features designed to streamline processes and uncover actionable insights.
As businesses navigate an increasingly complex landscape, utilizing a robust platform like FTMÇ can transform how they operate. By integrating this technology, organizations not only enhance their analytical capabilities but also foster a culture that values data-driven decisions.
With its user-friendly interface and powerful functionalities, FTMÇ empowers teams to make informed choices swiftly. It’s more than just software; it’s a strategic partner in organizational success. As companies invest in efficient solutions for data analysis, those who choose FTMÇ are likely to lead the way into a brighter future filled with potential and growth opportunities.
Embrace this shift toward smarter decision-making today—FTMÇ could be your key to unlocking unprecedented levels of success.
ALSO READ: UNVEILING TRASÑATOR: YOUR ULTIMATE GUIDE
FAQs
What is FTMÇ?
FTMÇ is an advanced data analysis tool designed to transform raw data into actionable insights, aiding organizations in making informed decisions swiftly and accurately.
How does FTMÇ enhance decision-making in organizations?
FTMÇ uses real-time analytics and machine learning algorithms to provide predictive insights, enabling teams to forecast outcomes and make data-driven decisions, thus improving overall performance.
What are the key features of FTMÇ?
FTMÇ’s offers features such as real-time data visualization, collaboration tools for team use, support for various data formats, and customizable dashboards tailored to specific organizational needs.
Can you provide examples of FTMÇ’s impact on organizations?
Yes, for instance, a retail chain reduced stockouts by 20% using FTMÇ’s for inventory management, and a hospital decreased patient waiting times by 30% through improved service delivery based on data insights.
What are the benefits of implementing FTMÇ’s in an organization?
FTMÇ’s enhances decision-making accuracy, speeds up data processing, fosters team collaboration, and provides predictive analytics, helping organizations stay agile and competitive in their industries.
TECHNOLOGY
Future Trends in New Vehicle Technology
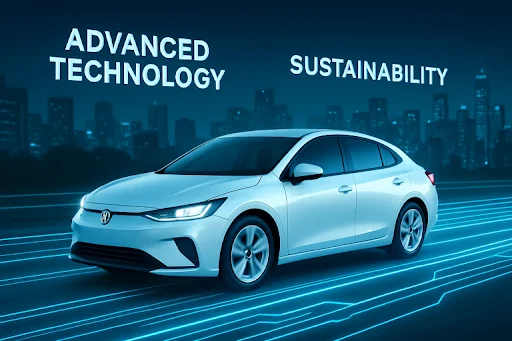
Table of Contents
- Electric Vehicles (EVs)
- Autonomous Driving
- Connected Cars and V2X Communication
- Software-Defined Vehicles (SDVs)
- Sustainable Materials in Vehicle Manufacturing
- Hydrogen Fuel Cell Vehicles
- Artificial Intelligence in Automotive Systems
- Cybersecurity in Automotive Technology
- Shaping the Road Ahead
- Embracing a New Era of Mobility
The automotive industry stands on the brink of a transportation revolution. As vehicles become more intelligent, greener, and more connected, drivers and industry leaders alike are navigating a rapidly evolving landscape. Consumers interested in the most innovative vehicles and up-to-date options can learn more about the latest models, features, and technology shaping the next generation of cars.
Understanding the key trends driving these changes is crucial if you want to make informed decisions about your next vehicle or simply stay ahead in an increasingly digital world. Breakthroughs in electric vehicles, autonomy, connectivity, and sustainability are not only transforming our daily commutes but also redefining what tomorrow’s roads and cities will look like.There’s so much more to discover—browse our related posts!
Electric Vehicles (EVs)
Electrification is at the forefront of automotive innovation. Once seen as a niche market, electric vehicles have rapidly gained mainstream acceptance. Automakers are releasing a diverse array of EV models, from family SUVs to luxury sedans, each promising cleaner transportation with reduced emissions. Breakthroughs in battery chemistry, particularly the emergence of solid-state batteries, now allow electric vehicles to travel further and charge faster than ever before. As highlighted by the U.S. Department of Energy, EVs offer significant environmental and economic advantages, helping to lower the barrier to entry and make ownership more convenient for everyone. Government incentives and regulations are further pushing the industry toward widespread adoption of electric mobility.
Autonomous Driving
Significant advancements in sensors, machine learning, and real-time data processing are paving the way for self-driving vehicles. Autonomous driving technology can already be found in many modern vehicles, primarily in the form of advanced driver assistance systems (ADAS). These semi-autonomous features—such as adaptive cruise control, lane-keeping assistance, and emergency braking—help minimize accidents and reduce driver fatigue.
Connected Cars and V2X Communication
Connectivity has quickly become a defining feature of the modern car. Vehicles now integrate with smartphones, cloud-based services, and even other vehicles or infrastructure through Vehicle-to-Everything (V2X) technology. This enables vehicles to communicate with traffic signals, road signs, and surrounding vehicles, paving the way for safer roads and more efficient traffic management. The exchange of real-time data helps alert drivers to hazards, optimize routing, and maximize fuel efficiency, making the driving experience more seamless and secure.
Software-Defined Vehicles (SDVs)
Software-defined vehicles (SDVs) represent a fundamental shift from hardware-centric automotive design towards a software-first approach. In these vehicles, critical systems—ranging from braking and steering to infotainment—are increasingly governed by onboard software. This architecture supports over-the-air (OTA) updates, allowing automakers to upgrade features and patch vulnerabilities without requiring a dealership visit. As SDVs become more prevalent, the automotive experience becomes increasingly personalized and adaptive, mirroring the rapid pace of technological change in other consumer devices.
Sustainable Materials in Vehicle Manufacturing
The drive toward sustainability isn’t limited to vehicle emissions; it also affects how vehicles are manufactured. Automakers are reducing their carbon footprints by adopting eco-friendly materials, including recycled plastics, plant-based fabrics, and renewable composites. For example, car interiors increasingly use reclaimed materials from the ocean or bioplastics derived from agricultural waste. These practices not only minimize environmental impact but also align with consumer expectations for responsible manufacturing.
Hydrogen Fuel Cell Vehicles
Hydrogen fuel cell vehicles are gaining traction, particularly in long-haul and commercial applications where traditional batteries may struggle to meet demands. These vehicles convert hydrogen gas into electricity, emitting only water vapor as a byproduct. With fast refueling and long ranges, hydrogen-powered vehicles are well-suited for use in buses, trucks, and other heavy-duty applications. As the hydrogen infrastructure expands, more regions may soon see these vehicles as viable, clean alternatives to both gasoline and battery-electric options.
Artificial Intelligence in Automotive Systems
Artificial intelligence (AI) is integral to many modern automotive innovations, powering everything from factory automation to in-vehicle infotainment systems and autonomous driving technology. AI analyzes vast amounts of sensor data to make split-second driving decisions, prevent collisions, and customize the in-cabin experience for each passenger. AI-driven systems are standard on many new vehicles, offering features such as voice-activated assistants, adaptive cruise control, and advanced navigation. As AI capabilities evolve, cars will become not only brighter but also safer and more responsive to drivers’ needs.
Cybersecurity in Automotive Technology
With vehicles now so heavily dependent on software and network connectivity, cybersecurity is more important than ever. Modern cars are equipped with dozens of electronic control units (ECUs), which are responsible for various functions, including braking, steering, and engine management. Protecting these systems against hacking and data breaches is crucial to ensure safety, privacy, and the uninterrupted operation of critical vehicle components. Manufacturers are implementing rigorous security protocols and partnering with technology firms to build more resilient automotive ecosystems.
The acceleration of vehicle technology is redefining both the driving experience and the automotive landscape. Staying aware of these trends and understanding their impact is vital whether you’re considering a new car purchase or simply keeping pace with industry developments. The future of vehicles is connected, sustainable, intelligent, and secure—offering possibilities that just a decade ago seemed out of reach.
Shaping the Road Ahead
With vehicles now so heavily dependent on software and network connectivity, cybersecurity is more important than ever. Modern cars are equipped with dozens of electronic control units (ECUs), which are responsible for various functions, including braking, steering, and engine management. Protecting these systems against hacking and data breaches is crucial to ensure safety, privacy, and the uninterrupted operation of critical vehicle components. Manufacturers are implementing rigorous security protocols and partnering with technology firms to build more resilient automotive ecosystems.
The acceleration of vehicle technology is redefining both the driving experience and the automotive landscape. Staying aware of these trends and understanding their impact is vital whether you’re considering a new car purchase or simply keeping pace with industry developments. The future of vehicles is connected, sustainable, intelligent, and secure—offering possibilities that just a decade ago seemed out of reach.
Embracing a New Era of Mobility
The automotive industry is undergoing a profound transformation that affects every aspect of how we travel, interact with vehicles, and perceive the role of transportation in our lives. From electric powertrains and autonomous systems to advanced connectivity and sustainable manufacturing, these innovations promise to deliver safer, cleaner, and more efficient mobility solutions. As these technologies continue to evolve and integrate, they will not only reshape the vehicles themselves but also the infrastructure, regulations, and user experiences surrounding them. Staying informed about these emerging trends empowers both consumers and industry players to navigate the road ahead with confidence and enthusiasm for the future of driving.
Don’t miss out on more great reads—click through our featured posts!
TECHNOLOGY
Peúgo Decoded: Your Ultimate Guide
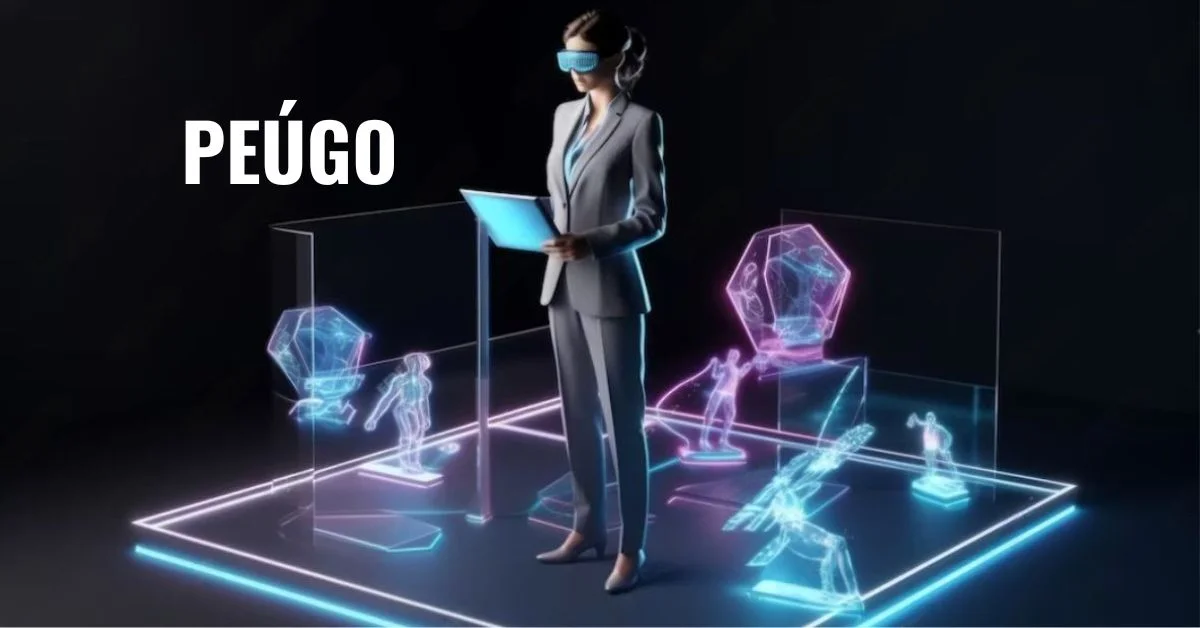
Introduction to Peúgo
In today’s rapidly evolving technological landscape, new innovations continue to emerge, revolutionizing the way we work and interact with digital platforms. Among these innovations is Peúgo, a cutting-edge solution that has been gaining significant traction in various industries. But what exactly is Peúgo, and why is it generating so much buzz? Let’s delve into the intricacies of this groundbreaking technology.
Origins and History
– Early Development
Peúgo traces its origins back to the early 21st century when a team of visionary developers set out to create a versatile and efficient solution to streamline digital processes.
– Evolution over Time
Since its inception, Peúgo has undergone significant evolution, incorporating advanced algorithms and functionalities to meet the ever-changing demands of modern businesses and consumers.
Understanding Peúgo: Definition and Concept
At its core, Peúgo can be defined as a comprehensive software platform designed to enhance productivity, efficiency, and collaboration within organizations. Its intuitive interface and robust features make it an indispensable tool for optimizing workflow management and achieving operational excellence.
ALSO READ: EVERYTHING ABOUT XATPES
Key Features and Characteristics
– Functionality
Peúgo boasts a wide array of features, including task automation, real-time analytics, and seamless integration with existing systems. Its user-friendly interface empowers users to accomplish tasks with ease, resulting in enhanced productivity and performance.
– Usability
One of the standout characteristics of Peúgo is its unparalleled usability. Whether you’re a seasoned professional or a novice user, navigating the platform is intuitive and straightforward, allowing for seamless adoption and implementation across organizations of all sizes.
ALSO READ: DECODING THE ENIGMA: U231748506 UNVEILED
Applications of Peúgo
– Industry Use Cases
From finance and healthcare to manufacturing and retail, Peúgo finds applications across a diverse range of industries. Its versatility and scalability make it a valuable asset for optimizing processes, driving innovation, and gaining a competitive edge in today’s digital landscape.
– Consumer Applications
In addition to its enterprise applications, Peú,go also caters to individual consumers, offering personalized solutions for managing tasks, organizing schedules, and enhancing overall productivity.
Advantages of Peúgo
– Efficiency
By automating repetitive tasks and streamlining workflows, Peú,go enables organizations to operate more efficiently, freeing up valuable time and resources that can be allocated to more strategic initiatives.
– Cost-effectiveness
The cost-effectiveness of Peú,go is another significant advantage, as it eliminates the need for multiple disparate solutions and reduces overhead costs associated with manual processes.
ALSO READ: BOLTBÓL: SHAPING THE FUTURE OF INNOVATION
Challenges and Limitations
– Technical Constraints
Despite its numerous benefits, Peúgo is not without its challenges. Technical constraints such as compatibility issues and system integration complexities may pose obstacles during implementation.
– Adoption Issues
Furthermore, widespread adoption of Peúgo may be hindered by resistance to change and the need for comprehensive training programs to familiarize users with its functionalities.
Peúgo vs. Competitors
– Comparative Analysis
In comparison to its competitors, Peú,go stands out for its intuitive interface, robust feature set, and scalability. Its ability to seamlessly integrate with existing systems gives it a competitive edge in the market.
ALSO READ: CRACKING THE CODE: A COMPREHENSIVE GUIDE TO 06SHJ06
Future Prospects and Trends
– Emerging Technologies
Looking ahead, the future of Peú,go is bright, with advancements in artificial intelligence and machine learning poised to further enhance its capabilities and drive innovation in the field of workflow management.
– Market Predictions
Analysts predict steady growth for the Peú,go market, fueled by increasing demand for digital transformation solutions and the growing emphasis on efficiency and productivity across industries.
ALSO READ: TECH DEMIS: NAVIGATING THE FUTURE OF TECHNOLOGY
Importance of Peúgo in Today’s Context
In conclusion, Peúgo represents a paradigm shift in the way organizations approach workflow management and productivity enhancement. Its versatility, usability, and cost-effectiveness make it an indispensable tool for businesses looking to stay ahead in today’s competitive landscape.
Conclusion
In summary, Peúgo offers a comprehensive solution for optimizing workflow management, enhancing productivity, and driving innovation across industries. With its user-friendly interface, advanced features, and promising future prospects, Peú,go is poised to revolutionize the way we work and collaborate in the digital age.
ALSO READ: QXEFV UNVEILED: THE ULTIMATE GUIDE
FAQs
What industries benefit the most from using Peúgo?
Industries across the board can benefit, but particularly those with complex workflow management needs such as finance, healthcare, manufacturing, and retail.
Is Peúgo suitable for small businesses?
Yes, Peúgo’s scalability makes it suitable for businesses of all sizes, including small and medium-sized enterprises (SMEs).
How does Peúgo contribute to sustainability?
Peú,go promotes sustainability by optimizing processes, reducing paper waste through digitalization, and minimizing resource consumption through efficient workflow management.
Can Peúgo be customized according to specific needs?
Absolutely, Peú,go offers customization options to tailor the platform to the unique requirements of different organizations and industries.
What sets Peú,go apart from similar solutions?
Peú,go stands out for its intuitive interface, robust feature set, seamless integration capabilities, and scalability, setting it apart from competitors in the market.
- GENERAL1 month ago
5 Factors That Affect Tattoo Removal Success
- ENTERTAINMENT2 months ago
Exploring the Kristen Archives: A Treasure Trove of Erotica and More
- LIFESTYLE6 months ago
The Disciplinary Wives Club: Spanking for Love, Not Punishment
- TECHNOLOGY5 months ago
Blog Arcy Art: Where Architecture Meets Art
- LIFESTYLE17 hours ago
Who Is Sandra Orlow?
- ENTERTAINMENT7 months ago
The Ultimate Guide to Shillong Teer Hit Number: How to Predict Your Next Win
- LIFESTYLE3 months ago
Berniece Julien: The Private Life of Tyson Beckford’s Partner
- GENERAL8 months ago
Worldwide Elephant List: Complete Reserves and Map 2024