BUSINESS
Choosing the Right Industrial Pump for Your Business Needs: Tips and Best Practices
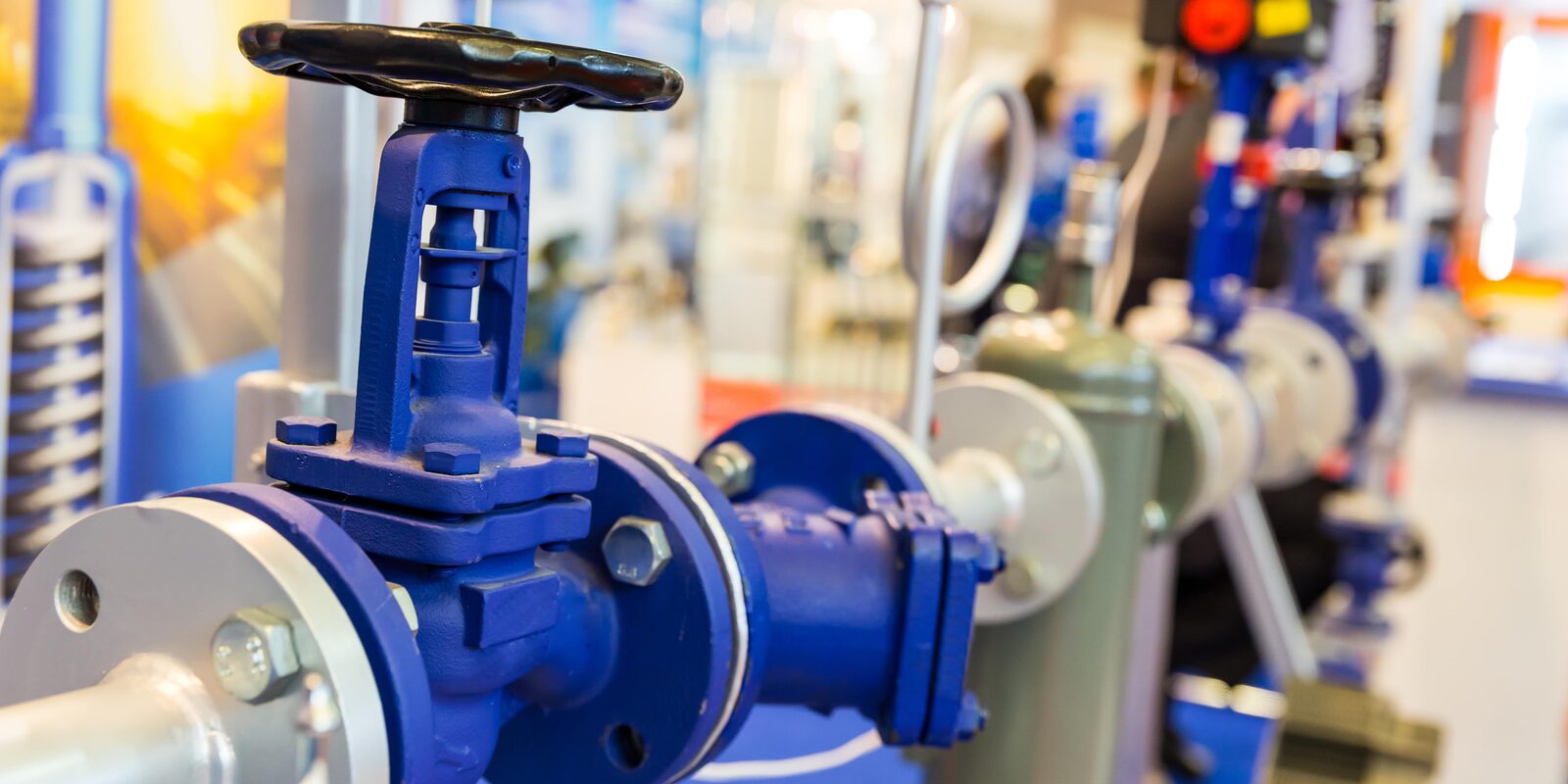
Key Takeaways
- Selecting an industrial pump requires careful consideration of various factors.
- Different types of pumps serve different applications and industries.
- Understand key parameters like flow rate, viscosity, and material compatibility.
- Maintenance and cost implications should influence your choice.
Due to the many factors, selecting an industrial pump requires careful consideration. This guide will help you understand what you need to know to make an informed decision that suits your needs. To explore your options further, visit this website for a detailed view of available pump types and specifications.
Industrial pumps come in varied designs, each suited to different applications and industries. Making the right choice can be challenging, but understanding key parameters and maintenance requirements will simplify the process. By delving into other types of pumps, their specific uses, and the key factors influencing their performance, you will be well-prepared to select the most efficient and cost-effective option for your needs.
Introduction to Industrial Pumps
Industrial pumps are crucial in various sectors, such as water treatment, chemical processing, and manufacturing. They facilitate the movement of liquids, gases, and slurries and are designed to operate under harsh conditions. Understanding their importance can guide you in making the right choice for your business operations. Without the right pump, processes can stall, contaminate, or even fail, highlighting the necessity for tailored solutions based on specific industrial requirements.
Types of Industrial Pumps
Centrifugal Pumps
Centrifugal pumps convert kinetic energy derived from a motor into hydrodynamic energy of fluid flow. They are popular due to their efficiency in handling large volumes of fluids and are widely used in industries like water treatment and chemical processing. These pumps come in various configurations, such as single-stage, multi-stage, and submersible, each offering unique benefits depending on the application’s needs. Centrifugal pumps provide a reliable, cost-effective solution for high-flow, low-viscosity substances, ensuring minimal downtime and maintenance.
Positive Displacement Pumps
Positive displacement pumps move fluids by trapping a fixed volume and forcing (displacing) that trapped volume into the discharge pipe. These pumps are preferred for high-viscosity fluids and are commonly found in applications such as oil and gas or food processing. They differ from centrifugal pumps by providing a consistent flow regardless of the pressure. This makes them ideal for scenarios where precision and consistent flow are critical, such as in chemical dosing or hydraulic systems. Their robust design makes them less prone to issues caused by variations in fluid characteristics, ensuring consistent performance.
Critical Factors in Choosing an Industrial Pump
Flow Rate
Flow rate is a critical parameter when selecting a pump. It determines how much fluid can be moved per unit of time, influencing an operation’s overall efficiency. Understanding your specific flow rate requirements will guide you to the correct type of pump. For example, processes requiring high-volume transfer will benefit from pumps designed to handle significant flow rates efficiently.
Viscosity
The viscosity of the fluid being pumped directly affects pump performance. High-viscosity fluids require unique pump designs that can handle the increased resistance. Knowing the viscosity of your fluids will help narrow down your options. For instance, positive displacement pumps perform better with viscous liquids such as oils and syrups, ensuring stable and consistent pump operation. Conversely, centrifugal pumps are more suited for low-viscosity fluids, offering greater efficiency and faster flow rates without straining the system.
Material Compatibility
Material compatibility is essential to avoid corrosion or wear over time. Pumps are made from stainless steel, cast iron, and specialized alloys. Selecting a pump constructed from materials compatible with the fluids ensures longevity and reliability. For instance, corrosive liquids like acids necessitate corrosion-resistant materials like stainless steel or special alloys. This compatibility prevents material degradation, reducing the risk of leaks and failures and ultimately lowering maintenance costs and downtime.
Application-Specific Pumps
Each industry has unique requirements that dictate the type of pump needed. For instance, adjustable-speed pumps are often chosen in wastewater treatment for energy efficiency, while high-pressure pumps are crucial in petrochemical industries. Understanding specific application requirements can significantly influence your choice. For example, food and beverage industries may require hygienic or sanitary pumps that comply with strict health regulations. On the other hand, industrial manufacturing might favor robust and durable pumps designed to handle abrasive and high-temperature fluids.
Maintenance Considerations
Regular maintenance is vital for optimal pump performance. This includes routine inspection, lubrication, and part replacements. A good maintenance schedule prolongs the pump’s lifespan, ensures consistent operation, and prevents unexpected downtimes. For instance, adhering to a maintenance routine can identify wear and tear early, allowing for proactive repairs rather than costly emergency fixes. Employing predictive maintenance techniques, like vibration analysis and thermal imaging, can further enhance pump reliability and operational efficiency.
Conclusion
Choosing the right industrial pump for your business involves understanding various factors such as flow rate, viscosity, and material compatibility. Consider the long-term costs and maintenance needs to ensure you make an informed decision that benefits your operations in the long run. Investing time in evaluating these factors will enhance operational efficiency, lead to significant cost savings, and minimize downtime. By staying informed and proactive, businesses can ensure their pump systems support their goals and contribute to overall productivity.
BUSINESS
Top 10 Tips for Choosing Reliable Moving Services in Washington DC
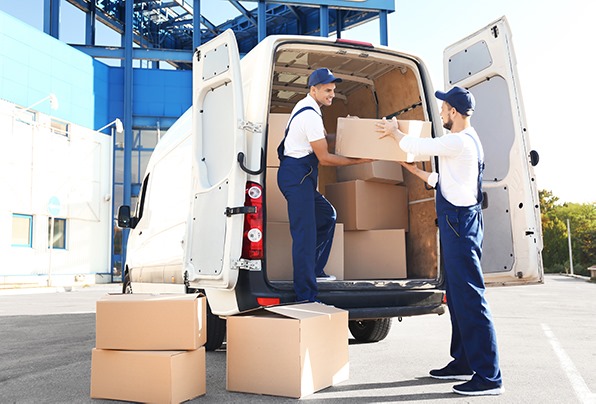
Planning a move in the nation’s capital can feel overwhelming, especially when it comes to choosing the right movers. With so many companies offering moving services Washington DC, it’s essential to know what to look for to ensure your belongings are handled with care and professionalism. Below are ten practical tips that will help you make the best decision for a smooth and stress-free move.
1. Check Licensing and Insurance
The first step in choosing a reliable moving company is to confirm that they are properly licensed and insured. Legitimate movers must follow federal and state regulations, and having insurance guarantees that your belongings are covered in case of damage or loss. Always ask for proof of licensing and insurance before signing any contract.
2. Read Reviews and Testimonials
Customer experiences can give you valuable insights into a moving company’s reliability. Browse online reviews, testimonials, and ratings on trusted platforms. Pay attention to how the company responds to complaints—it shows their level of professionalism and commitment to resolving issues.
3. Get Multiple Quotes
Don’t settle for the first moving company you contact. Request at least three estimates from different providers. Compare the services included, overall pricing, and any extra fees. Be cautious of quotes that are unusually low, as they may indicate hidden charges or poor service quality.
4. Ask About Experience in Washington DC
Washington DC has unique challenges, including heavy traffic, narrow streets, and strict building regulations. A company with local experience knows how to navigate these obstacles efficiently. Ask how long they’ve been serving the DC area and whether they have handled moves similar to yours.
5. Understand the Services Offered
Not all moving companies provide the same services. Some offer full-service moving with packing, storage, and unpacking options, while others handle only transportation. Clarify what’s included in your package and whether there are additional costs for packing materials or special items like pianos or antiques.
6. Verify Professionalism and Equipment
Reliable movers should arrive with clean, well-maintained trucks and professional moving equipment. Staff should be polite, uniformed, and trained in handling items safely. Professional presentation often reflects the quality of service you can expect throughout your move.
7. Ask About Estimates and Contracts
Make sure your moving company provides a written estimate. Ask whether it’s binding or non-binding, and read the contract carefully to avoid surprises. A reliable mover will explain the terms clearly and give you documentation that protects both parties.
8. Look for Transparent Communication
Clear communication is one of the hallmarks of a trustworthy moving service. The company should answer your questions promptly, explain their policies, and give you realistic timelines. If you find it difficult to get straight answers, consider it a red flag.
9. Check for Hidden Fees
Some movers may charge extra for stairs, long carries, or heavy items. Before signing a contract, ask about potential hidden fees to avoid unexpected costs on moving day. Transparency in pricing is a sign of a trustworthy company.
10. Trust Your Instincts
Finally, trust your intuition. If something doesn’t feel right—whether it’s unprofessional behavior, vague answers, or a lack of transparency—it’s better to walk away. A reliable moving company will give you peace of mind, not additional stress.
Conclusion
Finding the right moving service in Washington DC takes research, comparison, and careful consideration. By checking credentials, reading reviews, and asking the right questions, you can choose movers who will handle your belongings safely and efficiently. Use these ten tips to guide your search and ensure a smooth transition to your new home.
BUSINESS
Pikruos: Your Partner in Business Technology Solutions
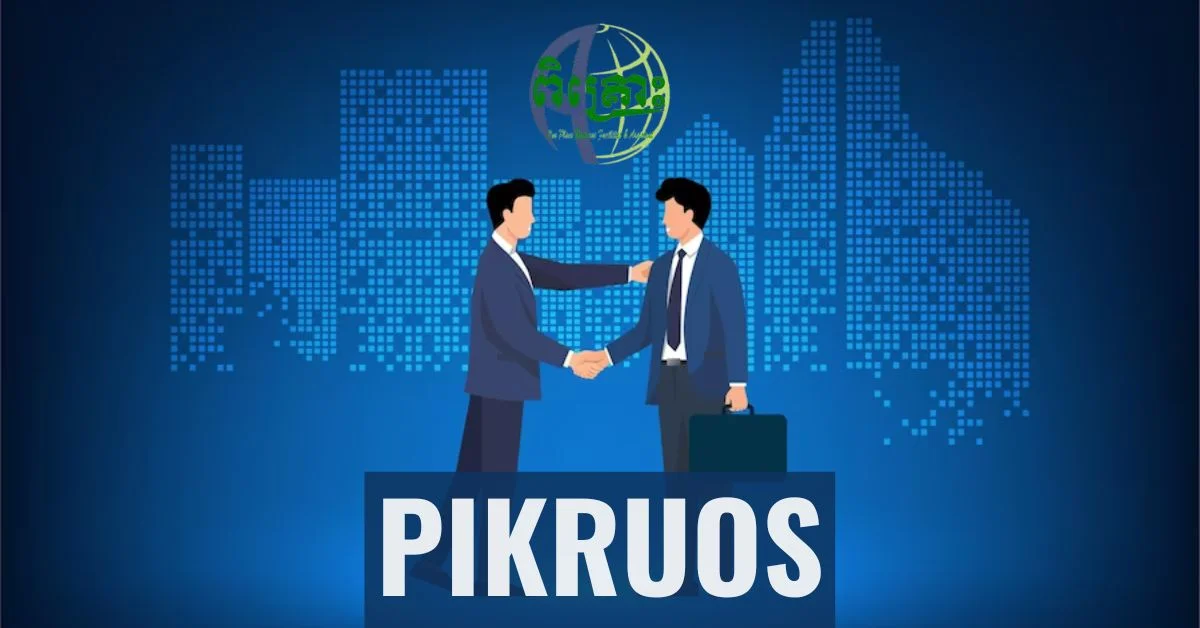
Introduction to Pikruos
In today’s fast-paced digital landscape, businesses are constantly seeking ways to improve efficiency and stay ahead of the competition. Enter Pikruos—a dynamic partner dedicated to delivering cutting-edge technology solutions tailored for your unique business needs. Whether you’re a start-up or an established enterprise, navigating the complex world of technology can be daunting. That’s where Pikruos shines, providing exceptional support that empowers your organization to thrive in a tech-driven environment. With innovative services designed to streamline operations and enhance productivity, it’s time to explore how partnering with Pikruos can transform your business journey.
The Importance of Technology Solutions in Business
In today’s fast-paced business landscape, technology solutions are no longer optional; they are essential. Companies rely on these tools to streamline operations and enhance productivity.
Effective technology solutions can automate tedious tasks, freeing up valuable time for teams to focus on strategic initiatives. This efficiency drives growth and innovation.
Moreover, the right tech can improve customer experiences. Businesses that embrace digital transformation often see a boost in engagement and satisfaction.
Data-driven insights enable firms to make informed decisions quickly. Organizations harnessing technology stay ahead of competitors by adapting swiftly to market changes.
Security is another crucial aspect. Robust technology solutions safeguard sensitive information against cyber threats, ensuring trust with clients and stakeholders alike.
Investing in effective business technologies paves the way for sustainable success in an ever-evolving environment. Adapting to these advancements keeps businesses agile and competitive.
Services Offered by Pikruos
Pikruos provides a diverse range of technology solutions tailored to meet the unique needs of businesses. From IT consulting to software development, every service is designed with efficiency in mind.
Their cloud services enable seamless data access and enhanced collaboration for teams. With robust security measures, Pikruos ensures that your information remains protected at all times.
Custom software solutions allow businesses to streamline operations effectively. Whether it’s a mobile app or an enterprise system, their innovative approach prioritizes user experience and functionality.
Additionally, Pikruos offers comprehensive support and maintenance services. This way, clients can focus on growth while knowing their technology infrastructure is well cared for.
With ongoing training and resources provided by experts, businesses are empowered to adapt swiftly in today’s fast-paced digital landscape. The commitment to customer satisfaction sets Pikruos apart as a true partner in business technology solutions.
Real World Examples of Pikruos’ Success
Pikruos has transformed businesses across various industries through innovative technology solutions. One notable case involved a mid-sized retail company struggling with inventory management. Pikruos implemented an advanced tracking system that streamlined operations, significantly reducing overstock and stockouts.
In another instance, a healthcare provider faced challenges in patient data handling. With Pikruos’ customized software solution, they enhanced data security while improving access for medical staff. This led to faster patient care and increased satisfaction rates.
Additionally, a startup in the tech sector benefited from Pikruos’ strategic consulting services. By optimizing their digital presence and automating workflows, they achieved impressive growth within months.
These examples illustrate how tailored technological interventions by Pikruos can drive efficiency and success for diverse organizations. Each story reflects their commitment to understanding unique business needs and delivering impactful results.
Why Choose Pikruos for Your Business Technology Needs?
Choosing Pikruos means investing in innovation and expertise. With a team of seasoned professionals, we deliver tailored solutions that align with your specific business goals.
Our commitment to quality sets us apart. We understand the unique challenges businesses face today and provide strategies that drive growth and efficiency.
Pikruos prioritizes customer satisfaction above all. Our collaborative approach ensures you are involved throughout the process, fostering transparency and trust.
We leverage cutting-edge technology to streamline operations. This not only boosts productivity but also enhances user experience across your organization.
When you partner with Pikruos, you’re choosing a long-term ally in navigating the complexities of modern business technology. We adapt to industry changes swiftly, ensuring your business remains competitive in an ever-evolving landscape.
Customer Testimonials and Reviews
Pikruos has garnered a multitude of positive reviews from satisfied clients who appreciate the company’s commitment to excellence. Customers often highlight the personalized approach taken by the team, ensuring that each solution is tailored specifically to their business needs.
One client shared how Pikruos transformed their outdated systems into streamlined processes, resulting in significant efficiency gains. This success story resonates with many who have experienced similar transformations.
Another testimonial praised Pikruos for its responsive customer support. Clients feel reassured knowing they can rely on expert assistance whenever challenges arise.
Many businesses value transparency and communication throughout projects. Feedback indicates that Pikruos excels in keeping stakeholders informed at every stage, fostering trust and collaboration.
Such endorsements showcase not just technical capability but also a genuine dedication to helping businesses thrive through innovative technology solutions.
Conclusion: Partnering with Pikruos for a Successful Future
Choosing Pikruos as your partner in business technology solutions can set your company on a path to success. With their extensive range of services tailored for various industries, they understand the unique challenges businesses face today. Their commitment to delivering effective technology solutions ensures that you stay ahead of the competition.
Customer testimonials highlight not just satisfaction but genuine transformations within organizations that have chosen Pikruos. The real-world examples demonstrate how businesses have thrived with the right technological support and guidance.
By collaborating with Pikruos, you’re not just opting for a service provider; you’re investing in a partnership focused on innovation and growth. This collaboration promises to equip your business with the tools necessary for navigating an ever-evolving digital landscape, ultimately leading towards lasting success.
FAQs
What is Pikruos?
Pikruos is a business technology solutions provider that offers tailored IT services such as software development, cloud solutions, consulting, and support to help businesses thrive in a digital-first world.
How does Pikruos’s help businesses improve efficiency?
Pikruos’s streamlines business operations by offering automation, secure data access, and custom software—freeing up time for strategic growth and innovation.
Which industries benefit most from Pikruos’s solutions?
Pikruos’s serves a wide range of industries including retail, healthcare, and tech startups—providing customized solutions to meet unique operational challenges.
What sets Pikruos’s apart from other IT service providers?
Pikruos’s stands out for its personalized approach, transparent collaboration, expert consulting, and long-term support that adapts with business needs.
Does Pikruos provide ongoing support and training?
Yes, Pikruos offers comprehensive maintenance and training to ensure clients can confidently manage their tech infrastructure and stay updated with the latest tools.
BUSINESS
Transforming Events with Complete Furniture Hire Solutions for Every Occasion
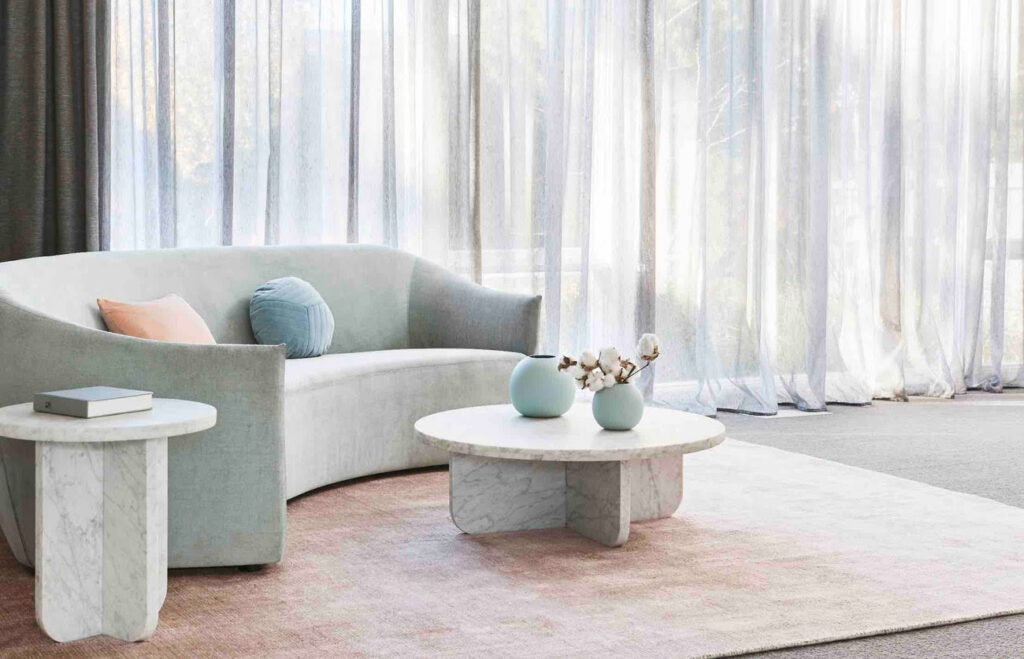
Planning an event, whether intimate or large-scale, requires careful attention to detail. From décor and lighting to food and entertainment, every aspect plays a role in creating the right atmosphere. Among these, event furniture is one of the most important elements that can make or break the overall experience for guests. The right chairs, tables, lounges, and décor items not only provide comfort but also set the tone and style of the occasion.
This is where complete furniture hire solutions for events big and small come in. By partnering with a professional event hire company like M Event Hire, you can access a wide variety of stylish, functional, and customizable furniture that perfectly matches your event’s theme and scale.
Why Furniture Hire is Essential for Events
No matter the type of gathering—be it a wedding, birthday celebration, gala dinner, or corporate function—the right furniture hire services can completely transform your venue. Here’s why:
- Enhances Guest Experience
Comfortable seating, elegant tables, and beautifully arranged lounges ensure your guests feel welcomed and valued. - Creates the Right Ambiance
Furniture contributes to the overall décor and vibe of the event. For instance, rustic wooden tables set a cozy tone, while sleek modern lounges create a chic, contemporary look. - Saves Time and Effort
Instead of worrying about sourcing, transporting, and setting up furniture, hiring experts means everything is delivered, installed, and packed away seamlessly. - Flexibility for All Event Sizes
Whether you’re hosting 20 people in a backyard or 500 guests at a grand venue, professional event hire companies can scale up or down depending on your needs.
Types of Event Furniture to Consider
Event hire services offer a wide range of furniture and accessories designed to suit all themes and occasions. Here are some popular options:
- Seating Solutions: Chiavari chairs, banquet chairs, bar stools, and lounge seating.
- Tables: Round banquet tables, cocktail tables, trestle tables, and coffee tables.
- Lounges & Sofas: Perfect for creating relaxed zones within your event.
- Outdoor Furniture: Benches, deck chairs, and marquees for outdoor gatherings.
- Décor Items: Lighting, table centerpieces, rugs, and decorative partitions.
By choosing complete furniture hire solutions for events big and small, you’ll have access to all of these elements in one place.
Benefits of Choosing M Event Hire
When planning an event in Australia, M Event Hire stands out as a trusted partner for providing top-quality furniture and event solutions. Here’s why:
- Wide Range of Options: From classic to modern designs, their extensive catalog caters to weddings, corporate events, festivals, and private parties.
- Affordable Packages: Hiring furniture is often more cost-effective than purchasing, especially for one-time events.
- Professional Setup: The team handles delivery, installation, and removal, saving you stress on the big day.
- Tailored Solutions: Whether it’s an intimate dinner or a large-scale event, they customize packages to suit your needs.
Event Trends: Furniture That Makes a Statement
Modern event styling is about more than just functionality; it’s about making a statement. Here are some trending furniture hire ideas:
- Mix-and-Match Seating: Combining different chair styles adds personality and flair.
- Rustic & Boho Chic: Timber tables paired with rattan lounges and earthy décor are trending for weddings and outdoor events.
- Luxury Lounges: Plush velvet lounges and ottomans create a VIP atmosphere at corporate and gala events.
- Sustainable Furniture: Eco-conscious choices like upcycled wood and reusable décor items are becoming increasingly popular.
With the right furniture hire solutions, you can bring any of these styles to life effortlessly.
Tips for Choosing the Right Furniture Hire Service
- Check the Inventory – Ensure the company has the specific furniture pieces you need.
- Read Reviews – Customer feedback can help you understand service quality.
- Consider Delivery & Setup – Always confirm logistics to avoid last-minute issues.
- Match Your Theme – Choose furniture that aligns with your event’s theme, colors, and style.
- Budget Wisely – Opt for complete hire packages that include setup, styling, and pickup for better value.
Final Thoughts
Event planning can feel overwhelming, but with the right support, it becomes a seamless and enjoyable process. Choosing complete furniture hire solutions for events big and small ensures that every detail of your celebration is covered—from stylish seating to decorative touches that impress your guests.
By partnering with experts like M Event Hire, you can focus on enjoying your special day while professionals handle the setup and styling. Whether it’s a wedding, corporate event, birthday, or festival, the right furniture hire company will help you transform your vision into reality
- GENERAL1 month ago
5 Factors That Affect Tattoo Removal Success
- ENTERTAINMENT2 months ago
Exploring the Kristen Archives: A Treasure Trove of Erotica and More
- LIFESTYLE6 months ago
The Disciplinary Wives Club: Spanking for Love, Not Punishment
- TECHNOLOGY6 months ago
Blog Arcy Art: Where Architecture Meets Art
- ENTERTAINMENT7 months ago
The Ultimate Guide to Shillong Teer Hit Number: How to Predict Your Next Win
- LIFESTYLE1 week ago
Who Is Sandra Orlow?
- LIFESTYLE3 months ago
Berniece Julien: The Private Life of Tyson Beckford’s Partner
- Uncategorized12 months ago
Conrad Fisher Transformation: From Top Student to Troubled Soul