GENERAL
Common Mistakes to Avoid When Sourcing Industrial Equipment Supply
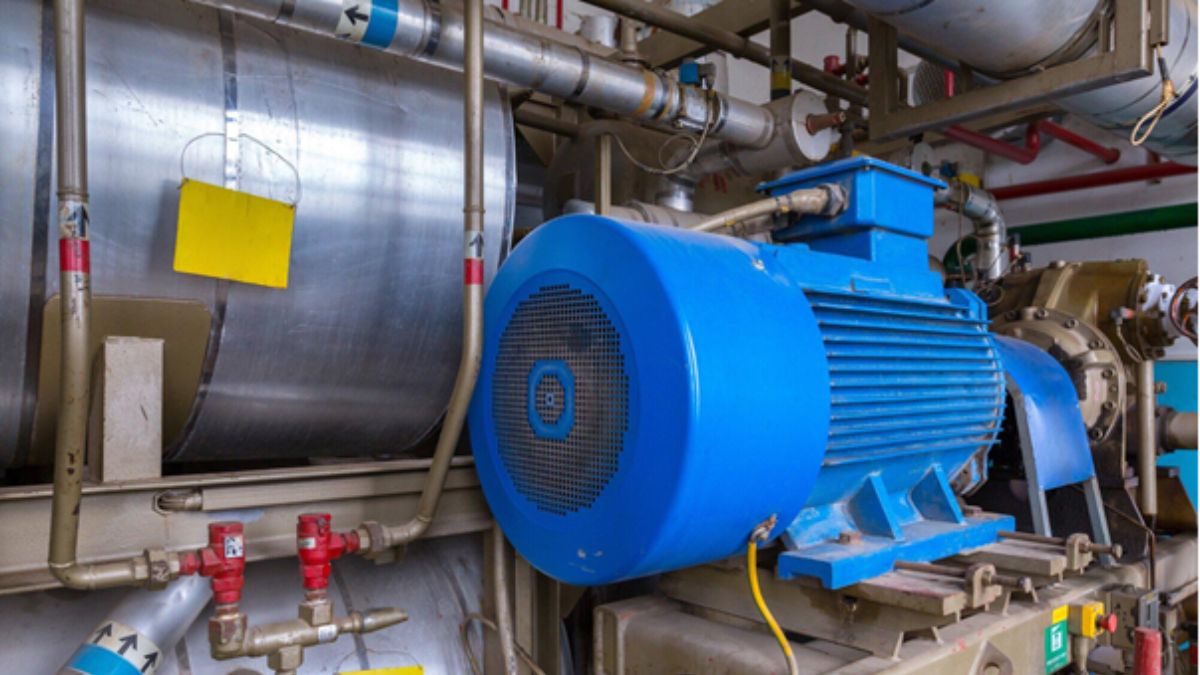
Have you ever faced issues when trying to buy industrial equipment? It may seem simple, but sourcing the right industrial equipment supply can be tricky.
Many companies often make costly mistakes. In the fast-paced world of industrial operations, acquiring the right tools is crucial for success.
But don’t worry. By the end of this blog post, you’ll know how to avoid these common pitfalls and make smart decisions that will save you time and money.
Rushing Supplier Selection
Choosing the right supplier is one of the most important steps in sourcing strategies. Many businesses rush this process and end up with a poor match. Some may choose the first supplier they find or pick one based on price alone.
But there’s more to it. You need to check if the supplier has a good track record and can meet your needs. Without careful supplier selection, you may face delays, low-quality equipment, or even legal problems.
Establishing good communication with potential suppliers is crucial for understanding their capabilities. It’s also wise to assess their financial stability to ensure they can sustain long-term partnerships. Lastly, visiting the supplier’s facilities can provide valuable insights into their operational standards.
Ignoring Cost-Effective Solutions
Focusing on only the upfront cost is another common mistake in equipment purchasing. It’s easy to pick the cheapest option. But is it the best value?
Many companies forget to consider the long-term costs. Will the equipment last? How much maintenance will it need?
A cost-effective solution means looking at the total cost of ownership. This includes the initial price, but also energy use, repairs, and how long the equipment will work well.
Skipping Research on Sourcing Strategies
Every company needs a plan when sourcing industrial equipment. Many don’t take the time to research proper sourcing strategies. They skip steps and end up with poor-quality equipment or unreliable suppliers.
A solid strategy involves comparing suppliers, checking for certifications, and thinking about long-term goals. Don’t fall into the trap of rushing into procurement errors. Taking the time to create a plan will save you a lot of stress.
Overlooking Supplier Contracts
Sometimes businesses skip reviewing the contract with their supplier. This is a big mistake. A contract protects both parties. It should cover everything, like delivery times, payment terms, and what happens if something goes wrong.
Without a clear contract, you may face unexpected issues. For example, your supplier could raise prices or deliver poor-quality products without any penalties. Always review the contract carefully and ensure all details are in writing.
Failing to Check Supplier Reliability
A reliable supplier is key to a smooth procurement process. Some companies skip checking the history of their suppliers. This can lead to major problems later. You should always check if your supplier has a good reputation.
A good example of a reliable supplier is Pro-Tools. Many companies have had great success with them. They provide dependable equipment and services, helping businesses avoid common procurement errors.
Be Smart When Sourcing Industrial Equipment Supply
In the world of industrial equipment supply, mistakes can be costly. Rushing supplier selection, ignoring cost-effective solutions, and skipping research are just a few common errors. Always plan your sourcing strategies carefully and review your supplier contracts.
By avoiding these mistakes, you can save money, time, and headaches. Additionally, building strong relationships with reliable suppliers can enhance your business operations. Constant evaluation and adaptation are key to ensuring long-term success in this dynamic industry.
Did you like this guide? Great! Browse our website for more!
GENERAL
Practicing Mindful Online Behavior
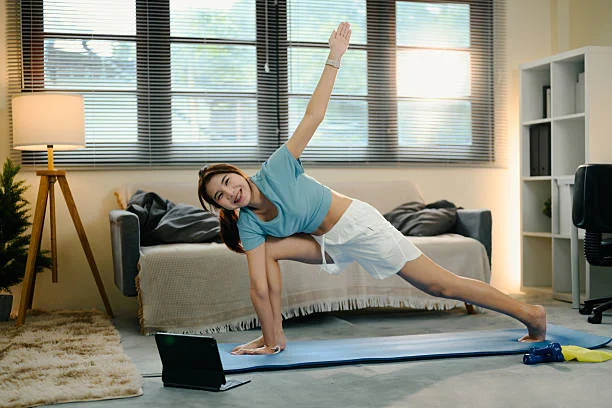
In today’s digital world, we spend a huge part of our lives online—whether it’s scrolling social media, chatting with friends, or managing finances. But it’s easy to get caught up in the endless flow of information and reactions without really thinking about how it affects us. Practicing mindful online behavior means being present, self-aware, and intentional with how we interact in the digital space. This mindset doesn’t just help reduce stress and emotional ups and downs; it also builds healthier relationships with technology and the people we engage with online. For example, those facing financial challenges might find that being mindful about online spending and information helps them avoid pitfalls and seek support like debt relief programs when needed.
Continue your journey: This related article is worth your time.
Understanding Mindfulness in a Digital Context
Mindfulness traditionally means paying attention to the present moment without judgment. When applied to online behavior, it means noticing what you’re doing and why, rather than just reacting automatically. Instead of mindlessly clicking through posts or responding with frustration, you slow down and consider the impact of your actions.
Being mindful online also means recognizing your emotional state before engaging. Are you tired, stressed, or angry? If so, you might want to pause before responding to a message or reading news that could trigger negative feelings. This awareness can prevent unnecessary conflicts and reduce emotional reactivity.
The Emotional Toll of Unchecked Online Habits
Many people don’t realize how much their mood and mental health can be affected by online activities. Constant notifications, comparing ourselves to others, or reading negative comments can increase stress and anxiety. This emotional toll can spill into offline life, affecting relationships and overall well-being.
Practicing mindful online behavior helps break this cycle. By setting boundaries like limiting screen time, choosing positive content, and avoiding toxic interactions, you protect your mental space. When your online experience is calmer and more intentional, you’re less likely to feel overwhelmed or exhausted.
Building Healthier Online Relationships
Online connections are a big part of modern life, but they can sometimes lead to misunderstandings or conflicts. Mindfulness encourages you to communicate with empathy and clarity. Before posting or commenting, think about how your words might be received and whether they add value to the conversation.
This approach fosters more respectful and meaningful interactions. You’re less likely to get pulled into arguments or misunderstandings because you’re choosing your responses thoughtfully. Over time, this creates a more positive online community around you, which benefits your mental health and social network.
Mindful Consumption of Information
The internet offers endless streams of news and information, but not all of it is accurate or helpful. Mindfulness online includes being selective about what you consume and questioning sources before accepting information as true.
Taking time to verify facts and avoid sharing rumors or sensationalized news helps reduce misinformation. It also keeps your online space more positive and less cluttered with negativity. By curating your digital diet carefully, you maintain clearer thinking and reduce stress from conflicting or alarming information.
Financial Mindfulness in the Digital Age
Money management is another area where mindful online behavior plays a crucial role. The convenience of online shopping and digital payments can lead to impulsive spending. Being mindful means pausing before purchases, considering your budget, and avoiding the trap of “buy now, pay later” schemes that can create debt.
If you’re feeling overwhelmed by finances, mindful online behavior includes seeking reliable information and support. This might mean researching and contacting debt relief programs or using budgeting tools online. Taking intentional steps helps you stay in control and avoid financial stress caused by careless online habits.
Practicing Digital Detox and Breaks
Part of mindful online behavior is knowing when to step away. Taking regular breaks from screens and social media can refresh your mind and body. This isn’t about avoiding technology but about creating balance.
During digital detox periods, you might focus on offline activities like reading, exercise, or spending time with loved ones. These breaks help you reset your attention and emotions so that when you return online, you interact more consciously and positively.
Tips for Cultivating Mindful Online Habits
Start small by setting daily or weekly limits on your screen time or social media use. Use apps or phone settings that track and restrict usage if needed. Before responding to messages or posts, take a moment to breathe and reflect.
Ask yourself: Is this reaction helpful? Am I contributing positively? Is this content good for my well-being? Over time, these questions build awareness and control.
Another tip is to create “mindful moments” by scheduling specific times to check emails or social media rather than constantly interrupting your day. This focused approach reduces distraction and improves productivity.
The Long-Term Benefits of Mindful Online Behavior
When you practice mindfulness in the digital world, you gain more than just reduced stress. You build stronger emotional resilience, better relationships, and improved focus. Your online experiences become tools that support your goals rather than obstacles.
Mindfulness online can also improve your overall life satisfaction. By choosing where to put your attention and energy, you reclaim time and mental space that might otherwise be wasted on negative or mindless scrolling.
Final Thoughts
Practicing mindful online behavior is about being intentional with your digital life. It means slowing down, being aware of your feelings and actions, and making choices that support your well-being and relationships. Whether it’s protecting your mental health, building better online connections, or managing finances wisely, mindfulness can transform how you experience the internet. If you’re facing financial stress, remember that mindful decisions online can guide you toward helpful resources like Debt Relief Programs. By embracing this approach, you create a healthier, more balanced digital life that benefits both you and those around you.
Don’t miss out on more great reads—click through our featured posts!
GENERAL
Dumb and Dumber (1994): A Comedy Classic That Defined a Generation
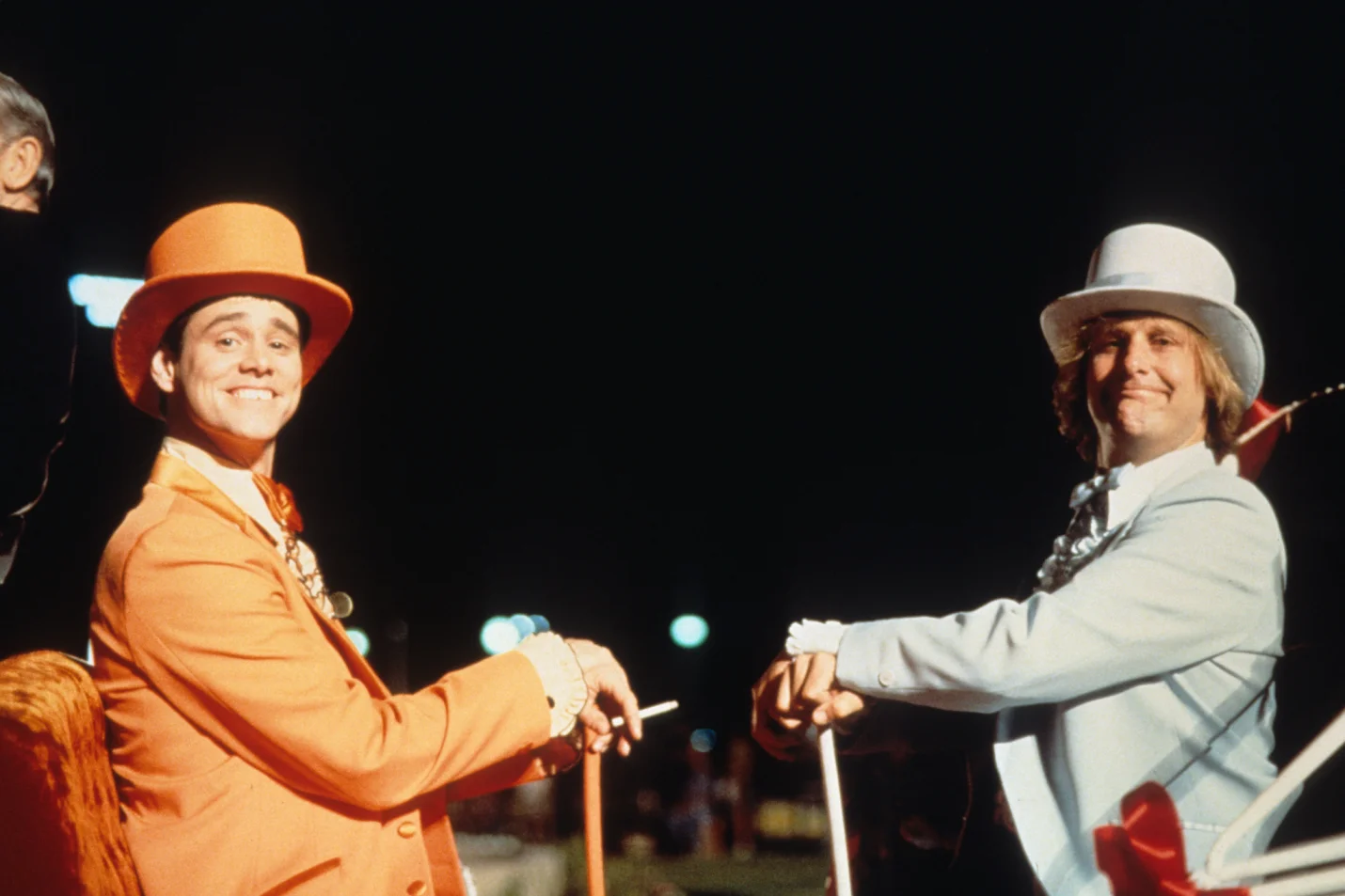
Released in 1994, Dumb and Dumber quickly cemented itself as one of the most beloved and iconic comedy films of the 1990s. Directed by Peter Farrelly and starring the legendary duo Jim Carrey and Jeff Daniels, the movie redefined slapstick and absurd humor for a new generation. With its unforgettable characters, hilarious dialogues, and ridiculous plotlines, Dumb and Dumber became a cult favorite and remains a go-to comedy for fans around the world. The fashion from the film, especially the now-famous Jim Carrey Jacket, also became a pop culture staple, widely recognized in costume parties and nostalgia-themed events.
There’s so much more to discover—browse our related posts!
Plot Overview: An Absurd Road Trip
The story follows two dimwitted but kind-hearted best friends, Lloyd Christmas (Jim Carrey) and Harry Dunne (Jeff Daniels), as they embark on a cross-country journey to return a briefcase to a woman Lloyd fell in love with at first sight. What they don’t realize is that the suitcase is filled with ransom money meant for a kidnapping deal. Their cluelessness leads them into one misadventure after another, involving mistaken identities, run-ins with criminals, and outrageously funny misunderstandings.
Set against the backdrop of snowy Aspen, Colorado, the duo’s journey becomes a series of comedic mishaps that showcase the depth of their friendship and the height of their ignorance. Yet, it’s exactly this mixture of stupidity and sincerity that makes Dumb and Dumber work.
Jim Carrey and Jeff Daniels: The Perfect Comic Pairing
At the time of release, Jim Carrey was skyrocketing to fame with films like Ace Ventura: Pet Detective and The Mask, both released in the same year. His elastic expressions, slapstick timing, and zany energy perfectly matched the tone of Dumb and Dumber. Lloyd Christmas became an unforgettable character thanks to Carrey’s over-the-top physical comedy and childlike charm.
Jeff Daniels, known primarily for serious roles before this film, took a bold risk stepping into the comedic shoes of Harry Dunne. His deadpan delivery and awkwardness complemented Carrey’s hyperactivity, making the duo feel oddly balanced despite their shared idiocy. The chemistry between Carrey and Daniels is undeniable, and it’s what propels the movie from simple silliness to comedic brilliance.
Cultural Impact and Memorable Moments
Few comedies from the ’90s have had as lasting an impact as Dumb and Dumber. Its lines—like “So you’re telling me there’s a chance!”—have become meme-worthy quotes repeated endlessly by fans. The film’s humor, a mix of gross-out gags, wordplay, and physical comedy, struck a chord with audiences, especially teenagers and young adults.
The film inspired fashion trends, Halloween costumes, and parodies for decades. The scene where Lloyd and Harry show up in orange and blue tuxedos is still one of the most referenced movie fashion moments. The movie also redefined what buddy comedies could be, influencing future films like Step Brothers, Harold & Kumar, and even The Hangover series.
Why It Still Works Today
Even after three decades, Dumb and Dumber holds up because of its unapologetic embrace of stupidity. It doesn’t try to be clever or politically correct—it simply dives headfirst into absurdity. There’s no moral lesson or deep message. Instead, the film gives viewers permission to laugh without guilt, offering an escape from the seriousness of life.
Another reason for its staying power is how well it captures the friendship dynamic. Lloyd and Harry may be clueless, but their loyalty to each other is endearing. They stick together through thick and thin, driven by a genuine desire to do what they think is right—even if it makes no sense to anyone else.
Critical Reception and Box Office Success
Critics were initially divided on Dumb and Dumber, with some dismissing it as mindless humor and others praising it for its unfiltered comedic style. Over time, however, the film has been re-evaluated and embraced as a cult comedy classic. It holds a solid rating on review platforms and is often included in “Top Comedy Films of All Time” lists.
Financially, the movie was a massive success. Made on a modest budget of around $17 million, it grossed over $247 million worldwide. This success paved the way for a prequel (Dumb and Dumberer: When Harry Met Lloyd) and a sequel (Dumb and Dumber To), though neither captured the same magic as the original.
The Farrelly Brothers’ Signature Style
Directors Peter and Bobby Farrelly used Dumb and Dumber to launch their successful run in comedy filmmaking. Their signature blend of lowbrow humor and oddly wholesome storytelling became a trendsetter. Later films like There’s Something About Mary and Me, Myself & Irene followed a similar formula—mixing absurdity with heart—and were met with critical and commercial success.
The Farrellys’ ability to find humor in everyday stupidity while maintaining an undercurrent of emotional honesty is what made Dumb and Dumber such a standout. Their direction kept the film focused, even while letting Carrey and Daniels go wild with their improvisations.
Iconic Style: From Haircuts to Tuxedos
Beyond the jokes and gags, the film’s visual style became iconic in its own right. Lloyd’s bowl cut, Harry’s shaggy look, and their bright-colored tuxedos are unforgettable. Their wardrobe wasn’t just funny—it was symbolic of how out-of-place they were in a world they didn’t understand.
Fans still cosplay as Lloyd and Harry at conventions, and the costumes have become staples at 90s-themed parties. Even casual outfits, like Lloyd’s orange hoodie or Harry’s shearling coat, have become associated with the film. These details have given the film a unique identity that goes beyond its humor.
Legacy of Laughter
Dumb and Dumber may not be everyone’s cup of tea, but for those who appreciate juvenile humor and over-the-top antics, it remains unmatched. Its influence can be seen in countless modern comedies, and it continues to be a benchmark for comedic timing and character chemistry.
What makes the film truly special is that it never tries to be more than it is. It embraces its title, leans into the ridiculous, and celebrates idiocy in a way that few films dare to do. That commitment to pure comedy is what keeps fans coming back.
Final Thoughts
For all its silliness, Dumb and Dumber remains a landmark film in the comedy genre. It helped launch Jim Carrey into superstardom, showcased Jeff Daniels’ surprising range, and gave audiences something rare: a genuinely funny, endlessly quotable, and surprisingly sweet story of two fools just trying to do something right. From outrageous fashion to ridiculous one-liners, its charm lies in its unapologetic embrace of absurdity. Whether you’re watching it for the first time or the fiftieth, it never fails to deliver laughs—especially when you spot the timeless Jeff Daniels hoodie that fans still talk about today.
Having more content? Dive into our latest posts now!
GENERAL
Everything About project valvrein
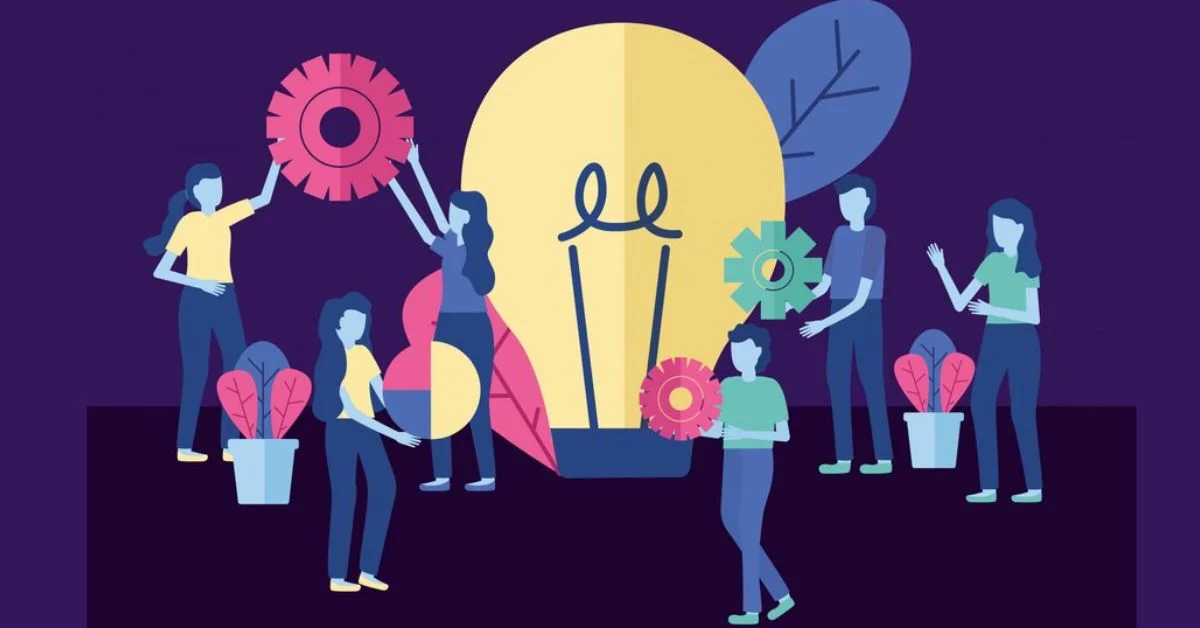
Introduction to Project Valvrein
Welcome to the thrilling world of Project Valvrein, where creativity meets innovation in a masterpiece in the making. Dive into a realm where imagination knows no bounds and possibilities are endless. Join us on this exciting journey as we uncover the vision, passion, and dedication behind one of the most anticipated projects in the gaming industry. Gear up for an adventure like no other – Project Valvrein awaits!
The Vision Behind the Project
Project Valvrein is more than just a game; it’s a visionary masterpiece in the making. The creators behind this ambitious project have set out to redefine the gaming experience, pushing boundaries and challenging conventions. Their vision is one of immersive storytelling, captivating visuals, and groundbreaking gameplay that will transport players to a world like no other.
At the core of their vision is a commitment to innovation and creativity. They aim to create an interactive universe where players can truly lose themselves in an epic adventure filled with intrigue, mystery, and wonder. With meticulous attention to detail and a passion for excellence, the team behind Project Valvrein is dedicated to delivering an unforgettable gaming experience that will leave players craving for more.
By combining cutting-edge technology with artistic flair, they are shaping a new standard in gaming entertainment that promises to captivate audiences worldwide. Stay tuned as we delve deeper into the creative minds behind Project Valvrein and uncover the magic that fuels their extraordinary vision.
The Creative Team and Their Roles
Project Valvrein boasts a talented creative team, each member bringing their unique skills and expertise to the table. The lead game designer, Sarah, is known for her innovative gameplay mechanics that push boundaries in the gaming world. John, the art director, brings breathtaking visuals to life with his eye for detail and passion for immersive worlds.
The narrative designer, Alex, weaves intricate storylines filled with rich lore and engaging plot twists that keep players on the edge of their seats. Mark handles sound design like a maestro, creating captivating soundtracks that elevate the gaming experience to new heights.
Together, this dynamic team collaborates seamlessly to bring Project Valvrein’s vision to fruition. Each individual plays a crucial role in shaping the game into a masterpiece that promises to captivate gamers worldwide.
ALSO READ: TYRONE’S UNBLOCKED GAMES SLOPE: A THRILLING ADVENTURE IN THE GAMING WORLD
Building the World of Valvrein
In the development of Project Valvrein, creating a captivating and immersive world was paramount. The creative team worked tirelessly to craft a realm that would draw players in from the moment they entered the game.
Every aspect of Valvrein’s world was meticulously designed, from its landscapes to its architecture, each detail contributing to the overall atmosphere and storytelling. The team drew inspiration from various sources, blending fantasy elements with innovative ideas to bring this unique world to life.
Through intricate world-building techniques, they were able to establish not just a backdrop for gameplay but a living, breathing environment filled with history, culture, and mystery. Players will find themselves exploring ancient ruins, bustling cities, lush forests – each location teeming with secrets waiting to be uncovered.
The attention to detail in constructing Valvrein’s world sets it apart as an experience that transcends traditional gaming boundaries. As players journey through this richly imagined landscape, they will discover wonders beyond their wildest imaginations – all within the vast expanse of Project Valvrein.
Developing Characters and Storylines
In the world of Project Valvrein, character development is a cornerstone of the storytelling experience. Each character is meticulously crafted to have depth and complexity, adding layers to the immersive narrative. From courageous heroes to cunning villains, every character plays a vital role in shaping the evolving storyline.
The creative team behind Project Valvrein delves deep into each character’s motivations, fears, and aspirations. By exploring their backstories and relationships with one another, they bring authenticity and relatability to the game’s cast. This attention to detail ensures that players form emotional connections with the characters as they embark on their journey through Valvrein.
As the storylines unfold, unexpected twists and turns keep players on their toes, challenging them to think critically and make impactful decisions that shape the outcome of their adventure. With rich dialogue and dynamic interactions between characters, Project Valvrein sets a new standard for narrative-driven gameplay.
ALSO READ: TR2GAMES SLOPE: A THRILLING JOURNEY INTO GAMING EXCITEMENT
Crafting Stunning Visuals and Soundtracks
Enter the world of Project Valvrein, where visuals and soundtracks intertwine to mesmerize players. The creative team meticulously crafts stunning visuals that transport players to a realm filled with breathtaking landscapes and intricate details. Each frame is a work of art, capturing the essence of this fantastical universe.
The soundtrack of Project Valvrein is more than just background music; it’s an immersive experience that enhances every moment of gameplay. From epic battle themes to haunting melodies, the music sets the tone for each encounter and deepens the emotional connection with the story.
Every visual element is carefully designed to evoke emotions and immerse players in the rich tapestry of Valvrein. The attention to detail shines through in every pixel, creating a truly immersive gaming experience. And paired with a masterfully composed soundtrack, players are transported into a world where fantasy becomes reality.
Challenges and Triumphs in the Making of Valvrein
The journey of creating Project Valvrein was not without its challenges. The team faced obstacles ranging from technical issues to creative differences, yet they persevered with unwavering determination. As the project evolved, new ideas clashed with established concepts, requiring compromise and innovation.
One of the biggest triumphs was overcoming a major setback in the development process. With resilience and teamwork, the creative minds behind Valvrein found solutions that pushed the project forward. Each hurdle served as an opportunity for growth and improvement, shaping Valvrein into a truly unique gaming experience.
Through dedication and passion, the team transformed setbacks into stepping stones towards success. The challenges faced during development ultimately fueled their creativity and commitment to delivering a masterpiece in the making.
ALSO READ: DHAMAKA ZONE CELEBRITY GOSSIP
Anticipation for the Release
As the release date for Project Valvrein draws near, fans around the world are buzzing with excitement. With teasers and trailers showcasing the stunning visuals and captivating storyline, anticipation is at an all-time high.
Gamers eagerly await the chance to immerse themselves in the richly detailed world of Valvrein, filled with mystery, intrigue, and adventure. The promise of a truly immersive gaming experience has set expectations soaring.
The creative team’s dedication and passion for their craft shine through in every aspect of the project, from character development to sound design. This level of commitment has only fueled fans’ anticipation further.
With each new update or sneak peek into the game’s development process, enthusiasm reaches new heights. The countdown to launch day is met with eager anticipation as players prepare to embark on an unforgettable journey through Valvrein.
Stay tuned as we continue to uncover more about this highly anticipated release!
Impact on the Gaming Industry
Project Valvrein is poised to have a significant impact on the gaming industry. With its innovative gameplay mechanics and immersive storytelling, it has the potential to set a new standard for interactive entertainment.
The meticulous attention to detail in crafting the world of Valvrein showcases a level of dedication that is sure to inspire other game developers. The stunning visuals and captivating soundtracks created for the game are raising the bar for aesthetic excellence in gaming.
By pushing boundaries and exploring new horizons, Project Valvrein challenges conventional norms and opens up exciting possibilities for future game development. Its success could pave the way for more ambitious projects that prioritize creativity and originality over commercial trends.
As anticipation grows for the release of Project Valvrein, gamers around the world are eagerly awaiting their chance to delve into this virtual masterpiece. The impact of this game on the industry is undeniable, marking a turning point towards more sophisticated and engaging gaming experiences.
ALSO READ: EVERYTHING ABOUT NILES GARDEN CIRCUS TICKETS
Conclusion: The Future of Project Valvrein
The future of Project Valvrein is filled with endless possibilities and excitement. As the release date draws near, fans and critics alike are eagerly anticipating the unveiling of this gaming masterpiece. With its innovative gameplay, captivating storyline, and breathtaking visuals, Project Valvrein has the potential to make a significant impact on the gaming industry.
As we look ahead to what lies in store for this ambitious project, one thing is certain – Project Valvrein is poised to redefine the gaming landscape and leave a lasting impression on players around the world. Stay tuned for more updates and get ready to embark on an unforgettable journey into the world of Valvrein.
- GENERAL4 weeks ago
5 Factors That Affect Tattoo Removal Success
- ENTERTAINMENT1 month ago
Exploring the Kristen Archives: A Treasure Trove of Erotica and More
- TECHNOLOGY5 months ago
Blog Arcy Art: Where Architecture Meets Art
- LIFESTYLE5 months ago
The Disciplinary Wives Club: Spanking for Love, Not Punishment
- LIFESTYLE2 weeks ago
Who Is Sandra Orlow?
- LIFESTYLE2 months ago
Berniece Julien: The Private Life of Tyson Beckford’s Partner
- GENERAL8 months ago
Worldwide Elephant List: Complete Reserves and Map 2024
- ENTERTAINMENT1 month ago
Kiss KH: The Streaming Platform Redefining Digital Engagement and Cultural Currents