BUSINESS
Essential Insights into Conveyor Impact Rollers
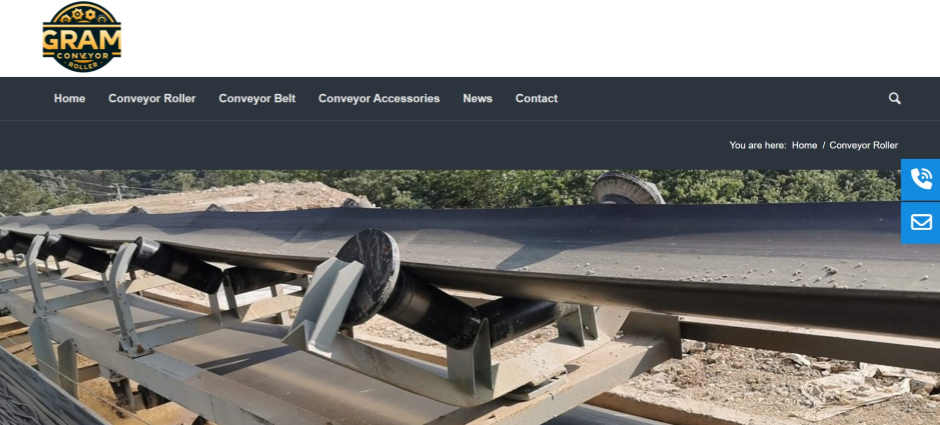
Conveyor impact rollers are specialized components designed to absorb and dissipate the impact forces from heavy, abrasive, or sharp materials being loaded onto conveyor belts. These conveyor rollers play a crucial role in protecting the conveyor system, reducing wear and tear, and ensuring efficient operation. Nylon conveyor rollers, on the other hand, are made from durable synthetic polymers known for their strength, lightweight properties, and resistance to corrosion and chemicals. These conveyor rollers are highly relevant in modern industries where hygiene, maintenance, and operational efficiency are paramount. Nylon rollers offer several advantages, including enhanced durability, reduced noise, and lower maintenance costs, making them indispensable in sectors such as food processing, pharmaceuticals, packaging, and automotive manufacturing.
Key Features of Conveyor Impact Rollers
Conveyor impact rollers are crucial components designed to endure harsh industrial environments and protect conveyor systems from damage caused by heavy, abrasive, or sharp materials.
Design and Construction
Core Material: Impact rollers typically feature a robust core made from high-strength steel or aluminum. This core provides the necessary structural integrity to handle substantial loads without deforming.
Cushioning Layer: Surrounding the core is a thick layer of shock-absorbing material, such as rubber or polyurethane. This layer is essential for dissipating the energy from impacts, thereby reducing the stress on the conveyor belt.
Sealed Bearings: High-quality impact rollers often include sealed bearings to protect against dust and debris. Sealed bearings ensure smooth rotation and extend the lifespan of the rollers by reducing wear and tear.
Impact Absorption Capabilities
Energy Dissipation: The primary function of impact rollers is to absorb and dissipate the kinetic energy from heavy and fast-moving materials. The cushioning layer compresses upon impact, spreading the force over a larger area and minimizing the impact on the conveyor belt.
Protection of Conveyor System: By absorbing these forces, impact rollers prevent damage to the conveyor belt and structure, reducing maintenance needs and extending the overall lifespan of the system.
Common Sizes and Dimensions
Variety of Sizes: Impact rollers are available in a range of sizes and dimensions to accommodate different conveyor systems. Common diameters range from 50mm to 200mm, with lengths varying to fit specific conveyor widths.
Custom Dimensions: Custom-sized impact rollers can be manufactured to meet unique requirements, ensuring compatibility with specialized conveyor setups and specific operational needs.
Role of Nylon in Impact Rollers
Material Benefits: Incorporating nylon into impact rollers offers several advantages. Nylon is lightweight yet strong, providing durability without adding significant weight to the conveyor system. This reduces the overall load and energy consumption.
Corrosion Resistance: Nylon is highly resistant to corrosion, making it ideal for use in environments where exposure to moisture, chemicals, and other corrosive substances is common.
Low Friction and Noise: Nylon’s low friction coefficient ensures smooth operation, reducing wear on both the rollers and the conveyor belt. Additionally, nylon helps in minimizing operational noise, contributing to a quieter and more comfortable working environment.
Extended Lifespan: The durability and resistance of nylon to various industrial stresses ensure that nylon impact rollers have a longer lifespan, resulting in lower maintenance costs and reduced downtime.
In summary, the key features of conveyor impact rollers include their robust design and construction, effective impact absorption capabilities, availability in various sizes and dimensions, and the significant role of nylon in enhancing performance. These features make impact rollers indispensable in protecting conveyor systems and ensuring efficient, long-term operation across various industrial applications.
Applications of Conveyor Impact Rollers
Conveyor impact rollers are essential in various heavy-duty industries, providing crucial protection and efficiency improvements in environments where the material handling process involves significant impact and stress.
Mining
Role in Mining Operations: In the mining industry, conveyor systems are used to transport heavy and abrasive materials such as ore, coal, and gravel. Impact rollers are strategically placed at loading points to absorb the shock from falling materials.
Benefits: By mitigating the impact forces, these rollers protect the conveyor belt and structure from damage, reducing maintenance needs and downtime. This is particularly important in mining, where equipment reliability is critical for continuous operations.
Integration of Nylon Rollers: Nylon conveyor rollers are also utilized in mining for their durability and corrosion resistance. They are often used in conjunction with impact rollers to ensure smooth, efficient material transport, especially in areas with exposure to moisture and chemicals.
Construction
Role in Construction Sites: Construction sites involve the handling of heavy materials such as concrete, steel beams, and aggregate. Conveyor systems equipped with impact rollers are used to transport these materials efficiently and safely.
Benefits: Impact rollers at loading points prevent damage to the conveyor belt from the high-impact loads common in construction, ensuring a longer lifespan and reduced operational costs.
Integration of Nylon Rollers: Nylon rollers are employed in construction conveyor systems for their lightweight and easy maintenance properties. They help reduce the overall weight of the conveyor system, making it more energy-efficient and easier to install and maintain.
Heavy Manufacturing
Role in Manufacturing Plants: Heavy manufacturing industries, such as automotive and machinery production, require the movement of large, heavy components. Impact rollers are crucial in these settings to handle the impact of loading and unloading heavy parts.
Benefits: These rollers absorb shock and reduce the risk of conveyor belt damage, maintaining smooth operation and minimizing interruptions in the manufacturing process.
Integration of Nylon Rollers: Nylon conveyor rollers are integrated into these systems to provide smooth, quiet operation and resistance to chemicals and oils commonly used in manufacturing processes. This combination ensures both durability and efficiency.
Integration of Nylon Conveyor Rollers in These Applications
Complementary Use: In all these industries, nylon conveyor rollers complement impact rollers by providing additional benefits such as corrosion resistance, lightweight construction, and reduced noise levels. This integration enhances the overall performance of the conveyor system.
Specific Roles: While impact rollers handle the heavy impact and load-bearing functions, nylon rollers are used in other parts of the conveyor system to ensure smooth and efficient transport, especially in areas where the risk of chemical exposure and moisture is high.
Efficiency and Maintenance: The use of nylon rollers reduces the wear on conveyor belts and other components, leading to lower maintenance costs and longer system lifespans. This is particularly beneficial in industries where operational efficiency and minimal downtime are crucial.
Conveyor impact rollers are indispensable in industries such as mining, construction, and heavy manufacturing due to their ability to absorb shock and protect conveyor systems. The integration of nylon conveyor rollers in these applications further enhances system performance, offering durability, corrosion resistance, and reduced maintenance needs. Together, impact and nylon rollers create a robust, efficient conveyor system capable of handling the demands of heavy-duty industrial environments.
Sizing and Selection of Conveyor Impact Rollers
Selecting the correct size and type of conveyor impact rollers is crucial for ensuring the efficiency and longevity of your conveyor system. Here’s a detailed guide on the importance of correct sizing, how to choose the right size, available customization options, and the benefits of nylon material in impact roller customization.
Importance of Correct Sizing
Optimal Performance: Correctly sized impact rollers ensure optimal performance by providing the necessary support and impact absorption tailored to the specific needs of the conveyor system. Improperly sized rollers can lead to inadequate impact absorption, increased wear and tear, and potential damage to the conveyor belt and structure.
Load Capacity: Ensuring the rollers are the right size for the load they will carry prevents overloading, which can cause premature failure of the rollers and associated conveyor components.
Operational Efficiency: Proper sizing contributes to the smooth operation of the conveyor, minimizing downtime and maintenance costs. It also ensures that the materials are transported efficiently without causing undue stress on the system.
Guide to Choosing the Right Size
Assessing Load Requirements: Determine the maximum weight and type of materials the conveyor will handle. This information is essential for selecting rollers that can support the load without deforming or failing.
Conveyor Dimensions: Measure the width and length of the conveyor system to ensure that the rollers fit correctly. The diameter and length of the rollers must match the dimensions of the conveyor frame and the width of the belt.
Impact Zone Analysis: Identify the high-impact zones where materials are loaded onto the conveyor. These areas require rollers with enhanced impact absorption capabilities. Consider factors such as drop height and material speed.
Roller Material and Design: Choose rollers made from materials that can withstand the environmental conditions and operational demands. For example, in corrosive environments, nylon rollers are preferable due to their chemical resistance.
Customization Options
Custom Dimensions: Manufacturers offer customization of roller dimensions to fit non-standard conveyor systems. This includes specific diameters, lengths, and shaft sizes tailored to unique requirements.
Material Selection: Customization can include the choice of materials for both the core and the cushioning layer. Options such as steel cores with nylon or rubber cushioning provide a balance of strength and impact absorption.
Enhanced Features: Custom features such as additional sealing, specialized bearings, and specific surface coatings can be added to meet the operational and environmental demands of the application.
Color and Branding: Custom colors and branding options are available for easy identification and integration into existing conveyor systems.
Benefits of Nylon Material in Impact Roller Customization
Durability and Strength: Nylon provides excellent durability and impact resistance, making it suitable for high-impact applications. Its strength ensures that the rollers maintain their shape and functionality under heavy loads.
Corrosion Resistance: Nylon’s resistance to chemicals, moisture, and corrosive substances makes it ideal for use in harsh environments. This extends the lifespan of the rollers and reduces maintenance costs.
Lightweight: Nylon is lighter than many other materials, reducing the overall weight of the conveyor system. This improves energy efficiency and makes installation and maintenance easier.
Low Friction and Noise: Nylon’s low friction coefficient ensures smooth operation, reducing wear on the conveyor belt and minimizing noise levels. This is beneficial in environments where noise reduction is important.
Versatility: Nylon can be easily molded and customized to specific shapes and sizes, providing flexibility in design and allowing for tailored solutions that meet specific operational needs.
The correct sizing and selection of conveyor impact rollers are vital for the efficient and reliable operation of conveyor systems. Understanding load requirements, conveyor dimensions, and impact zones helps in choosing the right size. Customization options allow for tailored solutions, and the use of nylon material offers significant benefits, including durability, corrosion resistance, lightweight, and low friction. By carefully selecting and customizing impact rollers, businesses can enhance the performance and longevity of their conveyor systems.
Top Conveyor Impact Roller Manufacturers
Choosing the right conveyor impact roller manufacturer is essential to ensure the quality, reliability, and efficiency of your conveyor system. Here are some of the top manufacturers in the industry, along with their innovations, quality considerations, and focus on nylon conveyor rollers.
Market Leaders
GRAM Conveyor
Overview: GRAM Conveyor is renowned for its high-quality conveyor rollers and extensive industry experience. They are recognized for their commitment to innovation, quality, and customer satisfaction.
Innovations: GRAM Conveyor has developed advanced manufacturing techniques that enhance the durability and performance of their impact rollers. Their focus on continuous improvement and adoption of cutting-edge technology ensures their products meet the highest standards.
Quality and Durability: GRAM Conveyor adheres to stringent quality control measures, ensuring that their rollers are durable and reliable. They use premium materials and advanced engineering to create impact rollers that withstand harsh industrial conditions.
Nylon Conveyor Rollers: GRAM offers a range of nylon conveyor rollers known for their strength, corrosion resistance, and lightweight properties. These rollers are ideal for applications requiring durability and efficiency.
Innovations and Technologies
Interroll
Innovations: Interroll is a global leader in conveyor technology, known for its innovative solutions. They utilize state-of-the-art manufacturing processes, including precision engineering and automation, to produce high-performance impact rollers.
Technologies: Interroll’s use of advanced materials and designs ensures their rollers provide excellent impact absorption and durability. Their rollers are engineered to minimize downtime and maintenance, enhancing overall operational efficiency.
Nylon Integration: Interroll integrates nylon in their roller designs to offer benefits such as low friction, noise reduction, and resistance to chemicals and moisture.
Quality and Durability Considerations
Rexnord
Quality: Rexnord places a strong emphasis on quality control and adherence to international standards. Their manufacturing processes include rigorous testing and inspection to ensure each roller meets high-performance criteria.
Durability: Rexnord’s impact rollers are designed for longevity, with features that enhance their resistance to wear and tear. They use high-strength materials and robust construction techniques to create rollers that can handle heavy-duty applications.
Nylon Rollers: Rexnord’s range of nylon rollers offers excellent durability and impact resistance, making them suitable for various industrial environments. Their nylon rollers are designed to provide long-lasting performance and reduce maintenance costs.
Leading Manufacturers of Nylon Conveyor Rollers
Hilman Rollers
Overview: Hilman Rollers is a leading manufacturer specializing in heavy-duty rollers. Their products are known for their strength, reliability, and innovative designs.
Nylon Roller Features: Hilman’s nylon rollers are engineered to offer high load capacity, corrosion resistance, and low maintenance. They are designed to meet the demands of industries such as mining, construction, and manufacturing.
Quality and Durability: Hilman ensures that their nylon rollers are manufactured to the highest quality standards. They use premium nylon materials and advanced production techniques to create rollers that are both durable and efficient.
Flexco
Overview: Flexco is a well-respected name in the conveyor industry, known for its comprehensive range of conveyor products and solutions.
Innovations: Flexco continuously invests in research and development to improve their products. They offer innovative solutions that enhance the performance and reliability of conveyor systems.
Nylon Rollers: Flexco’s nylon rollers are designed for durability and efficiency. They provide excellent resistance to wear, chemicals, and moisture, making them ideal for a wide range of applications.
Selecting a top conveyor impact roller manufacturer involves considering factors such as innovation, quality, and durability. Market leaders like GRAM Conveyor, Interroll, Rexnord, Hilman Rollers, and Flexco are recognized for their high-quality products and commitment to customer satisfaction. Their use of advanced technologies and materials, including nylon, ensures that their rollers offer superior performance, longevity, and efficiency in various industrial applications.
Conveyor impact rollers are essential for protecting conveyor systems from heavy, abrasive, or sharp materials. Key takeaways include the importance of correct sizing and selection, the benefits of customization, and the advantages of nylon rollers, such as durability, corrosion resistance, and low friction. To maximize performance, it is best to conduct regular maintenance, choose the right materials for specific applications, and work with reputable manufacturers like GRAM Conveyor and Interroll. Future trends in conveyor impact rollers point towards increased use of advanced materials like nylon for enhanced durability and efficiency. Innovations in manufacturing technologies and smart monitoring systems will further improve roller performance, reducing downtime and operational costs.
BUSINESS
Top 10 Tips for Choosing Reliable Moving Services in Washington DC
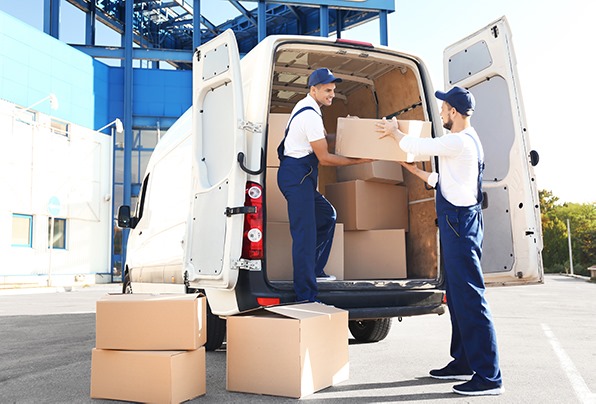
Planning a move in the nation’s capital can feel overwhelming, especially when it comes to choosing the right movers. With so many companies offering moving services Washington DC, it’s essential to know what to look for to ensure your belongings are handled with care and professionalism. Below are ten practical tips that will help you make the best decision for a smooth and stress-free move.
1. Check Licensing and Insurance
The first step in choosing a reliable moving company is to confirm that they are properly licensed and insured. Legitimate movers must follow federal and state regulations, and having insurance guarantees that your belongings are covered in case of damage or loss. Always ask for proof of licensing and insurance before signing any contract.
2. Read Reviews and Testimonials
Customer experiences can give you valuable insights into a moving company’s reliability. Browse online reviews, testimonials, and ratings on trusted platforms. Pay attention to how the company responds to complaints—it shows their level of professionalism and commitment to resolving issues.
3. Get Multiple Quotes
Don’t settle for the first moving company you contact. Request at least three estimates from different providers. Compare the services included, overall pricing, and any extra fees. Be cautious of quotes that are unusually low, as they may indicate hidden charges or poor service quality.
4. Ask About Experience in Washington DC
Washington DC has unique challenges, including heavy traffic, narrow streets, and strict building regulations. A company with local experience knows how to navigate these obstacles efficiently. Ask how long they’ve been serving the DC area and whether they have handled moves similar to yours.
5. Understand the Services Offered
Not all moving companies provide the same services. Some offer full-service moving with packing, storage, and unpacking options, while others handle only transportation. Clarify what’s included in your package and whether there are additional costs for packing materials or special items like pianos or antiques.
6. Verify Professionalism and Equipment
Reliable movers should arrive with clean, well-maintained trucks and professional moving equipment. Staff should be polite, uniformed, and trained in handling items safely. Professional presentation often reflects the quality of service you can expect throughout your move.
7. Ask About Estimates and Contracts
Make sure your moving company provides a written estimate. Ask whether it’s binding or non-binding, and read the contract carefully to avoid surprises. A reliable mover will explain the terms clearly and give you documentation that protects both parties.
8. Look for Transparent Communication
Clear communication is one of the hallmarks of a trustworthy moving service. The company should answer your questions promptly, explain their policies, and give you realistic timelines. If you find it difficult to get straight answers, consider it a red flag.
9. Check for Hidden Fees
Some movers may charge extra for stairs, long carries, or heavy items. Before signing a contract, ask about potential hidden fees to avoid unexpected costs on moving day. Transparency in pricing is a sign of a trustworthy company.
10. Trust Your Instincts
Finally, trust your intuition. If something doesn’t feel right—whether it’s unprofessional behavior, vague answers, or a lack of transparency—it’s better to walk away. A reliable moving company will give you peace of mind, not additional stress.
Conclusion
Finding the right moving service in Washington DC takes research, comparison, and careful consideration. By checking credentials, reading reviews, and asking the right questions, you can choose movers who will handle your belongings safely and efficiently. Use these ten tips to guide your search and ensure a smooth transition to your new home.
BUSINESS
Pikruos: Your Partner in Business Technology Solutions
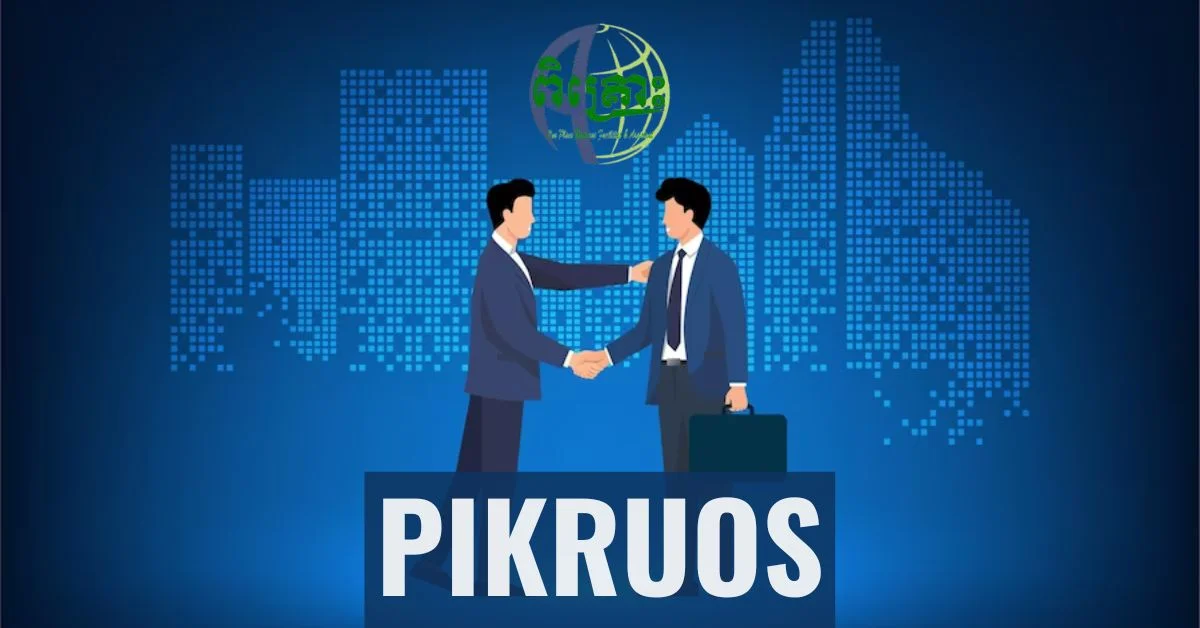
Introduction to Pikruos
In today’s fast-paced digital landscape, businesses are constantly seeking ways to improve efficiency and stay ahead of the competition. Enter Pikruos—a dynamic partner dedicated to delivering cutting-edge technology solutions tailored for your unique business needs. Whether you’re a start-up or an established enterprise, navigating the complex world of technology can be daunting. That’s where Pikruos shines, providing exceptional support that empowers your organization to thrive in a tech-driven environment. With innovative services designed to streamline operations and enhance productivity, it’s time to explore how partnering with Pikruos can transform your business journey.
The Importance of Technology Solutions in Business
In today’s fast-paced business landscape, technology solutions are no longer optional; they are essential. Companies rely on these tools to streamline operations and enhance productivity.
Effective technology solutions can automate tedious tasks, freeing up valuable time for teams to focus on strategic initiatives. This efficiency drives growth and innovation.
Moreover, the right tech can improve customer experiences. Businesses that embrace digital transformation often see a boost in engagement and satisfaction.
Data-driven insights enable firms to make informed decisions quickly. Organizations harnessing technology stay ahead of competitors by adapting swiftly to market changes.
Security is another crucial aspect. Robust technology solutions safeguard sensitive information against cyber threats, ensuring trust with clients and stakeholders alike.
Investing in effective business technologies paves the way for sustainable success in an ever-evolving environment. Adapting to these advancements keeps businesses agile and competitive.
Services Offered by Pikruos
Pikruos provides a diverse range of technology solutions tailored to meet the unique needs of businesses. From IT consulting to software development, every service is designed with efficiency in mind.
Their cloud services enable seamless data access and enhanced collaboration for teams. With robust security measures, Pikruos ensures that your information remains protected at all times.
Custom software solutions allow businesses to streamline operations effectively. Whether it’s a mobile app or an enterprise system, their innovative approach prioritizes user experience and functionality.
Additionally, Pikruos offers comprehensive support and maintenance services. This way, clients can focus on growth while knowing their technology infrastructure is well cared for.
With ongoing training and resources provided by experts, businesses are empowered to adapt swiftly in today’s fast-paced digital landscape. The commitment to customer satisfaction sets Pikruos apart as a true partner in business technology solutions.
Real World Examples of Pikruos’ Success
Pikruos has transformed businesses across various industries through innovative technology solutions. One notable case involved a mid-sized retail company struggling with inventory management. Pikruos implemented an advanced tracking system that streamlined operations, significantly reducing overstock and stockouts.
In another instance, a healthcare provider faced challenges in patient data handling. With Pikruos’ customized software solution, they enhanced data security while improving access for medical staff. This led to faster patient care and increased satisfaction rates.
Additionally, a startup in the tech sector benefited from Pikruos’ strategic consulting services. By optimizing their digital presence and automating workflows, they achieved impressive growth within months.
These examples illustrate how tailored technological interventions by Pikruos can drive efficiency and success for diverse organizations. Each story reflects their commitment to understanding unique business needs and delivering impactful results.
Why Choose Pikruos for Your Business Technology Needs?
Choosing Pikruos means investing in innovation and expertise. With a team of seasoned professionals, we deliver tailored solutions that align with your specific business goals.
Our commitment to quality sets us apart. We understand the unique challenges businesses face today and provide strategies that drive growth and efficiency.
Pikruos prioritizes customer satisfaction above all. Our collaborative approach ensures you are involved throughout the process, fostering transparency and trust.
We leverage cutting-edge technology to streamline operations. This not only boosts productivity but also enhances user experience across your organization.
When you partner with Pikruos, you’re choosing a long-term ally in navigating the complexities of modern business technology. We adapt to industry changes swiftly, ensuring your business remains competitive in an ever-evolving landscape.
Customer Testimonials and Reviews
Pikruos has garnered a multitude of positive reviews from satisfied clients who appreciate the company’s commitment to excellence. Customers often highlight the personalized approach taken by the team, ensuring that each solution is tailored specifically to their business needs.
One client shared how Pikruos transformed their outdated systems into streamlined processes, resulting in significant efficiency gains. This success story resonates with many who have experienced similar transformations.
Another testimonial praised Pikruos for its responsive customer support. Clients feel reassured knowing they can rely on expert assistance whenever challenges arise.
Many businesses value transparency and communication throughout projects. Feedback indicates that Pikruos excels in keeping stakeholders informed at every stage, fostering trust and collaboration.
Such endorsements showcase not just technical capability but also a genuine dedication to helping businesses thrive through innovative technology solutions.
Conclusion: Partnering with Pikruos for a Successful Future
Choosing Pikruos as your partner in business technology solutions can set your company on a path to success. With their extensive range of services tailored for various industries, they understand the unique challenges businesses face today. Their commitment to delivering effective technology solutions ensures that you stay ahead of the competition.
Customer testimonials highlight not just satisfaction but genuine transformations within organizations that have chosen Pikruos. The real-world examples demonstrate how businesses have thrived with the right technological support and guidance.
By collaborating with Pikruos, you’re not just opting for a service provider; you’re investing in a partnership focused on innovation and growth. This collaboration promises to equip your business with the tools necessary for navigating an ever-evolving digital landscape, ultimately leading towards lasting success.
FAQs
What is Pikruos?
Pikruos is a business technology solutions provider that offers tailored IT services such as software development, cloud solutions, consulting, and support to help businesses thrive in a digital-first world.
How does Pikruos’s help businesses improve efficiency?
Pikruos’s streamlines business operations by offering automation, secure data access, and custom software—freeing up time for strategic growth and innovation.
Which industries benefit most from Pikruos’s solutions?
Pikruos’s serves a wide range of industries including retail, healthcare, and tech startups—providing customized solutions to meet unique operational challenges.
What sets Pikruos’s apart from other IT service providers?
Pikruos’s stands out for its personalized approach, transparent collaboration, expert consulting, and long-term support that adapts with business needs.
Does Pikruos provide ongoing support and training?
Yes, Pikruos offers comprehensive maintenance and training to ensure clients can confidently manage their tech infrastructure and stay updated with the latest tools.
BUSINESS
Transforming Events with Complete Furniture Hire Solutions for Every Occasion
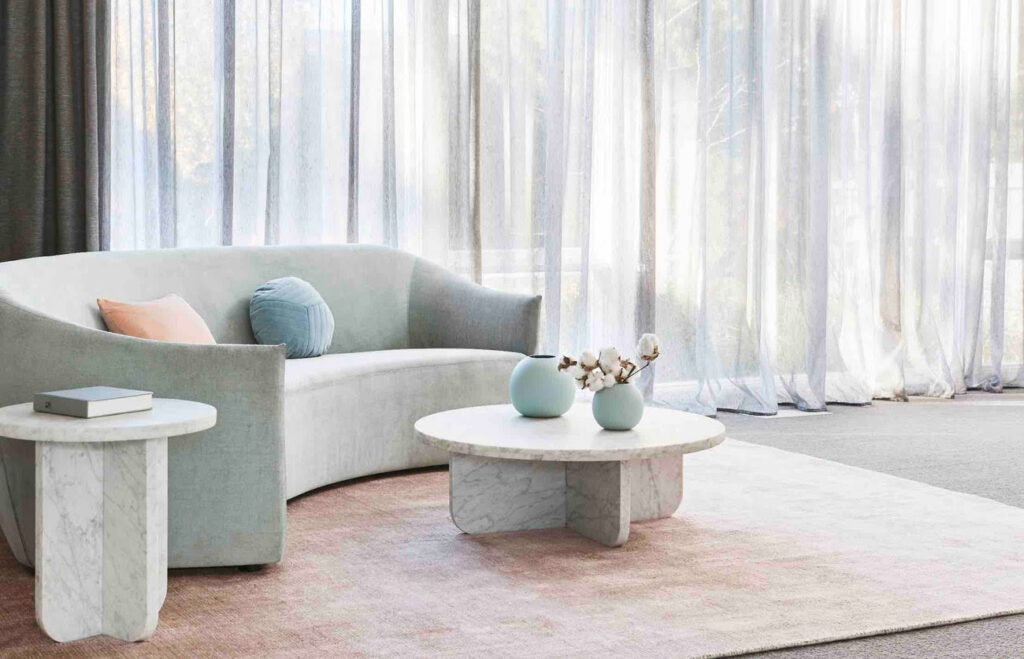
Planning an event, whether intimate or large-scale, requires careful attention to detail. From décor and lighting to food and entertainment, every aspect plays a role in creating the right atmosphere. Among these, event furniture is one of the most important elements that can make or break the overall experience for guests. The right chairs, tables, lounges, and décor items not only provide comfort but also set the tone and style of the occasion.
This is where complete furniture hire solutions for events big and small come in. By partnering with a professional event hire company like M Event Hire, you can access a wide variety of stylish, functional, and customizable furniture that perfectly matches your event’s theme and scale.
Why Furniture Hire is Essential for Events
No matter the type of gathering—be it a wedding, birthday celebration, gala dinner, or corporate function—the right furniture hire services can completely transform your venue. Here’s why:
- Enhances Guest Experience
Comfortable seating, elegant tables, and beautifully arranged lounges ensure your guests feel welcomed and valued. - Creates the Right Ambiance
Furniture contributes to the overall décor and vibe of the event. For instance, rustic wooden tables set a cozy tone, while sleek modern lounges create a chic, contemporary look. - Saves Time and Effort
Instead of worrying about sourcing, transporting, and setting up furniture, hiring experts means everything is delivered, installed, and packed away seamlessly. - Flexibility for All Event Sizes
Whether you’re hosting 20 people in a backyard or 500 guests at a grand venue, professional event hire companies can scale up or down depending on your needs.
Types of Event Furniture to Consider
Event hire services offer a wide range of furniture and accessories designed to suit all themes and occasions. Here are some popular options:
- Seating Solutions: Chiavari chairs, banquet chairs, bar stools, and lounge seating.
- Tables: Round banquet tables, cocktail tables, trestle tables, and coffee tables.
- Lounges & Sofas: Perfect for creating relaxed zones within your event.
- Outdoor Furniture: Benches, deck chairs, and marquees for outdoor gatherings.
- Décor Items: Lighting, table centerpieces, rugs, and decorative partitions.
By choosing complete furniture hire solutions for events big and small, you’ll have access to all of these elements in one place.
Benefits of Choosing M Event Hire
When planning an event in Australia, M Event Hire stands out as a trusted partner for providing top-quality furniture and event solutions. Here’s why:
- Wide Range of Options: From classic to modern designs, their extensive catalog caters to weddings, corporate events, festivals, and private parties.
- Affordable Packages: Hiring furniture is often more cost-effective than purchasing, especially for one-time events.
- Professional Setup: The team handles delivery, installation, and removal, saving you stress on the big day.
- Tailored Solutions: Whether it’s an intimate dinner or a large-scale event, they customize packages to suit your needs.
Event Trends: Furniture That Makes a Statement
Modern event styling is about more than just functionality; it’s about making a statement. Here are some trending furniture hire ideas:
- Mix-and-Match Seating: Combining different chair styles adds personality and flair.
- Rustic & Boho Chic: Timber tables paired with rattan lounges and earthy décor are trending for weddings and outdoor events.
- Luxury Lounges: Plush velvet lounges and ottomans create a VIP atmosphere at corporate and gala events.
- Sustainable Furniture: Eco-conscious choices like upcycled wood and reusable décor items are becoming increasingly popular.
With the right furniture hire solutions, you can bring any of these styles to life effortlessly.
Tips for Choosing the Right Furniture Hire Service
- Check the Inventory – Ensure the company has the specific furniture pieces you need.
- Read Reviews – Customer feedback can help you understand service quality.
- Consider Delivery & Setup – Always confirm logistics to avoid last-minute issues.
- Match Your Theme – Choose furniture that aligns with your event’s theme, colors, and style.
- Budget Wisely – Opt for complete hire packages that include setup, styling, and pickup for better value.
Final Thoughts
Event planning can feel overwhelming, but with the right support, it becomes a seamless and enjoyable process. Choosing complete furniture hire solutions for events big and small ensures that every detail of your celebration is covered—from stylish seating to decorative touches that impress your guests.
By partnering with experts like M Event Hire, you can focus on enjoying your special day while professionals handle the setup and styling. Whether it’s a wedding, corporate event, birthday, or festival, the right furniture hire company will help you transform your vision into reality
- GENERAL1 month ago
5 Factors That Affect Tattoo Removal Success
- ENTERTAINMENT2 months ago
Exploring the Kristen Archives: A Treasure Trove of Erotica and More
- LIFESTYLE6 months ago
The Disciplinary Wives Club: Spanking for Love, Not Punishment
- TECHNOLOGY6 months ago
Blog Arcy Art: Where Architecture Meets Art
- ENTERTAINMENT7 months ago
The Ultimate Guide to Shillong Teer Hit Number: How to Predict Your Next Win
- LIFESTYLE1 week ago
Who Is Sandra Orlow?
- LIFESTYLE3 months ago
Berniece Julien: The Private Life of Tyson Beckford’s Partner
- Uncategorized12 months ago
Conrad Fisher Transformation: From Top Student to Troubled Soul