GENERAL
How to Choose the Right Tank Cleaning Systems for Your Facility?
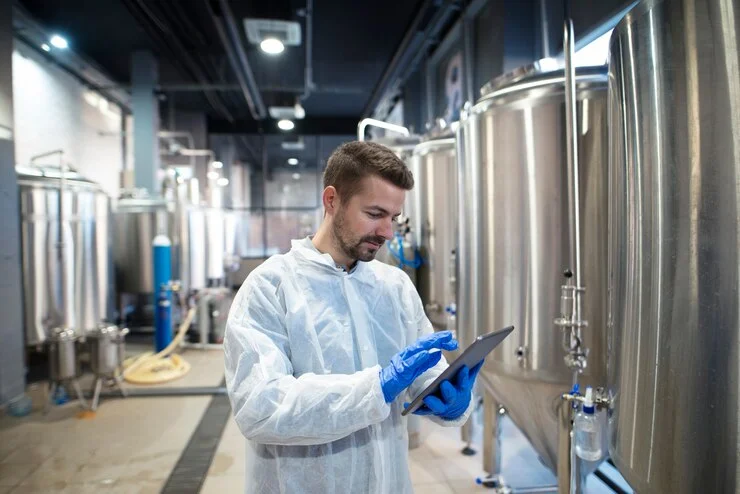
Selecting the right tank cleaning system is crucial for maintaining efficiency and productivity in any facility that uses storage or processing tanks. Tank cleaning equipment directly impacts the quality of your products, operational costs, and overall plant performance. Proper cleaning ensures sanitation standards are met while minimizing downtime and resource usage.
When evaluating tank cleaning requirements, consider factors such as tank size, shape, and material, as well as the types of products being processed. The cleaning method and equipment must be compatible with your specific needs to achieve optimal results. For instance, some applications may require high-pressure sprays, while others benefit from gentler cleaning techniques.
Advancements in technology have made a wide range of tank cleaning equipment online available, from simple manual devices to fully automated systems. Choosing the right solution involves balancing effectiveness, efficiency, and cost. It’s essential to assess your facility’s unique needs and consult with experts to find the most suitable tank cleaning systems for your operation.
Key Takeaways
- Tank cleaning systems significantly affect product quality and operational efficiency
- Evaluate specific tank characteristics and processing needs when selecting equipment
- Balance effectiveness, efficiency, and cost when choosing cleaning solutions
Evaluating Tank Cleaning Requirements
Effective tank cleaning relies on a thorough assessment of specific needs, chemical considerations, and quality standards. Proper evaluation ensures optimal cleaning results while maintaining safety and efficiency.
Assessing Tank Cleaning Needs
Tank size, shape, and material play crucial roles in determining cleaning requirements. Larger tanks may need more powerful cleaning systems, while oddly shaped vessels require specialized nozzles for complete coverage. Tank material influences the choice of cleaning agents and methods.
Residue type and volume impact cleaning intensity. Sticky or hardened deposits demand stronger cleaning solutions and longer cycle times. Frequency of cleaning cycles affects equipment selection, with more frequent cleaning potentially justifying investment in automated systems.
Production schedules must be considered. Fast turnaround times may necessitate quicker, more efficient cleaning processes. The type of product being stored or processed in the tank also influences cleaning protocols.
Understanding the Impact of Chemicals and Temperature
Chemical compatibility is essential for effective cleaning and tank integrity. Cleaning agents must remove residues without damaging tank surfaces or components. Some materials may react with certain chemicals, requiring careful selection.
Temperature affects cleaning efficiency and safety. Higher temperatures often improve cleaning power but may pose risks to workers and equipment. Cold cleaning can be less effective but safer for heat-sensitive materials.
Proper chemical concentrations are critical. Too weak, and cleaning is ineffective; too strong, and it may cause damage or waste resources. pH levels of cleaning solutions must be appropriate for the tank material and residue type.
Considering Product Quality and Safety
Regulatory compliance drives many cleaning requirements, especially in food, pharmaceutical, and chemical industries. Strict standards may dictate specific cleaning methods or validation processes.
Cross-contamination prevention is crucial. Thorough cleaning between product batches ensures quality and safety. Some industries require sterile conditions, necessitating more rigorous cleaning and sanitization procedures.
Worker safety is paramount. Proper ventilation, protective equipment, and safe chemical handling procedures must be implemented. Automated cleaning systems can reduce worker exposure to hazardous conditions.
Environmental impact should be considered. Choosing eco-friendly cleaning agents and minimizing water usage can improve sustainability. Proper disposal of cleaning waste is essential for regulatory compliance and environmental protection.
Selecting Tank Cleaning Equipment
Choosing the right tank cleaning equipment is crucial for efficient and effective cleaning processes. The proper selection impacts cleaning efficiency, water usage, and the ability to address challenging cleaning scenarios.
Analyzing Cleaning Efficiency and Water Usage
Tank cleaning machines come in various types, each with different efficiency levels and water consumption rates. Rotary jet heads offer high-impact cleaning with minimal water usage. They are ideal for removing stubborn residues and cleaning large tanks.
Static spray balls provide gentler cleaning and are suitable for lighter soiling. They use more water but are effective for rinsing and sanitizing tasks. Rotary spray heads offer a balance between impact and coverage, making them versatile for many applications.
When selecting equipment, consider the specific cleaning requirements of your tanks and the types of residues you typically encounter. Evaluate the water pressure and flow rates needed for optimal cleaning performance.
Advanced Equipment Options
Modern tank cleaning devices offer advanced features to enhance cleaning effectiveness. Programmable cleaning cycles allow for customized cleaning patterns and durations. This flexibility ensures thorough cleaning while minimizing water and energy consumption.
Some equipment incorporates self-cleaning mechanisms to prevent clogging and maintain consistent performance. These features are particularly valuable when dealing with challenging residues or in facilities with hard water.
For IBC totes and smaller tanks, specialized compact cleaners are available. These units provide targeted cleaning in confined spaces without the need for confined space entry, improving safety and efficiency.
Addressing Hard-To-Reach Areas and Stubborn Residue
Certain tank configurations present challenges for thorough cleaning. Tanks with complex internal structures or hard-to-reach areas require specialized equipment. Articulating spray heads can maneuver around obstacles and reach shadowed zones.
For stubborn residues, high-pressure jet heads deliver concentrated cleaning power. These devices can effectively remove hardened deposits or viscous materials that resist conventional cleaning methods.
Consider equipment with adjustable spray patterns to adapt to different tank geometries. This versatility ensures comprehensive coverage and reduces the need for multiple cleaning devices.
When dealing with particularly challenging cleaning scenarios, consult with equipment manufacturers. They can provide guidance on selecting the most appropriate tank cleaning nozzles and devices for your specific needs.
Conclusion
Selecting the right tank cleaning system is crucial for maintaining productivity and sanitation in processing facilities. Key factors to consider include tank size, cleaning requirements, and industry regulations. Proper equipment selection ensures efficient cleaning, reduces downtime, and promotes product quality and safety.
Facility managers should carefully evaluate their specific needs and consult with manufacturers or industry experts when choosing tank cleaning solutions. By investing time in this decision-making process, companies can optimize their cleaning operations and achieve long-term benefits in efficiency and compliance.
GENERAL
Kingkaex: A Deep Dive into Myth, Culture, and History
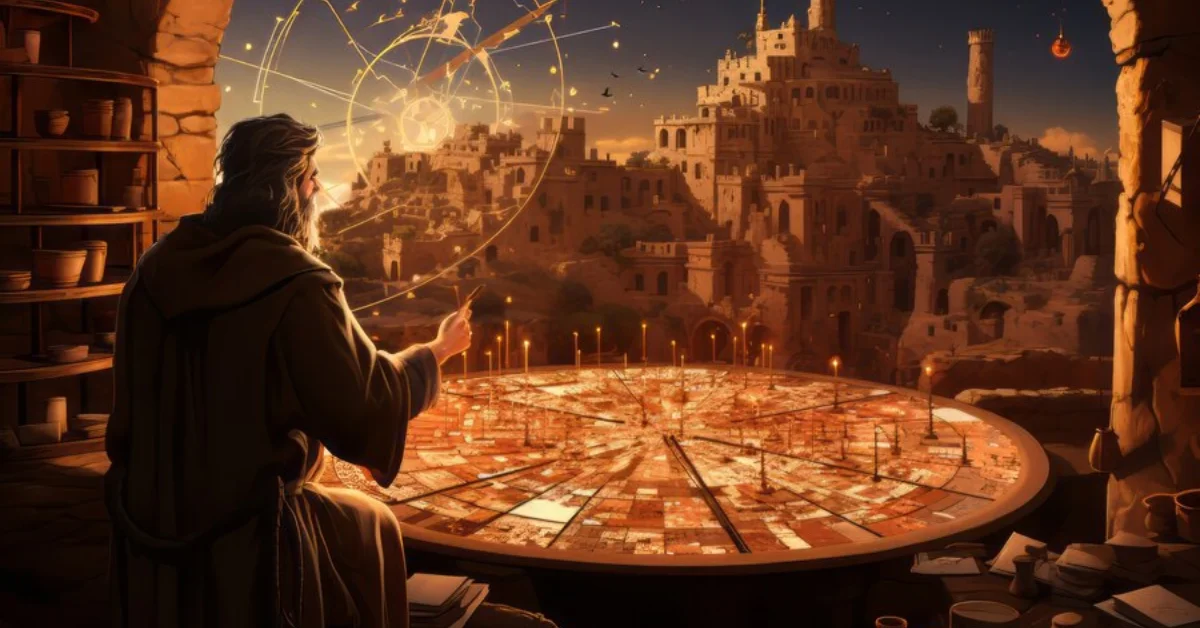
Welcome to the enchanting world of Kingkaex, where myth, culture, and history converge to create a game like no other. Delve into the origins of this intriguing pastime as we unravel its mystical beginnings and explore how it has evolved over time. Join us on a journey through the ages as we uncover why Kingkaex continues to captivate players around the globe today. Whether you’re a seasoned enthusiast or new to the game, prepare to be immersed in a realm where strategy meets tradition in an unforgettable gaming experience.
The Origins of Kingkaex in Myth and Legend
Legend has it that Kingkaex originated in the ancient kingdom of Draegonnia, where it was believed to be a gift from the gods themselves. The mythical creature known as the Kingkaex was said to possess extraordinary powers and wisdom, making it a symbol of strength and leadership.
Stories passed down through generations spoke of brave warriors who rode into battle atop their loyal Kingkaex companions, inspiring fear in their enemies and awe in their allies. It was said that those who mastered the art of taming a Kingkaex were destined for greatness and glory.
As time went on, these tales evolved into elaborate myths and folklore, weaving together themes of courage, loyalty, and destiny. The legend of the Kingkaex became intertwined with the cultural identity of Draegonnia, shaping its traditions and values for centuries to come.
The Influence of Culture on Kingkaex
Culture plays a significant role in shaping the game of Kingkaex, infusing it with unique customs and traditions that add depth and richness to the gameplay experience.
From the intricate designs on the playing pieces to the ceremonial rituals performed before a match, culture weaves its way through every aspect of Kingkaex, giving it a sense of history and authenticity.
Different regions have their own variations of Kingkaex, reflecting diverse cultural influences and beliefs. These variations showcase how adaptable and versatile the game is, able to evolve alongside changing cultural landscapes.
The values embedded in various cultures also influence how players approach strategy and competition in Kingkaex. Respect for tradition, teamwork, or individual prowess can all manifest differently depending on cultural norms.
Culture not only enhances the aesthetic appeal of Kingkaex but also adds layers of meaning and significance that make each game uniquely enriching.
Historical Significance of Kingkaex
Kingkaex holds a rich historical significance that dates back centuries, tracing its roots to ancient civilizations where it was played as a symbolic ritual. The game served as a reflection of societal values and beliefs, often embodying themes of strategy, bravery, and honor.
Historically, Kingkaex was not just a pastime but an integral part of cultural ceremonies and celebrations. It brought communities together, fostering camaraderie and unity among people from all walks of life. Its presence in various historical records showcases its enduring appeal across different regions and time periods.
Through the ages, Kingkaex evolved alongside changing societies, adapting rules and gameplay to reflect shifting cultural norms. Despite these transformations, the core essence of the game remained intact – promoting strategic thinking, teamwork, and sportsmanship.
As civilizations rose and fell throughout history, Kingkaex stood as a constant source of entertainment and connection for generations. Its longevity speaks volumes about its resilience in the face of ever-changing landscapes – both physical and metaphorical.
The legacy of Kingkaex continues to resonate today as players worldwide engage with this timeless game that transcends boundaries imposed by time or geography.
Contemporary Relevance and Popularity of Kingkaex
In today’s fast-paced world, Kingkaex continues to captivate players of all ages with its blend of strategy and excitement. Its timeless appeal lies in its ability to bring people together, fostering camaraderie and friendly competition.
With the rise of digital gaming, Kingkaex offers a refreshing alternative that promotes face-to-face interaction and social connection. It serves as a welcome break from screens and devices, allowing players to engage in real-time gameplay that stimulates both the mind and body.
The game’s adaptability makes it suitable for various settings – whether it’s a casual gathering at home or a competitive tournament on a larger scale. Its accessibility means that anyone can learn to play, adding to its widespread popularity across different communities.
As we navigate the complexities of modern life, Kingkaex stands out as a reminder of simpler times when fun was measured by shared experiences rather than virtual likes. Its enduring relevance speaks volumes about the human need for meaningful connections and memorable moments spent in good company.
How to Play Kingkaex: Rules and Gameplay?
Kingkaex is a captivating game that combines strategy and skill, making it an exciting pastime for players of all ages. To begin playing Kingkaex, you’ll need a game board with various pieces representing different characters from mythology. The objective is to outmaneuver your opponent by strategically moving your pieces across the board.
Each character in Kingkaex has unique abilities and strengths, adding depth to the gameplay. Players take turns moving their pieces and using special powers to gain an advantage over their adversary. The dynamic nature of the game keeps players on their toes, requiring quick thinking and tactical planning.
Victory in Kingkaex requires a combination of foresight, adaptability, and cunning. Whether you’re a seasoned player or new to the game, each match offers an opportunity for strategic growth and development.
So grab a friend or family member, set up your board, and immerse yourself in the world of Kingkaex for hours of fun-filled entertainment!
Benefits of Playing Kingkaex
Playing Kingkaex’s offers numerous benefits beyond just entertainment. It can improve cognitive skills such as strategic thinking and decision-making, as players must plan their moves carefully to outwit their opponents. Additionally, the game promotes social interaction and communication among participants, fostering teamwork and friendly competition.
Engaging in Kingkaex’s can also enhance problem-solving abilities by challenging players to adapt to changing circumstances on the board. This helps sharpen critical thinking skills and encourages creative solutions to overcome obstacles during gameplay. Moreover, the game provides a mental workout that stimulates brain activity while offering a fun way to relax and unwind.
Furthermore, playing Kingkaex’s can boost concentration and focus as players must stay alert throughout the game to anticipate their opponent’s moves. This heightened awareness not only improves attention span but also enhances memory retention over time. Diving into a game of Kingkaex offers a holistic experience that nurtures both mental acuity and social connections for an enriching pastime.
Controversies Surrounding Kingkaex
Controversies have long swirled around the beloved game of Kingkaex’s, sparking heated debates among fans and critics alike. One major point of contention revolves around the game’s violent origins in ancient myth and legend. Some argue that its aggressive nature perpetuates a culture of competition at all costs, while others see it as simply part of its historical roots.
Another hotly debated topic is the issue of cultural appropriation within Kingkaex’s. Critics claim that the game appropriates elements from diverse cultures without proper respect or understanding, while supporters maintain that it serves as a unifying force by showcasing different traditions in a fun and engaging way.
Furthermore, there are concerns about the potential for injuries during intense gameplay, raising questions about player safety and well-being. Despite these controversies, one thing remains clear: Kingkaex’s continues to capture the hearts and minds of players worldwide with its blend of strategy, skill, and excitement.
Conclusion: Why You Should Give Kingkaex a Try?
Kingkaex is not just a game; it’s a journey through myth, culture, and history. By exploring the origins of Kingkaex in ancient legend, understanding its cultural significance, and appreciating its historical impact, players can immerse themselves in a rich tapestry of storytelling that spans centuries.
The contemporary popularity of Kingkaex speaks to its enduring appeal and ability to captivate players young and old. With simple rules yet complex strategies, Kingkaex offers an engaging challenge for those looking to test their skills and strategic thinking.
Playing Kingkaex not only provides entertainment but also offers numerous benefits such as improving cognitive abilities, enhancing social interaction, and fostering creativity.
Despite some controversies surrounding the game, its overall positive impact on individuals and communities cannot be denied. So why wait? Step into the world of Kingkaex today and experience the magic for yourself. Give Kingkaex a try – you won’t be disappointed!
FAQs
Q: What is Kingkaex?
Ans: Kingkaex is a strategic board game that blends myth, culture, and history into an immersive gaming experience. Players maneuver character pieces across a board, utilizing unique abilities to outwit opponents.
Q: Where did Kingkaex’s originate?
Ans: Kingkaex’s originated in the ancient kingdom of Draegonnia, believed to be a divine gift symbolizing strength and leadership. It evolved from mythical legends into a cultural tradition celebrated for centuries.
Q: How does culture influence Kingkaex’s?
Ans: Culture enriches Kingkaex’s through diverse customs and traditions reflected in gameplay aesthetics and strategic approaches. Regional variations highlight its adaptability and historical context.
Q: What is the historical significance of Kingkaex’s?
Ans: Historically, Kingkaex’s served as both a ceremonial ritual and entertainment, promoting values like bravery and unity. It has endured through centuries, adapting to reflect societal changes while maintaining its core essence.
Q: Why should I play Kingkaex?
Ans: Playing Kingkaex promotes cognitive skills like strategic thinking and decision-making, enhances social interaction, and provides a mental workout. It offers a blend of fun, cultural exploration, and competitive challenge for players of all ages.
GENERAL
Өйёу: A Deep Dive into Cultural and Linguistic Significance
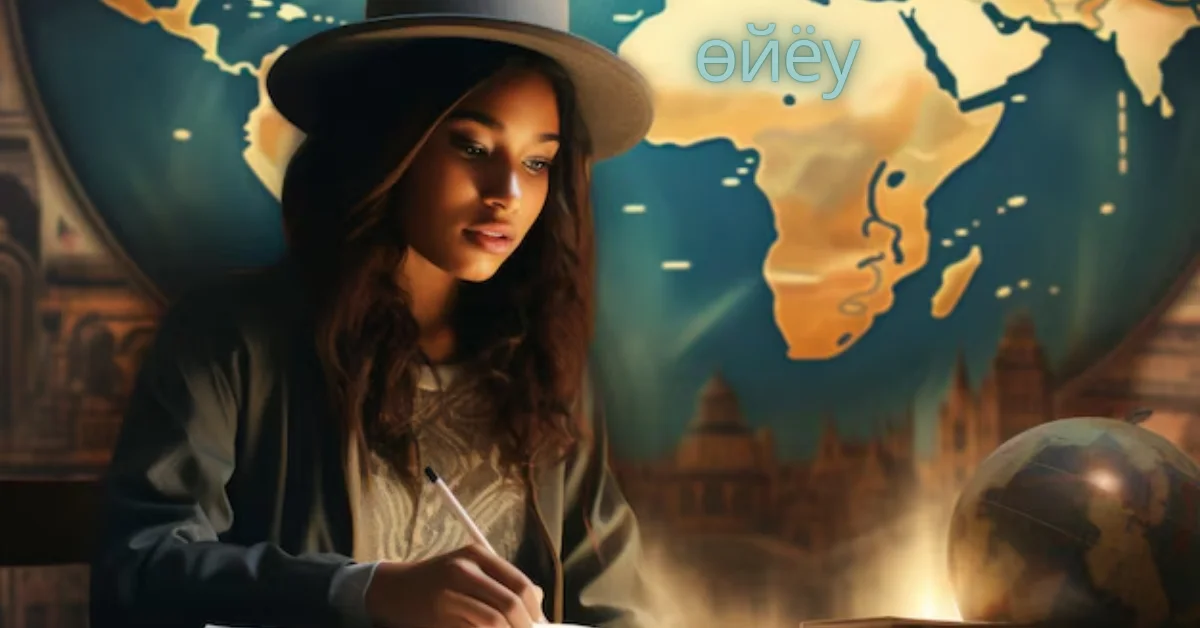
Introduction to the word Өйёу
The word “өйёу” carries a richness that extends far beyond its few syllables. Often overlooked, this term encapsulates layers of history, culture, and community significance. But what makes it so special? As we embark on a journey through the origins and meanings of “өйёу,” we’ll uncover fascinating insights into how this word resonates across different cultures and languages. From its roots to its modern-day applications, join us as we explore the many dimensions of “өйёу.” You might just find yourself seeing language—and culture—in a whole new light.
History of the word and its origins
The word “өйёу” has deep roots that trace back to ancient communities. Its origins can be found in the language of the Turkic peoples, where it first emerged as a term reflecting familial bonds and social closeness.
Through centuries, “өйёу” evolved alongside cultural practices. It began to embody not just a literal meaning but also emotional nuances related to home life and relationships.
Various dialects adapted the term, infusing it with regional flavors. This richness showcases how languages morph and develop over time due to migration and interaction between diverse groups.
Historical texts highlight its usage in literature and folklore, demonstrating its significance across generations. Each mention adds layers of meaning that resonate within many cultures today.
Cultural significance of Өйёу in various communities
The word Өйёу resonates deeply within various communities, serving as a bridge across cultures. It embodies warmth, hospitality, and connection. In many traditions, this term symbolizes an invitation to share not just food but stories and experiences.
For some groups, Өйёу represents the essence of family gatherings. It’s about creating memories around a table filled with laughter and love. The act of sharing a meal while using this term fosters closeness among participants.
In artistic expressions like music and dance, Өйёу is often celebrated. Festivals highlight its significance through performances that reflect communal values rooted in unity.
Different regions have nuanced interpretations of the word too. Each community adds layers to its meaning based on local customs and practices—showcasing how language evolves alongside culture itself.
Linguistic analysis and translations of Өйёу
The word Өйёу holds fascinating complexities in linguistic analysis. Its roots trace back to ancient languages, reflecting a blend of cultural influences over time.
In terms of translation, Өйёу can mean different things based on context. It may signify a specific object or even an abstract concept in various dialects. This flexibility showcases the richness of its usage.
Phonetics also play a crucial role. The pronunciation varies across regions, impacting how it is understood and integrated into everyday speech.
Translating Өйёу requires sensitivity to these nuances. Language isn’t static; it evolves with society’s needs and values. Understanding this helps grasp its true essence within communication.
As globalization continues, the exploration of words like Өйёу sheds light on our collective identity while celebrating diversity among cultures and languages alike.
Use of Өйёу in modern society
The term “өйёу” has found its place in modern society, bridging traditional values with contemporary life. In various communities, it serves as a reminder of cultural heritage while adapting to new contexts.
Social media platforms are buzzing with the use of “өйёу,” where younger generations express their identity and connection to their roots. Hashtags featuring this word often accompany posts celebrating cultural events or personal milestones.
In education, “өйёу” is gaining traction within curricula focused on indigenous languages and cultures. Schools aim to foster an appreciation for linguistic diversity through workshops and community projects centered around this powerful term.
Moreover, artists incorporate “өйёу” into music, literature, and visual arts. This creative expression not only keeps the word alive but also invites dialogue about its significance in today’s world. The versatility of “өйёу” ensures it remains relevant as society evolves.
Impact on language and culture
The word өйёу resonates deeply within various languages and cultures. It embodies not just a term, but a rich tapestry of meanings that evolve with time and context.
Its impact extends beyond mere vocabulary. In communities where the term is prevalent, it fosters connections among individuals. The shared understanding enriches cultural identity and promotes unity.
Moreover, as globalization spreads, the essence of өйёу challenges linguists to adapt its meaning across borders. Different interpretations arise in diverse settings, showcasing its flexibility.
This adaptation leads to hybrid expressions that blend traditional roots with modern influences. Such transformations reflect the dynamic nature of language itself.
In art and literature, references to өйёу paint vivid imagery that captures collective experiences. These narratives help preserve heritage while inviting new generations to explore their linguistic roots.
Future of Өйёу in a globalized world
As the world becomes increasingly interconnected, the future of өйёу faces both challenges and opportunities. Globalization opens doors for cultural exchange but can also dilute local languages and traditions.
In urban centers, where diverse communities converge, the use of өйёу may flourish through social interactions. Younger generations might adopt it alongside other languages, creating a hybrid linguistic landscape that reflects their multicultural identities.
Digital platforms will play a crucial role in this evolution. Online spaces allow speakers to share their culture and heritage with a global audience. Podcasts, blogs, and social media continue to promote awareness about the significance of words like өйёу.
However, there is also concern over potential erosion due to dominant global languages. It raises questions about preservation efforts within communities committed to keeping their language alive amidst change. How they navigate this delicate balance will shape the trajectory of өйёу moving forward.
Conclusion
The word өйёу weaves a rich tapestry of history and meaning across cultures and languages. Its origins reflect a deep connection to community, tradition, and shared experiences. This significance can be seen in various practices and rituals that celebrate the essence of the term.
As societies evolve, so does the usage of сөздәрі like өйёу. In modern contexts, it finds new expressions through art, literature, and social interactions. It resonates with younger generations who are keen on preserving their linguistic heritage while adapting to contemporary influences.
Looking ahead, the future of өйёу in an increasingly globalized world is promising yet uncertain. The challenge lies in balancing modernization with cultural preservation. As communities continue to embrace their unique identities amid globalization pressures, words like өйёу’s serve as anchors to remind us of our roots.
Understanding this word’s impact enhances our appreciation for language diversity. It invites ongoing exploration into how such terms shape identity and foster connections among people worldwide. Embracing these elements will ensure that even as times change, essential aspects of culture endure through expressions like Өйёу.
FAQs
What is “Өйёу”?
“Өйёу” is a culturally significant term with deep roots in various communities, representing concepts like home, family, and connection.
Where did the word “Өйёу’s” originate?
The word “Өйёу’s” originates from ancient Turkic languages, where it was used to express familial bonds and social closeness.
How is “Өйёу’s” used in modern society?
In modern society, “Өйёу’s” is celebrated in social media, education, and the arts, symbolizing cultural heritage and identity.
What is the cultural significance of “Өйёу’s”?
“Өйёу’s” carries deep cultural significance, representing warmth, hospitality, and community, often used in family gatherings and traditional practices.
How does “Өйёу’s” impact language and culture?
“Өйёу’s” influences language and culture by fostering connections, preserving heritage, and adapting to global influences while maintaining its traditional essence.
GENERAL
Understanding Iversær: A Comprehensive Guide
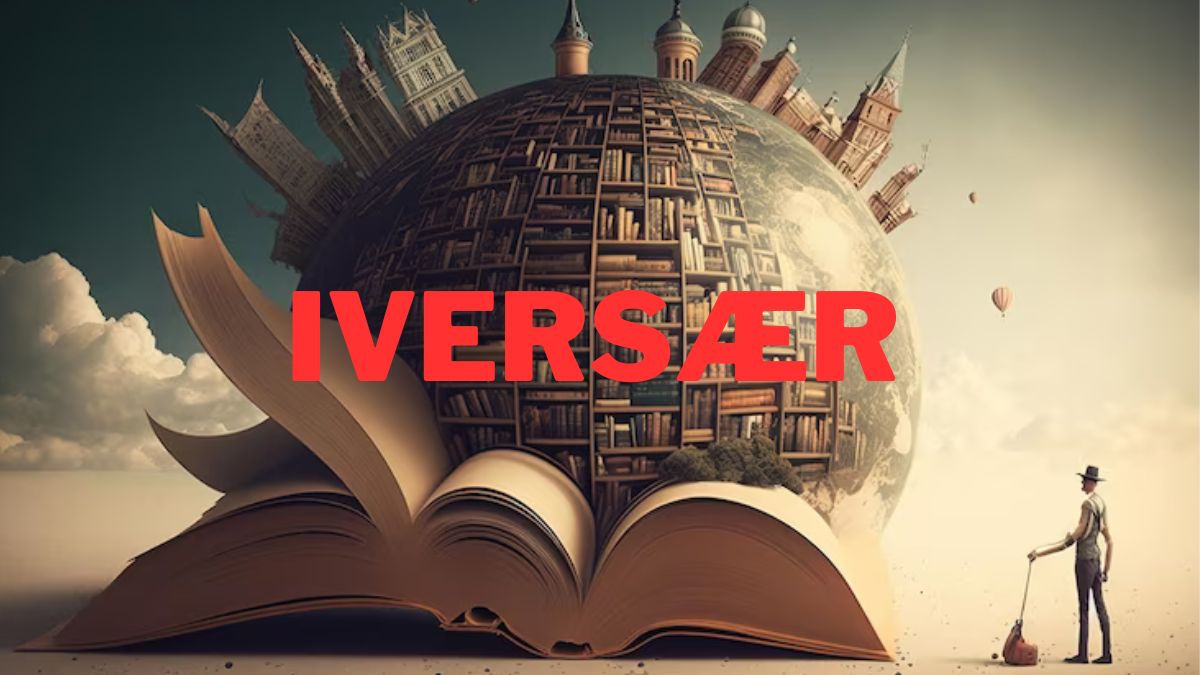
Introduction to Iversær
Imagine a concept that intertwines ancient wisdom with modern living, creating a bridge between tradition and contemporary life. This is Iversær—a term that might be new to many but holds profound significance for those who embrace its principles. Whether you’re seeking balance in your daily routine or looking to deepen your understanding of cultural practices, Iversær offers a unique lens through which to view the world around you. Join us as we delve into the essence of Iversær, exploring its history, core principles, applications in everyday life, and much more. It’s time to uncover what makes this fascinating concept resonate across cultures and generations.
What is Iversær?
Iversær is a concept that intertwines philosophy, self-awareness, and personal growth. Rooted in ancient wisdom, it invites individuals to explore their inner selves with curiosity and compassion.
At its core, Iversær emphasizes the importance of understanding one’s thoughts and emotions. It encourages introspection as a means to foster deeper connections with others and the world around us.
This practice isn’t merely theoretical; it involves active engagement with daily experiences. Through mindfulness techniques or reflective journaling, practitioners can uncover insights about their motivations and desires.
The beauty of Iversær lies in its adaptability. Each person can interpret it uniquely based on their life circumstances. This flexibility makes it accessible for anyone seeking clarity amidst life’s complexities.
The History and Origin of Iversær
The history of Iversær is rich and complex, weaving through various cultures over centuries. It is believed to have originated in ancient times, where it was first practiced for its spiritual benefits.
Ancient texts suggest that early practitioners used Iversær as a tool for personal growth and community bonding. As societies evolved, so did the methods associated with it.
Iversær gained popularity during the Middle Ages when scholars began documenting its principles in manuscripts. This sparked interest among thinkers who sought deeper meaning in their lives.
With globalization, the practice spread beyond borders. Different regions adapted Iversær to fit local customs and beliefs, enriching its significance further.
Today, Iversær reflects a blend of tradition and modern interpretation. Its journey continues to inspire individuals seeking enlightenment across diverse backgrounds.
The Basic Principles of Iversær
Iversær is built on a foundation of simplicity and balance. Its core principles emphasize harmony between the self and the environment. This approach encourages individuals to reflect on their thoughts, emotions, and actions.
Another key principle is adaptability. Iversær teaches that flexibility in thought can lead to greater resilience in life’s challenges. It fosters an understanding that change is a part of existence.
Moreover, mindfulness plays a crucial role within Iversær. Practicing awareness allows individuals to connect deeply with their surroundings. This connection helps cultivate gratitude for life’s experiences.
Collaboration forms another essential aspect of Iversær principles. Working together enhances creativity and problem-solving skills among groups or communities.
Appreciation for diversity enriches the practice of Iversær. Recognizing different perspectives leads to deeper insights, fostering empathy and collective growth.
Applying Iversær in Daily Life
Applying Iversær in daily life can transform ordinary routines into mindful experiences. Begin with small changes, like incorporating intentional breathing during your morning coffee. This simple act can enhance awareness and presence.
Consider utilizing Iversær principles during meal times. Focus on the colors, textures, and flavors of your food. Savor each bite instead of rushing through meals. It cultivates gratitude and appreciation for nourishment.
Incorporate reflection moments throughout your day. Whether it’s a short walk or quiet time in nature, pause to process your thoughts and feelings without distractions.
Engaging with others using Iversær encourages deeper connections. Listen actively rather than passively responding in conversations. This fosters empathy and understanding within relationships.
Embrace creativity as part of the Iversær approach by exploring new hobbies or interests regularly. Allowing yourself the space to experiment nurtures growth and self-discovery in everyday life.
Benefits of Using Iversær
Using Iversær brings a multitude of benefits that can enhance both personal and communal well-being. One significant advantage is the way it promotes mindfulness. By encouraging individuals to focus on their thoughts and feelings, Iversær helps create a deeper connection with oneself.
Another benefit lies in its ability to foster community bonds. When practiced collectively, participants share experiences that promote empathy and understanding among diverse groups. This sense of unity can lead to stronger relationships within communities.
Additionally, integrating Iversær into daily routines may improve stress management. It provides tools for navigating life’s challenges by offering clarity and perspective during tough times.
Moreover, users often report heightened creativity as they embrace new ways of thinking through this practice. The freedom to explore different perspectives ignites innovative ideas and problem-solving skills essential for personal growth.
Criticisms and Controversies Surrounding Iversær
Iversær has attracted its fair share of criticisms and controversies. Detractors often question its scientific validity. They argue that the principles lack empirical support, rendering them ineffective for many practitioners.
Moreover, some cultural purists feel Iversær dilutes traditional practices. They believe that blending it with modern approaches risks losing authentic roots. This tension between innovation and tradition fuels ongoing debates.
Additionally, certain applications of Iversær’s have sparked ethical concerns. Critics point out instances where individuals exploit the concept for personal gain rather than communal benefit. Such actions can lead to misunderstandings and disillusionment among followers.
The varying interpretations across different communities further complicate discussions around Iversær’s. What one group views as beneficial might be seen as problematic by another. These divergent perspectives continue to shape the narrative surrounding this intriguing practice.
Incorporating Iversær into Different Cultures and Societies
Iversær’s offers a fascinating lens to explore cultural diversity. Different societies can adapt its principles in unique ways, enriching their traditions.
In Eastern cultures, Iversær’s may blend with existing philosophies like Taoism or Buddhism. This creates a holistic approach emphasizing balance and harmony in daily life.
Western societies might embrace Iversær’s as an innovative tool for wellness. It could be integrated into corporate settings, fostering mindfulness among employees for enhanced productivity.
Indigenous tribes often focus on communal aspects of Iversær’s, using it to strengthen community bonds. The practice can serve as a means of storytelling and preserving heritage through shared experiences.
By merging with local customs, Iversær’s evolves while maintaining its core values. Each culture adds layers of depth, making the concept more inclusive and resonant across global communities.
Future of Iversær
The future of Iversær’s is brimming with potential. As awareness grows, more individuals are exploring its applications in various fields.
Emerging technologies may enhance how we practice and understand Iversær’s. Virtual reality and artificial intelligence could offer immersive experiences that deepen engagement.
Educational institutions might begin incorporating Iversær’s into their curriculums. This shift could foster a new generation adept at applying these principles to solve real-world problems.
Cultural exchanges will likely play a vital role as well. Diverse interpretations from different societies can enrich the core tenets of Iversær’s, making it more applicable across borders.
Social media platforms might become hubs for communities sharing insights and practices related to Iversær’s. This connectivity can spark collaborations that push the boundaries of traditional understanding.
As society evolves, so too will the ways we interpret and implement Iversær’s in everyday life, ensuring its relevance for years to come.
Conclusion
Understanding Iversær opens up a fascinating realm of knowledge that can enrich our daily lives. From its intriguing history and principles to the myriad benefits it offers, there’s much to explore. While criticisms exist, they often serve as catalysts for deeper discussions and improvements in practice.
As societies continue to evolve, so too does the application of Iversær’s across different cultures. The future holds promise for this concept as it integrates with modern lifestyles, adapting while maintaining its core values. Embracing Iversær might just lead us towards greater understanding and harmony within ourselves and among others.
The journey into Iversær’s is one worth taking—a path filled with insights that resonate on multiple levels. Whether you are new to the idea or looking to deepen your existing knowledge, the exploration of Iversær invites curiosity and engagement at every turn.
ALSO READ: Мультипарад Unites Cultures Through Art, Music, and Tradition
FAQs
What is “Iversær”?
Iversær is a holistic concept rooted in ancient wisdom that promotes self-awareness, emotional insight, and balanced living. It encourages reflection and mindfulness in daily life.
Where did the concept of Iversær’s originate?
Iversær’s is believed to have ancient roots, evolving through various cultural practices. Its principles were refined over centuries and adapted globally for personal and communal well-being.
How can I apply Iversær’s in my daily routine?
You can practice Iversær’s by embracing mindfulness, engaging in reflective journaling, and being present in everyday tasks like eating or walking. Start small and stay consistent.
Is Iversær’s tied to any specific religion or culture?
No, Iversær’s is a universal philosophy. While it draws on spiritual traditions, it remains adaptable across cultures and belief systems, allowing for personal interpretation.
What are the main benefits of practicing Iversær?
Practicing Iversær can improve mental clarity, emotional balance, creativity, and interpersonal relationships by fostering empathy, presence, and intentional living.
- GENERAL1 month ago
5 Factors That Affect Tattoo Removal Success
- ENTERTAINMENT2 months ago
Exploring the Kristen Archives: A Treasure Trove of Erotica and More
- LIFESTYLE6 months ago
The Disciplinary Wives Club: Spanking for Love, Not Punishment
- TECHNOLOGY5 months ago
Blog Arcy Art: Where Architecture Meets Art
- LIFESTYLE2 days ago
Who Is Sandra Orlow?
- ENTERTAINMENT7 months ago
The Ultimate Guide to Shillong Teer Hit Number: How to Predict Your Next Win
- LIFESTYLE3 months ago
Berniece Julien: The Private Life of Tyson Beckford’s Partner
- GENERAL8 months ago
Worldwide Elephant List: Complete Reserves and Map 2024