BUSINESS
How to Fix a Failed ERP Implementation for Your Manufacturing Organization?
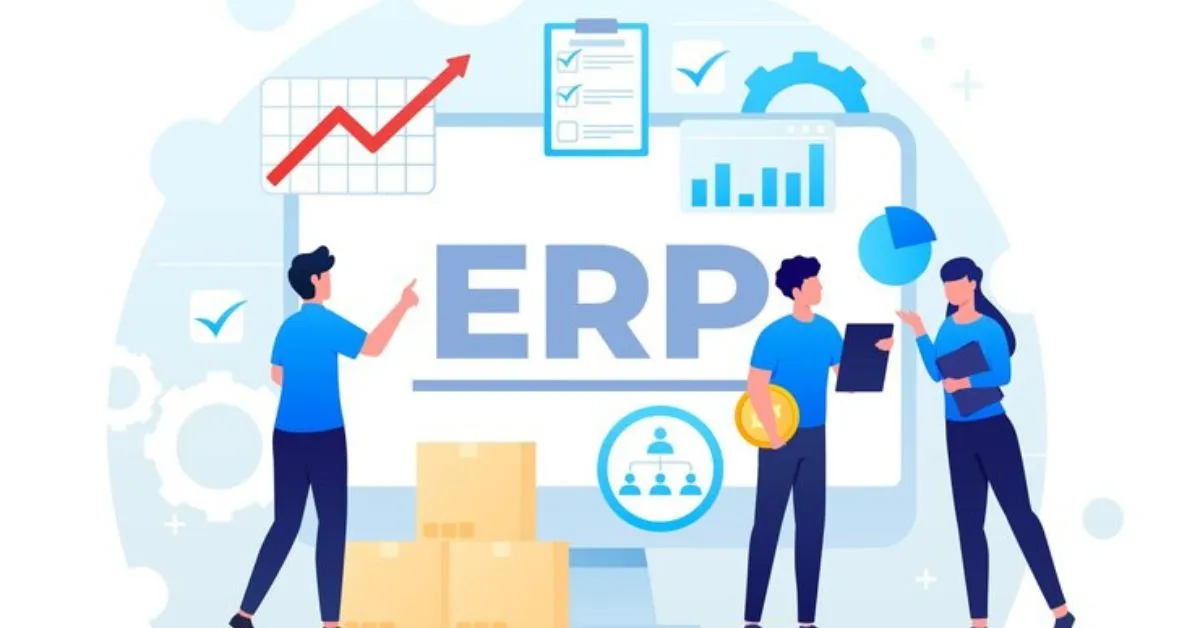
ERP implementation failure in any company, including manufacturing organization, is the worst-case scenario. The implementation team will deploy the best strategies to avoid ERP implementation failure.
However, even after giving the best efforts, the implementation team sometimes fails to deploy the ERP system effectively. Often, troubled implementations are behind schedule, cost more than the pre-determined budget, or fail to deliver expected business benefits. The aftermath of such project failure can disrupt operations in the manufacturing unit and demoralize employees at every level.
You can restore your manufacturing business confidence and re-align the production projects with business priorities by deploying a successful Manufacturing ERP Software recovery plan. This article discusses the causes of ERP implementation failure and how to fix it.
Causes of ERP Implementation Failure
Lack of clear goals and objectives
Without determining what you want your manufacturing business to achieve with an ERP system, you will find it difficult to properly plan, implement, and measure the system’s success.
Insufficient training and support
Employees should be properly trained and supported to implement and use the new ERP system effectively. Without adequate training and support, employees might struggle to implement and use the platform, leading to adoption issues and poor productivity.
Inadequate data migration
Migrating business data from traditional database systems to the new ERP platform can be complex and time-consuming. If the data migration process is not carried out properly, it can result in data loss, errors, and inaccuracies.
Customization issues
Many ERP systems designed for the manufacturing industry are highly configurable, but not appropriately customized can lead to compatibility issues and system errors.
Inadequate testing
Testing is vital to successfully implement ERP software, as it helps identify and resolve potential issues before the system goes live. Without deploying adequate testing techniques, you can’t discover potential issues until after the ERP system is in production, leading to downtime and other problems.
How Can You Fix a Failed ERP Implementation?
Following these steps can help you fix a failed ERP implementation in your manufacturing organization:
Identify the root cause of the failure
You should thoroughly analyze the ERP implementation process to determine what went wrong. It might include reviewing project documentation, interviewing stakeholders, and analyzing system logs.
Create a plan to address identified issues
Once you have identified the root cause of the ERP implementation failure, create a plan to address the identified issues. It might include revising the project scope, adding additional resources to the implementation project, or revisiting the implementation timeline.
Communicate with stakeholders
You should inform the stakeholders involved in the ERP implementation project about the progress of the recovery effort and keep them engaged in the recovery process as much as possible.
Identify and mitigate risk
Identifying the risks associated with the recovery effort beforehand is recommended. In addition, try to mitigate them as early as possible. It might include the risks related to data integrity, compliance, or system availability.
Continuously monitor the recovery progress
Your job doesn’t end with deploying the recovery plan and strategies. Instead, you should continuously monitor the progress of your recovery effort and make adjustments as and when needed to fix ERP implementation failure successfully.
Consider professional help
Your in-house employees might not be capable enough to fix the ERP implementation failure. In such a case, consider hiring professional consultants specialized in implementing the erp for manufacturing companies and helping you with your recovery efforts.
Post-implementation review
After successfully implementing the ERP system, you should conduct a thorough review to identify the lessons that you can apply in future ERP implementation projects.
Concluding Thoughts
Implementing an ERP system is crucial to automate, streamline, and optimize all manufacturing company operations, functions, and activities. With a technologically advanced ERP system, you can do everything from purchase and procurement to inventory and human resource management within less time, effort, and cost.
However, some manufacturing units fail to implement ERP systems successfully, impacting business productivity. It can be a long and arduous road to recover from a failed ERP system implementation, but getting your manufacturing company back on track is crucial. Following the above-discussed tips can help you recover from the ERP implementation failure. Don’t hesitate to make internal business process changes to deploy the ERP system and leverage its functionality efficiently.
Eresource infotech Pvt ltd is leading ERP Software Company In India. We provides ERP Software for manufacturing, construction, process manufacturing, transportation, trading and distribution industries.
BUSINESS
ADA to USD Historical Price Trends
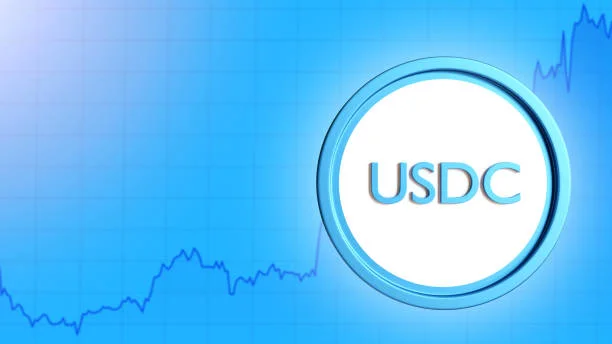
Cardano’s ADA token has captured investor attention since its launch, moving from a niche academic blockchain project to one of the top cryptocurrencies by market capitalization. Understanding its historical price performance against the US dollar or USD Historical reveals more than just numbers—it offers a window into how market cycles, sentiment, and technological progress shape value in the crypto economy.
This deep dive goes beyond a simple timeline of prices. We’ll explore key milestones, market psychology, and macro factors that have influenced ADA’s USD performance over time, drawing lessons that could help shape future investment strategies.
The conversation doesn’t end here—discover more insights.
The Launch Era – 2017’s Low Entry Point
Cardano entered the market in September 2017 after an initial coin offering (ICO) that raised over $60 million. At launch, ADA traded at roughly $0.02–$0.03 USD or USD Historical.
Why This Matters:
- Investor Accessibility – The sub-$0.05 range made ADA accessible to a broad audience, attracting early adopters willing to bet on an ambitious smart contract platform.
- Initial Volatility – Prices saw quick fluctuations even in the first weeks. Early volatility reflected uncertainty about Cardano’s roadmap, as its proof-of-stake mechanism was still unproven.
Unique Insight:
The early ADA market was less about technical indicators and more about ideological positioning. Investors were drawn by the promise of peer-reviewed blockchain development, but the lack of a functioning mainnet with smart contracts meant valuation was largely speculative.
First Crypto Bull Run – Late 2017 to Early 2018
By December 2017, during the first major cryptocurrency bull run, ADA surged above $1 USD. This was a massive gain for those who entered in the early months.
Contributing Factors:
- Bitcoin’s rapid climb toward $20,000 in December 2017 triggered a spillover into altcoins.
- ADA benefited from being seen as a “next generation” blockchain competitor to Ethereum.
Unique Insight:
ADA’s first big rally shows how network effect speculation works in crypto: even without a complete product, strong branding and perceived innovation can drive exponential growth—though such growth can be fragile without matching fundamentals.
The 2018–2019 Bear Market
After hitting its first major peak, ADA entered a prolonged downturn, falling below $0.05 USD by the end of 2018.
Key Lessons from This Period:
- Correlation with Market Leaders – ADA’s decline mirrored Bitcoin’s, showing its dependence on broader crypto sentiment.
- Long Development Cycles – Cardano’s deliberate development pace frustrated traders expecting rapid deliverables.
Unique Insight:
For patient investors, the 2018–2019 period demonstrated that bear markets are accumulation phases. Those who continued dollar-cost averaging (DCA) during this period set themselves up for significant returns in the next cycle.
2020–2021 – The Smart Contract Hype and All-Time High
ADA’s next major rally began in mid-2020, accelerating in 2021. The price climbed from under $0.10 in early 2020 to an all-time high of around $3.09 in September 2021.
Drivers of Growth:
- The “Alonzo” upgrade announcement brought smart contract capabilities to the network.
- Increased staking participation—Cardano’s proof-of-stake system encouraged holders to lock up ADA, reducing sell pressure.
- A general bull market driven by institutional interest in crypto.
Unique Insight:
This run was not purely speculative—it was technology milestone-driven speculation. The market priced in expectations of a vibrant DeFi ecosystem on Cardano, but the slower-than-expected rollout of dApps post-Alonzo showed the risk of buying the rumor, facing the reality.
2022–2023 – The Consolidation and Macro Headwinds
Following its ATH, ADA saw a steep correction in 2022, falling back toward $0.25–$0.40 USD. This was influenced by:
- Global inflation concerns leading to tighter monetary policy.
- Risk asset selloffs across tech and crypto sectors.
- Underwhelming immediate adoption of Cardano-based dApps.
Unique Insight:
This phase reinforced the idea that crypto assets behave like high-beta tech stocks during macroeconomic stress. Even fundamentally sound projects suffer when liquidity dries up.
2024–2025 – Recovery Signs and a New Market Phase
By mid-2024, ada price usd began to show signs of recovery, trading between $0.60–$0.80 USD. Increased developer activity, new DeFi protocols on Cardano, and improved interoperability with other blockchains helped renew interest.
Unique Insight:
Unlike earlier cycles where hype vastly outpaced delivery, this recovery has been fundamentals-first. The market is rewarding tangible progress—such as increased total value locked (TVL) in Cardano’s DeFi space—rather than just promises.
Observing ADA Price Trends – Patterns Across Cycles
When we examine ADA’s full trading history, several consistent themes emerge:
- Narrative-Driven Peaks – Price surges often coincide with key announcements, upgrades, or industry-wide bullish narratives.
- Heavy Correlation with Bitcoin – While Cardano has its unique story, macro movements in BTC dictate broader liquidity flows.
- Long Accumulation Periods – ADA tends to spend extended time consolidating before breakouts, rewarding patient holders.
- Overestimation of Speed – Market participants frequently overestimate how quickly upgrades will translate into adoption.
The Psychology Behind ADA’s USD Price Movements
Price history alone doesn’t tell the full story—investor psychology plays a huge role.
- FOMO Phases – Retail traders rush in during rapid climbs, often at cycle peaks.
- Fear-Driven Capitulation – Bear market bottoms are marked by extremely negative sentiment and low trading volume.
- Builder Resilience – Even during price downturns, Cardano’s core development activity remains high, which helps support long-term confidence.
Unique Insight:
Historical ADA/USD charts often act as a mirror for sentiment cycles—when optimism is at its highest, risk is greatest; when despair dominates, opportunity is often near.
Using Historical Trends for Future Positioning
Studying ADA’s historical price trends offers several strategic takeaways for traders and investors:
- Avoid Chasing Parabolic Moves – Waiting for retracements can improve entry points.
- Diversify Entry Timing – Dollar-cost averaging during sideways markets can mitigate risk.
- Track Ecosystem Growth – Tangible network usage data is a better long-term indicator than speculative hype.
Conclusion – What ADA’s History Tells Us
ADA’s USD price history is a story of ambition, market psychology, and cyclical growth. From its sub-$0.05 launch days to a $3+ all-time high and back into consolidation, the token’s journey underscores the importance of patience, fundamentals, and realistic expectations.
For those willing to look beyond short-term volatility, ADA’s track record offers a valuable blueprint: major gains have historically come to those who accumulate during periods of apathy and hold through technical milestones.
FAQs
1. What was ADA’s lowest historical price in USD?
ADA’s all-time low was around $0.0195 USD in October 2017, shortly after its initial launch.
2. When did ADA reach its highest historical price in USD?
ADA reached its all-time high of approximately $3.09 USD in September 2021 during the crypto market’s peak and the anticipation of the Alonzo smart contract upgrade.
3. How does ADA’s price history compare to other top cryptocurrencies?
Similar to many altcoins, ADA’s price movements closely follow Bitcoin’s overall trend, but it has shown stronger narrative-driven spikes than some competitors due to its academic development approach and milestone-based roadmap.
Curious hearts and bright minds—follow the path to more wisdom on Crispme.
BUSINESS
What Makes a Great Alternative Data Platform for Modern Lenders?
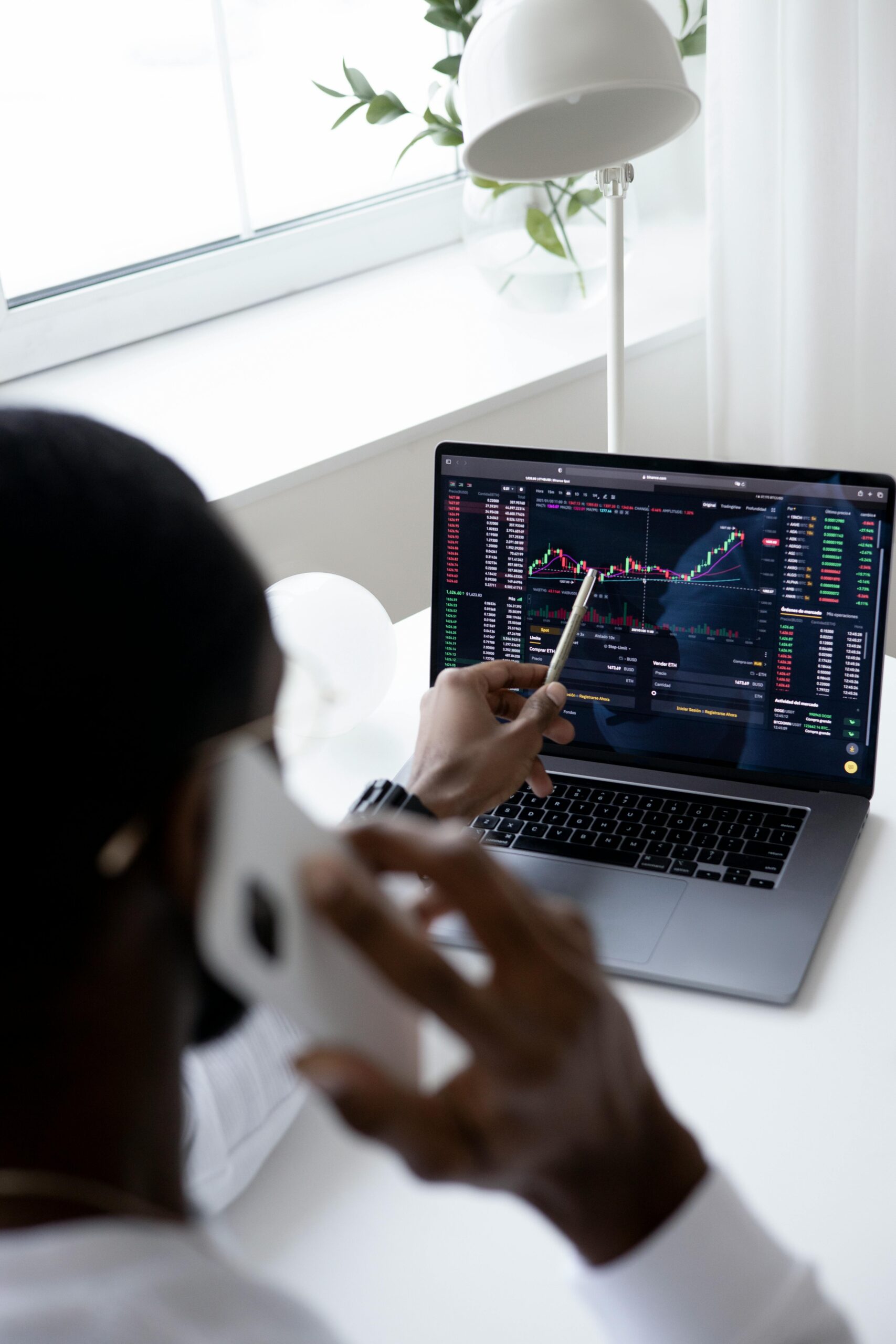
Modern lending has outgrown traditional credit scores. Millions of reliable borrowers are still underserved because their financial histories don’t tell the full story.
That’s why many lenders are turning to platforms unlocking non-traditional signals like digital footprints, behavioral patterns, and device insights. But not every alternative data platform offers the same value.
In this article, we’ll break down what features matter when choosing an alternative data provider.
Why Traditional Credit Data Isn’t Enough Anymore
Traditional credit scoring often fails to capture the full picture of someone’s financial reliability. It relies on past borrowing behavior, like loans, credit cards, and repayment history, which not everyone has.
This means millions of people with little or no credit history get overlooked. Commonly affected groups include:
- Gig economy workers like delivery drivers, ride-share operators, and freelancers.
- Young adults and students who haven’t had time to build credit.
- Self-employed professionals and small business owners with irregular income.
- Migrants and expats who don’t have local credit histories.
- Unbanked or underbanked individuals in emerging markets.
- Stay-at-home caregivers who manage finances informally but aren’t on formal accounts.
Many of these individuals are responsible with money. But legacy systems can’t see it.
Relying only on traditional bureau data means missing out on trustworthy borrowers. To close that gap, lenders need broader context and smarter signals.
That’s where an alternative data platform makes all the difference.
What Is an Alternative Data Platform?
An alternative data platform collects, analyzes, and scores non-traditional data points. These include email and phone metadata, device type, location history, online behavior, and social signals.
Instead of relying on past financial records, these platforms assess digital presence. They work in real time, integrating directly with loan origination systems via API.
This data helps fill the gaps when credit history is thin, giving lenders new ways to evaluate risk.
Core Capabilities Every Modern Lender Should Look For
1. Real-Time Data Collection and Scoring
Speed matters – especially in digital lending. The platform should collect and return insights instantly.
Look for systems that support seamless API integration to avoid delays in decision-making.
2. Coverage Across Global and Local Data Sources
A good platform pulls from both global and region-specific services. For example, DiDi usage in Mexico or WhatsApp activity in LATAM.
Local signals matter when assessing regional borrowers and understanding their habits.
3. Transparent and Explainable Models
Lenders need to understand how scores are calculated. Explainable AI ensures compliance and helps teams justify decisions to regulators.
With new rules like the EU AI Act and ECOA, this isn’t optional anymore.
4. Data Privacy and Security Compliance
Handling sensitive data means following strict rules. A trustworthy platform should comply with ISO 27001, GDPR, and similar standards.
Look for audit readiness and secure data flows.
5. Built-In AI Functionality
Modern platforms should include machine learning capabilities that improve over time.
AI can enhance fraud detection, automate risk assessments, and uncover patterns that traditional models might miss.
6. Expert Technical Support
A great platform doesn’t just offer data, it comes with people who know how to use it.
Look for providers that offer:
- Dedicated integration support
- Help with interpreting data
- Training for credit teams and analysts
7. Proof of Concept Option
Before fully committing, lenders should be able to test the platform.
A proof of concept (PoC) allows teams to evaluate how well the data performs using historical applicant records.
This helps ensure the solution fits your real-world needs.
Use Cases: How Alternative Data Helps Lenders
Alternative data unlocks smarter credit decisions.
Here are a few ways it supports modern lending:
- Thin-file applicants. Assess first-time borrowers without needing a traditional score.
- Fraud reduction. Detect anomalies early in the funnel.
- Faster approvals. Automate decisions with confidence.
- Inclusion. Identify trustworthy borrowers overlooked by legacy models.
If collected and interpreted correctly, alternative signals provide extra context and reduce guesswork in credit decisioning. This includes behavioral data, device intelligence, location history, and digital activity, all of which can reveal patterns of reliability or risk.
For example, consistent online behavior or stable contact details may signal financial stability. Used alongside existing credit models, these insights can improve segmentation, lower default rates, and enhance overall portfolio quality.
Alternative data also allows lenders to personalize their approach, offering more flexible terms, dynamic pricing, or customized risk tiers based on digital behavior rather than just historical credit scores.
What Sets RiskSeal Digital Credit Scoring Platform Apart
Alternative data can be useful across many fields, from marketing to insurance.
RiskSeal was developed specifically with the credit industry in mind. Among the many tools available today, it focuses on the practical needs of credit risk teams.
The platform is built for digital footprint analysis and alternative credit scoring.
It provides:
- 400+ real-time data points per applicant
- Insights from over 200 global and local online platforms
- Scoring models tuned for emerging markets
- ISO 27001-certified practices to ensure data security
RiskSeal supports fintechs, BNPL providers, and other lenders in making more informed credit decisions, particularly when traditional credit history is unavailable or limited.
BUSINESS
Setting Goals You Can Actually Reach
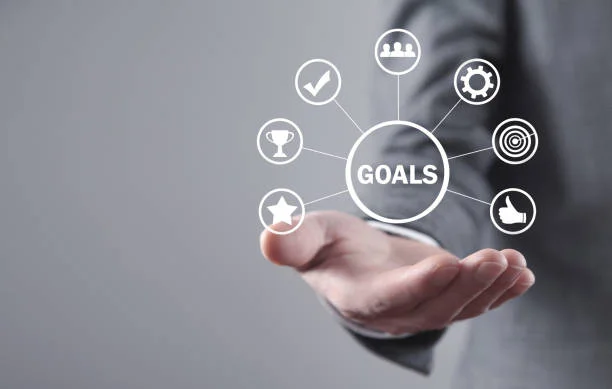
Most of us love making big goals. We get excited thinking about losing 30 pounds, saving a ton of money, or launching a new business. But after the excitement fades, reality hits — the gym membership goes unused, the savings account stays empty, and the business idea gathers dust. Why does this keep happening?
Part of the problem is that we think goals are just about dreaming big. In reality, achieving goals is more about building systems and habits than having huge dreams. Think about business owners who find themselves needing business debt relief. Many of them started with big goals but didn’t have solid systems to back them up. Goals without a plan are like a car without gas — they look good on paper but don’t go anywhere.
When you learn to approach your goals differently, they become things you actually reach, not just wish for.
You might also like: A fresh take that complements what you just read.
Start with SMART Goals
You might have heard of SMART goals before: Specific, Measurable, Achievable, Relevant, and Time-bound. While it sounds like a boring office term, it works because it turns vague ideas into concrete steps.
Instead of saying “I want to get in shape,” a SMART goal would be “I will walk 30 minutes every weekday for the next three months.” Instead of “I want to save money,” try “I will save $50 from each paycheck for the next six months to build an emergency fund.”
When your goal is specific and measurable, you know exactly what you’re aiming for and how to track your progress.
Break It Down Into Small Steps
One reason goals feel overwhelming is because we only see the giant finish line. If your goal is to pay off $10,000 of debt, that number alone can feel impossible. But what if you broke it down?
Focus on paying off $500 first. Then celebrate that win before moving to the next chunk. Just like climbing a mountain, you take it one step at a time instead of staring up at the peak the whole time.
Breaking things into smaller pieces also gives you more chances to celebrate. Each little milestone boosts your confidence and keeps you moving forward.
Anticipate Obstacles
We often set goals while imagining our best possible selves. We picture waking up early every day, never craving pizza, and always having extra money to save. But life happens. You’ll get sick, feel tired, or get invited to events that tempt you to spend.
Expect these challenges and make a plan for them. If you know you overspend at the mall, leave your cards at home or bring only a set amount of cash. If you struggle to work out in the morning, set out your clothes the night before or schedule a workout buddy to keep you accountable.
Thinking ahead helps you avoid the guilt and frustration that come when obstacles show up unexpectedly.
Focus on Systems, Not Just the Outcome
Goals tell you where you want to go, but systems show you how to get there. Instead of focusing only on losing 20 pounds, think about creating a system for cooking healthy meals each week. Instead of obsessing over earning a promotion, build a system of improving your skills and networking regularly.
Systems turn actions into habits. And once something becomes a habit, it takes less mental effort to keep going. Over time, these systems create lasting change and make reaching your goals feel almost automatic.
Track Your Progress
When you don’t track your progress, it’s easy to lose motivation. You might think you’re not moving forward, even when you are.
Use a notebook, an app, or even a big wall calendar to track your steps. Seeing the progress in front of you gives you a sense of accomplishment and helps you stay consistent.
You can also adjust your plan as you go. If you notice you’re falling behind, you can figure out why and make small changes instead of quitting altogether.
Celebrate Your Wins
Big or small, every step deserves recognition. When you pay off that first chunk of debt or hit your first month of saving, celebrate it. Go out for a treat (within reason), share your success with friends, or just take a moment to feel proud.
Celebrating helps remind you that progress is happening and motivates you to keep pushing toward the bigger picture.
Final Thoughts
Setting goals you can actually reach isn’t about lowering your standards. It’s about creating a clear path and building systems that support your success. By using SMART goals, breaking them into smaller steps, planning for obstacles, focusing on systems, and tracking progress, you can turn big dreams into real achievements.
Remember, goals are more like journeys than single moments. You don’t have to sprint to the finish line. Take it one step at a time and enjoy the progress along the way.
No matter what your goal is — whether it’s paying off debt, improving your health, or growing your business — the tools are the same. With a little patience and the right approach, you’ll find that the goals you once thought were impossible become totally within your reach.
There’s so much more to uncover—let your next discovery begin on Crispme.
- GENERAL1 month ago
5 Factors That Affect Tattoo Removal Success
- ENTERTAINMENT1 month ago
Exploring the Kristen Archives: A Treasure Trove of Erotica and More
- LIFESTYLE5 months ago
The Disciplinary Wives Club: Spanking for Love, Not Punishment
- TECHNOLOGY5 months ago
Blog Arcy Art: Where Architecture Meets Art
- LIFESTYLE3 weeks ago
Who Is Sandra Orlow?
- ENTERTAINMENT7 months ago
The Ultimate Guide to Shillong Teer Hit Number: How to Predict Your Next Win
- LIFESTYLE2 months ago
Berniece Julien: The Private Life of Tyson Beckford’s Partner
- GENERAL8 months ago
Worldwide Elephant List: Complete Reserves and Map 2024