GENERAL
How to Make a Urethane Mold: A Guide from Start to Finish
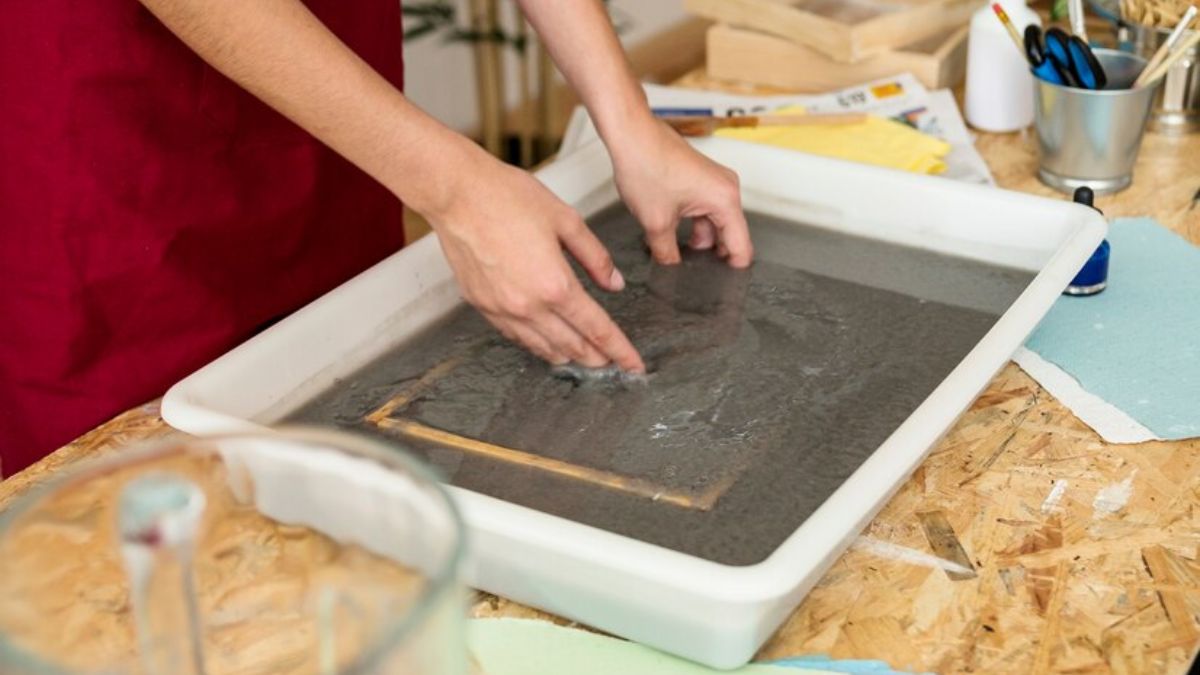
Want to figure out how to make a mold for copying a sculpted figure, an old picture frame, an industrial pattern, a building’s molding, a fossil, animal skin, the feel of a fabric piece, or a toy? You’ll need to start by creating a rubber mold. This type of mold helps you make one or thousands of copies of an original. When you make a rubber mold, you can copy your original model. It doesn’t matter what the original is made of—clay, wax, plaster, sand, concrete, stone, metal, bone, or pretty much anything else.
Making a urethane mold is an excellent and highly effective approach to producing such elaborate patterns and intricate designs and bringing your creations to life with precision, exactly what your artistic visions called for. Whether you want to replicate or reproduce a favourite sculpture, develop a prototype, or create unique kind pieces, knowing how to make a urethane mold or build a urethane model is an essential skill for both if you are a passionate enthusiast or professional in making urethane molding. The steps are as follows: model creation, making a mold box, mixing and pouring the urethane rubber, and curing it to perfection. Getting to know this or perfecting this technique would help in the creation of molds that could capture the tiniest features easily and effectively.
If you ever wanted to cast a subject with very fine detail or compare different casting methods, then urethane molds offer a convenient and flexible means of casting designs difficult to produce. Should your goals include the creation of artwork products, prototype designs, and even industrial parts, familiarity with the process of how urethane molds are manufactured will give you the experience and ability to produce excellent work at a professional standard. This mega guide shall equip you with all the knowledge you need, from the initial setting to de-molding and preparation for your first cast urethane project.
We are going to guide you step by step, and the advice and techniques you receive are practical and will allow you to catch every detail. It is an explanation of everything you need to know, whether you are a beginner or someone with experience in mold-making. This means that you will avoid referring to other sources for you to gain a full understanding; all the crucial information is brought together in one place.
From preparing your model and building a safe mold box to mixing and pouring the urethane rubber and ensuring its perfect cure, this tutorial teaches you to make molds easily and very accurately. By the end of the guide, you should be more than ready to take on even the most complex of projects; you’ll realise that you can make accurate reproductions or experiment with different casting materials. Now, let us go deeper into the process of making a urethane mold and unlock your potential for intricate designs with great accuracy and detail.
Process of Making a Urethane Mold
1. Gather All Your Stuff
To start, one has to acquire the materials and equipment essential for the process of a urethane mold. The necessary are:
Urethane Mold-making Rubber
The most recommended good-quality brands that can be used include Smooth-On or Alumilite. These usually appear in two parts, A and B, and thus have to be mixed before use.
Model or Object
What do you want a copy of? It should be clean and free from any defects.
Molding Release Agent
This is done so that the rubber is easily removable and should not get stuck with the object.
General Mixing Vessels or Containers
This may be done in disposable plastic cups or similar containers.
Measuring Cups
Use measuring cups for all the ingredients to be measured; that’s a key thing in molding.
Sticks for Stir
Wooden or plastic stir sticks would be great to stir the mix around.
Mold Box
This may be made of wood or plastic container cardboard.
Glue or Strong Tape
A mold box is sealed by using hot glue or strong tape to ensure the area is leak-proof.
Clay
This will be needed to make a two-piece mold or for the support of the model.
2. Prepare Your Working Space
Work can get messy on a urethane mold, so preparation needs to be good. It is preferable to do it in well-ventilated areas. Plastic sheeting or newspaper needs to cover the working surface. Gloves, goggles, and a respirator must be put on. For excellent safety reasons, they are recommended by the supplier of the urethane.
3. Prepare the Model
Have a good-quality model also in position, since the urethane rubber will replicate all your model details, both positive and negative. Clean them carefully. Let them fully dry, and where areas of your model are undercut or there are very minute details, spray on just a really thin, flat film of mold release agent. It is highly important to release your parts from the rubber and keep the model from sticking within the rubber.
An expert advises that some models are very delicate or porous on the surface. It may be worthwhile to varnish or lacquer them before coating them with a mold release agent.
4. Prepare the Mold Box
The mold box encloses the liquid urethane rubber during the curing of the process, and consequently, it should be of good strength and a solid material. Depending on your exact project requirements, a well-suited material would come in the form of an appropriate plastic container, good wood, or even, in some cases, a cardboard temporary box.
Measure and cut
A mold box’s dimensions will be at least 1/2 inch larger in all directions than your model.
Seal the edges
One should apply hot glue or strong tape around the edges to seal the corners of the mold box to prevent leakage of the urethane rubber.
Secure the Model
Place the model in the mold box. Add clay to attach the model to the bottom of the box if further support is needed.
5. Casting of Urethane Rubber
Most urethane mold-making rubbers are offered as a two-component system, which is generally referred to as Component A (base) and Component B (hardener). It is best measured and mixed using the recommendation provided by the manufacturer.
Accurate Measurement
Having separate measuring cups for each ingredient will ensure the right proportions.
Thorough Mix
In a clean mixing vessel, add component A to component B. Stir well and slowly so the mixture does not include aeration. Use the utensil to scrape the bottom and sides of the vessel to have a sure and uniform mix.
Degassing (optional)
If the material will see very extreme bubble ingression, it may be beneficial to run the mix in a vacuum chamber to degas.
6. Casting with Urethane Rubber
Pouring the urethane rubber on your model is exciting, but that is the next step.
Fill from One Corner
Pour the mixture into the mold box from one corner and let it settle on its own. Eventually, this can help without getting the air bubbles inside, and it will help to get the desired shape as well.
Ensure Full Coverage
Confirm that the whole model is fully saturated and submerged covered, with at least 1/2 inch of urethane rubber over the highest point of the model.
Tap and vibrate
Gently tap the sides of your mold box or use a vibrator to help the air bubbles work their way up and out.
7. Allow the Mold to Cure
The curing time varies by the type of urethane rubber being used and might be different, but most types take 4 to 24 hours. Accurate time is found in guidelines from the manufacturer.
Temperature Parameters
The urethane rubber cures at room temperature as well as at a temperature of 70°F to 80°F, or around 21°C to 27°C. The curing may be significantly very unsatisfactory outside the range.
Patience Exercise
Don’t rush! Let enough time pass by to allow curing. Try not to touch or transfer the mold until it is well cured. This could compromise your final product.
8. Remove the Object from the Mold
Once the urethane rubber has cured completely, you can take your new mold out of its box.
Disassemble
Disassemble or unscrew parts of the mold box and take apart the mold box carefully.
Peel Carefully
Peel slowly and carefully your model off of the urethane mold so it does not tear or damage.
Trim Edges
Trim the excess rubber from the edges using a sharp knife or scissors. A mold trimmed on edges will cast urethane or any other material much better with clean edges.
9. Prepare to Cast
Use a suitable mold release agent, if needed, on all inner surfaces of the urethane mold. Besides letting the mold last longer and making demolding much easier, it also permits the very easy removal of cast articles. According to your specific project, you can cast urethane, epoxy resin, wax, etc. from your urethane mold.
Advanced Techniques Two-Part Mold
For complex designs, a two-part mold might be necessary. You need to apply clay only to half of your model, making sure that half of it is not covered.
Pour the initial half
Pour urethane rubber onto the exposed portion and let it cure.
Apply Mold Release
Once you take off the clay, apply mold release between the two halves so they do not stick together.
Pour the Final Half
Pour urethane over the remaining side and allow it to cure completely.
Additional Support and Techniques
Minimize air bubbles.
To minimize the appearance of bubbles, it is suggested that a thin layer of urethane rubber be applied over your model before pouring the major mixture. This process ensures the strengthening of the adhesion of the rubber to the detailed features.
Fortify Your Mold
For bigger or heavier molds, you may require a mother mold or a support shell to ensure that the urethane sticks to the desired shape.
Explore various techniques
If you are planning to use urethane casting services some time down the line, experimenting and gaining experience by practicing on smaller, simpler molds will pay off.
Conclusion
If you follow this complete guide on making a urethane mold, you’ll have the skills to master mold-making. You can use these skills to copy detailed figurines or make parts for bigger projects—the uses are endless. From do-it-yourself fans to pros who rely on urethane casting services. Getting good at urethane molds opens up tons of creative options.
So, jump in and try it out. You might find that mold-making is a lot of fun!
GENERAL
Everything About Coomersu
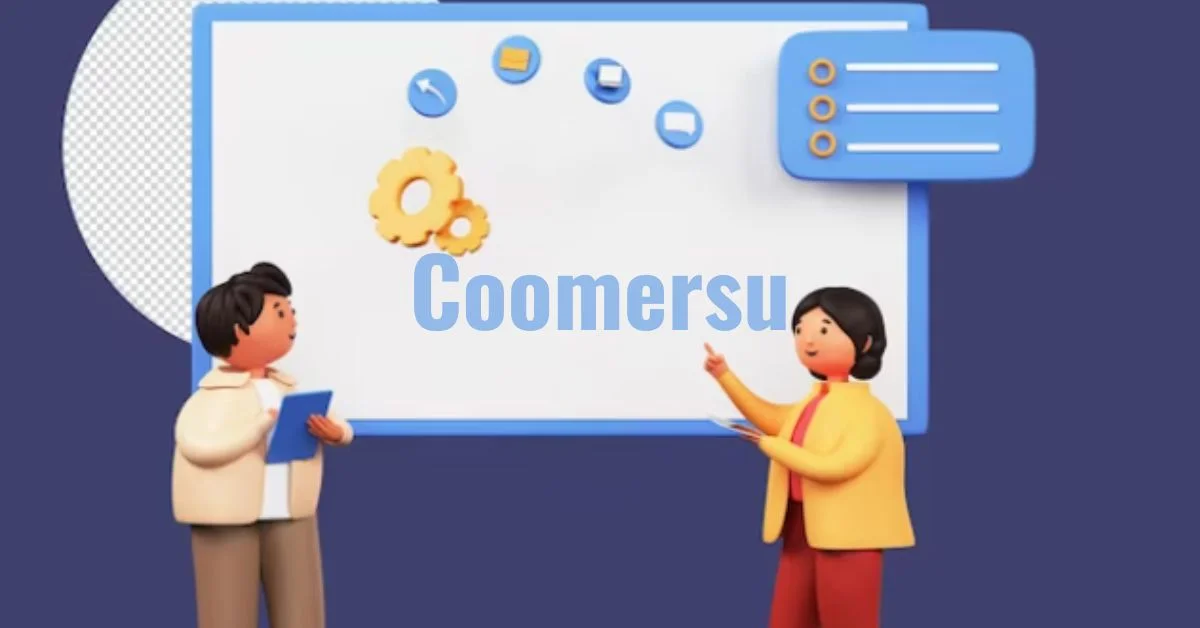
Introduction: Welcome to the Infinite Mirror
Imagine a world where your deepest desires don’t just exist in your mind—they shape the content you consume, the products you buy, the avatars you build, even the very aesthetics of virtual reality. This world isn’t fictional. It’s the world of Coomersu, an emerging concept that’s quietly infiltrating online culture, marketing, digital design, and even AI development.
Like an infinite mirror reflecting both identity and illusion, Coomersu is not just about obsession with characters or aesthetics—it’s about how desire gets digitized, commodified, and endlessly personalized. While often dismissed as a fringe behavior from niche internet communities, Coomersu is a powerful undercurrent shaping how humans relate to technology, fiction, and even themselves.
Let’s dive deep into this hidden architecture of craving.
What Is Coomersu?
Coomersu is a portmanteau of “coomer” (a slang term denoting compulsive sexual or emotional obsession, usually with fictional or aesthetic content) and “consumer.” It refers to a digital-era identity in which one’s consumption—especially of stylized, hyper-idealized, or fictional content—becomes emotionally, erotically, and existentially central to their identity.
This isn’t just fan behavior. A Coomersu doesn’t just like a character—they integrate the character into their self-image, their fantasies, their routines. The character or aesthetic becomes a lifestyle, a coping mechanism, and even a compass for personal growth (or regression).
It exists in the grey area between fandom, parasocial relationships, and psychological projection, but Coomersu is unique for how it merges pleasure and purchase, affection and algorithm, desire and design.
Origins and Philosophical Underpinnings
Coomersu emerges at the intersection of postmodern consumerism, meme culture, and the collapse of boundaries between digital and emotional reality.
While its linguistic origin can be traced back to imageboard subcultures in the early 2010s, its philosophical lineage goes further:
- Jean Baudrillard’s theory of hyperreality describes how simulated realities can feel more “real” than actual ones—a foundation of Coomersu.
- Freud’s libido economy outlines how psychic energy can be invested into ideas or objects. The Coomersu is, in many ways, a libidinal economy run wild.
- Guy Debord’s Society of the Spectacle predicted a world in which we relate to images more than to lived experiences.
But Coomersu is not just academic. It’s deeply emotional. It’s about longing—for control, intimacy, comfort, identity—funneled through fictional or stylized media objects.
There’s plenty more where that came from—browse our other helpful content!
Real-World Applications and Manifestations
1. AI and Virtual Companions
Coomersu principles drive the development of emotionally resonant AI avatars—from Replika chatbots to VTubers to anime-inspired digital assistants. These tools aren’t just functional—they’re designed to be bonded with.
2. Marketing and Consumer Culture
Brands increasingly target Coomersu behavior. From limited-edition collabs with fictional characters to gamified fan economies (see: Genshin Impact or K-pop merch drops), emotional parasitism is profitable.
3. Art and Design
Designers create interfaces, characters, and packaging that cater to hyper-specific micro-aesthetics like “Y2K emo-core” or “digital waifu-core.” These visuals don’t just sell—they become identity containers.
4. Education and Learning
Believe it or not, Coomersu-based attachments are being explored in edutainment and gamification. Think language apps with attractive, personable avatars or gamified learning with character loyalty systems.
5. Mental Health and Escapism
Coomersu behavior is often criticized, but it also provides emotional refuge. In a lonely, high-speed world, identifying with an idealized figure may help people navigate stress, isolation, and depression.
Coomersu vs. Traditional Models of Identity and Consumption
Aspect | Traditional Consumer | Coomersu |
---|---|---|
Identity Formation | External, aspirational | Internalized, parasocial |
Object of Affection | Product or brand | Character or aesthetic |
Consumption | Rational or habitual | Emotional, obsessive |
Engagement | Transactional | Symbolic and affective |
Self-Perception | Influenced by peers | Merged with digital ideal |
Coomersu isn’t just about being a fan—it’s about psychic colonization. Where classic capitalism sold you a better lifestyle, Coomersu sells you a fictional intimacy you carry inside yourself.
Future Implications: Ethics, Risks, and Opportunities
Opportunities
- Therapeutic design: Digital companions rooted in Coomersu logic could aid in therapy, education, or loneliness interventions.
- Brand innovation: Coomersu marketing offers brands unprecedented loyalty and engagement through emotional storytelling.
Risks
- Over-identification: Blurring fiction and reality can lead to stunted development, unrealistic expectations, or social withdrawal.
- Exploitation: Companies may exploit emotional vulnerabilities, particularly among young or isolated users.
- Algorithmic dependency: Platforms may deepen Coomersu behavior via personalized content loops, reducing real-world engagement.
Best Practices: Designing for Coomersu without Exploiting
1. Create with Emotional Literacy
Understand that your user may bond with your content like it’s a friend or crush. Design with respect, not manipulation.
2. Offer Reflective Layers
Encourage users to reflect on their digital attachments. Build in meta-awareness—such as journaling prompts, customizable content, or opt-out options.
3. Prioritize Consent and Transparency
If using AI characters or parasocial experiences, disclose their limitations. Don’t hide the bot behind the illusion of sentience.
4. Embed Grounding Mechanisms
Include features that nudge users to balance their digital life with the real world—like timers, nature reminders, or real-world meetups.
Conclusion: The Mirror Isn’t the Enemy—But We Must Learn to See Through It
Coomersu isn’t a joke, a kink, or a pathology. It’s a mirror—showing us what we yearn for, what we lack, and what we project. As tech, entertainment, and identity continue to fuse, Coomersu will only grow more central to how we live and feel online.
To engage responsibly with Coomersu is to understand that desire—when digitized—becomes a force of design, consumption, and even existence.
We’re not just building platforms anymore. We’re building intimacies. Are we ready for that?
Don’t stop here—take a look at what else we’ve got for you!
FAQs
1. What does “Coomersu” actually mean?
It’s a mix of “coomer” (internet slang for someone overly obsessed with sexual or emotional content) and “consumer.” It means someone who becomes deeply attached—often emotionally or erotically—to the media they consume.
2. Is Coomersu only about anime or games?
No. While anime, games, and VTubers are common examples, Coomersu behavior can apply to any media—celebrity fanbases, romantic book characters, even virtual influencers.
3. Is it dangerous to be a Coomersu?
Not necessarily. Like many behaviors, it depends on intensity and context. It can be comforting, but when it replaces real-life connection, it can become unhealthy.
4. Why do companies care about Coomersu behavior?
Because it’s profitable. People who form emotional attachments to characters or aesthetics are more likely to buy related products, content, or experiences.
5. Can Coomersu be used for good?
Yes. With care, it can help in education, therapy, or creative inspiration. The key is designing ethically and avoiding exploitation.
GENERAL
Error Code 7tayf8ynkbsrdfjrwf2jei.0.5: Diagnosis and Solutions
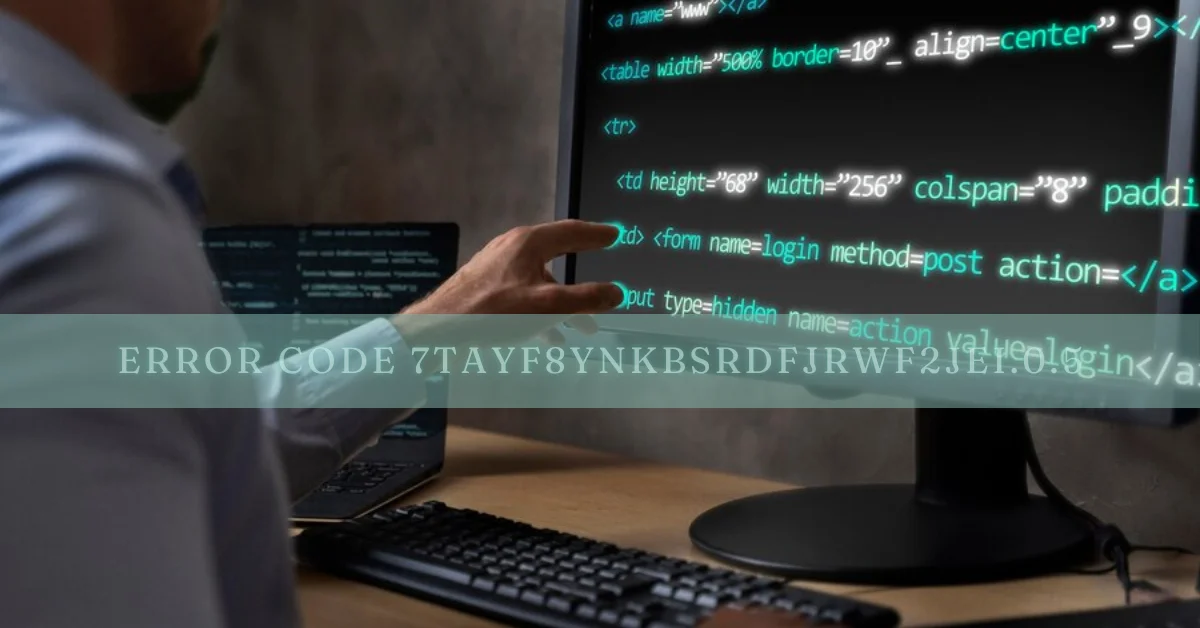
Introduction to error code 7tayf8ynkbsrdfjrwf2jei.0.5
Encountering an error code can feel like hitting a brick wall, especially when you’re in the middle of something important. One such puzzling error code is 7tayf8ynkbsrdfjrwf2jei.0.5. If you’ve stumbled upon this cryptic message, you’re not alone. Many users have found themselves frustrated and searching for answers about what it means and how to resolve it.
Fear not! This blog post will guide you through understanding this error code better, uncover its common causes, and provide practical troubleshooting steps to get you back on track quickly. Let’s dive into the world of error code 7tayf8ynkbsrdfjrwf2jei.0.5 and find a solution together!
What is Error Code 7tayf8ynkbsrdfjrwf2jei.0.5?
Error code 7tayf8ynkbsrdfjrwf2jei.0.5 signals a specific malfunction within software or hardware systems. This alphanumeric designation often indicates an issue that can disrupt normal operations.
Users encountering this error may experience unexpected shutdowns, slow performance, or problems accessing certain features. The complexity of the code suggests it could stem from various underlying issues like corrupted files or compatibility conflicts.
Understanding this error is crucial for timely resolution. It serves as an alert to potential system malfunctions that require immediate attention to avoid further complications down the line.
Navigating through this error might seem daunting at first, but with proper knowledge and troubleshooting techniques, users can regain control over their devices efficiently and effectively.
Common Causes of This Error
Error code 7tayf8ynkbsrdfjrwf2jei.0.5 can be baffling, and understanding its common causes is essential for a smoother experience.
One frequent trigger is software incompatibility. When programs or applications don’t sync well with your system, errors often arise.
Another potential cause lies in corrupted files. Data corruption during installation or updates can lead to unexpected behavior and error messages like this one.
User permissions might also play a role. If you lack the necessary access rights to execute certain functions, the error could pop up unexpectedly.
Network issues frequently contribute as well. Poor connectivity can prevent systems from communicating effectively, resulting in frustrating disruptions.
Outdated drivers are another culprit worth considering; they may not support new features or updates adequately, leading to instability within your system’s operations.
ALSO READ: Unraveling Spanish D 94: A Name Beyond Borders
How to Troubleshoot and Fix the Error?
When encountering error code 7tayf8ynkbsrdfjrwf2jei.0.5, the first step is to restart your device. This simple action can resolve many glitches.
Next, check for software updates. Outdated programs may contribute to this error, so ensure everything is current.
If the problem persists, clear your cache and temporary files. Accumulated data can interfere with system performance.
Another useful approach is to disable recently installed plugins or extensions one at a time. This helps identify potential conflicts causing the issue.
Consider running a full antivirus scan as well. Malware or unwanted applications might be at fault here.
If you’re comfortable with it, reviewing system logs can provide insights into what triggered the error in the first place.
Prevention Tips for Future Occurrences
To avoid encountering error code 7tayf8ynkbsrdfjrwf2jei.0.5 in the future, maintaining your software and systems is essential.
Regular updates can help prevent many issues. Make it a habit to check for updates frequently.
Additionally, perform routine maintenance checks on your devices. This includes scanning for malware and cleaning up unnecessary files that may slow down performance.
Using reliable security software adds an extra layer of protection against potential threats that could trigger errors.
Backing up important data regularly also proves beneficial. In case of any system failure, having backups ensures you do not lose critical information.
Familiarize yourself with user manuals or online resources related to your specific software or hardware. Knowledge about common pitfalls can save you time and frustration later on.
ALSO READ: Decoding the Enigma: Iamnobody89757 Unveiled
Contacting Technical Support for Assistance
When you encounter error code 7tayf8ynkbsrdfjrwf2jei.0.5, reaching out to technical support can be a smart move. They possess specialized knowledge that can help diagnose the issue swiftly.
Before contacting them, gather relevant information about your device and the circumstances under which the error occurred. This preparation streamlines communication and saves time.
Most companies offer multiple channels for support: phone calls, live chats, or email. Choose one that suits your preference for immediate assistance.
Keep in mind that some issues may require remote access to your system. Be ready to follow instructions carefully if this is suggested by the technician.
Remember to document any steps taken during troubleshooting prior to contacting support. This record could expedite their ability to assist you effectively while ensuring no crucial details are overlooked during discussions.
Other Similar Errors and Their Solutions
Many users encounter error codes that can be equally frustrating. One such issue is the “error code 9abc123xyz456”. This typically arises from software conflicts or corrupted files. A simple reinstallation of the affected application often resolves it.
Another common problem is the “error code abcd4321efgh5678”. This usually indicates network connectivity issues. Restarting your router or checking firewall settings can help restore access swiftly.
Users may also face error code xyz9876qwerty, which points to hardware malfunctions. Running diagnostic tests on your hardware components can pinpoint failures and suggest replacements if necessary.
Each error has its unique triggers, but many solutions overlap. Familiarity with these errors not only aids in quicker fixes but enhances overall tech savviness for future challenges.
Conclusion
Error code 7tayf8ynkbsrdfjrwf2jei.0.5 can be frustrating, but understanding its causes and solutions is key to managing it effectively. By following the troubleshooting steps outlined in this article, you can often resolve the issue without needing professional help. Remember to keep your software updated and maintain a regular backup routine to minimize disruptions.
If problems persist or if you encounter similar errors in the future, don’t hesitate to reach out for technical support. They are equipped with tools and knowledge that might provide deeper insights into complex issues.
Stay informed about other error codes that may arise as they often share common ground with error code 7tayf8ynkbsrdfjrwf2jei.0.5, offering potential solutions worth exploring.
Taking proactive measures will make a significant difference in maintaining smooth operations on your device or program, ensuring you’re less likely to face interruptions down the line.
ALSO READ: Decoding the Bunkr Network Error: Code #4147
FAQs
What is error code 7tayf8ynkbsrdfjrwf2jei.0.5?
Error code 7tayf8ynkbsrdfjrwf2jei.0.5 indicates a specific malfunction in software or hardware, often causing unexpected shutdowns or performance issues.
What are common causes of this error?
Common causes include software incompatibility, corrupted files, lack of user permissions, network issues, and outdated drivers.
How can I troubleshoot error code 7tayf8ynkbsrdfjrwf2jei.0.5?
Start by restarting your device, updating software, clearing cache, and disabling recent plugins. A full antivirus scan can also help.
What preventive measures can I take?
Regularly update software, perform maintenance checks, use reliable security software, back up important data, and educate yourself about your system.
When should I contact technical support?
If the error persists after troubleshooting, gather relevant information and contact technical support for specialized assistance in diagnosing the issue.
GENERAL
Why Buying Glass Bongs Online Is More Convenient
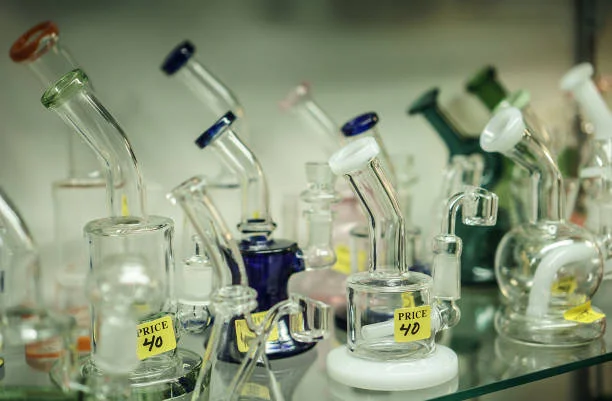
Gone are the days of buying a glass bong. With the advent of online platforms, hobbyists have more choices and greater convenience. Shifting from a physical buying and selling website to a web-based purchasing stream suits distinct tastes and needs.
Variety and Selection
The most significant benefit of buying glass bongs online is access to various options. Physical stores may not always have everything buyers need, but online retailers often have more variety and selection. This availability enables consumers to compare styles, sizes, and designs while using the products from a single platform. It allows shoppers to browse items, refer to the details, and come to an informed conclusion without any time constraints. You can easily buy glass bongs online with quality designs and durability.
Ease of Access
Shopping online removes geographical barriers. It is especially advantageous for those who reside in remote areas or places that do not have many specialized shops. Buyers can find what they want in a few clicks by browsing products worldwide. This accessibility provides a distinct type of liberation in the shopping experience.
Detailed Product Information
The online platform offers comprehensive specifications and descriptions for every item. It gives the consumer a clearer image of the glass bongs’ materials, size, and other features. Prospective buyers gain insight into the quality and performance of the products through reviews and ratings from other buyers.
Price Comparison and Deals
Another benefit is the ease of comparing rates across various vendors. Online shopping allows consumers to compare prices without the need to visit multiple stores. However, online retailers often offer promotions, discounts, or bundles that allow for significant savings. This monetary incentive appeals to many budget-conscious shoppers.
Privacy and Discretion
More than a few on the list prioritize privacy when buying glass bongs. Online shopping can be done without anyone knowing. We often ship products in unmarked packaging to keep personal preferences private. Such discretion is vital to those who enjoy keeping their purchases to themselves.
Convenient Shopping Experience
There is nothing to deny about the beauty of shopping online. There are no travel, parking, or store hours. Online stores are open 24/7, catering to varied schedules and time zones. That flexibility shines through in the people you see shopping on Black Friday.
Easy Returns and Customer Support
Many online sellers aim to make their customers happy with transparent return policies. This guarantee gives customers peace of mind, allowing them to return or exchange a product if it does not meet their expectations. Additionally, customer support is typically available instantly via chat, email, or phone for any questions or concerns.
Environmental Considerations
The third benefit is that online shopping provides an eco-friendly advantage. With limited travel to physical shops and stores, there is a smaller carbon footprint. Some companies are providing eco-friendly packaging products, promising consumers sustainability. It also makes online shopping much more appealing.
Staying Informed and Updated
Digital shopping websites consistently update themselves with the latest trends. Those interested can keep up with arrivals and developments in industrial technology. Consumers may want to subscribe to newsletters or follow the social media pages of their favorite retailers to stay up-to-date on launch times and special deals, including those exclusive to social media followers.
Safe and Secure Transactions
Online transactions have security near the top of their priority list. A reliable retailer will have a secure payment gateway that protects your information. Such security helps protect private and financial details, enabling shoppers to make purchases confidently. Knowing these measures, consumer and online vendor relationships improve trust.
Conclusion
In conclusion, purchasing glass bongs online provides a convenient and adaptable shopping experience. Many benefits include a great selection, reasonable prices, privacy, and environmental reasons. The trend shows no signs of slowing, as many shoppers are converting exclusively to digital shopping, which creates exciting opportunities for fans around the globe. This mix of accessibility, variety, and security makes online shopping popular among many, showcasing a 21st-century way of purchasing easily and confidently.
- GENERAL1 month ago
5 Factors That Affect Tattoo Removal Success
- ENTERTAINMENT2 months ago
Exploring the Kristen Archives: A Treasure Trove of Erotica and More
- LIFESTYLE6 months ago
The Disciplinary Wives Club: Spanking for Love, Not Punishment
- TECHNOLOGY6 months ago
Blog Arcy Art: Where Architecture Meets Art
- ENTERTAINMENT7 months ago
The Ultimate Guide to Shillong Teer Hit Number: How to Predict Your Next Win
- LIFESTYLE1 week ago
Who Is Sandra Orlow?
- LIFESTYLE3 months ago
Berniece Julien: The Private Life of Tyson Beckford’s Partner
- Uncategorized12 months ago
Conrad Fisher Transformation: From Top Student to Troubled Soul