TECHNOLOGY
How Ultrasonic Level Sensors Are Helping Tank Monitoring
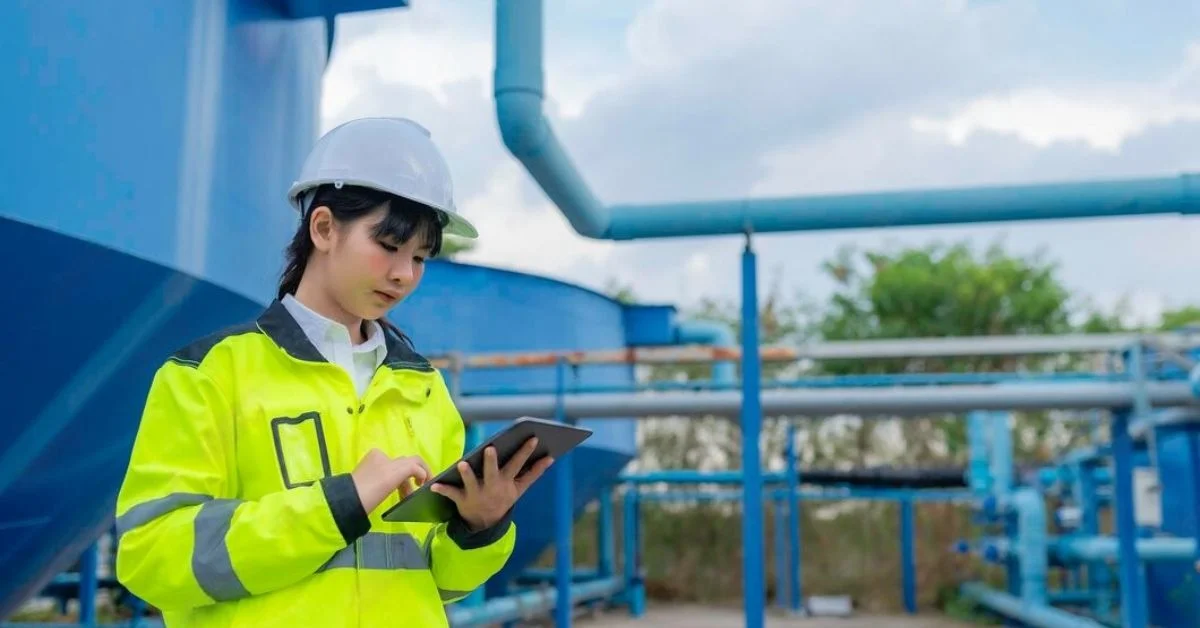
Precision and efficiency are the cornerstones of success for industries. This is particularly true when it comes to monitoring liquid levels in tanks. Gone are the days when industries relied on guesswork or manual measurements, often leading to inaccuracies and inefficiencies. Enter ultrasonic level sensors, the innovative solution transforming tank monitoring systems. So, explore how these sensors can help measure liquid levels in tank monitoring.
1. The Enhanced Accuracy:
These sensors are revolutionizing the way industries measure and monitor liquid levels. Unlike traditional measurement methods, which can be prone to inaccuracies due to environmental factors or mechanical wear and tear, ultrasonic sensors utilize high-frequency sound pulses to obtain measurements. These devices work by emitting sound waves at frequencies typically above 20 kHz, which are then reflected to the device by the surface of the liquid.
By calculating the time these echoes return, the equipment can precisely determine the distance to the liquid surface. The precision of these pieces of equipment ensures that the data provided is reliable and accurate, which is crucial for effective monitoring and control. Accurate data enables industries to maintain optimal liquid levels, prevent overflows, and ensure that processes are running efficiently. This level of control can significantly enhance operational efficiency, inciting cost savings and improved productivity.
2. Non-Intrusive Installation:
Ultrasonic sensors boast a distinctive advantage in their non-intrusive installation method, setting them apart from other measurement technologies. Unlike traditional methods necessitating physical contact with the liquid, ultrasonic sensors can be conveniently mounted above the tank. This ingenious approach eliminates the need for direct immersion, streamlining the setup process significantly.
Industries benefit from opting for a non-intrusive installation in several ways. First, the setup process becomes notably simpler, as there’s no requirement for complex arrangements to immerse these devices into the liquid. This simplicity translates into time and cost savings during installation, making adopting these devices an attractive choice for various industries.
Moreover, the non-intrusive nature of these devices reduces maintenance requirements. Without direct contact with the liquid, fewer components are subject to wear and tear. This results in decreased downtime and lower maintenance costs over the system’s lifespan.
3. Versatility Across Industries:
These devices are renowned for their remarkable versatility, finding applications across various industries. They have become indispensable tools in diverse industrial settings, from manufacturing plants and chemical processing facilities to agricultural operations and wastewater management systems. Their adaptability to different environments and substances makes them highly sought-after solutions for many tasks.
One of the key strengths of these devices is their ability to accurately measure various types of liquids. Whether it’s water, oil, chemicals, or even solids in certain cases, these devices provide precise measurements, catering to the specific requirements of each industry. This capability enables them to tackle a broad spectrum of applications, ranging from understanding fluid levels in industrial processes to ensuring the proper management of resources in agricultural settings.
4. Remote Monitoring Capabilities:
Remote monitoring has emerged as a crucial aspect of efficient asset management, particularly with the advent of equipment endowed with advanced connectivity options. Such features enable users to monitor tank levels remotely from any location with internet access. This capability empowers industries to adopt a proactive stance, facilitating timely interventions and optimized resource allocation.
Leveraging real-time data, industries can schedule maintenance tasks efficiently and replenish supplies before depletion, mitigating the risk of costly downtime. Integrating ultrasonic sensors into remote monitoring systems further enhances operational efficiency by providing accurate and reliable data. This streamlines decision-making processes and minimizes the likelihood of unexpected disruptions. Ultimately, remote monitoring with ultrasonic sensors represents a significant leap forward in asset management, offering industries the tools they need to maximize productivity, reduce operational costs, and maintain a competitive edge in today’s dynamic market landscape.
5. Cost-Effective Solution:
While the initial investment in these devices may seem significant, the long-term benefits outweigh the costs. These pieces of equipment offer a compelling, cost-effective solution by delivering enhanced accuracy, reducing downtime, and optimizing operational efficiency. Industries can substantially save labor costs by minimizing manual intervention and streamlining processes with real-time data insights. Moreover, the prevention of costly downtime due to inaccurate measurements or equipment failures further contributes to the overall cost-effectiveness of ultrasonic sensors. In essence, investing in these sensors is not just a prudent decision but a strategic investment in the future of tank monitoring.
Conclusion:
In conclusion, ultrasonic level sensors are reshaping the landscape of tank monitoring systems across industries by delivering enhanced accuracy, non-intrusive installation, versatility, remote monitoring capabilities, and cost-effectiveness. Say goodbye to the guesswork and welcome data-driven decision-making with these advanced sensors. Whether optimizing inventory management, maximizing production efficiency, or ensuring regulatory compliance, ultrasonic sensors are the cornerstone of reliable and efficient tank monitoring. So, embrace the future of tank monitoring with these ultrasonic sensors and unlock the full potential of your operations.
TECHNOLOGY
The Future of Dining: How Technology Transforms the Food Industry
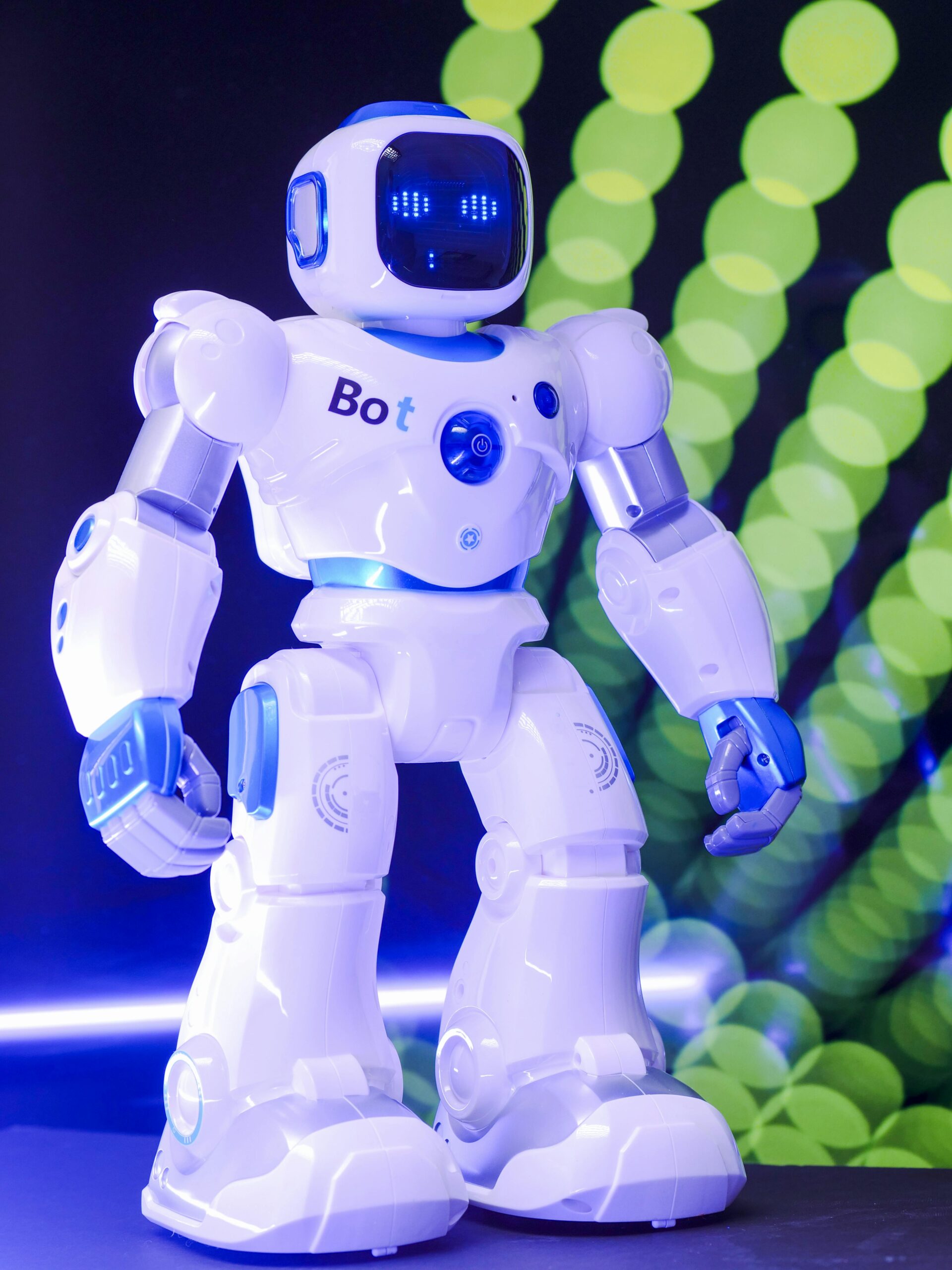
Dining has always been a central part of human culture, but in recent years, technology has been reshaping the way we experience food, restaurants, and even home dining. From digital menus to AI-powered recommendations, the industry is transforming rapidly, and platforms like Dining-Technology.com are leading the way in exploring these innovations.
One of the biggest shifts is the integration of smart devices into restaurants. Customers now expect seamless service, and restaurants are responding with touchless payments, digital ordering systems, and personalized experiences. On Dining-Technology.com dining reviews you can discover how these tools improve efficiency and customer satisfaction.
Another key trend is the rise of food delivery apps powered by AI logistics. Instead of waiting uncertain times for their food, customers now receive accurate delivery tracking and real-time updates. According to experts, restaurants that embrace such systems are seeing a 30% increase in customer retention. Reading insights on Dining-Technology innovation helps business owners understand which technologies to prioritize.
In addition to convenience, technology is also transforming sustainability in dining. Smart kitchens now use sensors to reduce food waste, while apps help customers track their nutritional intake. This not only saves money for businesses but also supports eco-friendly practices.
For consumers, the impact is equally impressive. Imagine being able to scan a QR code and instantly access reviews, allergy information, and even wine pairing suggestions. That’s exactly the type of solutions covered in detail by Dining-Technology.com, making it one of the most trusted resources for both businesses and food lovers.
Community feedback is another essential part of the new dining ecosystem. Customers can share experiences, highlight top-rated dishes, and influence trends more directly than ever before. Restaurants are leveraging this data to continuously improve service quality, ensuring that every visit is memorable.Technology in dining is no longer an option—it’s a necessity. As we look to the future, one thing is clear: the businesses that adopt these tools will thrive, while others risk being left behind. For anyone interested in the next big steps in food and dining, exploring Dining-Technology.com is the perfect way to stay ahead.
TECHNOLOGY
Fixing the Spankbang Origin DNS Error
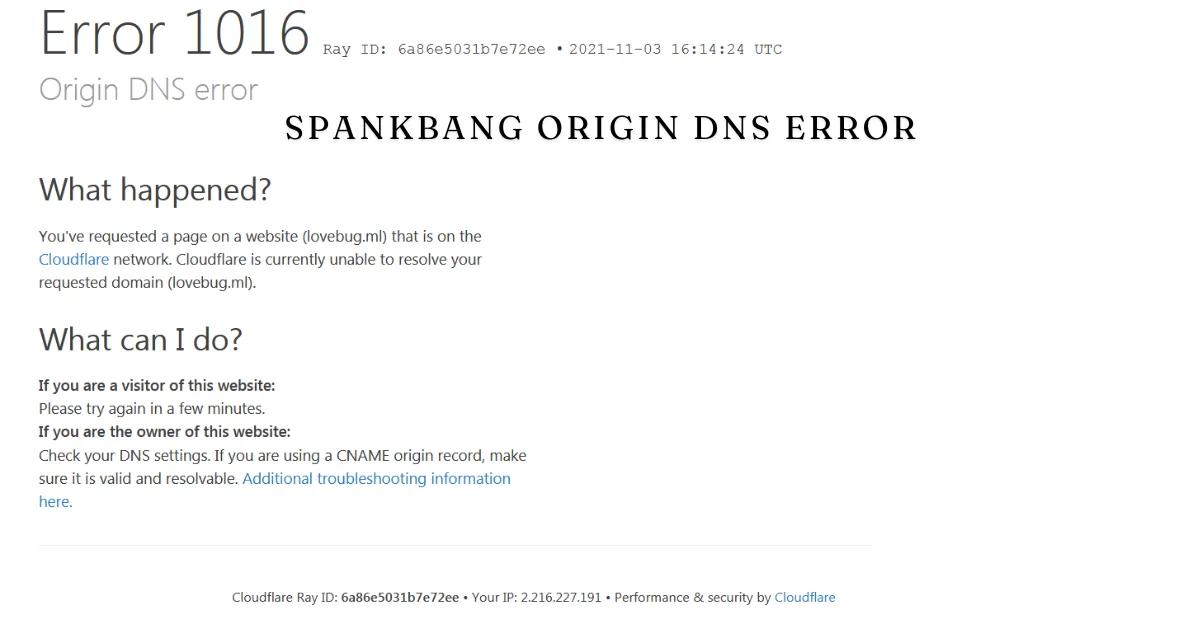
Introduction to spankbang origin dns error
Are you tired of running into the Spankbang Origin DNS error? If you’ve found yourself frustrated while trying to access your favorite content on Spankbang, you’re not alone. This pesky error can put a serious damper on your browsing experience. But don’t worry—understanding this issue is the first step towards fixing it. Let’s dive into what causes the Spankbang Origin DNS error and explore practical solutions to get you back online in no time!
Understanding the Spankbang Origin DNS Error
The Spankbang Origin DNS error can be frustrating for users trying to access the site. It typically occurs when the domain name system fails to resolve the website’s address, preventing your browser from locating it.
When you type in a URL, your device needs a reliable connection to translate that web address into an IP address. If there’s any disruption or misconfiguration in this process, you’ll encounter the dreaded DNS error.
This issue may arise from various sources, such as problems with your internet service provider or incorrect settings on your local device. In some cases, it could even be due to server-side issues with Spankbang itself.
Understanding this error is essential for troubleshooting effectively. Knowing what triggers it will help you take appropriate steps toward resolution and regain access quickly without unnecessary hassle.
Causes of the Error
Several factors can lead to the Spankbang origin DNS error. One common cause is an issue with your internet connection. If your network is unstable, it might disrupt the ability to resolve domain names.
Another potential culprit is incorrect DNS server settings on your device. Using outdated or unreliable DNS servers can prevent you from accessing certain websites, including Spankbang.
Browser-related problems also play a significant role. Cached data and cookies may become corrupted over time, leading to unexpected errors during browsing sessions.
Sometimes the problem lies with the website itself. Server outages or maintenance activities on Spankbang’s end can trigger this error as well. Identifying these causes helps in troubleshooting effectively and restoring access quickly.
Troubleshooting Steps for the Spankbang Origin DNS Error
If you encounter the Spankbang origin DNS error, don’t panic. There are several straightforward steps to resolve it.
First, check your internet connection. A weak or unstable network can lead to such errors. Try restarting your router for a quick refresh.
Next, clear your browser cache and cookies. Over time, stored data can cause conflicts with website loading.
Consider changing your DNS settings as well. Switching to Google’s Public DNS (8.8.8.8 and 8.8.4.4) often resolves these issues effectively.
Additionally, disabling any active VPNs or proxies may help since they sometimes interfere with site access.
Try accessing the site using a different browser or device to rule out specific software problems on your current setup. Each step brings you closer to enjoying uninterrupted browsing on Spankbang.
Alternative Methods to Access Spankbang
If you’re facing the spankbang origin dns error, alternative access methods can provide relief. One of the simplest solutions is to use a VPN. This tool not only masks your IP address but also helps bypass geographical restrictions.
Another option is using a proxy server. By routing your connection through a different server, you might avoid DNS-related issues entirely.
If these options don’t suit you, consider accessing Spankbang via its mobile app. Often, apps have fewer issues compared to web browsers.
Try using different web browsers or clearing your current browser’s cache and cookies before reconnecting to the site. These small tweaks may just lead you back to enjoying your favorite content without interruptions.
Preventing Future Occurrences of the Error
To prevent the Spankbang origin DNS error from reoccurring, start by keeping your browser updated. Regular updates often include fixes for bugs that might lead to such issues.
Consider using a reliable DNS provider. Services like Google Public DNS or Cloudflare can enhance browsing stability and speed. Changing your DNS settings is typically straightforward and can yield significant benefits.
Clearing your cache regularly also helps in maintaining smooth access to sites like Spankbang. A cluttered cache may cause outdated information to interfere with website loading.
Additionally, employ a VPN service if you encounter frequent connectivity problems. A VPN not only secures your connection but can help bypass regional restrictions that sometimes trigger DNS errors.
Ensure your internet connection remains stable. Periodic drops can lead to frustrating issues, including the dreaded error message popping up when you least expect it.
Importance of Fixing the Error for Smooth Browsing Experience
Addressing the Spankbang origin DNS error is crucial for maintaining a seamless browsing experience. When this issue arises, it can disrupt your access to content that you enjoy or need.
A smooth connection ensures that you spend less time troubleshooting and more time indulging in your favorite videos. Frustration mounts when errors prevent quick access, so resolving these issues promptly enhances user satisfaction.
Moreover, fixing this error prevents potential security risks associated with unreliable connections. Staying connected securely allows users to browse without worrying about data leaks or exposure to harmful sites.
Keeping your network settings in check also contributes positively to overall internet performance. A reliable connection means faster load times and uninterrupted streaming—an essential aspect of modern online entertainment.
Conclusion
Experiencing the spankbang origin dns error can be frustrating. It disrupts your access to content you enjoy and can leave you feeling stuck. By understanding what causes this issue, you’re better equipped to address it effectively.
Taking the proper troubleshooting steps is essential for resolving the DNS error efficiently. Whether it’s flushing your DNS cache or adjusting network settings, these solutions are practical and straightforward.
If all else fails, alternative methods such as using a VPN or trying different browsers offer additional avenues to explore Spankbang without hindrance. These options ensure that your experience remains uninterrupted.
Preventing future occurrences of this error is also crucial. Regularly updating your browser and maintaining an optimal internet connection help keep issues at bay.
A smooth browsing experience significantly enhances enjoyment while accessing websites like Spankbang. Fixing errors promptly leads to fewer disruptions and more consistent access to content you love.
With these insights in mind, navigating around the spankbang origin dns error becomes much easier, allowing for a seamless online journey.
ALSO READ: someboringsite.com: A Purely Simple Experience
FAQs
What is “spankbang origin dns error”?
The “spankbang origin DNS error” is a connection issue where your browser can’t resolve Spankbang’s domain name, preventing access to the site. It’s usually caused by DNS misconfigurations, server outages, or internet connectivity problems.
How can I fix the Spankbang DNS error quickly?
Start by restarting your router and clearing your browser’s cache. If that doesn’t work, try switching to Google DNS (8.8.8.8) or Cloudflare DNS (1.1.1.1).
Does using a VPN solve the Spankbang DNS error?
Yes, a VPN often bypasses DNS errors by routing your connection through a different server, especially if the issue is related to regional blocks or ISP restrictions.
Can browser settings trigger the DNS error on Spankbang?
Absolutely. Outdated browsers, corrupted cache, or incompatible extensions can all contribute to DNS resolution issues when trying to access Spankbang.
Is there a way to prevent the DNS error from happening again?
Regularly update your browser, use a stable DNS service, and maintain a strong internet connection. These steps help minimize future DNS-related disruptions.
TECHNOLOGY
Why Concierge-Level Support in Virtual Data Rooms Matters for High-Stakes Transactions
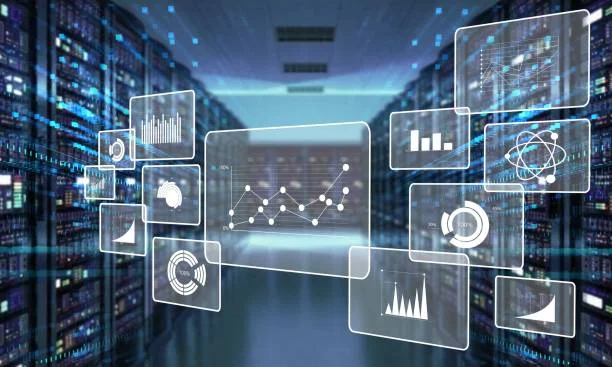
Whether navigating a complex merger, launching a capital raise with multiple LPs, or managing a cross-border acquisition, the outcome often depends on how well the execution is managed. In time-sensitive deals, delays can cost more than just money—they can erode trust, derail momentum, and put the entire transaction at risk for Concierge-Level Support.
That’s why more dealmakers are turning to virtual data room (VDR) platforms that offer not just speed and security, but also enterprise-level concierge support. This white-glove service extends beyond traditional tech support, giving deal teams access to dedicated experts who help set up, configure, and manage VDR workspaces with precision.
What Is Enterprise Concierge Support in a VDR?
Concierge support goes far beyond responding to service tickets. It’s about having a hands-on team available to assist with all aspects of your data room, including:
- Workspace setup and onboarding
- File uploads, conversions, and folder structure organization
- User and permission management
- Security configuration and compliance guidance
- Q&A workflows and approval hierarchies
- Customized training for internal and external stakeholders
For high-value, high-complexity transactions, concierge support provides the infrastructure and expertise required to move fast without sacrificing accuracy or control.
Why Basic Support Isn’t Enough for Enterprise Deals
In large transactions, multiple stakeholders need access at different levels—legal teams, analysts, auditors, investors, and compliance officers. Each participant has unique requirements and permissions. Coordinating that complexity with a slow support desk or self-service tools is a recipe for confusion.
Many VDR providers still rely on:
- Email-only support queues
- Business-hours-only availability
- Limited onboarding help
- Little to no experience with regulated or sensitive transactions
By contrast, concierge-level VDR services offer real-time responsiveness and strategic guidance to ensure your workspace is optimized for speed and precision.
How Concierge Support Enhances the Deal Lifecycle
Here’s how expert VDR support directly improves outcomes at every stage of the transaction process:
1. Rapid Launch with Reduced Risk
A strong start can make all the difference. Instead of spending days or weeks configuring a workspace, concierge teams can handle setup on your behalf:
- Custom folder structures built to match your workflow
- Pre-assigned permission tiers for each stakeholder group
- Bulk file uploading and document import support
This gets your data room live quickly and minimizes the chance of permission errors that could expose confidential documents to the wrong eyes.
2. On-Demand Help When It Matters Most
During the peak of diligence, deal teams can’t afford to wait for answers. Whether it’s resolving an access issue, tagging documents for review, or troubleshooting file visibility, real-time support ensures your progress doesn’t stall.
Concierge support includes:
- Live response via phone or email
- Specialists trained in private equity, M&A, and cross-border deal complexity
- 24/7 availability when transactions require round-the-clock attention
When critical moments arise, immediate solutions can be the difference between closing and losing a deal.
3. Elevated Stakeholder Experience
For many investors and buyers, your data room is their first impression of your organization. A smooth, intuitive interface—and quick access to the right documents—speaks volumes about your professionalism.
With concierge support:
- Stakeholders are guided through onboarding
- Access challenges are handled proactively
- Corporate branding can be applied for a seamless experience
- FAQ and navigation aids can be built in to reduce confusion
These touches improve trust and help keep participants focused on the deal, not the platform.
4. Support for Security and Regulatory Compliance
Complex transactions often involve regulated data—financial disclosures, personal information, health records, and more. Maintaining compliance with data protection laws (like GDPR or HIPAA) is non-negotiable.
Concierge support teams can help:
- Configure user permissions aligned with compliance best practices
- Set up audit trails and activity tracking
- Apply security settings like dynamic watermarking and access expiration
This reduces the risk of non-compliance and ensures sensitive data stays protected throughout the deal.
Measurable ROI From Expert VDR Support
Concierge-level support isn’t just a value-add—it can directly impact the speed and success of your transaction. Benefits include:
- Faster onboarding and setup
- Fewer technical errors or stakeholder complaints
- Higher investor or acquirer engagement
- Smoother close processes and better buyer experiences
- Greater confidence in compliance and document control
Every saved hour, reduced error, or avoided delay compounds over the life of a high-value deal.
What Sets Leading Concierge Support Apart
Not all VDR support is created equal. The most effective concierge services provide:
- Dedicated account managers with experience in your industry
- Tailored onboarding for each new workspace
- Proactive assistance during critical transaction stages
- Integrated guidance on permissions, structure, and legal compliance
- Rapid-response help desks staffed by professionals—not generic agents
This type of support is designed for speed, accuracy, and reliability—exactly what’s required in the pressure-filled environment of modern dealmaking.
The Case for Concierge VDR Support in Strategic Transactions
When deals involve multiple parties, sensitive data, and tight timelines, execution matters more than ever. A virtual data room with concierge support provides the tools and expertise to move faster, collaborate more effectively, and protect your most valuable information at every stage.
From quick setup to ongoing assistance and compliance peace of mind, enterprise concierge support can transform a standard data room into a fully managed, strategic advantage.
Explore the featured posts and gain top strategies to enhance your business today.
- GENERAL2 months ago
5 Factors That Affect Tattoo Removal Success
- ENTERTAINMENT2 months ago
Exploring the Kristen Archives: A Treasure Trove of Erotica and More
- LIFESTYLE6 months ago
The Disciplinary Wives Club: Spanking for Love, Not Punishment
- TECHNOLOGY6 months ago
Blog Arcy Art: Where Architecture Meets Art
- ENTERTAINMENT7 months ago
The Ultimate Guide to Shillong Teer Hit Number: How to Predict Your Next Win
- LIFESTYLE2 weeks ago
Who Is Sandra Orlow?
- LIFESTYLE3 months ago
Berniece Julien: The Private Life of Tyson Beckford’s Partner
- Uncategorized1 year ago
Conrad Fisher Transformation: From Top Student to Troubled Soul