BUSINESS
Injection Molding Manufacturers
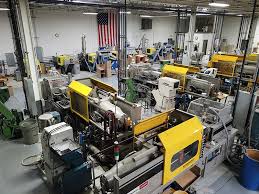
Injection molding manufacturers are pivotal in the modern manufacturing landscape, offering advanced solutions for producing high-quality, precision parts. Among the various types of injection molding, metal injection molding (MIM) stands out for its ability to create complex, high-strength components. Both plastic and metal injection molding companies are instrumental in driving innovation across industries, from automotive and aerospace to medical devices and consumer electronics.
The Role of Injection Molding Manufacturers
Injection molding manufacturers specialise in transforming raw materials into finished parts through the injection molding process. This method involves injecting molten material into a mold to form the desired shape. The process is highly versatile and efficient, making it suitable for mass production of parts with consistent quality and precision.
Manufacturers in this field cater to a wide range of industries, providing solutions for producing components that meet strict specifications. Their expertise in mold design, material selection, and process optimization ensures that each part meets the required standards for performance and durability.
Plastic Injection Molding: Versatility and Efficiency
Plastic injection molding is the most common form of injection molding, used extensively across various sectors. The process begins with the creation of a mold, typically made from steel or aluminium. The mold consists of two halves: the cavity side and the core side. These halves are designed to form the shape of the desired part.
The plastic injection molding process involves several key steps:
- Material Preparation: Plastic pellets are fed into a heated barrel, where they are melted into a molten state.
- Injection: The molten plastic is injected into the mold cavity under high pressure, ensuring it fills all cavities and details.
- Cooling: The material is allowed to cool and solidify within the mold.
- Ejection: Once cooled, the mold opens, and the finished part is ejected.
Plastic injection molding offers numerous advantages, including high precision, fast production cycles, and the ability to produce complex geometries. It is widely used for manufacturing parts such as automotive components, consumer electronics, packaging, and medical devices.
Metal Injection Molding (MIM): Combining Strength and Complexity
Metal injection molding (MIM) is a specialised form of injection molding that combines the versatility of plastic injection molding with the strength and durability of metal. MIM is particularly suitable for producing small, intricate metal parts that require high strength and precision.
The MIM process involves the following steps:
- Feedstock Preparation: A mixture of metal powders and a binder material is created to form a feedstock. The binder helps hold the metal powders together during the molding process.
- Injection Molding: The feedstock is injected into a mold cavity using the same principles as plastic injection molding.
- Debinding: The binder material is removed from the molded part, typically through a combination of thermal and chemical processes.
- Sintering: The debound part is heated to a high temperature in a controlled atmosphere, causing the metal particles to bond and form a solid, dense structure.
MIM offers several benefits, including the ability to produce complex shapes with high precision, excellent mechanical properties, and efficient material usage. It is widely used in industries such as aerospace, medical devices, automotive, and firearms.
Choosing the Right Injection Molding Manufacturer
Selecting the right injection molding manufacturer is crucial for ensuring the success of your project. Here are some key factors to consider when making your choice:
- Expertise and Experience: Look for manufacturers with a proven track record and extensive experience in your industry. Experienced companies are more likely to understand your unique requirements and deliver high-quality results.
- Technological Capabilities: Ensure the manufacturer has access to advanced injection molding technologies and equipment. This includes capabilities for both plastic and metal injection molding.
- Quality Assurance: Choose a manufacturer with robust quality control processes to ensure the parts meet your specifications and standards.
- Customer Service: Effective communication and collaboration are essential. Select a manufacturer that values customer service and is responsive to your needs.
- Cost and Lead Time: Consider the manufacturer’s pricing structure and ability to meet your project deadlines without compromising quality.
The Future of Injection Molding Manufacturers
As technology continues to advance, injection molding manufacturers are poised to play an increasingly important role in the manufacturing landscape. Innovations in materials, mold design, and automation will enhance the capabilities of these manufacturers, allowing for even more precise and efficient production.
For instance, the development of new materials with improved properties will expand the range of applications for both plastic and metal injection molding. Additionally, advancements in mold design and simulation software will enable manufacturers to create more complex and precise molds, further improving the quality and performance of the final parts.
Automation and Industry 4.0 technologies are also set to revolutionise the injection molding industry. Automated systems for material handling, molding, and quality control will increase efficiency and reduce costs. The integration of smart sensors and data analytics will enable real-time monitoring and optimization of the injection molding process, leading to improved consistency and reduced downtime.
Conclusion
Injection molding manufacturers, including both plastic and metal injection molding companies, are essential partners in the modern manufacturing process. Their expertise, advanced technologies, and commitment to quality ensure the production of high-precision, consistent parts across various industries. By collaborating with these manufacturers, companies can bring innovative products to market, driving progress and success in the competitive global market.
As the industry evolves, the synergy between plastic and metal injection molding will continue to drive innovation, enabling the creation of complex, high-performance components. With ongoing advancements in technology and materials, injection molding manufacturers will remain at the forefront of precision manufacturing, shaping the future of countless industries.
BUSINESS
Pikruos: Your Partner in Business Technology Solutions
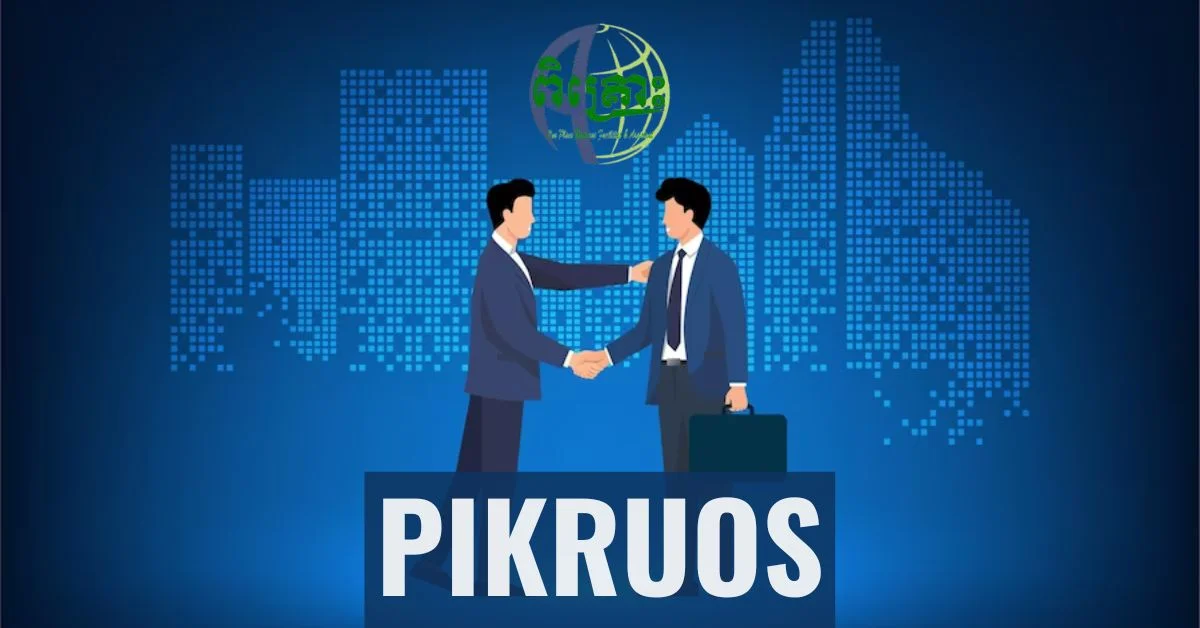
Introduction to Pikruos
In today’s fast-paced digital landscape, businesses are constantly seeking ways to improve efficiency and stay ahead of the competition. Enter Pikruos—a dynamic partner dedicated to delivering cutting-edge technology solutions tailored for your unique business needs. Whether you’re a start-up or an established enterprise, navigating the complex world of technology can be daunting. That’s where Pikruos shines, providing exceptional support that empowers your organization to thrive in a tech-driven environment. With innovative services designed to streamline operations and enhance productivity, it’s time to explore how partnering with Pikruos can transform your business journey.
The Importance of Technology Solutions in Business
In today’s fast-paced business landscape, technology solutions are no longer optional; they are essential. Companies rely on these tools to streamline operations and enhance productivity.
Effective technology solutions can automate tedious tasks, freeing up valuable time for teams to focus on strategic initiatives. This efficiency drives growth and innovation.
Moreover, the right tech can improve customer experiences. Businesses that embrace digital transformation often see a boost in engagement and satisfaction.
Data-driven insights enable firms to make informed decisions quickly. Organizations harnessing technology stay ahead of competitors by adapting swiftly to market changes.
Security is another crucial aspect. Robust technology solutions safeguard sensitive information against cyber threats, ensuring trust with clients and stakeholders alike.
Investing in effective business technologies paves the way for sustainable success in an ever-evolving environment. Adapting to these advancements keeps businesses agile and competitive.
Services Offered by Pikruos
Pikruos provides a diverse range of technology solutions tailored to meet the unique needs of businesses. From IT consulting to software development, every service is designed with efficiency in mind.
Their cloud services enable seamless data access and enhanced collaboration for teams. With robust security measures, Pikruos ensures that your information remains protected at all times.
Custom software solutions allow businesses to streamline operations effectively. Whether it’s a mobile app or an enterprise system, their innovative approach prioritizes user experience and functionality.
Additionally, Pikruos offers comprehensive support and maintenance services. This way, clients can focus on growth while knowing their technology infrastructure is well cared for.
With ongoing training and resources provided by experts, businesses are empowered to adapt swiftly in today’s fast-paced digital landscape. The commitment to customer satisfaction sets Pikruos apart as a true partner in business technology solutions.
Real World Examples of Pikruos’ Success
Pikruos has transformed businesses across various industries through innovative technology solutions. One notable case involved a mid-sized retail company struggling with inventory management. Pikruos implemented an advanced tracking system that streamlined operations, significantly reducing overstock and stockouts.
In another instance, a healthcare provider faced challenges in patient data handling. With Pikruos’ customized software solution, they enhanced data security while improving access for medical staff. This led to faster patient care and increased satisfaction rates.
Additionally, a startup in the tech sector benefited from Pikruos’ strategic consulting services. By optimizing their digital presence and automating workflows, they achieved impressive growth within months.
These examples illustrate how tailored technological interventions by Pikruos can drive efficiency and success for diverse organizations. Each story reflects their commitment to understanding unique business needs and delivering impactful results.
Why Choose Pikruos for Your Business Technology Needs?
Choosing Pikruos means investing in innovation and expertise. With a team of seasoned professionals, we deliver tailored solutions that align with your specific business goals.
Our commitment to quality sets us apart. We understand the unique challenges businesses face today and provide strategies that drive growth and efficiency.
Pikruos prioritizes customer satisfaction above all. Our collaborative approach ensures you are involved throughout the process, fostering transparency and trust.
We leverage cutting-edge technology to streamline operations. This not only boosts productivity but also enhances user experience across your organization.
When you partner with Pikruos, you’re choosing a long-term ally in navigating the complexities of modern business technology. We adapt to industry changes swiftly, ensuring your business remains competitive in an ever-evolving landscape.
Customer Testimonials and Reviews
Pikruos has garnered a multitude of positive reviews from satisfied clients who appreciate the company’s commitment to excellence. Customers often highlight the personalized approach taken by the team, ensuring that each solution is tailored specifically to their business needs.
One client shared how Pikruos transformed their outdated systems into streamlined processes, resulting in significant efficiency gains. This success story resonates with many who have experienced similar transformations.
Another testimonial praised Pikruos for its responsive customer support. Clients feel reassured knowing they can rely on expert assistance whenever challenges arise.
Many businesses value transparency and communication throughout projects. Feedback indicates that Pikruos excels in keeping stakeholders informed at every stage, fostering trust and collaboration.
Such endorsements showcase not just technical capability but also a genuine dedication to helping businesses thrive through innovative technology solutions.
Conclusion: Partnering with Pikruos for a Successful Future
Choosing Pikruos as your partner in business technology solutions can set your company on a path to success. With their extensive range of services tailored for various industries, they understand the unique challenges businesses face today. Their commitment to delivering effective technology solutions ensures that you stay ahead of the competition.
Customer testimonials highlight not just satisfaction but genuine transformations within organizations that have chosen Pikruos. The real-world examples demonstrate how businesses have thrived with the right technological support and guidance.
By collaborating with Pikruos, you’re not just opting for a service provider; you’re investing in a partnership focused on innovation and growth. This collaboration promises to equip your business with the tools necessary for navigating an ever-evolving digital landscape, ultimately leading towards lasting success.
FAQs
What is Pikruos?
Pikruos is a business technology solutions provider that offers tailored IT services such as software development, cloud solutions, consulting, and support to help businesses thrive in a digital-first world.
How does Pikruos’s help businesses improve efficiency?
Pikruos’s streamlines business operations by offering automation, secure data access, and custom software—freeing up time for strategic growth and innovation.
Which industries benefit most from Pikruos’s solutions?
Pikruos’s serves a wide range of industries including retail, healthcare, and tech startups—providing customized solutions to meet unique operational challenges.
What sets Pikruos’s apart from other IT service providers?
Pikruos’s stands out for its personalized approach, transparent collaboration, expert consulting, and long-term support that adapts with business needs.
Does Pikruos provide ongoing support and training?
Yes, Pikruos offers comprehensive maintenance and training to ensure clients can confidently manage their tech infrastructure and stay updated with the latest tools.
BUSINESS
Transforming Events with Complete Furniture Hire Solutions for Every Occasion
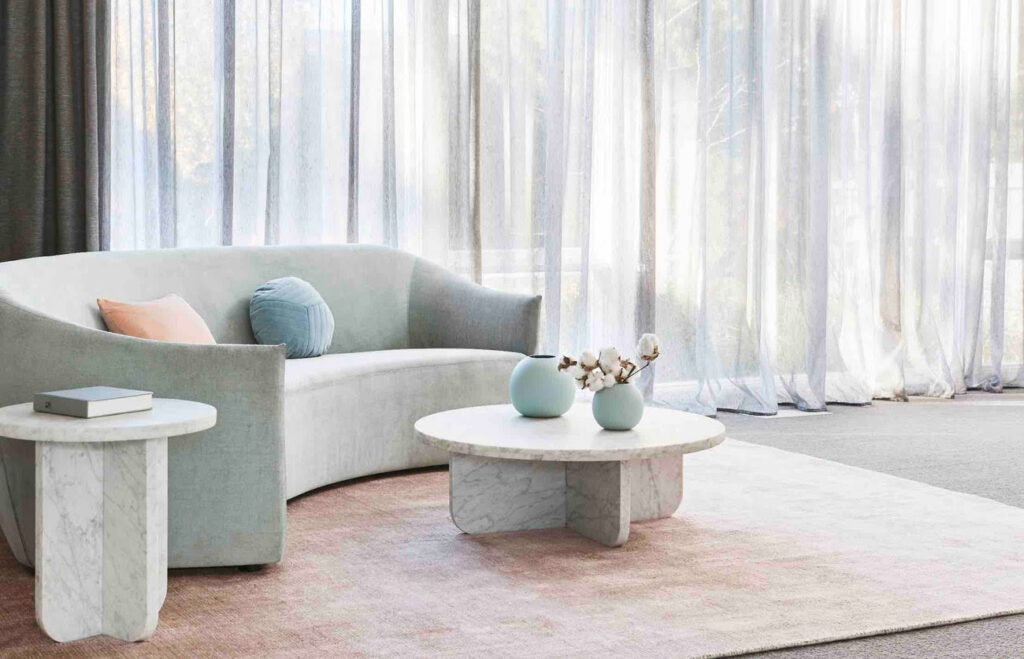
Planning an event, whether intimate or large-scale, requires careful attention to detail. From décor and lighting to food and entertainment, every aspect plays a role in creating the right atmosphere. Among these, event furniture is one of the most important elements that can make or break the overall experience for guests. The right chairs, tables, lounges, and décor items not only provide comfort but also set the tone and style of the occasion.
This is where complete furniture hire solutions for events big and small come in. By partnering with a professional event hire company like M Event Hire, you can access a wide variety of stylish, functional, and customizable furniture that perfectly matches your event’s theme and scale.
Why Furniture Hire is Essential for Events
No matter the type of gathering—be it a wedding, birthday celebration, gala dinner, or corporate function—the right furniture hire services can completely transform your venue. Here’s why:
- Enhances Guest Experience
Comfortable seating, elegant tables, and beautifully arranged lounges ensure your guests feel welcomed and valued. - Creates the Right Ambiance
Furniture contributes to the overall décor and vibe of the event. For instance, rustic wooden tables set a cozy tone, while sleek modern lounges create a chic, contemporary look. - Saves Time and Effort
Instead of worrying about sourcing, transporting, and setting up furniture, hiring experts means everything is delivered, installed, and packed away seamlessly. - Flexibility for All Event Sizes
Whether you’re hosting 20 people in a backyard or 500 guests at a grand venue, professional event hire companies can scale up or down depending on your needs.
Types of Event Furniture to Consider
Event hire services offer a wide range of furniture and accessories designed to suit all themes and occasions. Here are some popular options:
- Seating Solutions: Chiavari chairs, banquet chairs, bar stools, and lounge seating.
- Tables: Round banquet tables, cocktail tables, trestle tables, and coffee tables.
- Lounges & Sofas: Perfect for creating relaxed zones within your event.
- Outdoor Furniture: Benches, deck chairs, and marquees for outdoor gatherings.
- Décor Items: Lighting, table centerpieces, rugs, and decorative partitions.
By choosing complete furniture hire solutions for events big and small, you’ll have access to all of these elements in one place.
Benefits of Choosing M Event Hire
When planning an event in Australia, M Event Hire stands out as a trusted partner for providing top-quality furniture and event solutions. Here’s why:
- Wide Range of Options: From classic to modern designs, their extensive catalog caters to weddings, corporate events, festivals, and private parties.
- Affordable Packages: Hiring furniture is often more cost-effective than purchasing, especially for one-time events.
- Professional Setup: The team handles delivery, installation, and removal, saving you stress on the big day.
- Tailored Solutions: Whether it’s an intimate dinner or a large-scale event, they customize packages to suit your needs.
Event Trends: Furniture That Makes a Statement
Modern event styling is about more than just functionality; it’s about making a statement. Here are some trending furniture hire ideas:
- Mix-and-Match Seating: Combining different chair styles adds personality and flair.
- Rustic & Boho Chic: Timber tables paired with rattan lounges and earthy décor are trending for weddings and outdoor events.
- Luxury Lounges: Plush velvet lounges and ottomans create a VIP atmosphere at corporate and gala events.
- Sustainable Furniture: Eco-conscious choices like upcycled wood and reusable décor items are becoming increasingly popular.
With the right furniture hire solutions, you can bring any of these styles to life effortlessly.
Tips for Choosing the Right Furniture Hire Service
- Check the Inventory – Ensure the company has the specific furniture pieces you need.
- Read Reviews – Customer feedback can help you understand service quality.
- Consider Delivery & Setup – Always confirm logistics to avoid last-minute issues.
- Match Your Theme – Choose furniture that aligns with your event’s theme, colors, and style.
- Budget Wisely – Opt for complete hire packages that include setup, styling, and pickup for better value.
Final Thoughts
Event planning can feel overwhelming, but with the right support, it becomes a seamless and enjoyable process. Choosing complete furniture hire solutions for events big and small ensures that every detail of your celebration is covered—from stylish seating to decorative touches that impress your guests.
By partnering with experts like M Event Hire, you can focus on enjoying your special day while professionals handle the setup and styling. Whether it’s a wedding, corporate event, birthday, or festival, the right furniture hire company will help you transform your vision into reality
BUSINESS
Why Businesses Can’t Ignore AI-First SaaS Development in 2025
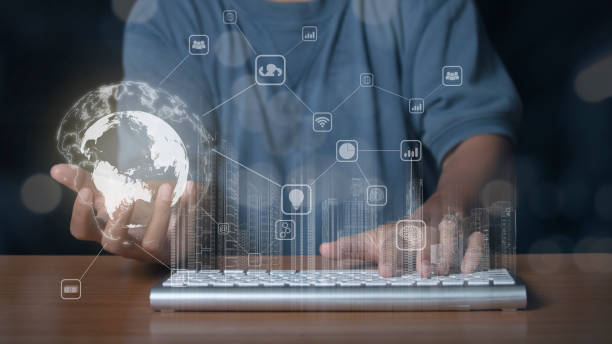
The year 2025 is the beginning of a new era in technology as companies are fast waking up to the effects of AI-first approaches in software development. One of the most important changes is the emergence of AI-first SaaS development, a trend which is reshaping the way organizations develop, deploy, and maintain digital tools. Rather than sticking to the conventional coding, companies are adopting the use of artificial intelligence as a way of making processes simple and cutting down time-to-market. This shift is not all about speed, it is about smarter, adaptive and cost effective solutions that are transforming the SaaS industry.
What is AI-First SaaS Development?
The AI-first SaaS development is the strategy of applying artificial intelligence as the basis of creating and enhancing software-as-a-service platforms. The AI-first development is in contrast to traditional coding, where developers manually enter all the functions; instead, creators can simply explain what they want to see and leave the solution to the AI. This is commonly known as vibe coding whereby the intent and aims are converted into working software.
Why AI-First SaaS Matters in 2025
By 2025, it is a competitive digital world that requires quicker, smarter and more dependable solutions. Businesses do not have the luxury to take months to come up with tools and only then get to the market. Using AI-first SaaS, companies are able to design, test, and deploy solutions within days or hours. This pace is coupled with the flexibility where companies can make immediate adjustments as the needs of the customers evolve. To the business, this translates to reduced risk, reduced costs and increased innovation.
Benefits of AI-First SaaS Development
Companies are not implementing AI-first SaaS because it is cool. The benefits are both tangible and quantifiable. With AI-first development, businesses can have:
- Quicker product development and shorter development cycles
- The reduced expenditure because of fewer manual codes and tests
- Enhanced flexibility to customer requirements
- Increased efficiency at the team level
- Streamlined processes that lessen the dependence on big IT staffs
Velzeno and the Shift Toward Smarter SaaS
Online platforms such as Velzeno show the ways in which businesses can experiment and integrate the appropriate digital tools in order to remain competitive in this era of AI. These platforms enable decision-makers to select SaaS solutions that can really drive growth through reviews, insights, and comparisons. It is not only developers that can take advantage of the AI-first SaaS, but also entrepreneurs, small businesses, and enterprises using smarter tools without requiring deep technical expertise.
Real-World Use Cases of AI-First SaaS
AI-first SaaS is already addressing practical problems across a variety of industries. It is used by startups to develop minimum viable products at a blistering pace, minimizing the risks and costs of starting up new ventures. AI-first SaaS tools allow small businesses to automate workflow, customer relationship management and even content creation. Giant companies are reducing their dependence on IT departments by letting automation tools driven by AI handle routine and elaborate tasks. These practical examples demonstrate that AI-first SaaS is not a theory anymore; it is changing operations all around.
Challenges of AI-First SaaS Development
Although the opportunities are huge, AI-first SaaS is not problem-free. Companies need to take into consideration:
- Sometimes AI fails to interpret the intent of the user correctly
- Security and compliance issues Data security and compliance issues
- The necessity of human control in the key decisions
- Restrictions in very complex or specialized enterprise solutions
The above challenges point to the relevance of planning well when implementing AI-first SaaS. To get the optimal outcomes, companies should balance automation and human experience.
The Future of SaaS in 2025 and Beyond
In the future, AI-first SaaS is set to expand further as additional companies realize the benefits of taking this direction. Developers will no longer write manual code but will direct AI in clear intention. Companies adopting AI-first will most probably perform better compared to those still stuck with the old development. The future of SaaS will be in the hands of businesses that can innovate using AI as the central element of their strategies, with increased speed, reduced costs and smarter automation.
Conclusion
AI-first SaaS development in 2025 is not just a trend. It is a metamorphosis that companies cannot overlook. The establishment of AI-first practices such as vibe coding is not only accelerating the development process but also producing tools that are more responsive to the needs of customers. Social media like Velzeno are making this transition easier by giving businesses reliable information about digital tools. The SaaS environment is changing, and those who adopt AI-first solutions today will be the victors that create smarter, more efficient systems in the future.
- GENERAL1 month ago
5 Factors That Affect Tattoo Removal Success
- ENTERTAINMENT2 months ago
Exploring the Kristen Archives: A Treasure Trove of Erotica and More
- LIFESTYLE6 months ago
The Disciplinary Wives Club: Spanking for Love, Not Punishment
- TECHNOLOGY5 months ago
Blog Arcy Art: Where Architecture Meets Art
- LIFESTYLE3 days ago
Who Is Sandra Orlow?
- ENTERTAINMENT7 months ago
The Ultimate Guide to Shillong Teer Hit Number: How to Predict Your Next Win
- LIFESTYLE3 months ago
Berniece Julien: The Private Life of Tyson Beckford’s Partner
- Uncategorized12 months ago
Conrad Fisher Transformation: From Top Student to Troubled Soul