HOME IMPROVEMENT
Insulation Beyond Buildings: Exploring Specialized Products for Industrial and Automotive Applications
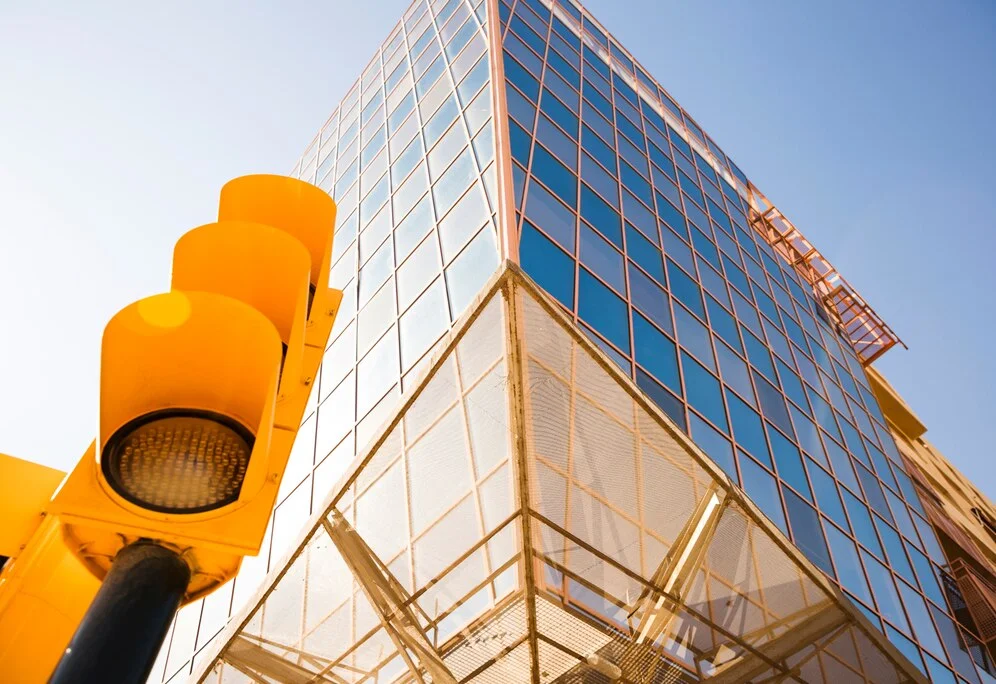
Insulation is most commonly associated with keeping buildings warm in winter and cool in summer. However, insulation has many critical uses beyond the walls of homes and offices. Specialized insulation products play essential roles in transportation, shipping, energy, manufacturing, and other industrial sectors.
This article will provide an overview of key insulation types used in non-building applications and explain how they meet the demanding performance requirements of sectors like automotive, marine shipping, oil and gas, power generation, and cryogenic storage.
Insulating the Open Road: Automotive Sector Relies on Advanced Materials
Creating an efficient and comfortable driving experience is no easy task – vehicles must maintain safe operating temperatures across a wide variety of grueling conditions, from the cold of winter to the heat of summer and everything in between. Insulation and insulating techniques are critical to achieving this balance.
Insulation helps automakers reduce noise from the engine and road, prevent condensation on cold surfaces, protect passengers from high exhaust temperatures, and stabilize temperatures around sensitive electronics. Materials like fiberglass mats, molded foam parts, multi-layer heat shields, and woven textile wraps are strategically placed throughout the vehicle.
Newer electric vehicles have their own unique insulation needs around battery packs and power control systems. Insulation helps maintain optimum battery temperature to maximize range and prevent overheating. As automotive design and technology continues advancing rapidly in coming years, high performance insulation will remain a key enabler.
Shipping Solutions: Battling Condensation and Extending Shelf Life
Effective insulation is mandatory for refrigerated shipping containers transporting perishable goods like produce, meat, dairy and pharmaceuticals across seas and highways. Preventing condensation build-up and maintaining a stable cold chain environment ensures products arrive safely at their destination.
Shipping containers and trucks designed for refrigeration use foam and foil-based insulation panels featuring water-resistant coatings. Desiccants are also added to actively absorb condensation. Logistics teams carefully monitor the insulation’s performance using hanging temperature probes, wireless sensors on external walls and other smart tracking methods.
Insulated containers also see heavy usage beyond cold chain logistics. Companies commonly use them to ship temperature-sensitive bulk liquids like certain chemicals, waste oils or tank cleaning fluids. Ventilated insulation panels help stabilize the enclosed environment.
Oil Flows Freely: Pipe Insulation Crucial for Energy Sector
Whether carrying crude oil from wellheads or refined products to terminals, insulation is indispensable for maintaining energy pipeline integrity and efficiency. Keeping fluids warm in pipelines prevents freezing, wax or hydrate formation that can completely block flow. Insulation also preserves product quality by minimizing stratification and separation issues.
Common insulation solutions for pipelines include polyurethane foam coverings or customizable jacketing made from weather-resistant fabrics. Hybrid methods are popular as well, combining multiple materials to optimize thermal performance and ruggedness. Proper installation procedures performed by skilled tradesmen are vital for preventing corrosion under insulation.
Pipelines that run above ground or through cold climate regions often use heating systems to maintain temperatures, relying on robust insulation to retain warmth. Heated pipelines require both a protective outer layer resistant to crushing loads as well as an insulation barrier to lock in heat. Load-bearing insulation replaces concrete weights in many above-ground applications.
Turbine Insulation: Withstanding Extreme Forces
The turbine is the powerhouse of most electricity generation plants. Turbine insulation protects operators, improves performance and prevents system failures in challenging operating environments.
Insulation panels around turbines must tolerate vibrational forces, temperature swings ranging from -70°C to over 500°C and possible contact with oils or steam. High-density materials like compacted vermiculite boards and flexible thermal blankets meet these demands. Carefully sealing joints and openings preserves insulation integrity.
Coatings are often applied to turbine insulation to resist heat absorption. Some advanced ceramic coatings even reflect a significant portion of heat. Proper insulation is particularly critical for gas turbines, as maintaining proper operating temperatures enables high fuel efficiency. Routine inspection and maintenance of insulation ensures it performs as designed over decades of operation.
Liquid Air: Cryogenic Storage Requires Specialized Materials
Storing industrial gases at extremely low temperatures – down to -270°C for liquid oxygen – requires insulation technology outside traditional realms. Refrigerated liquid air storage maintains gases in a dense liquid state, conserving space compared to bulky compressed gas cylinders.
Cryogenic insulation must almost fully block external heat transfer while remaining ductile enough to shrink and expand alongside intense temperature fluctuations. Foam, fiberglass and vacuum-insulated panels combine with supplemental insulation layers for achieving high performance. Protective coatings guard insulation against moisture intrusion while preventing atmospheric oxygen and nitrogen liquefaction on cold surfaces.
High-performance insulation allows liquid air vessels to maintain internal environments with negligible heat leakage. This capability enables indefinite storage periods, so gases remain available for medical facilities, manufacturers, aerospace and other end users.
The Future of Insulation: Automation and Aerogels
While traditional insulation materials like wool, foam and mineral fibers still dominate industrial uses, innovations emerge constantly to push thermal efficiency higher. Two promising developments on the horizon are automated insulation processes and next-generation aerogel compounds boasting extreme lightness and low conductivity.
Automating aspects like applying insulation jacketing, scanning for defects, and predicting repair needs through sensors and AI analysis will accelerate maintenance workflows. Aerogels made from silica, carbon nanotubes and other substances underline high costs presently but exhibit major potential for creating lighter insulation solutions. Even NASA relies on aerogel advances to handle extreme cold during space exploration missions.
Final words
This overview of specialized insulation only scratches the surface of this often-overlooked industry changing lives daily through enabling reliable electricity, accessible food supply chains, fuel transportation networks, lifesaving medical gases and comfortable automotive travel. As global energy demands, and engineering capabilities grow more complex, high-performance insulation will remain a hidden necessity across infrastructure sectors. Pushing thermal conductivity lower through both legacy and emerging materials ensures insulation’s essential role for decades to come.
HOME IMPROVEMENT
Rental Scams in the US: Tips for Immigrants to Stay Safe
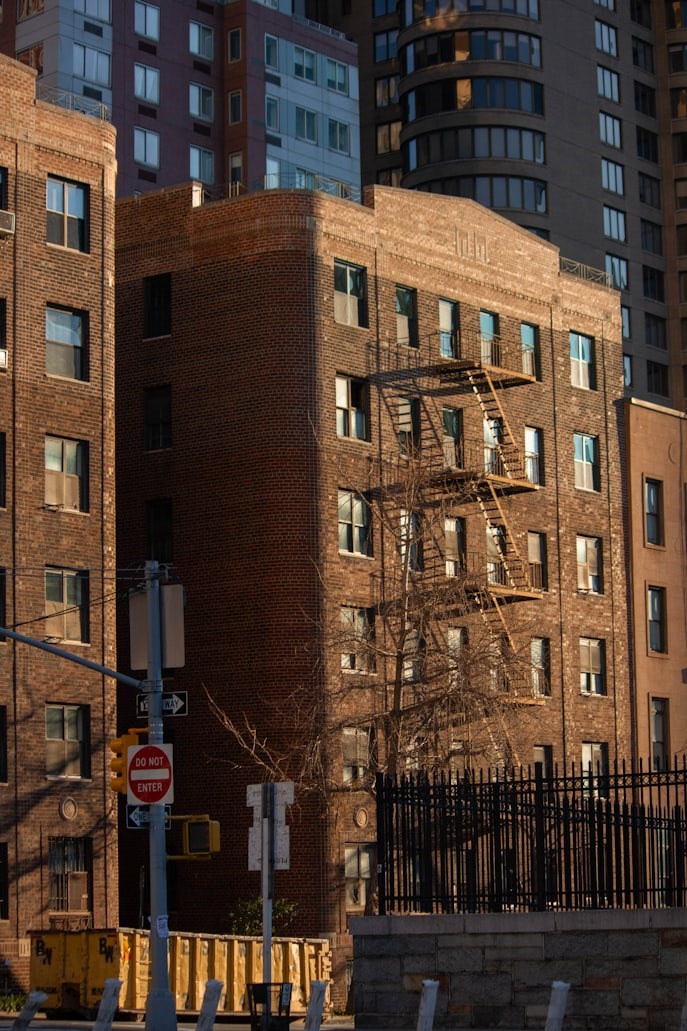
The US is one of the most popular countries in the world for immigration. Every day, hundreds of people arrive in the USА in search of a new life or self-fulfillment, and a significant number of them come from the former Soviet Union. Many Ukrainians and Georgians who arrive in America are exposed to a large number of risks and threats, including fraud. It comes in many forms, but a particularly painful problem is the increasing incidence of fraud when renting housing, when our compatriots, so to speak, are deceived and deprived of their funds from their very first steps in the US.
Tips for Avoiding Problems When Renting
As in their own countries, Ukrainians and Georgians may encounter common scams, including fake ads, fake landlords, and unofficial agreements. As we know, scammers use similar approaches in our countries, but when arriving in the US, our compatriots believe that they are safer here and that there is no need to be as vigilant as they are at home. However, to their disappointment, they discover that they can encounter the same problems here.
New immigrants face language barriers, lack of credit history, and unfamiliarity with local laws, all of which make them very vulnerable, which scammers take advantage of. Don’t want to find yourself in a similar situation? Then use reliable resources like Tbilistings, where they will help you find safe housing and take your first steps in the US.
Scammers often post attractive ads with low prices and very beautiful photos, which should already raise suspicion at this stage. But when you contact them and try to rent the property, they ask for a prepayment. Without thinking about the risks and making the payment, you may soon discover that there is no housing at all, the photos are taken from a completely different property, and the scammer’s phone number is no longer available. Often, scammers pretend to be the owners of the apartment, while having no connection to the property. Even if the property is real, you are asked to pay a deposit to reserve it, and then they disappear.
A common technique used by scammers is urgency, which they use to pressure the applicant, forcing them to act rashly and quickly, to pay money in advance so that the property is not taken by someone else. In the end, you may find that, as in previous cases, there is no housing, or the scammer has no connection to it, being neither the owner of the housing nor even a real estate agent.
HOME IMPROVEMENT
Why LED Lamps Are a Must-Have for Every Manicure Master – Ulka Global Guide
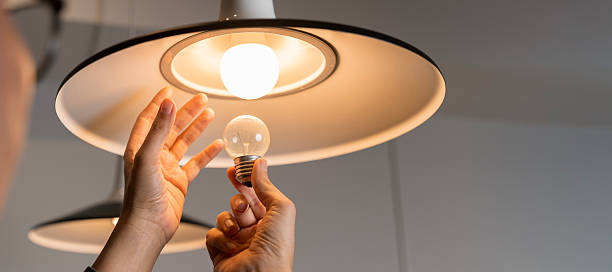
In the professional nail industry, quality tools make all the difference. One of the most essential devices for any nail technician is the LED lamp. Whether you’re working in a high-end salon or offering mobile services, the right lamp can greatly impact your results and efficiency. At Ulka Global, we specialize in manufacturing professional manicure equipment, including LED lamps designed to meet the highest standards of performance, safety, and reliability.
What Are LED Lamps for Manicures?
A LED lamp for manicure is a specialized device used to cure (harden) gel polish, gel extensions, or other light-reactive nail products. Unlike traditional UV lamps, LED lamps use advanced light-emitting diodes that cure gel faster, more efficiently, and with less energy consumption.
Our range of Ulka Global LED lamps combines cutting-edge technology with sleek design, ensuring that nail masters have a reliable tool to deliver perfect results every time.
Why Are LED Lamps So Important?
- Faster Curing Time
One of the biggest advantages of LED lamps is their speed. They cure gel polish in just 30–60 seconds, compared to 2–3 minutes for older UV lamps. This means quicker services, more clients, and higher productivity for busy nail technicians. - Better Results and Long-Lasting Manicures
With the right LED lamp, gel polish cures evenly and thoroughly, ensuring a durable, chip-resistant finish. This enhances the quality of your work and keeps your clients coming back. - Energy-Efficient and Long-Lasting
LED bulbs consume less energy and have a much longer lifespan than traditional UV bulbs—often up to 50,000 hours. That means fewer replacements and lower maintenance costs over time. - Safe and Gentle on Skin
Ulka Global LED lamps emit a narrow light spectrum, which reduces unnecessary UV exposure. This makes them a safer choice for both clients and technicians, especially during repeated use throughout the day. - Professional Appearance and Comfort
A well-designed lamp adds to your salon’s professional image. Our LED lamps feature modern, ergonomic designs that are comfortable for both clients and nail masters. Spacious interiors and open designs accommodate all hand sizes and reduce awkward positioning during curing. - Versatility
Ulka Global LED lamps support a wide range of gel products—gel polish, builder gels, rubber bases, top coats, and more. With multiple curing modes and timers, our lamps give you full control over each step of the manicure process.
Why Choose Ulka Global LED Lamps?
At Ulka Global, we engineer our lamps for daily professional use, focusing on durability, performance, and style. Our manicure LED lamps offer:
- High power output for ultra-fast curing
- Motion sensors and intelligent timers for convenience
- Cool light technology to minimize heat spikes
- Stylish, minimalist designs that elevate any workspace
- Compatibility with all gel systems used in modern salons
We understand the needs of nail artists because we design our tools for professionals who demand reliability and efficiency.
A high-quality LED lamp is a cornerstone of any successful nail studio. It affects not only the curing process but also the overall speed, safety, and satisfaction of your services. At Ulka Global, we’re committed to helping manicure masters deliver their best work with equipment that performs as hard as they do.
HOME IMPROVEMENT
10 Inspiring Vacation Home Design Ideas for Your Perfect Getaway
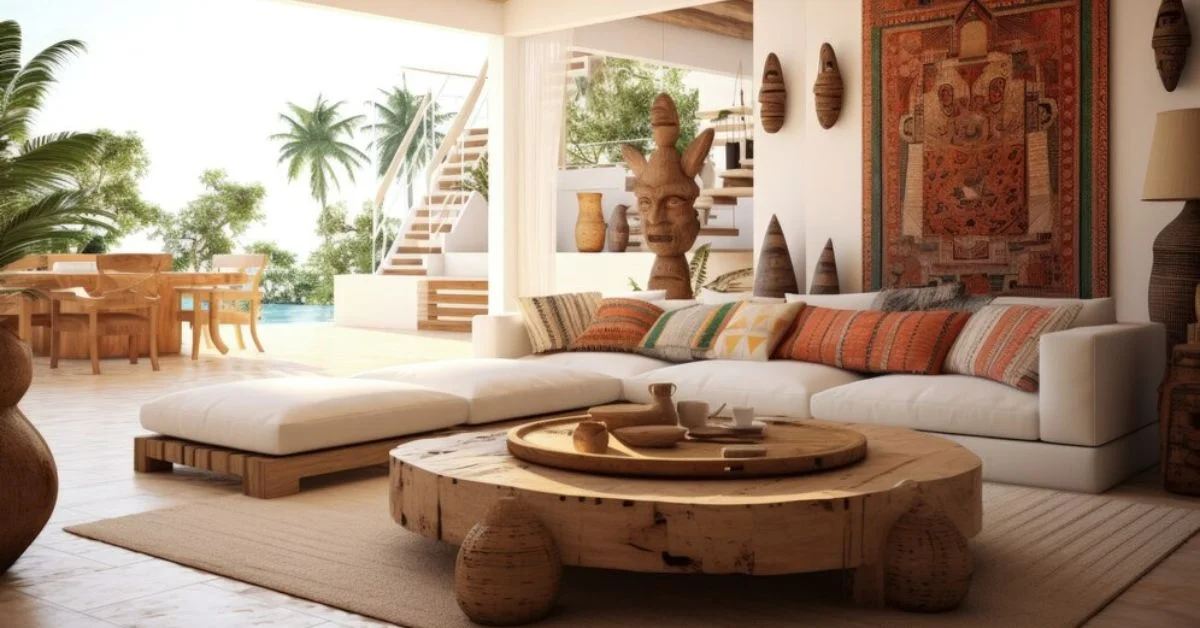
Are you dreaming of your vacation home? A place where you can escape the hustle and bustle of everyday life and relax in a tranquil, serene environment? Designing your vacation home is an exciting journey, allowing you to create a space perfectly tailored to your tastes and needs. Whether you’re envisioning a cozy mountain retreat, a breezy coastal getaway, or a rustic cabin in the woods, here are ten inspiring vacation home design ideas to help you create your perfect escape.
1. Embrace Natural Light
Incorporating natural light into your vacation home design can transform the space, making it feel bright, airy, and welcoming. Large windows, skylights, and glass doors allow natural light to flood the interior, creating a seamless connection with the surrounding landscape. Position seating areas, dining spaces, and relaxation zones to take advantage of the natural light and stunning views.
2. Create an Outdoor Oasis
Whether you own a beach house, a mountain retreat, or a lakeside cabin, maximizing the outdoor space to create an oasis will allow you to fully appreciate your vacation home’s unique location. A great way to elevate your outdoor environment and create a soothing ambiance is by incorporating a water fountain design. The sound of flowing water can instantly calm the mind and soothe the body, making it the perfect addition to your outdoor oasis.
Whether you choose a small tabletop fountain or a grand waterfall, the serene sound and beauty of the water will enhance your overall experience. Combine this with comfortable seating, inviting dining areas, and one of our favorite amenities – a hot tub or fire pit, and you’ll have a personal paradise ready for you to relax and unwind.
3. Open Floor Plan
An open floor plan can enhance the sense of space and flow in your vacation home. By combining the kitchen, living, and dining areas into one cohesive space, you can create an inviting environment that encourages socializing and relaxation. Incorporate high ceilings, exposed beams, and natural materials to add warmth and character to the interior while maintaining a sense of openness.
4. Cozy Fireplace
A cozy fireplace is a must-have feature for any vacation home, adding warmth, charm, and ambiance to the space. Whether you prefer a traditional wood-burning fireplace, a gas insert, or a modern ethanol burner, a fireplace can become the focal point of your living area. Surround the fireplace with comfortable seating, plush rugs, and built-in shelving to create a cozy nook where you can curl up with a good book or enjoy intimate conversations.
5. Rustic Charm
Embrace the rustic charm of your vacation home’s surroundings by incorporating natural materials and textures into your design. Exposed wood beams, stone accents, and reclaimed wood flooring can add warmth and character to the interior, while rustic furniture, cozy textiles, and vintage décor create a welcoming and relaxed atmosphere.
Pay homage to the local environment by incorporating design elements inspired by the surrounding landscape, such as nautical accents for a coastal retreat or log cabin-inspired details for a mountain getaway.
6. Serene Bedroom Retreats
Design serene and restful bedroom retreats where you can relax and recharge after a day of adventure. Choose a soothing color palette, luxurious bedding, and plush pillows to create a comfortable and inviting space.
Maximize storage with built-in closets, dressers, and bedside tables to keep the room clutter-free. Consider incorporating large windows or a private balcony to take advantage of the views and natural light, creating a tranquil sanctuary where you can rest and rejuvenate.
7. Gourmet Kitchen
Design a gourmet kitchen where you can unleash your inner chef and prepare delicious meals for family and friends. Opt for high-quality appliances, durable countertops, and ample storage to make cooking and entertaining a breeze.
Consider incorporating a large island or breakfast bar, providing additional workspace and seating for casual dining. Enhance the kitchen’s functionality and style with custom cabinetry, under-cabinet lighting, and stylish hardware, creating a space that’s as beautiful as it is practical.
8. Spa-Inspired Bathroom
Create a spa-inspired bathroom where you can pamper yourself and indulge in relaxation. Incorporate luxurious features such as a soaking tub, walk-in shower, and double vanity, providing the ultimate in comfort and convenience.
Choose natural materials, such as stone, marble, and wood, to create a serene and sophisticated atmosphere. Add finishing touches such as plush towels, soft lighting, and scented candles to evoke the feeling of a luxurious retreat.
9. Entertainment Zone
Design an entertainment zone where you can gather with family and friends to enjoy games, movies, and quality time together. Create a dedicated space with comfortable seating, a large-screen TV, and a selection of games and activities to keep everyone entertained. Consider incorporating a wet bar, mini-fridge, or popcorn machine to enhance the experience, providing everything you need for a fun and memorable vacation.
10. Personal Touches
Finally, don’t forget to add personal touches that reflect your unique style and personality. Whether it’s family photos, cherished artwork, or souvenirs from your travels, incorporating personal items into your vacation home design can make it feel truly special and one-of-a-kind. Take inspiration from the local culture, landscape, and architecture, infusing your vacation home with elements that speak to your passions and interests.
In Conclusion
Designing your vacation home is an exciting opportunity to create a space that reflects your lifestyle, tastes, and aspirations. By incorporating these ten inspiring design ideas, you can create the perfect getaway where you can relax, recharge, and make lasting memories with family and friends. Whether you’re seeking a cozy mountain retreat, a breezy coastal getaway, or a rustic cabin in the woods, let these ideas inspire you to create your dream vacation home.
- GENERAL2 months ago
5 Factors That Affect Tattoo Removal Success
- ENTERTAINMENT2 months ago
Exploring the Kristen Archives: A Treasure Trove of Erotica and More
- LIFESTYLE6 months ago
The Disciplinary Wives Club: Spanking for Love, Not Punishment
- TECHNOLOGY6 months ago
Blog Arcy Art: Where Architecture Meets Art
- ENTERTAINMENT7 months ago
The Ultimate Guide to Shillong Teer Hit Number: How to Predict Your Next Win
- LIFESTYLE2 weeks ago
Who Is Sandra Orlow?
- LIFESTYLE3 months ago
Berniece Julien: The Private Life of Tyson Beckford’s Partner
- Uncategorized1 year ago
Conrad Fisher Transformation: From Top Student to Troubled Soul