BUSINESS
Maximizing Efficiency: Top Warehouse Optimization Techniques for Better Space Utilization
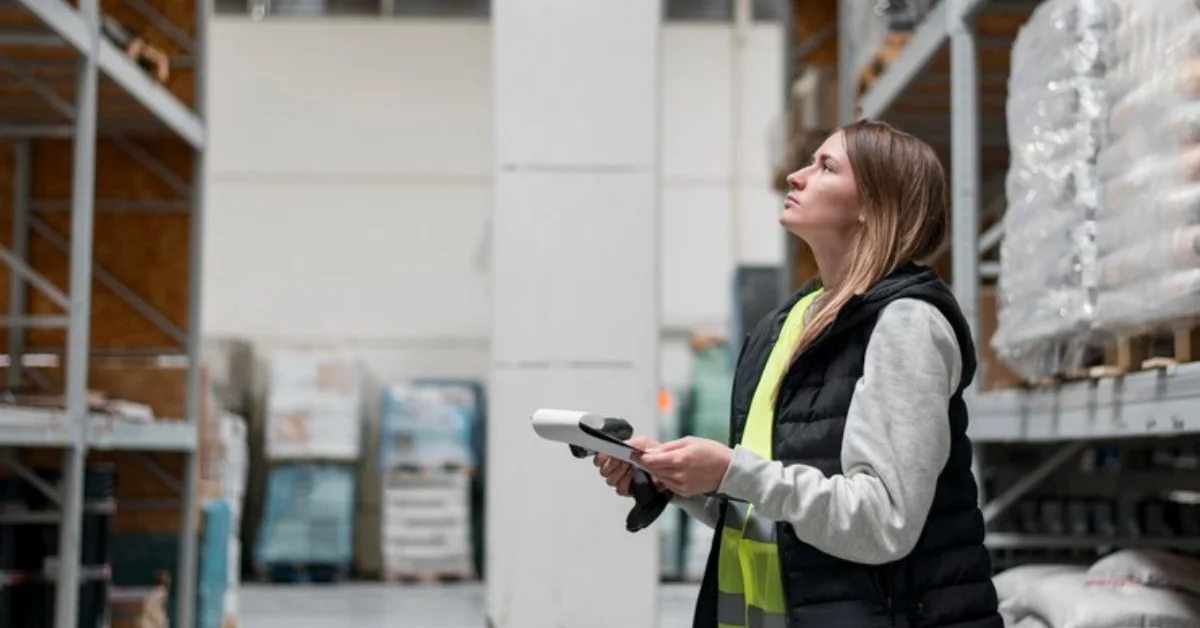
In today’s fast-paced world, where every second counts and space is at a premium, optimizing your warehouse isn’t just a luxury—it’s a necessity. Imagine transforming your cluttered aisles into streamlined pathways that enhance workflow and boost productivity dramatically. Welcome to the future of warehousing! In this blog post, we’ll explore innovative techniques that not only maximize efficiency but also revolutionize how you utilize every square foot of your storage space. Whether you’re managing a bustling distribution center or a cozy retail stockroom, these top strategies will empower you to unlock hidden potential within your operations. Get ready to dive in and discover how smart optimization can lead to remarkable gains in both organization and profitability!
Introduction to Warehouse Optimization
The warehouse is the heartbeat of many businesses, serving as a vital link between suppliers and customers. In an age where efficiency can make or break success, optimizing your warehouse space has never been more crucial. With increasing demands for faster delivery times and lower operational costs, effective space utilization can lead to significant advantages.
Imagine transforming cluttered aisles into streamlined pathways that enhance productivity. Picture maximizing every inch of vertical storage while ensuring easy access to inventory. This isn’t just a dream; it’s entirely possible with the right techniques in place. Let’s dive into the world of warehouse optimization and discover how you can unlock new levels of efficiency!
Importance of Space Utilization in Warehouses
Effective space utilization in warehouses is crucial for operational efficiency. With rising demand and limited real estate, maximizing every square foot can significantly impact profitability.
When warehouse space is optimized, companies can store more products without the need for additional facilities. This means lower overhead costs and increased revenue potential.
Moreover, well-utilized spaces enhance workflow. Employees can navigate easily, reducing time spent searching for items or moving stock around. Increased efficiency leads to faster order fulfillment and improved customer satisfaction.
Additionally, optimal space usage contributes to safety standards within warehouses. Less clutter reduces hazards, ensuring a safer working environment for all staff members.
Common Challenges Faced in Warehouse Space Utilization
Warehouses often grapple with inefficient space utilization. One major challenge is poor inventory organization. When items are scattered without a logical system, it leads to wasted time searching for products.
Another issue stems from outdated layouts. As businesses evolve, spaces may no longer meet current needs. This mismatch can result in underused areas or congested pathways.
Additionally, fluctuating demand complicates storage strategies. Seasonal variations can leave warehouses overstocked or understocked, straining available space.
Employee training also plays a role. Without proper guidance on best practices, workers may inadvertently contribute to disorganization and inefficiencies.
Lastly, inadequate technology integration hampers performance. Relying on manual processes slows operations and limits visibility into inventory levels and locations. Each of these challenges requires targeted solutions for better efficiency in warehouse management.
Top Warehouse Optimization Techniques:
Efficiency in warehouse operations hinges on smart optimization techniques. Implementing proper inventory management is crucial. This ensures that stock levels are accurate and helps avoid overstocking or stockouts.
Utilizing vertical space can significantly increase storage capacity. Racking systems allow for the stacking of items, making use of overhead areas that would otherwise go unused.
A slotting system enhances picking efficiency by organizing products based on their demand frequency and size. This minimizes travel time for workers during order fulfillment.
– Proper Inventory Management
Proper inventory management is the backbone of an efficient warehouse. It ensures that you know exactly what you have on hand and where it’s located. This visibility prevents overstocking and stockouts, both of which can be costly.
Utilizing software solutions for tracking inventory can simplify this process significantly. These tools allow real-time updates and streamline order processing. You gain insights into trends, helping to forecast demand.
Another important aspect is regular audits. Conducting frequent checks keeps your records accurate and identifies discrepancies early on. This proactive approach minimizes errors.
Incorporating barcode systems further enhances efficiency by speeding up the picking process. Scanning items reduces human error while saving time during inventory counts.
– Utilizing Vertical Space with Racking Systems
Maximizing vertical space is a game changer in warehouse optimization. Racking systems allow businesses to take advantage of the often-overlooked height of their facilities.
By installing tall racks, you can significantly increase your storage capacity without needing more floor space. This means more products stored securely and accessible.
Different types of racking systems cater to various needs—selective, drive-in, or pallet flow racking each offer unique benefits depending on your inventory type and turnover rate.
Implementing these solutions not only enhances organization but also improves picking efficiency. Warehouse staff can navigate aisles easily when items are organized vertically.
Additionally, investing in adjustable shelving helps accommodate changing inventory sizes over time. Flexibility is crucial for adapting to market demands while maintaining an efficient layout.
– Implementing a Slotting System
Implementing a slotting system can transform your warehouse efficiency dramatically. This technique involves strategically assigning products to specific locations based on their demand and characteristics.
Start by analyzing sales data to identify high-velocity items. These should be placed closer to packing areas for quicker access. Meanwhile, slower-moving inventory can occupy less accessible spaces without hindering operations.
Consider the shape and size of your products as you develop the layout. Group similar items together to streamline picking processes and reduce travel time for workers.
Regularly review and adjust your slotting strategy as trends shift or new products are introduced. Flexibility is key in maintaining an effective system that adapts to changing demands.
– Just-in-Time (JIT) Inventory Management
Just-in-Time (JIT) inventory management is a strategy designed to minimize waste and increase efficiency. By receiving goods only when they are needed in the production process, businesses can significantly reduce storage costs.
This approach requires precise planning and strong supplier relationships. Companies must forecast demand accurately to ensure that materials arrive exactly when required without delays or excess stock.
The benefits extend beyond cost reduction. JIT enhances flexibility, allowing warehouses to adapt quickly to market changes. It also improves cash flow since funds aren’t tied up in surplus inventory.
Conclusion:
Optimizing warehouse space can lead to significant improvements in efficiency and productivity. When warehouses utilize their available space effectively, they not only reduce costs but also enhance order accuracy and speed. This ultimately leads to greater customer satisfaction.
Getting started with warehouse optimization doesn’t have to be overwhelming. Identify areas where you can implement the techniques discussed earlier—like proper inventory management or utilizing vertical space with racking systems. Consider leveraging technology tools that aid in monitoring your storage capabilities and tracking inventory levels.
Regular assessments of your current setup will help pinpoint any inefficiencies that need addressing. Engage your team in brainstorming sessions for innovative ideas on improving workflows and maximizing every inch of your facility.
BUSINESS
Top 10 Tips for Choosing Reliable Moving Services in Washington DC
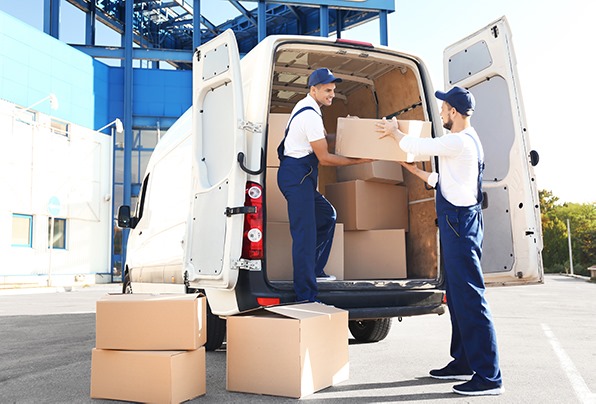
Planning a move in the nation’s capital can feel overwhelming, especially when it comes to choosing the right movers. With so many companies offering moving services Washington DC, it’s essential to know what to look for to ensure your belongings are handled with care and professionalism. Below are ten practical tips that will help you make the best decision for a smooth and stress-free move.
1. Check Licensing and Insurance
The first step in choosing a reliable moving company is to confirm that they are properly licensed and insured. Legitimate movers must follow federal and state regulations, and having insurance guarantees that your belongings are covered in case of damage or loss. Always ask for proof of licensing and insurance before signing any contract.
2. Read Reviews and Testimonials
Customer experiences can give you valuable insights into a moving company’s reliability. Browse online reviews, testimonials, and ratings on trusted platforms. Pay attention to how the company responds to complaints—it shows their level of professionalism and commitment to resolving issues.
3. Get Multiple Quotes
Don’t settle for the first moving company you contact. Request at least three estimates from different providers. Compare the services included, overall pricing, and any extra fees. Be cautious of quotes that are unusually low, as they may indicate hidden charges or poor service quality.
4. Ask About Experience in Washington DC
Washington DC has unique challenges, including heavy traffic, narrow streets, and strict building regulations. A company with local experience knows how to navigate these obstacles efficiently. Ask how long they’ve been serving the DC area and whether they have handled moves similar to yours.
5. Understand the Services Offered
Not all moving companies provide the same services. Some offer full-service moving with packing, storage, and unpacking options, while others handle only transportation. Clarify what’s included in your package and whether there are additional costs for packing materials or special items like pianos or antiques.
6. Verify Professionalism and Equipment
Reliable movers should arrive with clean, well-maintained trucks and professional moving equipment. Staff should be polite, uniformed, and trained in handling items safely. Professional presentation often reflects the quality of service you can expect throughout your move.
7. Ask About Estimates and Contracts
Make sure your moving company provides a written estimate. Ask whether it’s binding or non-binding, and read the contract carefully to avoid surprises. A reliable mover will explain the terms clearly and give you documentation that protects both parties.
8. Look for Transparent Communication
Clear communication is one of the hallmarks of a trustworthy moving service. The company should answer your questions promptly, explain their policies, and give you realistic timelines. If you find it difficult to get straight answers, consider it a red flag.
9. Check for Hidden Fees
Some movers may charge extra for stairs, long carries, or heavy items. Before signing a contract, ask about potential hidden fees to avoid unexpected costs on moving day. Transparency in pricing is a sign of a trustworthy company.
10. Trust Your Instincts
Finally, trust your intuition. If something doesn’t feel right—whether it’s unprofessional behavior, vague answers, or a lack of transparency—it’s better to walk away. A reliable moving company will give you peace of mind, not additional stress.
Conclusion
Finding the right moving service in Washington DC takes research, comparison, and careful consideration. By checking credentials, reading reviews, and asking the right questions, you can choose movers who will handle your belongings safely and efficiently. Use these ten tips to guide your search and ensure a smooth transition to your new home.
BUSINESS
Pikruos: Your Partner in Business Technology Solutions
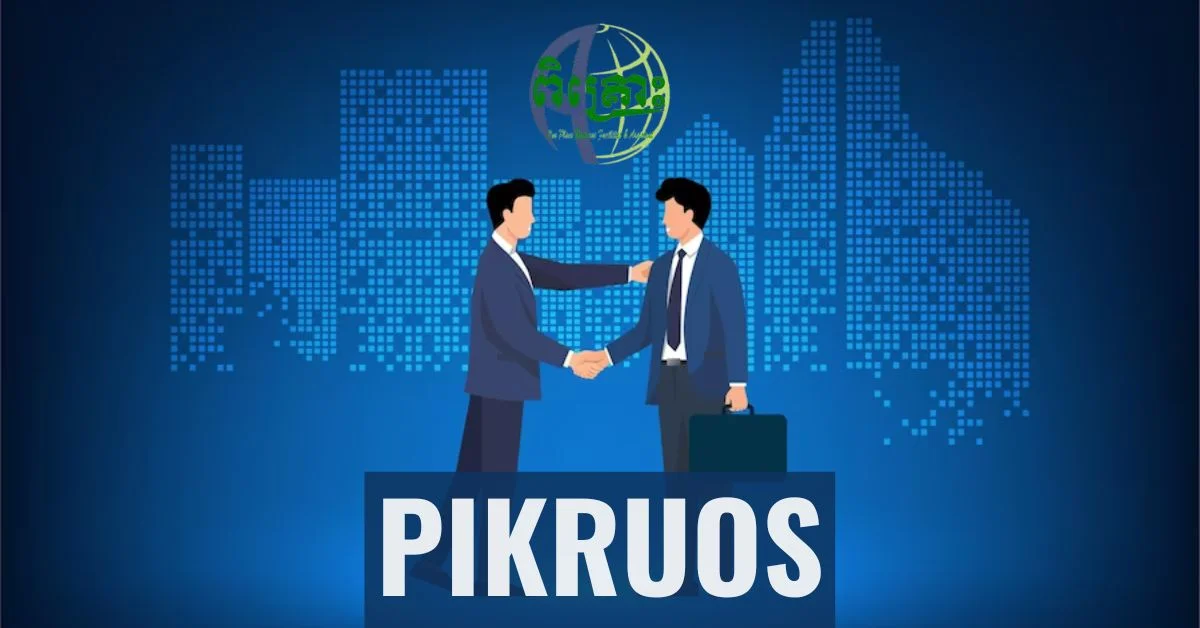
Introduction to Pikruos
In today’s fast-paced digital landscape, businesses are constantly seeking ways to improve efficiency and stay ahead of the competition. Enter Pikruos—a dynamic partner dedicated to delivering cutting-edge technology solutions tailored for your unique business needs. Whether you’re a start-up or an established enterprise, navigating the complex world of technology can be daunting. That’s where Pikruos shines, providing exceptional support that empowers your organization to thrive in a tech-driven environment. With innovative services designed to streamline operations and enhance productivity, it’s time to explore how partnering with Pikruos can transform your business journey.
The Importance of Technology Solutions in Business
In today’s fast-paced business landscape, technology solutions are no longer optional; they are essential. Companies rely on these tools to streamline operations and enhance productivity.
Effective technology solutions can automate tedious tasks, freeing up valuable time for teams to focus on strategic initiatives. This efficiency drives growth and innovation.
Moreover, the right tech can improve customer experiences. Businesses that embrace digital transformation often see a boost in engagement and satisfaction.
Data-driven insights enable firms to make informed decisions quickly. Organizations harnessing technology stay ahead of competitors by adapting swiftly to market changes.
Security is another crucial aspect. Robust technology solutions safeguard sensitive information against cyber threats, ensuring trust with clients and stakeholders alike.
Investing in effective business technologies paves the way for sustainable success in an ever-evolving environment. Adapting to these advancements keeps businesses agile and competitive.
Services Offered by Pikruos
Pikruos provides a diverse range of technology solutions tailored to meet the unique needs of businesses. From IT consulting to software development, every service is designed with efficiency in mind.
Their cloud services enable seamless data access and enhanced collaboration for teams. With robust security measures, Pikruos ensures that your information remains protected at all times.
Custom software solutions allow businesses to streamline operations effectively. Whether it’s a mobile app or an enterprise system, their innovative approach prioritizes user experience and functionality.
Additionally, Pikruos offers comprehensive support and maintenance services. This way, clients can focus on growth while knowing their technology infrastructure is well cared for.
With ongoing training and resources provided by experts, businesses are empowered to adapt swiftly in today’s fast-paced digital landscape. The commitment to customer satisfaction sets Pikruos apart as a true partner in business technology solutions.
Real World Examples of Pikruos’ Success
Pikruos has transformed businesses across various industries through innovative technology solutions. One notable case involved a mid-sized retail company struggling with inventory management. Pikruos implemented an advanced tracking system that streamlined operations, significantly reducing overstock and stockouts.
In another instance, a healthcare provider faced challenges in patient data handling. With Pikruos’ customized software solution, they enhanced data security while improving access for medical staff. This led to faster patient care and increased satisfaction rates.
Additionally, a startup in the tech sector benefited from Pikruos’ strategic consulting services. By optimizing their digital presence and automating workflows, they achieved impressive growth within months.
These examples illustrate how tailored technological interventions by Pikruos can drive efficiency and success for diverse organizations. Each story reflects their commitment to understanding unique business needs and delivering impactful results.
Why Choose Pikruos for Your Business Technology Needs?
Choosing Pikruos means investing in innovation and expertise. With a team of seasoned professionals, we deliver tailored solutions that align with your specific business goals.
Our commitment to quality sets us apart. We understand the unique challenges businesses face today and provide strategies that drive growth and efficiency.
Pikruos prioritizes customer satisfaction above all. Our collaborative approach ensures you are involved throughout the process, fostering transparency and trust.
We leverage cutting-edge technology to streamline operations. This not only boosts productivity but also enhances user experience across your organization.
When you partner with Pikruos, you’re choosing a long-term ally in navigating the complexities of modern business technology. We adapt to industry changes swiftly, ensuring your business remains competitive in an ever-evolving landscape.
Customer Testimonials and Reviews
Pikruos has garnered a multitude of positive reviews from satisfied clients who appreciate the company’s commitment to excellence. Customers often highlight the personalized approach taken by the team, ensuring that each solution is tailored specifically to their business needs.
One client shared how Pikruos transformed their outdated systems into streamlined processes, resulting in significant efficiency gains. This success story resonates with many who have experienced similar transformations.
Another testimonial praised Pikruos for its responsive customer support. Clients feel reassured knowing they can rely on expert assistance whenever challenges arise.
Many businesses value transparency and communication throughout projects. Feedback indicates that Pikruos excels in keeping stakeholders informed at every stage, fostering trust and collaboration.
Such endorsements showcase not just technical capability but also a genuine dedication to helping businesses thrive through innovative technology solutions.
Conclusion: Partnering with Pikruos for a Successful Future
Choosing Pikruos as your partner in business technology solutions can set your company on a path to success. With their extensive range of services tailored for various industries, they understand the unique challenges businesses face today. Their commitment to delivering effective technology solutions ensures that you stay ahead of the competition.
Customer testimonials highlight not just satisfaction but genuine transformations within organizations that have chosen Pikruos. The real-world examples demonstrate how businesses have thrived with the right technological support and guidance.
By collaborating with Pikruos, you’re not just opting for a service provider; you’re investing in a partnership focused on innovation and growth. This collaboration promises to equip your business with the tools necessary for navigating an ever-evolving digital landscape, ultimately leading towards lasting success.
FAQs
What is Pikruos?
Pikruos is a business technology solutions provider that offers tailored IT services such as software development, cloud solutions, consulting, and support to help businesses thrive in a digital-first world.
How does Pikruos’s help businesses improve efficiency?
Pikruos’s streamlines business operations by offering automation, secure data access, and custom software—freeing up time for strategic growth and innovation.
Which industries benefit most from Pikruos’s solutions?
Pikruos’s serves a wide range of industries including retail, healthcare, and tech startups—providing customized solutions to meet unique operational challenges.
What sets Pikruos’s apart from other IT service providers?
Pikruos’s stands out for its personalized approach, transparent collaboration, expert consulting, and long-term support that adapts with business needs.
Does Pikruos provide ongoing support and training?
Yes, Pikruos offers comprehensive maintenance and training to ensure clients can confidently manage their tech infrastructure and stay updated with the latest tools.
BUSINESS
Transforming Events with Complete Furniture Hire Solutions for Every Occasion
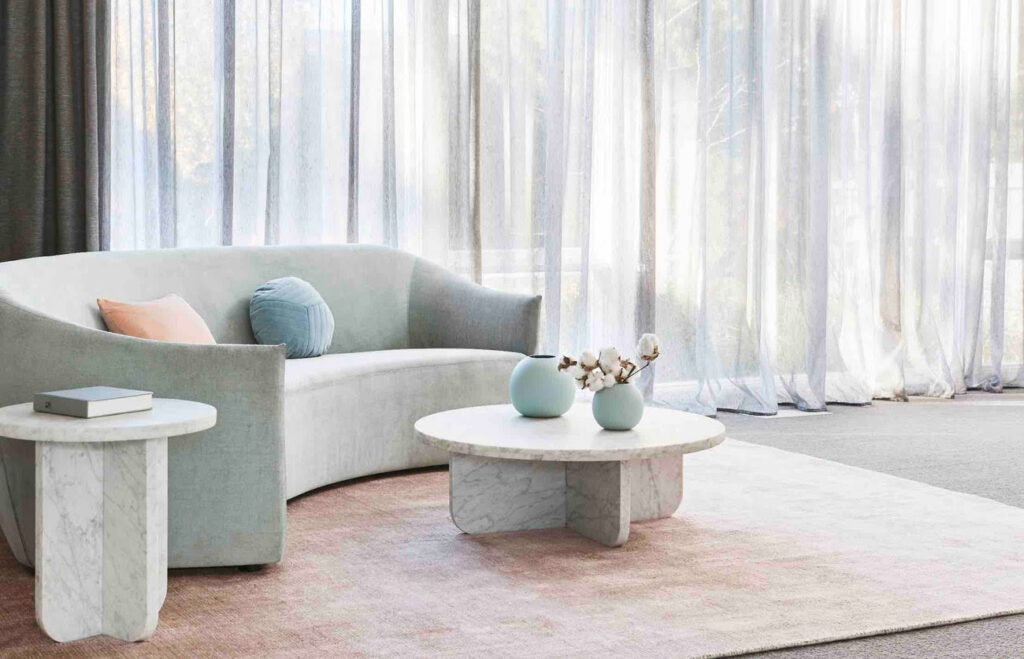
Planning an event, whether intimate or large-scale, requires careful attention to detail. From décor and lighting to food and entertainment, every aspect plays a role in creating the right atmosphere. Among these, event furniture is one of the most important elements that can make or break the overall experience for guests. The right chairs, tables, lounges, and décor items not only provide comfort but also set the tone and style of the occasion.
This is where complete furniture hire solutions for events big and small come in. By partnering with a professional event hire company like M Event Hire, you can access a wide variety of stylish, functional, and customizable furniture that perfectly matches your event’s theme and scale.
Why Furniture Hire is Essential for Events
No matter the type of gathering—be it a wedding, birthday celebration, gala dinner, or corporate function—the right furniture hire services can completely transform your venue. Here’s why:
- Enhances Guest Experience
Comfortable seating, elegant tables, and beautifully arranged lounges ensure your guests feel welcomed and valued. - Creates the Right Ambiance
Furniture contributes to the overall décor and vibe of the event. For instance, rustic wooden tables set a cozy tone, while sleek modern lounges create a chic, contemporary look. - Saves Time and Effort
Instead of worrying about sourcing, transporting, and setting up furniture, hiring experts means everything is delivered, installed, and packed away seamlessly. - Flexibility for All Event Sizes
Whether you’re hosting 20 people in a backyard or 500 guests at a grand venue, professional event hire companies can scale up or down depending on your needs.
Types of Event Furniture to Consider
Event hire services offer a wide range of furniture and accessories designed to suit all themes and occasions. Here are some popular options:
- Seating Solutions: Chiavari chairs, banquet chairs, bar stools, and lounge seating.
- Tables: Round banquet tables, cocktail tables, trestle tables, and coffee tables.
- Lounges & Sofas: Perfect for creating relaxed zones within your event.
- Outdoor Furniture: Benches, deck chairs, and marquees for outdoor gatherings.
- Décor Items: Lighting, table centerpieces, rugs, and decorative partitions.
By choosing complete furniture hire solutions for events big and small, you’ll have access to all of these elements in one place.
Benefits of Choosing M Event Hire
When planning an event in Australia, M Event Hire stands out as a trusted partner for providing top-quality furniture and event solutions. Here’s why:
- Wide Range of Options: From classic to modern designs, their extensive catalog caters to weddings, corporate events, festivals, and private parties.
- Affordable Packages: Hiring furniture is often more cost-effective than purchasing, especially for one-time events.
- Professional Setup: The team handles delivery, installation, and removal, saving you stress on the big day.
- Tailored Solutions: Whether it’s an intimate dinner or a large-scale event, they customize packages to suit your needs.
Event Trends: Furniture That Makes a Statement
Modern event styling is about more than just functionality; it’s about making a statement. Here are some trending furniture hire ideas:
- Mix-and-Match Seating: Combining different chair styles adds personality and flair.
- Rustic & Boho Chic: Timber tables paired with rattan lounges and earthy décor are trending for weddings and outdoor events.
- Luxury Lounges: Plush velvet lounges and ottomans create a VIP atmosphere at corporate and gala events.
- Sustainable Furniture: Eco-conscious choices like upcycled wood and reusable décor items are becoming increasingly popular.
With the right furniture hire solutions, you can bring any of these styles to life effortlessly.
Tips for Choosing the Right Furniture Hire Service
- Check the Inventory – Ensure the company has the specific furniture pieces you need.
- Read Reviews – Customer feedback can help you understand service quality.
- Consider Delivery & Setup – Always confirm logistics to avoid last-minute issues.
- Match Your Theme – Choose furniture that aligns with your event’s theme, colors, and style.
- Budget Wisely – Opt for complete hire packages that include setup, styling, and pickup for better value.
Final Thoughts
Event planning can feel overwhelming, but with the right support, it becomes a seamless and enjoyable process. Choosing complete furniture hire solutions for events big and small ensures that every detail of your celebration is covered—from stylish seating to decorative touches that impress your guests.
By partnering with experts like M Event Hire, you can focus on enjoying your special day while professionals handle the setup and styling. Whether it’s a wedding, corporate event, birthday, or festival, the right furniture hire company will help you transform your vision into reality
- GENERAL1 month ago
5 Factors That Affect Tattoo Removal Success
- ENTERTAINMENT2 months ago
Exploring the Kristen Archives: A Treasure Trove of Erotica and More
- LIFESTYLE6 months ago
The Disciplinary Wives Club: Spanking for Love, Not Punishment
- TECHNOLOGY6 months ago
Blog Arcy Art: Where Architecture Meets Art
- ENTERTAINMENT7 months ago
The Ultimate Guide to Shillong Teer Hit Number: How to Predict Your Next Win
- LIFESTYLE1 week ago
Who Is Sandra Orlow?
- LIFESTYLE3 months ago
Berniece Julien: The Private Life of Tyson Beckford’s Partner
- Uncategorized12 months ago
Conrad Fisher Transformation: From Top Student to Troubled Soul