TECHNOLOGY
Unlock Potential: The Impact of Quick Turn Tooling!
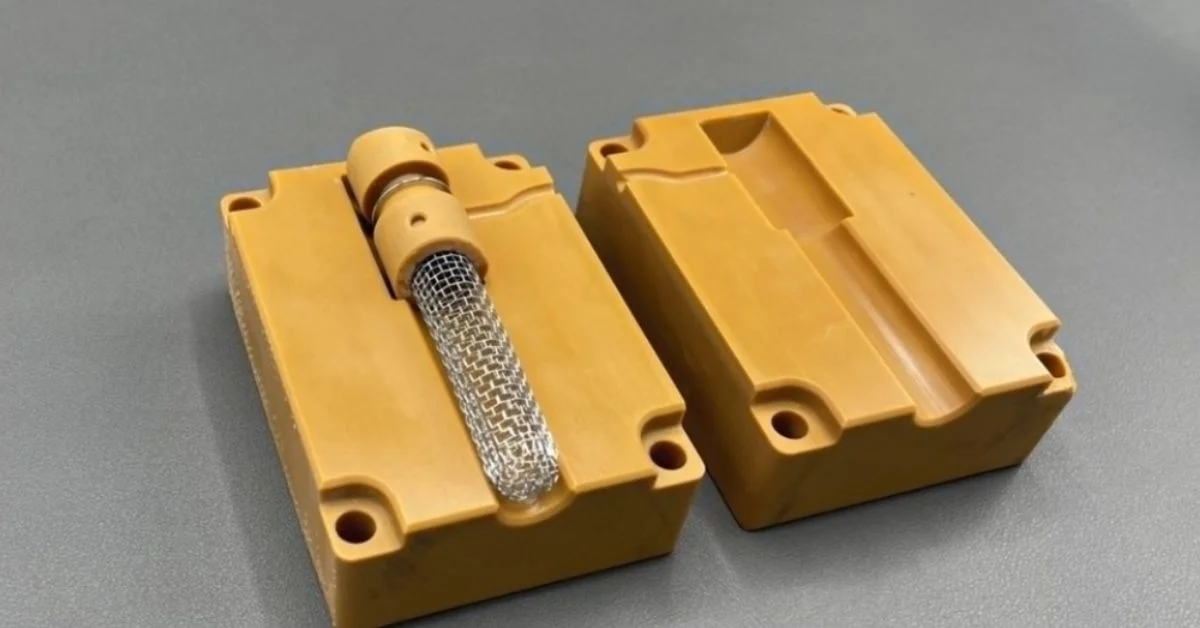
In the fast-pace manufacturing world, quick turn tooling proposes the future-ready innovation that totally changes the manufacturing process, from a concept to a finished product. This process utilizes novel techniques including the CNC process, additive manufacturing, and so forth to shorten the development period as much as possible.
It not only augments the capacity for repeatedly trying and learning from failure, but also provides a level of accuracy and expediency otherwise unmatched. quick turn tooling stands to the front leading the way and it is here when the latent potential of every project is discovered with project solutions being quickly brought into being forwards on at a previously unseen pace.
What is quick turn tooling?
Definition
The quick turn tooling (QTT) is a term used to refer to a quick part-formation process. It saves time associated with the development process by cutting the manufacturing time of molds and dies. Given its focus on rapid prototyping and quick production cycles, QTT is centered on agility and rapidity. Otrak uses CAD and CAM tech which are as accurate as machine tools that work in several industries.
Exploration
Analyzing QTT offers us a glimpse of its complex attachments, ranging from different aspects of our lives to history, future, memory and language. It supports a group of materials, from plastics and metals to glass. The process is associated with CNC machining, 3D printing, and EDM.
QTT is a technique that has an edge over other methods of manufacturing due to its ability to do quick iterations of designs, therefore, augments the duration required to manufacture products.
Concepts
Along with QTT’s approach to quick prototyping, faster testing procedure and agile manufacturing are the main themes of the company. Its versatility comes in demonstrating the expeditiousness of tools that are on demand for specific purposes.
QTT is the facilitating agent that closes the gap between the prototyping state and marketability of the products, thus assuring the advantage over other companies operating in the same field.
Traditional Contrast
It is much quicker like direct tooling but nowhere as slow as weeks or months. The conventional manufacturing approach is based on people who work using their hands and on extended machining time. QTT, unlike traditional translation movements, instills innovation through artificial intelligence and automation that will help you save on cost and time as you grapple with a handful of market demands time after time.
Feature | quick turn tooling | Traditional Tooling |
Definition | Rapid development and manufacturing of tools to expedite production processes. | Slower, sequential process for developing and manufacturing tools. |
Exploration | Encourages experimentation with design and materials for optimal outcomes. | Limited flexibility in design changes and material selection. |
Concepts | Focuses on speed, flexibility, and iteration. Uses CAD, CNC, additive manufacturing. | Emphasizes reliability and precision with established methods. |
Traditional Contrast | Dramatically reduces time from design to production. | Longer lead times from design to market. |
Cost Efficiency | Lower initial costs due to reduced development time and material waste. | Higher upfront costs due to longer development phases. |
Volume | Suited for low to medium volume production, with easy scaling options. | Best for high-volume production where setup costs are amortized. |
Customization | High degree of customization possible, supporting unique and complex designs. | Customization is possible but often costly and time-consuming. |
Table on quick turn tooling!
How Does quick turn tooling Work?
Process overview
quick turn tooling brings every manufacturing stage under the same roof, optimizing this process and decreasing lead times dramatically. First step is design analysis then expands to creating prototypes, and lastly, executive production. Stages like CAD, material selection and machining are what make progress in this stage. Machines that are operated by command and control systems such as EMP and CNC are central. The objective is capability to be rapidly production ready.
Design to production
In quick turn tooling, designs are hand-planted in products and the result is seen in a short order. CAD models are playing an important role as they indicate CNC machines and 3D printers how to act. This is a formation of the digital to physical link by means of material choice, tool path optimization, and testing. The corners of speed and precision are indispensable, which allows products to match the consumers’ exact specs.
3D printing
The 3D printing tool that has been considered offers a way of speed. This is how the layers are made, based on the designs. The pieces are built, with the construction starting from the bottom. It is very rich and has a high level of detail without anything extra added to the narrative. Yeah there are a variety of composite materials here starting from plastics extrusion to metals, a multi-purpose box again. The result? Use of 3D printing not only allows a quick creation of prototypes and functional parts, but also saves hours of time.
CNC machining:
NC technology is one of the integral parts of the Quick- Turn Tooling. It zaps, whittles, and cuts materials being sharper and cleaner than all around. CAD goes from aids; CNC machines are able to follow accurate coordinate data. These mostly manufacture parts, using metal and plastics. The tolerance is infinitely small. Efficiency and the quality of output are of paramount importance. They are critical for meeting the quick demands.
Why Choose quick turn tooling for Your Project?
Rapid prototyping
QTT offers an incredible value by converting a concept into a working prototype as fast as possible. By implying the design lacks within six hours or less. SLA and SLS technology collection enables designers to continuously modify and improve the prototypes to ensure they reach the required specs and are ready to go into full-scale production at any given time.
Time-to-market
With quick turn tooling, you not only speed your time to market but also dramatically achieve your product’s launch by zeroing in from the design to the shop. It optimizes production sequence, making the release quicker, thereafter. The emerging technologies increase the efficiency therefore leading to competitive edge that the innovative companies have quickly developed the innovation capturing the market attention before their competitors.
Advantages
quick turn tooling does save time and energy, despite being precise and versatile. Utilizing CNC machining and 3D printing casting, as well as avoiding using molds and expensive setups, enables effective manufacturing with reduced waste and lower costs.
New products impact
quick turn tooling supports the quick launching of new consumer products to the market with short lead times and quality defects free of charge. Through this it is possible to have testing, and selecting consumers, feedback which helps to make sure the products meet with the consumers’ needs. Through the speed of the process, in which many market players can take a hold of the public consciousness, some brand names can be perceived as leaders.
Exploring the Capabilities of quick turn tooling!
Material types
Rapid Turnover Tooling can work with any material unlike material that is limited by various materials. This technique does not require different types of tools and materials for different materials. Thanks to material options such as ABS, PC, and aluminum, printed design allows successful finishing of different projects, starting from the prototypes and ending up with functional parts, maintaining flexibility and quality.
Product variety
The key advantage of quick turn tooling is in its ability to deal with a variety of shapes. For instance, automotive components up to sophisticated medical devices are involved in its innovative scope of work. They, thus, quickly adapt, all the while presenting phenomena, even outside of their niche, accessible to research and development.
Precision
It is a unique feature in quick turn tooling that helps ensure high accuracy. The CNC machining technology presents flame-proof parts with precise tolerances. With this approach, pieces and parts are built fitting into perfection, work harmoniously and meet the warranty demanded in the industry hence aerospace and medical however critical they are.
Quality achievable
Unlike some other rapid machining providers, quick turn tooling manages to achieve high quality without slowing down the process of metal casting. Advanced mechanisms or techniques that are complemented with more strict quality control measures provide customers with products which reach the market faster and could hold or uphold excellence, satisfy the customers’ expectations and comply with the existing regulations.
The Role of CAD in Revolutionizing quick turn tooling!
CAD importance
CAD is the key, which helps transfer digital designs into the real world, where the parts become totally physically real. It facilitates designers to form reliable models and thus alleviate the risk of unwanted deflection of tools and products from standards. The digital trend change enhances clarity of works and reduces error occurrence as well as time consumption.
Design flexibility
CAD makes QTT so sensitive to customer design change because it can easily adjust the design. It enables redirection of priorities as the project develops and thus supports the dynamic change of project characteristics. The rapid adaptation capability in such robots guarantees that each industry’s bespoke solutions are developed through a custom approach.
Iteration speed
CAD quicken sequential loops in Quick Turned Tooling leading in a guided process that reduces prototyping time and enables parallel design, manufacture and production. Since design changes are being tried and tested in real-time, their effect on the changes is rapidly known and optimum solution is found. Such a quick pace is essential for preempting the rivals by getting to market faster.
Comparing quick turn tooling Techniques!
Additive manufacturing
The layer-by-layer fabrication of Additive Manufacturing stands out in the quick turn tooling because it creates components in a line-by-line manner. This method is particularly suitable for complicated shapes that traditional ways can’t deal with, thus reducing waste and allowing the diversification of varieties from Thermoplastic to metal. This is thus a very groundbreaking method that has led to the development of rapid prototypes.
CNC machining
CNC machining is the one that sets itself apart from the rest in the area of quick turn tooling for its outstanding precision and capability. Creating 3D printers gives ingenious tools of CAD to literally perform their functions across any range of materials within a short time span. CNC both for prototyping and production is there to provide a fine finish and exact clearance that is crucial for the demanding applications.
Urethane casting
Urethane casting technique is commonly used by quick turn tooling groups as it’s one of the cheap and fast ways to make high-quality low volume parts. Being cost-effective, offering a various range of material properties from rubber, to rigid plastics, make it our primary option. This method is ideally suitable for functional testing and would be used when the market-ready prototypes are available.
Rapid prototyping comparison
When it comes to quick turn tooling Techniques, Additive manufacturing will present you with the best fit if you need both complexity and customization effects. CNC machining provides precision and material diversity, and urethane casting is the best option if you are not ready for high-production orders. Each one is tailored for specific purposes hence they do not tend to cross each other paths thus, together they form a pipeline using which prototyping needs are addressed at all levels.
Feature/Technique | Additive Manufacturing | CNC Machining | Urethane Casting | Remarks |
Process Type | Layer-by-layer construction | Subtractive | Casting | Different foundational processes |
Material Compatibility | Plastics, Metals, Composites | Metals, Plastics, Composites | Polyurethanes, Silicones | Wide range across techniques |
Complexity & Design | High complexity & detail | Medium to high complexity | Medium complexity | Additive manufacturing leads in complexity |
Production Speed | Fast | Medium | Fast for initial parts | Urethane casting & additive manufacturing are quicker for initial pieces |
Finish Quality | Varies by technology | High | Medium to high | CNC machining provides superior surface finish |
Cost-Effectiveness | High for prototypes | High for production | Low for small batches | Urethane casting is most cost-effective for low volume |
Ideal Use Case | Prototyping, complex parts | Precision parts, large volumes | Short runs, prototypes | Each technique has its niche applications |
Table on Comparing Quick Turn Tooling Techniques!
Conclusion
Pulling the integrants of the evolutionary momentum quick turn tooling leaves for the world economy, it is apparent that this method is not only about speed. It summed up succinctly the cutting-edge, user-centric, and outcome-oriented technologies, which laid the foundation of a vast new dimension in the development process.
As we crack the speed barrier of Single Sustainable Tooling, one door after another begins to open up with reality-breaking potential that tear off the limits that border the creativity of the producers. quick turn tooling has become a technological advancement in the approach of manufacturing techniques, thus ensuring future usage in the trail of victory.
TECHNOLOGY
Tarnplanen: A New Blueprint for Real-Time Decision-Making
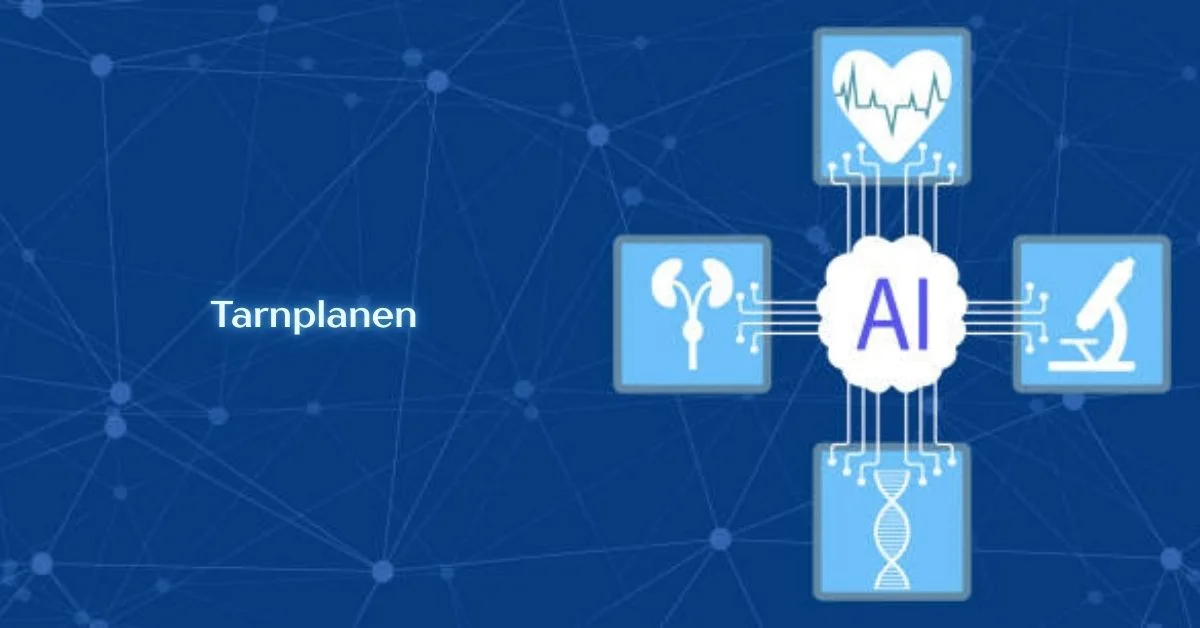
Introduction: The Map That Moves with You
Imagine navigating a dense forest with a GPS that doesn’t just mark your route but adapts in real time—responding to weather changes, unexpected terrain, or your shifting goals. That’s the conceptual power of Tarnplanen, a new way of planning that reshapes how we make decisions under pressure and uncertainty.
In a world where rigid schedules crumble in the face of global disruption—pandemics, climate shifts, AI revolutions—we need more than a plan. We need a living map. Enter Tarnplanen.
What Is Tarnplanen? A Definition in Motion
Tarnplanen is not your typical planning framework. It refers to a layered coordination structure for adaptive decision-making in complex, multivariable environments. Think of it as a flexible scaffolding that grows, contracts, and repositions itself in real-time to align with both internal feedback and external change.
Unlike traditional models that rely on sequential logic and static assumptions, Tarnplanen functions more like liquid architecture—built to bend, not break.
Metaphor: If a Gantt chart is a train on fixed tracks, Tarnplanen is a drone that recalibrates its flight path based on wind, terrain, and mission updates.
Roots of Tarnplanen: A Hybrid of Philosophy, Tech, and Chaos Theory
The philosophy behind Tarnplanen draws from several streams:
- Systems Thinking: Understanding that no element exists in isolation.
- Chaos Theory: Small changes lead to vast, nonlinear outcomes.
- Agile Methodologies: Prioritizing iteration, feedback loops, and stakeholder alignment.
Historically, war rooms, disaster response systems, and space missions required similar dynamic planning. But technology and data now allow us to scale these adaptive mechanisms across everyday industries.
Explore related articles to deepen your understanding before you go.
Real-World Applications: Tarnplanen in Action
Tarnplanen is gaining traction in sectors that demand fast, intelligent adaptation. Here’s a look at its real-world applications:
Real-World Use Cases
Sector | Use Case Example | Result or Benefit |
---|---|---|
AI | Adaptive model tuning based on real-time inputs | Improved accuracy and responsiveness |
Healthcare | Dynamic patient monitoring during surgery | Reduced risk and personalized treatment |
Education | Real-time curriculum shifts via student feedback loops | Enhanced engagement and learning outcomes |
Business | Flexible product roadmaps based on market data | Faster go-to-market and reduced waste |
Why Tarnplanen Wins: Comparisons & Differentiation
What sets Tarnplanen apart from conventional planning methods? Let’s break it down:
Key Differences Comparison
Feature/Aspect | Tarnplanen | Traditional Model |
---|---|---|
Scalability | Built to expand with complexity | Struggles beyond fixed variables |
Adaptability | Real-time recalibration | Static until formally revised |
User Focus | Multi-input, decentralized | Top-down, expert-driven |
Tarnplanen’s advantage is its resilience. It’s not just about predicting the future—it’s about responding effectively when predictions fail.
Emerging Trends & Future Implications
As AI becomes more embedded in our daily decision-making, Tarnplanen is poised to underpin smarter autonomous systems. Expect developments in:
- Augmented cognition: AI helping humans adapt in real time (think smart wearables).
- Decentralized governance: Communities using Tarnplanen-like structures for responsive policy.
- Climate response systems: Dynamic models adjusting in real-time to environmental data.
But risks loom: algorithmic overreach, ethical dilemmas in automated decisions, and loss of transparency. Future versions must ensure human oversight and cultural adaptability.
Implementation Blueprint: Making Tarnplanen Work
Deploying Tarnplanen isn’t about installing new software—it’s about shifting mindset and systems toward fluid responsiveness. Here’s how:
Implementation Tips / Best Practices
Strategy/Tip | Description | Value Delivered |
---|---|---|
Focus on Feedback Loops | Establish fast, frequent input cycles from users and environment | Ensures continuous course correction |
Start with Microplans | Pilot Tarnplanen at a small scale (e.g., one department) | Builds early wins and insights |
Iterate on Structure | Refine your decision map regularly—don’t set it and forget it | Maintains agility and relevance |
Whether it’s a startup pivoting strategy or a hospital managing a crisis, Tarnplanen thrives where change is constant.
Conclusion: Planning for Humans, Not Machines
At its core, Tarnplanen is a response to the human condition in a digital world. We are not linear beings—we adapt, shift, improvise. Why shouldn’t our plans do the same?
Tarnplanen’s isn’t just a framework. It’s a philosophy of living intelligence. It teaches us that the smartest path forward isn’t the one most mapped—it’s the one most responsive.
In adopting Tarnplanen, we reclaim flexibility, resilience, and above all, relevance in a world that refuses to stand still.
Loved this post? You’ll find even more just like it on our blog!
FAQs
Q1: What is Tarnplanen in plain terms?
A: It’s a flexible, real-time planning method that changes as your situation changes.
Q2: Is Tarnplanen’s a software tool?
A: No, it’s a planning philosophy or framework. But tools can be designed around it.
Q3: Who should use Tarnplanen’s?
A: Anyone in fast-changing environments—business leaders, teachers, doctors, or even parents.
Q4: What’s the biggest advantage of Tarnplanen’s?
A: Its ability to adapt in real time, reducing risk and waste.
Q5: How do I get started with Tarnplanen’s?
A: Begin small—use it for a single project or decision, and build feedback loops from there.
APPS & SOFTWARE
Exploring the Unique Features of Janitor AI Chatbot
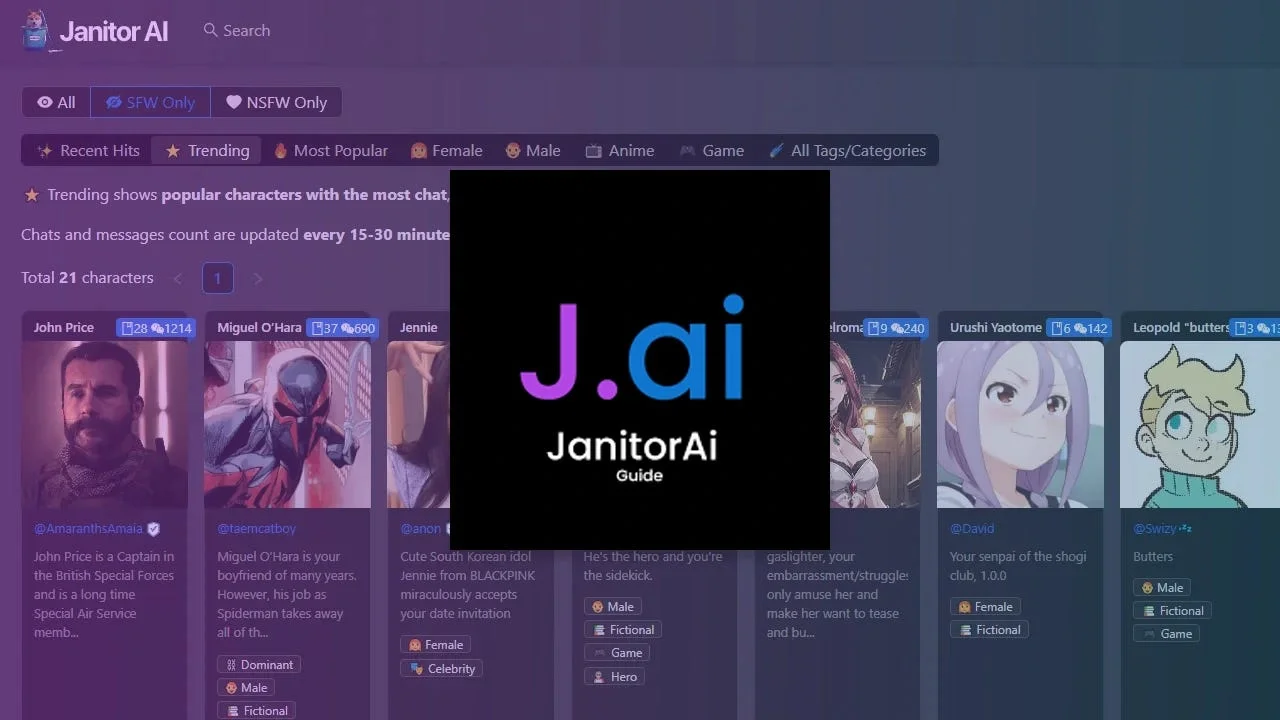
Janitor AI is a chatbot website with a unique anime-style character. Users can chat with other people’s characters or create their own. What sets Janitor AI apart is its support for NSFW roles, which is appealing to many users. Users can make money through chat services on Janitor AI, adding diversity to the character experience. However, the NSFW support also raises security concerns.
Janitor AI: A Unique Chatbot Experience
Janitor AI offers a unique chatbot experience through its anime-style character chat robot website. Users have the option to create their own characters or engage in conversations with other users’ created characters. What sets Janitor AI apart from other AI chatbots is its support for NSFW roles, allowing users to break through traditional security norms and explore more daring interactions. This feature has proven to be attractive to many users seeking a different kind of chatbot experience. While Janitor AI provides an opportunity for users to monetize their characters through chat services, the support for NSFW content also raises concerns about potential security issues.
Janitor AI Features
Janitor AI is an innovative platform that offers various features for users to interact with its anime-style character chat robot. Users can engage in conversations with the Janitor AI, create their own unique characters, or even chat with characters created by other users. The platform not only provides a fun and interactive experience but also allows users to generate income through chat services. This feature promotes diversity and enhances the overall character experience on Janitor AI, making it a popular choice for those looking to engage in creative and entertaining interactions online.
Diverse character styles
Janitor AI is a unique website that offers a diverse range of character styles through its anime-style chat robot feature. Users have the option to create their own customized characters or engage in conversations with other user-created characters. The platform also allows users to monetize their chat services, offering a creative way for individuals to earn money while enhancing the overall character diversity and user experience on Janitor AI. This innovative concept not only fosters creativity but also promotes a sense of community among users who share a passion for engaging with virtual characters.
Character marketization
Janitor AI is a unique website that offers a character marketization platform with its anime-style character chat robot feature. Users have the option to create their own characters or interact directly with other users’ created characters. This innovative concept allows everyone to not only enjoy chatting with various characters but also earn money by providing chat services. By fostering diversity and enhancing the overall user experience, Janitor AI opens up new opportunities for both creators and consumers in the digital world.
Adult content availability
Janitor AI is a unique website that offers adult content availability through its anime-style character chat robot, Janitorai. Users have the option to create their own characters or engage in conversations with other users’ created characters. The platform allows everyone to participate in creating characters and provides opportunities to earn money through chat services. This feature not only enhances the diversity of characters but also enriches the overall user experience on Janitor AI.
Local deployment option
Janitor AI offers a local deployment option for users to interact with its anime-style character chat robot website. Users can engage with the Janitor AI, a free service that allows them to create their own characters or chat directly with other users’ created characters. This platform provides an opportunity for everyone to not only explore diverse character creations but also potentially earn money through chat services. By enhancing the overall experience and diversity of characters available, Janitor AI aims to provide a unique and engaging online environment for users to connect and express themselves creatively.
Benefits of Using Janitor AI
Janitor AI is a unique anime-style character chat robot website that offers numerous benefits to its users. Not only can individuals create their own personalized characters, but they can also engage in conversations with other users’ created characters. The platform allows for a diverse and enriched experience, giving everyone the opportunity to showcase their creativity and interact with a wide range of characters. Additionally, users have the chance to make money through chat services on Janitor AI, further enhancing the appeal and utility of this innovative platform.
Personalized chat experience
Janitor AI offers a unique and personalized chat experience through its innovative AI technology. Users can interact with the Janitor AI, a charming anime-style character chat robot, for free on the website. Whether it’s seeking assistance with cleaning tips or simply engaging in casual conversation, Janitor AI is there to provide support and entertainment. The janitorai platform allows users to enjoy a fun and interactive experience while receiving helpful information and guidance from this virtual assistant.
Income generation opportunities
Janitor AI is a cutting-edge income generation opportunity that offers a free and innovative chatbot service. This unique AI, designed as an anime-style character, has quickly gained popularity for its ability to provide efficient cleaning solutions through interactive conversations. Users can access Janitor AI’s services through a chat platform, making it easy and convenient to receive assistance with various cleaning tasks. The combination of technology and creativity in Janitor AI makes it stand out as a versatile tool for both personal and commercial use.
Enhanced character diversity
Janitor AI is a unique anime-style character chat robot website that offers enhanced character diversity. Users can interact with the Janitor AI for free and engage in conversations through the Janitor AI chat feature. This innovative technology brings a fun and interactive element to online communication, allowing users to experience a unique and engaging way to connect with others. The Janitor AI adds a creative twist to traditional chat platforms, offering users an entertaining and personalized experience unlike any other.
Concerns and Challenges
One of the concerns and challenges surrounding the Janitor AI website is the potential impact of offering a free chat service with an anime-style character. While the novelty and entertainment value of interacting with an AI chatbot in this unique format may attract users, there are worries about the reliability and effectiveness of such a system. Additionally, there may be ethical considerations regarding the use of anime-style characters for customer service interactions. As Janitor AI continues to develop and refine its services, addressing these concerns will be crucial to ensuring a positive user experience and maintaining trust in the platform.
Security risks with NSFW content
The use of NSFW content on the Janitor AI website poses significant security risks for both the users and the platform itself. Such content can attract malicious actors and expose users to potential harm, such as phishing attacks or malware distribution. Additionally, the anime-style character chat robot format of Janitor AI may inadvertently make users more susceptible to engaging with risky content, as the cute and friendly appearance of the AI may lower their guard. It is crucial for the platform to implement strict security measures and moderation protocols to protect its users from these dangers.
Potential misuse of adult themes
There is a concern about the potential misuse of adult themes on the Janitor AI website, which features an anime-style character chat robot. The playful and colorful design of the website may attract younger audiences who could inadvertently stumble upon inappropriate content. It is important for the creators of Janitor AI to implement strict moderation measures to ensure that users are not exposed to any harmful or explicit material while interacting with the chatbot. Balancing the whimsical nature of the anime character with responsible content management will be crucial in maintaining a safe and enjoyable experience for all users.
Conclusion:
The Janitor AI Chatbot offers a range of unique features that set it apart from other chatbots in the market. Its advanced algorithms and machine learning capabilities allow for efficient and accurate responses to user queries. The free version of Janitor AI provides a valuable opportunity for businesses to experience its benefits without financial commitment. With its user-friendly interface and customizable options, Janitor AI is a powerful tool for enhancing customer service and streamlining operations. To take advantage of the innovative features of Janitor AI Chatbot, businesses are encouraged to explore its capabilities and integrate it into their workflow today.
APPS & SOFTWARE
AI Essay Writer By EssayGPT – Top Free Essay Generator
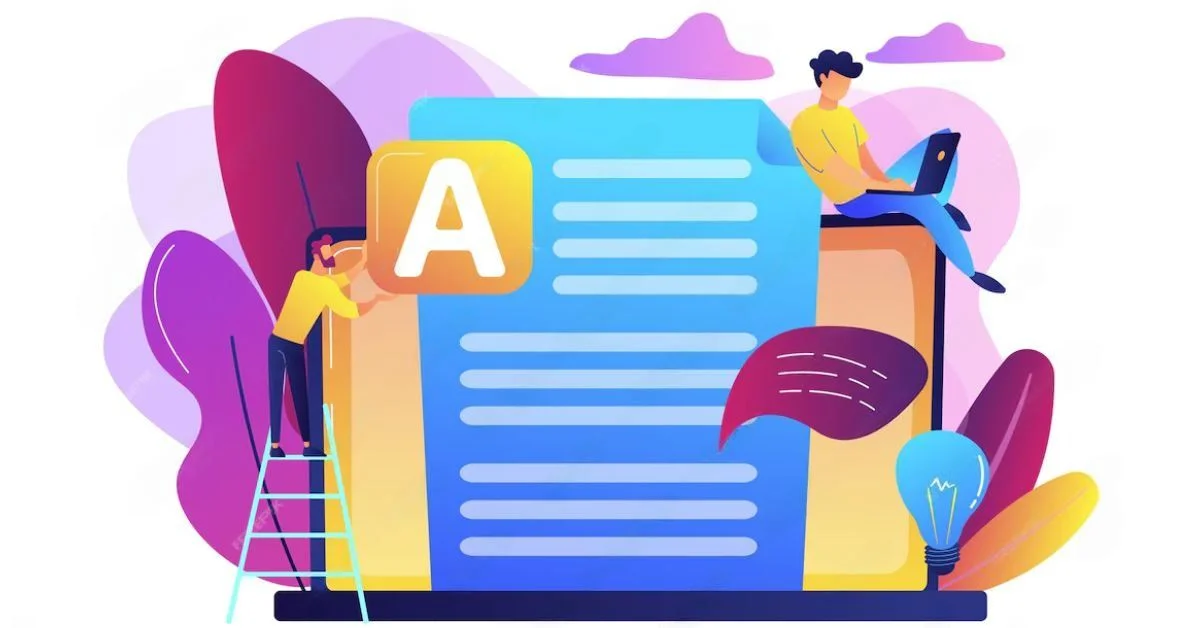
In the dynamic world of academic and professional writing, where the pressure to deliver high-quality, plagiarism-free, and engaging content is ever-present, the arrival of AI-powered essay writing tools has revolutionized the way we approach the written word. Among these groundbreaking advancements, EssayGPT stands out as a beacon of innovation, offering a suite of writing tools designed to cater to a myriad of writing needs. In this detailed review, we delve into the intricacies of EssayGPT, exploring its features, usability, and overall impact on the writing process.
What is EssayGPT?
A Multi-Faceted Writing Companion
At its core, EssayGPT is an AI essay writer that promises to generate plagiarism-free essays across a variety of disciplines and topics. Beyond mere essay writing, this AI-powered platform extends its capabilities to rewriting, summarizing, extending, and even generating thesis statements, making it a one-stop solution for students, academics, educators, content writers, and business professionals alike.
Cutting-Edge AI at Your Fingertips
Utilizing advanced natural language processing algorithms and machine learning techniques, EssayGPT analyzes the structure and style of any given topic, tapping into vast internet resources to produce well-researched and coherently structured essays. The tool not only adheres to grammatical and stylistic norms but also adjusts according to the contextual relevance of the topic and the target audience’s expectations.
Experiencing EssayGPT: A User’s Perspective
Accessibility and User Interface
Navigating through EssayGPT’s dashboard is a breeze, thanks to its clean and intuitive user interface. The ease of access, coupled with the tool’s web-based nature, allows users to start generating content without the hassle of sign-ups or subscriptions. This seamless accessibility underscores EssayGPT’s commitment to user convenience and efficiency.
A Symphony of Writing Tools
Academic Writing and Beyond
With an arsenal of features tailored for diverse writing demands, EssayGPT offers everything from essay checkers and rewriters to hook generators and research paper summarizers. Each tool is designed to enhance the writing process, whether by injecting creativity, ensuring originality, or simplifying complex subjects.
Customization and Precision
One of EssayGPT’s standout aspects is the level of customization it offers. Users can specify their target audience, desired tone, reference style, and essay type. This customization ensures that the output not only meets the specific requirements but also resonates with the intended readership.
Harnessing the Power of EssayGPT
A Boon for Students and Educators
For students grappling with tight deadlines and complex topics, EssayGPT emerges as a powerful ally, offering swift and insightful assistance in essay construction and research exploration. Educators, on the other hand, can leverage this tool to generate engaging example essays and stimulate creativity among their students.
A New Horizon for Professionals
Content creators and business professionals can utilize EssayGPT to maintain a consistent flow of high-quality writing, be it in the form of blog posts, reports, or marketing content. The ability to generate content across languages further amplifies its utility, breaking down linguistic barriers and expanding audience reach.
The Verdict: Transforming Writing with AI
Accelerating Creativity and Productivity
EssayGPT unmistakably accelerates the essay-writing process, marrying speed with sophistication. The rapid generation of well-structured, coherent, and customized content not only saves time but also allows for a more efficient allocation of creative energies towards refining and personalizing essays.
The Multilingual Maestro
With support for multiple languages, EssayGPT is a testament to the evolving capabilities of AI in bridging communication gaps. This feature is particularly beneficial for non-native speakers and professionals targeting global audiences.
Continuous Learning and Improvement
The essence of EssayGPT’s innovation lies in its capacity for growth. By learning from previous interactions and continuously updating its database and algorithms, EssayGPT ensures that the quality of essays remains high, fostering a cycle of constant improvement.
Conclusion: A Leap Towards the Future of Writing
EssayGPT stands as a testament to the transformative power of AI in the realm of writing. By offering a comprehensive suite of tools designed to address varied writing needs, it democratizes access to high-quality, customized, and engaging content. Whether you are a student, educator, professional writer, or business executive, EssayGPT equips you with the means to elevate your writing, making the process not just easier, but also more creative and fulfilling.
In the competitive and fast-paced world we navigate, EssayGPT serves as more than just a tool; it’s a partner in creativity, a catalyst for innovation, and a gateway to endless possibilities in the art of writing. As we continue to explore and embrace these AI-driven advancements, the future of writing looks not only brighter but boundless.
- ENTERTAINMENT4 days ago
Exploring the Kristen Archives: A Treasure Trove of Erotica and More
- ENTERTAINMENT1 day ago
Kiss KH: The Streaming Platform Redefining Digital Engagement and Cultural Currents
- EDUCATION1 day ago
Lingrohub Platform: A Complete Student Access Guide
- LIFESTYLE4 months ago
The Disciplinary Wives Club: Spanking for Love, Not Punishment
- TECHNOLOGY1 day ago
Casibom: The Digital Alchemy Reshaping Systems, Society, and Self
- TECHNOLOGY24 hours ago
Securing Your Online Presence: The Ultimate Guide to Buying an SSL Certificate
- TECHNOLOGY4 months ago
Blog Arcy Art: Where Architecture Meets Art
- BUSINESS24 hours ago
Diversifying Your Portfolio: The Key to Successful Investing in Portland, Oregon