BUSINESS
What Are the Key Considerations When Choosing Industrial Automation Systems?
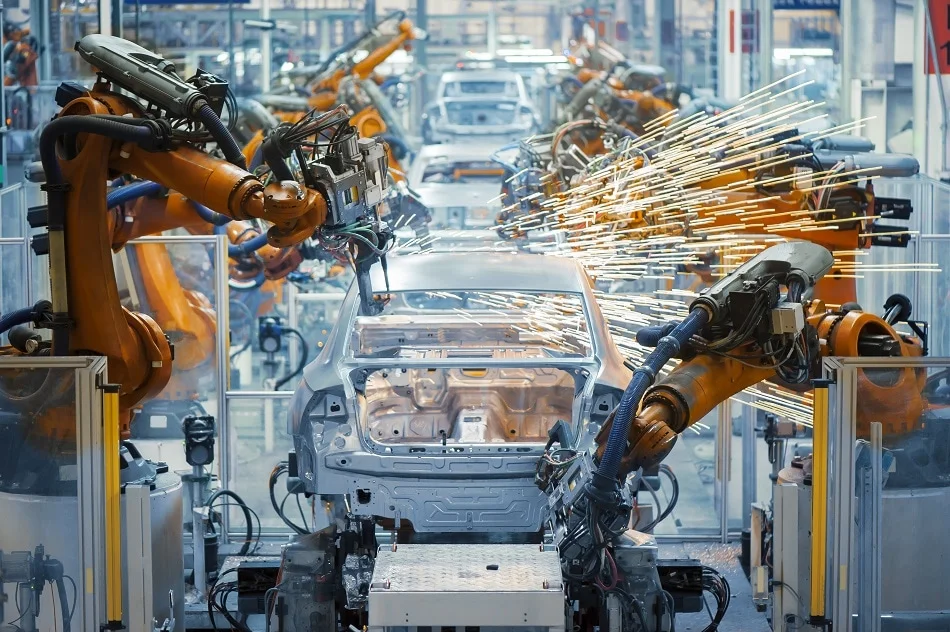
In today’s fast-paced industrial landscape, companies continuously seek ways to enhance productivity, improve efficiency, and reduce costs. One of the most effective solutions is the implementation of industrial automation systems, which enable manufacturers and industries to automate repetitive tasks, improve precision, and streamline operations. However, choosing the right industrial automation systems can be complex, considering many factors. The decision-making process requires careful planning and evaluation, from selecting the appropriate components to ensuring compatibility and scalability.
- Assessing the Needs of Your Operation
Before examining specific components or systems, it is essential to assess your business’s unique requirements. Different industries and processes have distinct needs, and the type of automation system you choose will depend on the tasks you want to automate, the scale of your operations, and the level of precision required.
For example, automotive, electronics, and pharmaceutical industries may require exact automation systems and the ability to handle complex tasks. On the other hand, industries like food and beverage or packaging might focus more on speed, efficiency, and reliability.
Key questions to consider include:
- What specific tasks or processes are you looking to automate?
- How critical are precision and repeatability in these tasks?
- What flexibility do you need to adapt to future process changes?
- Are you looking for full automation or partial automation?
By clearly identifying your operational goals, you can narrow your choices and select an industrial automation system that aligns with your business’s needs.
- Selecting the Right Components
Once you’ve established your automation goals, the next step is selecting the right components to work together to achieve them. Industrial automation systems comprise several critical elements, including actuators, sensors, controllers, and software interfaces. Each component ensures the system operates efficiently and meets the desired performance standards.
- Actuators: Actuators control the movement and action in automated systems. Electric actuators, such as those offered by ETI Systems, are popular because of their precision and low maintenance requirements.
- Sensors: Sensors are crucial for detecting changes in the environment or system and providing feedback to ensure accurate operation.
- Controllers: Programmable Logic Controllers (PLCs) and Distributed Control Systems (DCSs) control the automated processes and coordinate the functions of various components.
- Software: Modern automation systems often include advanced software that enables data monitoring, real-time adjustments, and integration with larger industrial control systems.
Choosing high-quality components is essential for ensuring the system’s long-term reliability and efficiency. Systems distributors like Digikey provide various automation components from multiple manufacturers, making it easier for businesses to source the parts they need from a single, trusted supplier.
- Compatibility and Integration
An essential consideration when selecting industrial automation systems is ensuring that all components are compatible with each other and can integrate seamlessly into your existing infrastructure. Many companies face challenges when implementing new automation systems due to compatibility issues between old and latest equipment. This can result in costly delays, increased downtime, and the need for expensive retrofits.
To avoid such challenges, businesses should prioritize modular and scalable automation systems. A modular system allows you to add or replace components without overhauling the entire system. Similarly, scalability ensures that you can quickly expand the system’s capacity as your business grows or your needs evolve.
- Scalability for Future Growth
One of automation’s key benefits is its ability to grow with your business. When selecting industrial automation systems, it’s essential to consider your company’s long-term goals. A system that meets your current needs may not be sufficient as your business expands or your production volume increases.
Scalability is crucial in automation systems. It allows you to upgrade or add new capabilities without having to invest in an entirely new system. For example, some systems allow you to add new actuators, sensors, or controllers as your operations evolve. By choosing a scalable system, you can maximize your return on investment and avoid the need for costly system replacements down the line.
- Cost Considerations
While automation can lead to significant cost savings in the long run by reducing labor costs and improving efficiency, the initial investment in industrial automation systems can be substantial. When evaluating the price, it’s essential to consider the long-term benefits that the system will bring. Investing in high-quality components from reputable manufacturers and system distributors like ETI Systems and Digikey can prevent costly breakdowns and reduce maintenance expenses. Additionally, energy-efficient components can help reduce operational costs by minimizing power consumption.
- Reliability and Maintenance
Industrial automation systems’ reliability depends on the quality of their components and the robustness of their design. When evaluating systems, look for components with a proven durability and longevity track record. It’s also important to consider the system’s maintenance requirements. Some systems require regular maintenance or part replacements, while others are designed to operate with minimal intervention.
Conclusion
By considering factors such as operational needs, component selection, compatibility, scalability, cost, reliability, and safety, you can make choices that will benefit your business in the long run.
BUSINESS
Mastering Debt Income Funds: A Comprehensive Guide to Enhancing Your Portfolio
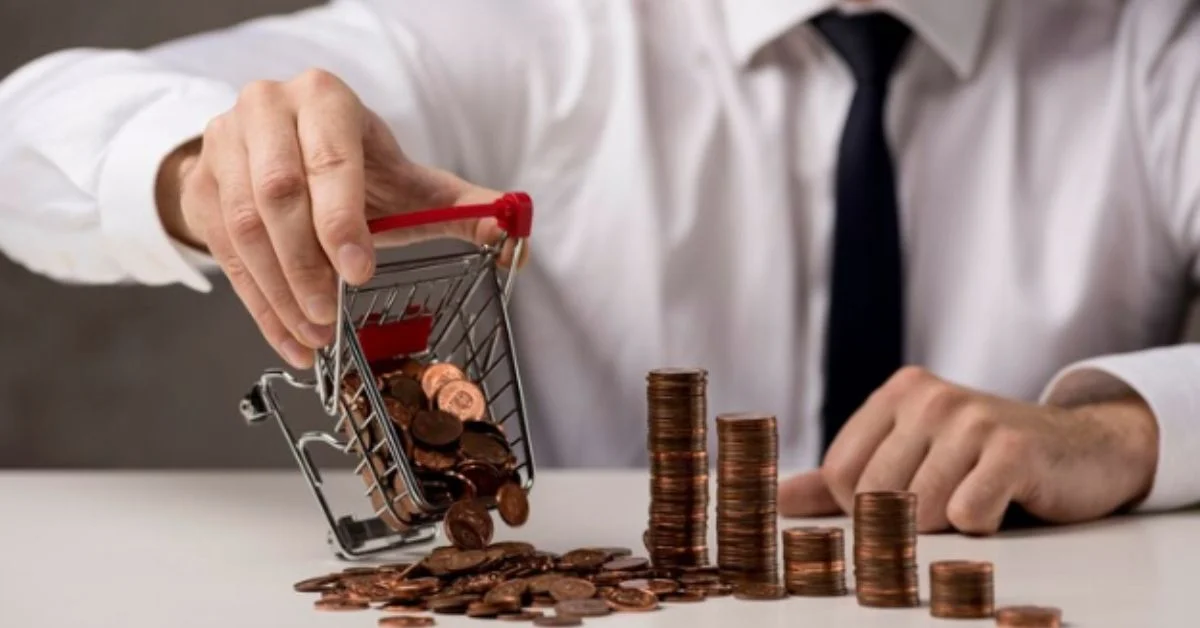
For investors seeking a blend of stability and steady income in their investment portfolios, debt income funds offer a promising avenue. Often viewed as a safer alternative to equity investments, these funds can provide regular income while preserving capital. This detailed guide delves into the world of debt income funds, helping you understand and learn opportunities with debt income funds to make informed investment decisions that align with your financial goals, learn opportunities with depb income funds
What are Debt Income Funds?
Debt income funds, commonly referred to as fixed-income securities, invest in a combination of debt instruments such as government bonds, corporate bonds, mortgage-backed securities, and other debt securities. The primary aim of these funds is to provide investors with regular income through interest payments, making them an ideal choice for income-focused investors.
Key Benefits of Investing in Debt Income Funds
1. Regular Income Stream: One of the most appealing aspects of debt income funds is their potential to generate a steady and predictable income stream through interest payments, which can be distributed monthly or quarterly to investors.
2. Lower Risk Profile: Compared to stocks and other equity investments, debt income funds typically have a lower risk profile. The investments are made in securities that have a fixed repayment schedule and interest rate, providing greater security and stability.
3. Diversification: By incorporating debt income funds into your portfolio, you can diversify your investments and reduce overall risk. This diversification can help buffer against volatility in the stock market.
4. Capital Preservation: Investors who are risk-averse or nearing retirement may find the capital preservation aspect of debts income funds attractive. These funds focus on maintaining the principal investment while providing returns through interest income.
How to Invest in Debt Income Funds
Step 1: Assess Your Financial Goals and Risk Tolerance
- Determine your investment objectives and how much risk you are willing to accept. Understanding your need for income generation versus capital growth is crucial in choosing the right debt income fund.
Step 2: Research Different Funds
- Learn opportunities with debts income funds by researching various funds available in the market. Look into their performance history, the credit quality of bonds they hold, their interest rate sensitivity, and management fees.
Step 3: Diversify Your Investments
- Consider diversifying across different types of debt funds, such as short-term, long-term, corporate bond, and government bond funds to balance risk and optimize returns.
Step 4: Monitor and Rebalance
- Regularly review your investment to ensure it continues to meet your financial goals. Rebalance your portfolio as necessary in response to changes in market conditions or in your financial circumstances.
Key Considerations When Choosing Debt Income Funds
1. Interest Rate Risk: Interest rate changes can affect the value of debts income funds. When interest rates rise, the value of existing bonds typically falls.
2. Credit Risk: The risk that the issuer of a bond will not be able to make principal and interest payments. Review the credit ratings of the bonds within the fund’s portfolio to assess this risk.
3. Inflation Risk: Inflation can erode the purchasing power of the payments from bonds. Consider inflation-protected securities as a potential component of your investment strategy.
4. Liquidity Risk: Some debts income funds may invest in securities that are less liquid than others, making it difficult to sell these investments at a fair price.
Maximizing Returns from Debt Income Funds
1. Use a Laddering Strategy: By creating a portfolio of bonds with staggered maturities, you can manage interest rate risks and provide liquidity and income continuity over time.
2. Focus on Quality: Investing in bonds with higher credit ratings may offer lower yields but provide greater security and stability.
3. Stay Informed: Keep up with financial news and trends related to interest rates and economic indicators that can impact bond markets. Knowledge can be a powerful tool in adjusting your investment strategy proactively.
Conclusion
Debt income funds can serve as a cornerstone of a well-rounded investment portfolio, offering benefits such as regular incomes, reduced risk, and capital preservation. By taking the time to learn opportunities with debt incomes funds and understanding how to effectively manage these investments, you can significantly enhance your financial stability and success. Whether you are a conservative investor focused on incomes or someone looking to diversify their investment risks, debt incomes funds provide a viable and strategic option for achieving your long-term financial objectives.
BUSINESS
Exploring the Benefits of ETRM Systems in Energy Trading
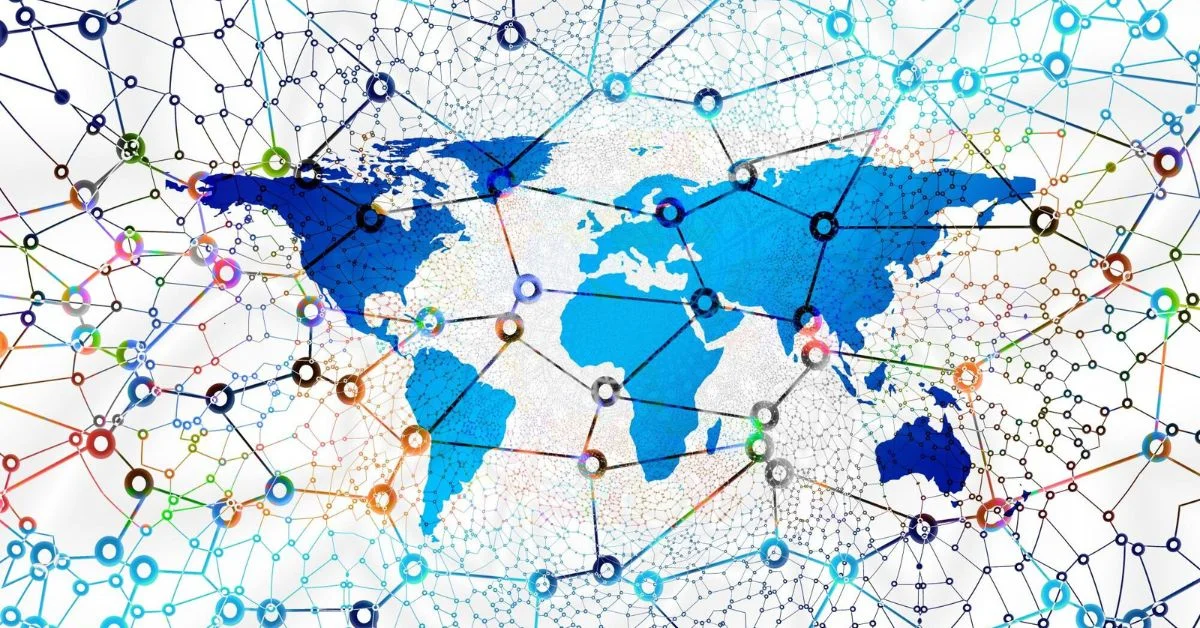
From the flick of the switch in our homes to the aggressive markets that power our industries, energy trading is an indispensable aspect of modern life. It’s a complex dance of supply and demand, regulations, geopolitics, and weather that hinges on one thing above all – information.
In this high-stakes arena, ETRM systems serve as beacons of order in an otherwise turbulent financial world. These systems are the backbone of energy trading and provide the necessary tools to manage risk.
Let’s take a closer look at how ETRM systems are unlocking growth in the energy trading industry.
Read on to begin!
Improved Operational Efficiency
This energy trading solution streamlines and automates many processes. This includes trade execution and settlement. These systems save time and resources for energy trading companies. This is made possible by reducing manual work and human error.
This allows them to focus on more strategic tasks. Such tasks include analyzing market trends and developing new trading strategies. Also, this power trading platform can integrate with other business functions. They can span from accounting and risk management.
This allows them to provide a comprehensive view of the company’s operations. Such an integration improves efficiency. This is achieved by eliminating silos and promoting better communication between departments.
Enhanced Decision-Making
Access to real-time data and advanced analytics tools is crucial in today’s fast-paced energy trading market. ETRM systems provide traders with accurate and up-to-date information on:
- market conditions
- supply and demand dynamics
- price fluctuations
This enables them to make faster, more informed decisions. Thus, allowing them to have a competitive edge.
Traders can also identify profitable opportunities and act on them before their competitors. This comes along with the ability to analyze vast amounts of data.
If you discover more about ETRM systems, you will find that some also offer predictive analytics. They help forecast future market trends and optimize trading strategies with the right decisions. This can further enhance a company’s bottom line.
Moreover, ETRM systems can also be tailored to fit the unique needs and processes of each energy trading company. This ensures that they are adaptable to different market conditions and regulations.
Scalability and Adaptability
ETRM systems must also be able to adapt and scale accordingly. This comes along as the energy trading industry continues to evolve. Such systems are designed to handle large volumes of data. Thus, they can easily integrate with new technologies and platforms.
This scalability allows energy trading companies to grow their operations. This is also achieved without worrying about outgrowing their systems. It enables them to quickly respond to market changes. Thus, adopt new trading strategies as needed.
Explore the Benefits of ETRM Systems in Energy Trading
ETRM systems play a crucial role in the energy trading industry. These systems are essential for navigating the complex and dynamic landscape of energy trading. They help unlock growth opportunities for companies.
The use of ETRM systems will only increase in importance. This comes along as technology continues to advance and regulations become more stringent.
So, embracing these systems if you are looking to succeed in the energy trading market.
Should you wish to explore other topics, visit our blog page. We’ve got more posts!
REAL ESTATE
Unveiling the Significance of Fill Dirt in Construction Projects
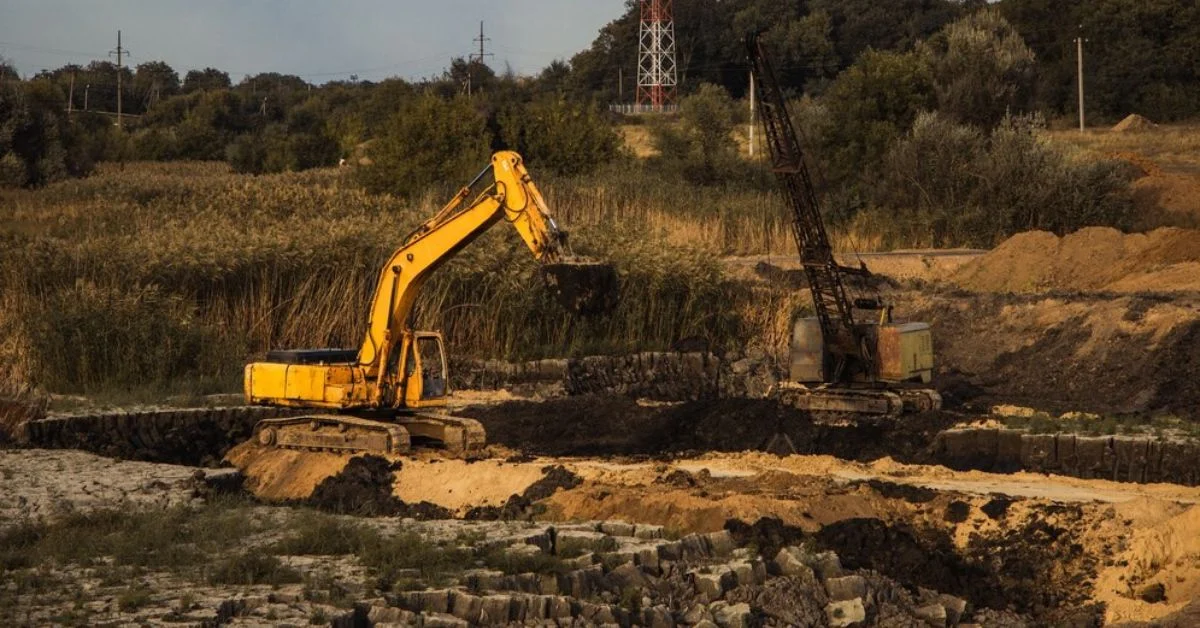
Introduction to Fill Dirt
In the realm of construction, landscaping, and environmental projects, the term “fill dirt” often emerges as a critical component. This humble material serves as the foundation for various endeavors, offering support, stability, and a plethora of other benefits. In this article, we delve into the depths of fill dirt, exploring its definition, uses, types, benefits, challenges, and much more.
What is Fill Dirt?
Definition
Fill dirt san Diego, in its simplest form, refers to the soil used to fill in depressions, level off terrain, or raise the ground’s elevation. It typically consists of soil excavated from construction sites or agricultural areas.
Composition
Fill dirt is primarily composed of soil, clay, sand, gravel, and organic matter. Its composition can vary depending on the source and location, with different ratios of these components influencing its properties.
Uses of Fill Dirt
Fill dirt finds widespread applications across various industries:
Construction
In construction projects, fill dirt is indispensable for creating a solid foundation, leveling building sites, and backfilling trenches or excavations.
Landscaping
Landscapers utilize fill dirt to sculpt the terrain, fill in low-lying areas, and create raised beds or slopes for gardens and outdoor spaces.
Environmental Projects
Fill dirt plays a crucial role in environmental restoration efforts, such as wetland mitigation, erosion control, and reclamation of disturbed sites.
Types of Fill Dirts
Several types of fill dirt are commonly used:
Topsoil
Topsoil is the uppermost layer of soil, rich in organic matter and nutrients, making it ideal for gardening and landscaping projects.
Subsoil
Subsoil lies beneath the topsoil and consists of clay, silt, and sand. While less fertile than topsoil, it provides structural support and stability.
Organic Fill
Organic fill, derived from compost or decomposed plant matter, enhances soil fertility and drainage, making it suitable for agricultural and landscaping purposes.
Benefits of Using Fill Dirts
Cost-Effectiveness
Fill dirt is often readily available at construction sites or excavation projects, reducing the need for purchasing expensive materials.
Stability and Support
Fill dirts provides a stable foundation for structures, prevents soil erosion, and minimizes the risk of foundation settlement.
Environmental Benefits
Using fill dirts from local sources reduces the environmental impact associated with transporting soil over long distances, thereby lowering carbon emissions.
How to Choose Fill Dirt
Selecting the right fill dirt is crucial for the success of any project:
Quality Assessment
Inspect the fill dirts for debris, contaminants, and proper soil composition to ensure its suitability for the intended use.
Quantity Estimation
Calculate the volume of fill dirts required based on the project’s specifications and dimensions of the area to be filled.
Source Verification
Verify the source of fill dirts to ensure compliance with local regulations and avoid potential legal issues or environmental liabilities.
Preparing and Using Fill Dirt
Proper preparation and installation techniques are essential for maximizing the benefits of fill dirt:
Site Preparation
Clear the area of vegetation, debris, and any obstructions before spreading fill dirts to ensure a smooth and even surface.
Proper Installation Techniques
Compact the fill dirts in layers using heavy machinery to achieve the desired density and stability, preventing future settlement.
Safety Considerations
While fill dirts offers numerous advantages, it also poses certain risks that must be addressed:
Environmental Impact
Improper disposal or contamination of fill dirts can harm ecosystems, pollute water sources, and disrupt natural habitats.
Soil Testing
Conduct soil tests to assess the quality and composition of fill dirts, identifying any potential contaminants or hazardous substances.
Erosion Control
Implement erosion control measures such as silt fences, vegetation barriers, and sediment ponds to prevent soil erosion and runoff.
Challenges Associated with Fill Dirt
Despite its utility, fill dirts presents certain challenges that require careful consideration:
Contamination Risks
Fill dirts sourced from industrial sites or landfills may contain pollutants, toxins, or hazardous materials that pose health and environmental risks.
Settlement Issues
Improper compaction or inadequate site preparation can lead to settlement problems, structural damage, and costly repairs.
Regulatory Compliance
Complying with local regulations, permits, and environmental standards is essential when sourcing and using fill dirts to avoid legal repercussions.
Case Studies and Examples
Explore real-world examples of fill dirts projects, highlighting successful implementations, innovative techniques, and lessons learned.
Future Trends in Fill Dirt Usage
As technology advances and environmental concerns grow, the use of sustainable fill materials, such as recycled aggregates and synthetic soils, is expected to rise.
Conclusion
In conclusion, fill dirt serves as a versatile and invaluable resource in various industries, offering solutions for construction, landscaping, and environmental challenges. By understanding its properties, applications, and considerations, stakeholders can harness the full potential of fill dirts while mitigating risks and maximizing benefits.
FAQs
What is the cost of fill dirt?
- The cost of fill dirts varies depending on factors such as location, quantity, and quality. It can range from a few dollars per cubic yard to higher prices for specialty blends or certified soil.
Can fill dirts be used for gardening?
- Fill dirts can be used for gardening, but its suitability depends on the composition and quality of the soil. Mixing fill dirt with compost or topsoil can improve its fertility and drainage for gardening purposes.
How do I know if the fill dirts is suitable for my project?
- Conduct a thorough inspection and testing of the fill dirts to assess its composition, compaction, and potential contaminants. Consulting with soil experts or engineers can also provide valuable insights into its suitability for specific projects.
Is fill dirts the same as topsoil?
- Fill dirts and topsoil are distinct types of soil with different compositions and uses. While topsoil is rich in organic matter and nutrients, fill dirts is often composed of subsoil, clay, sand, or recycled materials and is primarily used for filling and grading purposes in construction and landscaping projects.
Are there any environmental concerns associated with fill dirts?
Fill dirts sourced from contaminated sites or containing hazardous materials can pose environmental risks, including soil and water pollution, habitat destruction, and health hazards. Proper testing, sourcing, and disposal practices are essential for minimizing these concerns.
- TECHNOLOGY4 months ago
Blog Arcy Art: Where Architecture Meets Art
- ENTERTAINMENT1 week ago
Exploring the Kristen Archives: A Treasure Trove of Erotica and More
- ENTERTAINMENT4 days ago
Kiss KH: The Streaming Platform Redefining Digital Engagement and Cultural Currents
- LIFESTYLE4 months ago
The Disciplinary Wives Club: Spanking for Love, Not Punishment
- LIFESTYLE1 week ago
Who Is Sandra Orlow?
- GENERAL4 months ago
What are stories of male chastity? A Comprehensive Guide
- EDUCATION4 days ago
Lingrohub Platform: A Complete Student Access Guide
- ENTERTAINMENT4 weeks ago
MonkeyGG2: Your Personal Gaming Hub