REAL ESTATE
A Guide to Scaling Your Construction Business with the Right Tools and Equipment
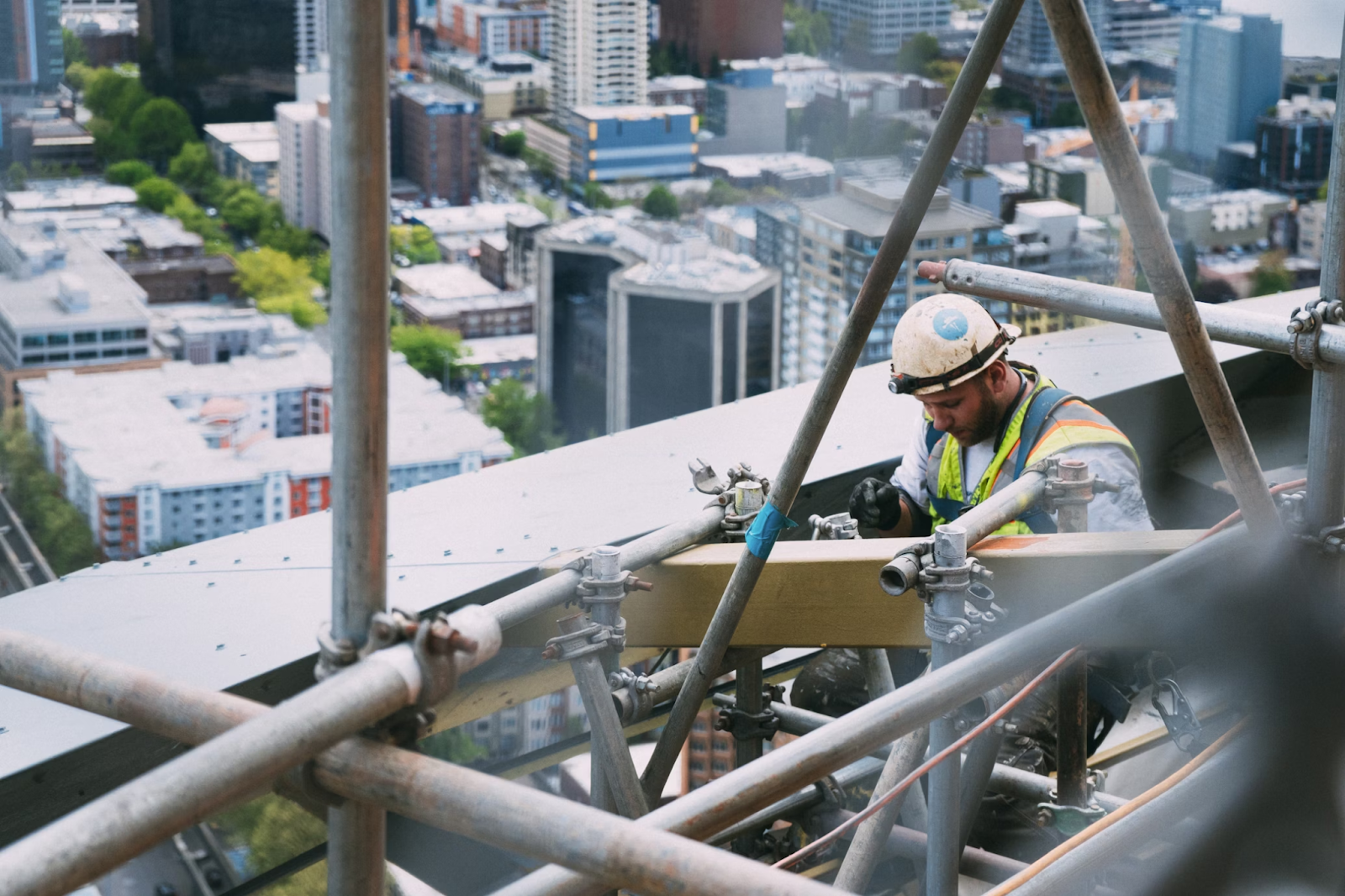
Scaling a construction business requires more than just a growing workforce or increased projects. The right tools and equipment play a pivotal role in achieving sustainable growth, improving efficiency, and maintaining competitive advantages. From advanced machinery to smart technology, investing in the proper resources can transform your operations and elevate your business.
The Importance of Proper Tools and Equipment
In the construction industry, the quality of tools and equipment directly impacts productivity and profitability. Outdated or inadequate machinery can slow projects, increase labor costs, and result in missed deadlines. Upgrading to modern, efficient tools not only improves project timelines but also enhances safety on job sites. For example, using advanced excavators, loaders, and cranes reduces manual labor and minimizes errors, ensuring projects are completed efficiently.
Investing in equipment that aligns with your business needs sets the foundation for scaling. Construction tools with enhanced capabilities enable teams to take on larger, more complex projects, positioning the business for growth in competitive markets.
Choosing the Right Heavy Machinery
Heavy machinery, such as excavators, bulldozers, and loaders, are integral to construction operations. Selecting the right models tailored to your projects can make a significant difference in performance and outcomes. Factors like fuel efficiency, capacity, durability, and ease of operation should guide your choices.
For earthmoving tasks, excavators are indispensable. Models like the John Deere 350G are popular for their balance of power and efficiency. These excavators offer advanced hydraulic systems, strong digging force, and reliability, making them ideal for large-scale projects. Consulting with experts in John Deere 350G models can help you determine if these machines meet your business’s specific needs. Choosing the right equipment ultimately ensures smoother operations and higher productivity on job sites.
The Impact of Technological Advancements
Technology continues to reshape the construction industry. Integrating modern technology into equipment and tools enhances performance, optimizes resources, and streamlines workflows. Equipment with GPS systems, telematics, and automation capabilities enables construction managers to monitor progress in real-time, reducing downtime and improving decision-making.
Smart technology also reduces operational costs. For example, telematics helps track fuel usage, machine hours, and maintenance schedules, ensuring machinery runs at peak performance. Construction businesses that embrace technological advancements experience greater efficiency and long-term cost savings, paving the way for growth.
Maintenance: A Key Factor in Equipment Longevity
Investing in high-quality tools and equipment is only the first step. Proper maintenance ensures that machinery operates efficiently and has a long lifespan. Regular inspections, preventive maintenance, and timely repairs are essential for avoiding costly breakdowns and project delays.
Partnering with experienced service providers who specialize in specific equipment can make maintenance more efficient. By following recommended service schedules and using quality replacement parts, businesses can minimize downtime and ensure consistent performance across projects. Reliable equipment translates to fewer disruptions, ultimately supporting business scalability.
Renting vs. Purchasing Equipment
Deciding whether to rent or purchase equipment depends on the scale and frequency of your projects. For businesses planning to scale operations, purchasing essential tools and machinery can be a worthwhile investment. Ownership provides long-term cost benefits and ensures availability whenever needed.
On the other hand, renting offers flexibility for businesses taking on short-term projects or testing new equipment. It reduces upfront costs, eliminates maintenance expenses, and allows access to the latest machinery models without significant financial commitment. Weighing the pros and cons of renting versus purchasing can help you make informed decisions aligned with your business strategy.
Building a Skilled Workforce
Having the right tools and equipment is only effective when paired with a skilled workforce. Proper training on machinery usage, safety protocols, and equipment maintenance enhances productivity and reduces risks on job sites. Investing in employee development ensures that your team can maximize the capabilities of advanced equipment and work efficiently.
Additionally, a trained workforce boosts morale and retention. Employees who are confident in using modern tools feel empowered to perform better, contributing to the overall growth of the business.
Financial Considerations for Equipment Investments
Scaling a construction business requires careful financial planning, especially when investing in tools and equipment. Balancing cash flow, securing financing, and exploring leasing options can help you acquire necessary resources without straining budgets.
Equipment financing options, such as loans or leases, provide flexibility for businesses looking to upgrade machinery. Additionally, understanding tax benefits like depreciation deductions can offset some costs. Partnering with financial advisors familiar with the construction industry ensures that your investments align with long-term growth goals.
Enhancing Safety and Compliance
Safety is a top priority in construction, and the right equipment plays a critical role in minimizing risks. Modern machinery often comes with enhanced safety features, such as backup cameras, automatic shutoffs, and stability controls. These features not only protect workers but also ensure compliance with industry regulations.
Staying compliant with safety standards reduces the likelihood of accidents, legal issues, and project delays. Businesses that prioritize safety create a positive work environment, earning trust from employees and clients alike—an essential aspect of scaling operations.
Leveraging Partnerships with Equipment Suppliers
Collaborating with reliable equipment suppliers and manufacturers provides access to quality tools, expert guidance, and ongoing support. Strong partnerships allow businesses to stay updated on new technologies, secure competitive pricing, and receive timely equipment servicing.
Suppliers who understand your business’s growth goals can recommend equipment tailored to specific projects, helping you make informed purchasing decisions. These partnerships ensure your business remains equipped to take on larger, more demanding projects as it scales.
The Role of Project Management Tools
Beyond physical equipment, project management tools are essential for scaling construction businesses. Software platforms that offer scheduling, budgeting, and collaboration features improve project oversight and efficiency. These tools enable managers to track resources, timelines, and expenses in real-time, ensuring projects stay on schedule and within budget.
Integrating project management solutions enhances communication between teams, clients, and stakeholders. This level of transparency and organization builds trust and supports smooth project execution, key factors in achieving sustainable growth.
Investing in the right tools and equipment is a cornerstone of scaling any construction business. From heavy machinery and smart technology to workforce training and project management tools, each resource plays a vital role in improving efficiency, safety, and profitability. By making strategic investments and fostering strong partnerships, construction businesses can position themselves for long-term success in a competitive industry.
BUSINESS
Limestone Commercial Real Estate Houston: Unveiling Opportunities
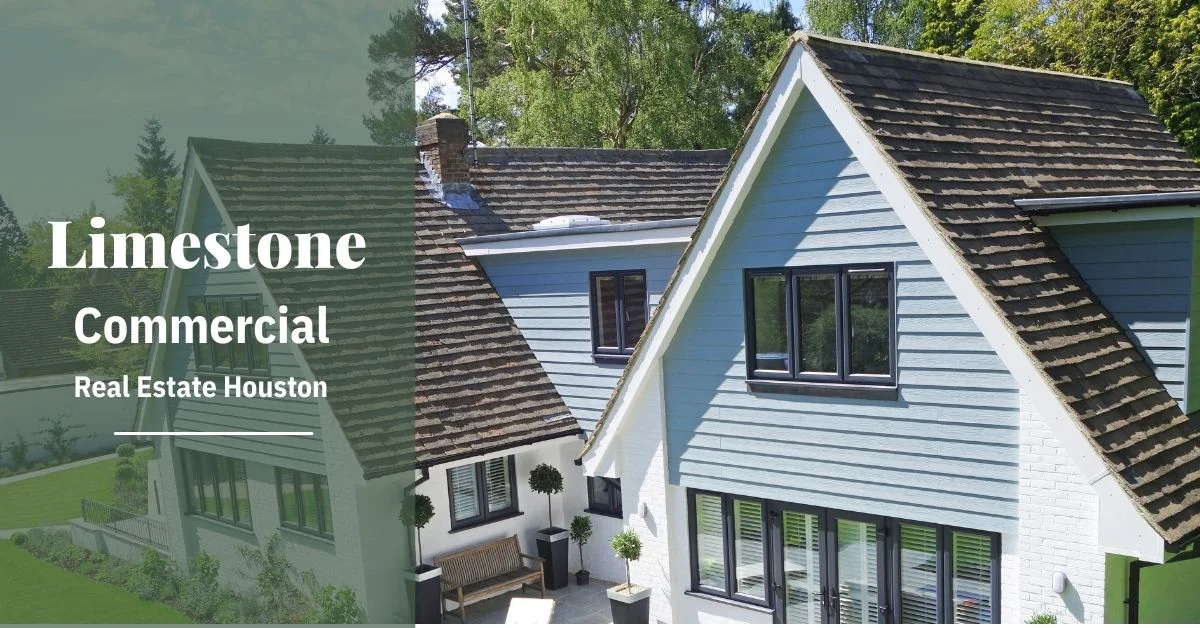
Welcome to the heart of Texas, where the dynamic landscape of Houston’s commercial real estate is undergoing a transformative shift, with limestone taking center stage. In this article, we will delve into the nuances of limestone commercial real estate in Houston, exploring its properties, growth trends, investment advantages, and potential challenges. So, buckle up as we embark on a journey through the vibrant world of limestone investments.
Introduction
Definition of Limestone in Commercial Real Estate
Limestone, a sedimentary rock rich in calcium carbonate, is not just a geological wonder but a key player in the realm of commercial real estate. Its unique characteristics make it a sought-after material for various construction projects.
Importance of Limestone in Houston
Houston’s bustling real estate scene has found a reliable ally in limestone. From towering skyscrapers to sustainable housing projects, the city’s landscape is shaped by the versatility of this rock.
Limestone Properties in Houston
Geographic Distribution
The sprawling geographic distribution of limestone deposits in and around Houston sets the stage for a diverse array of real estate opportunities. Understanding the regional variations is crucial for savvy investors.
Unique Features
What makes Houston’s limestone distinct? Explore the unique features that contribute to its appeal in the commercial real estate sector, from aesthetic qualities to structural strength.
Economic Impact
Beyond aesthetics, limestone brings substantial economic benefits. Unpack the economic impact of limestone in Houston, influencing job markets, property values, and community development.
ALSO READ: TOP SERVICES FOR BUILDERS TO SELL MORE HOMES
Growth Trends in Limestone Commercial Real Estate
Historical Perspective
Tracing the roots of limestone’s involvement in Houston’s real estate provides valuable insights into its journey. Historical trends lay the foundation for predicting future growth.
Current Market Trends
In a rapidly evolving market, staying abreast of current trends is paramount. Discover the latest market dynamics influencing limestone commercial real estate in Houston.
Future Projections
What does the future hold for limestone investments? Delve into projections and forecasts that shed light on potential opportunities and challenges on the horizon.
Advantages of Investing in Limestone Commercial Real Estate
Durability and Longevity
Limestone’s reputation for durability and longevity makes it a preferred choice for investors seeking sustainable and low-maintenance properties.
Environmental Considerations
As environmental consciousness rises, limestone’s eco-friendly attributes become a driving force in real estate decisions. Explore how sustainable practices contribute to a positive investment outlook.
Cost-Effectiveness
Balancing the books is crucial in real estate. Uncover the cost-effectiveness of limestone projects, providing investors with a favorable return on investment.
ALSO READ: CHOICE HOME WARRANTY GEORGE FOREMAN: PROTECTING YOUR HOME WITH STRENGTH AND ASSURANCE
Challenges and Considerations
Regulatory Compliance
Navigating regulatory landscapes is a challenge in any industry. Understand the regulatory considerations specific to limestone commercial real estate in Houston.
Market Fluctuations
Like any investment, limestone real estate is not immune to market fluctuations. Learn strategies to mitigate risks associated with economic uncertainties.
Environmental Impact Assessment
Scrutinizing the environmental impact of limestone projects is vital. Investors need to evaluate the ecological consequences and ensure responsible development practices.
Successful Case Studies
Notable Limestone Commercial Real Estate Projects
Dive into successful case studies that showcase the transformative power of limestone in real estate. From urban revitalization to sustainable development, these projects inspire future endeavors.
Impact on Local Communities
Limestone investments extend beyond financial gains, impacting local communities positively. Explore how these projects contribute to community development, employment, and overall well-being.
Lessons Learned
Reflect on lessons learned from past projects, providing invaluable insights for prospective investors looking to embark on their limestone real estate journey.
Expert Insights
Interviews with Industry Experts
Gain wisdom from industry experts through exclusive interviews. Experts share their perspectives on current trends, potential challenges, and the untapped opportunities within the limestone real estate sector.
Recommendations for Investors
Guidance from seasoned investors can be a game-changer. Discover recommendations and best practices for investors venturing into the dynamic world of limestone commercial real estate.
Future Opportunities
Peek into the crystal ball as experts share their views on future opportunities within the limestone real estate market, helping investors position themselves strategically.
ALSO READ: INDUSTRY TRENDS AND INNOVATIONS IN RV RENTAL MANAGEMENT
Tips for Navigating Limestone Real Estate Investments
Research and Due Diligence
Successful investments hinge on thorough research and due diligence. Explore strategies to effectively navigate the complex landscape of limestone real estate.
Working with Industry Professionals
Collaboration is key. Learn the importance of working with industry professionals, from geologists to real estate agents, to ensure a successful limestone investment journey.
Mitigating Risks
Risk management is at the forefront of savvy investing. Uncover effective ways to mitigate risks associated with limestone commercial real estate projects.
Conclusion
Recap of Key Points
In conclusion, our exploration of limestone commercial real estate in Houston has revealed a landscape rich in opportunities. Recap key points and insights gained throughout this article.
Encouragement for Investors
To the aspiring investors eyeing limestone projects in Houston, take heart. The city’s vibrant real estate scene, combined with the enduring qualities of limestone, presents a promising canvas for your investment endeavors.
ALSO READ: HOW SURETY BONDS WORK AND WHY YOU MIGHT NEED ONE
FAQs
What factors drive the demand for limestone commercial real estate?
The demand for limestone commercial real estate is driven by factors such as its durability, aesthetic appeal, and sustainability. Investors seek properties with long-term value and minimal maintenance, making limestone an attractive choice.
How can investors assess the geological suitability of a limestone property?
Geological assessments are crucial. Investors should enlist the expertise of geologists to evaluate factors like rock quality, stability, and potential environmental impact before making investment decisions.
Are there government incentives for investing in sustainable limestone projects?
Yes, many governments offer incentives for sustainable development projects, including those involving limestone. Investors can explore tax credits, grants, and other incentives that promote environmentally conscious real estate initiatives.
What role does technology play in the development of limestone commercial real estate?
Technology plays a significant role in the development of limestone commercial real estate, from advanced quarrying methods to sustainable construction practices. Innovations in technology contribute to more efficient and eco-friendly projects.
How can local communities benefit from limestone real estate projects?
Limestone projects can bring about positive changes in local communities by creating job opportunities, supporting infrastructure development, and contributing to overall community well-being. These projects often become integral parts of the community fabric.
BUSINESS
Limestone Commercial Real Estate Reviews
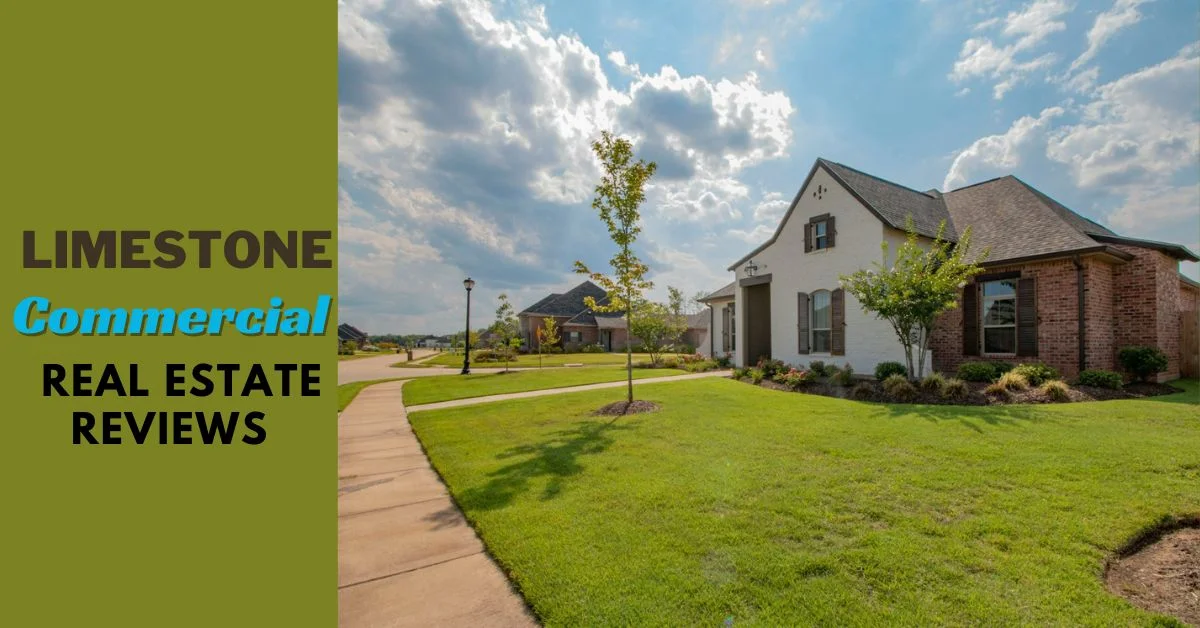
Introduction
Welcome to the world where timeless elegance meets enduring strength—Limestone Commercial Real Estate Reviews. In the dynamic landscape of architectural design and construction, certain materials stand out not just for their aesthetic appeal but also for their ability to define spaces that withstand the test of time. Limestone, a sedimentary rock formed over millennia, emerges as a stalwart companion in the realm of commercial real estate.
Limestone Commercial Real Estate Reviews: As we embark on this journey through the nuances and applications of limestone, it’s essential to grasp the foundational significance of this natural stone. Limestone is not merely a building material; it’s a narrative etched in the earth’s geological history. Its unique characteristics make it a favorite among architects, developers, and designers seeking a material that seamlessly blends functionality, aesthetics, and sustainability.
Importance of Limestone Commercial Real Estate Reviews
Durability and Long-Lasting Properties
Limestone’s significance in commercial real estate is underscored by its exceptional durability and long-lasting properties. Unlike synthetic materials that may degrade over time, limestone stands as a resilient choice, capable of enduring various environmental factors. This durability is especially crucial in commercial structures, where longevity is a key consideration for investors and developers.
The inherent strength of limestone ensures that it can withstand the rigors of daily use, making it an ideal material for high-traffic areas such as lobbies, corridors, and public spaces within commercial buildings. Its ability to resist wear and tear, maintaining its structural integrity over the years, contributes to the long-term value of the property.
Aesthetic Appeal and Design Versatility
Beyond its physical robustness, limestone’s aesthetic appeal and design versatility play a pivotal role in its importance within commercial real estate. Architects and designers appreciate the diverse palette that limestone offers, ranging from warm cream tones to cool gray hues. This versatility allows for the creation of structures that seamlessly integrate with their surroundings and architectural styles.
The aesthetic appeal of limestone extends beyond its color range to include intricate natural patterns and textures. Whether used for exterior facades or interior flooring, limestone adds a touch of sophistication and timeless elegance. Its visual appeal is not only pleasing to the eye but also contributes to the overall ambiance of commercial spaces.
In the competitive landscape of commercial real estate, the first impression matters. Limestone provides developers with a material that not only withstands the test of time but also enhances the visual allure of the property. This dual combination of durability and aesthetics positions limestone as a cornerstone in the construction and design of successful commercial real estate projects.
ALSO READ: REALESTATEVIEW: REVOLUTIONIZING PROPERTY SEARCHES
Limestone Commercial Real Estate Reviews Applications
Exterior Facades and Landscaping
Limestone Commercial Real Estate Reviews: Limestone’s application in exterior facades and landscaping further emphasizes its importance in commercial real estate. The stone’s ability to be cut and shaped into various forms allows architects to create striking facades that capture attention. From grand corporate buildings to boutique retail spaces, limestone exteriors convey a sense of permanence and sophistication.
Landscaping with limestone accents not only enhances the aesthetics of the surroundings but also provides a cohesive visual language between the building and its environment. Whether used for pathways, garden borders, or ornamental features, limestone in landscaping adds a touch of natural luxury, creating an inviting atmosphere for visitors and tenants alike.
Interior Flooring and Wall Cladding
Limestone Commercial Real Estate Reviews: Limestone’s significance extends seamlessly to the interiors of commercial real estate. As a flooring material, it brings a sense of timeless luxury. The natural variation in color and pattern ensures that each floor is unique, contributing to a bespoke interior design. In high-traffic areas such as shopping centers and corporate lobbies, limestone flooring not only withstands heavy use but also exudes an air of refinement.
Wall cladding with limestone adds depth and texture to interior spaces. Whether used in expansive atriums or as accent walls in meeting rooms, limestone imparts a sense of grandeur and sophistication. Its ability to complement various design styles, from classical to contemporary, makes it a versatile choice for interior applications.
The importance of limestone in these applications lies not only in its aesthetic contributions but also in its practicality. Limestone’s durability ensures that it can endure the challenges posed by both interior and exterior environments, making it a valuable investment for commercial properties.
Benefits of Choosing Limestone for Real Estate Projects
Sustainability and Environmental Considerations
One of the key benefits underscoring the importance of Limestone Commercial Real Estate Reviews is its sustainability and positive environmental impact. Limestone is a natural material formed over millions of years through geological processes, making it an inherently eco-friendly choice compared to synthetic alternatives.
The extraction and production of limestone typically have a lower environmental footprint, contributing to a more sustainable construction industry. Furthermore, the availability of locally sourced limestone reduces transportation-related carbon emissions, aligning with the growing demand for environmentally responsible building materials.
Limestone’s sustainability extends beyond its initial use. When a building reaches the end of its lifecycle, limestone can often be recycled or repurposed, minimizing waste and further contributing to a circular and sustainable construction economy.
Low Maintenance and Cost-Effectiveness
Practicality and cost-effectiveness are paramount considerations in commercial real estate, and limestone excels in these aspects. The low maintenance requirements of limestone make it an attractive choice for property developers. Regular cleaning with mild detergents and periodic sealing are typically sufficient to keep limestone surfaces looking pristine.
While the initial investment in limestone may be higher than some synthetic alternatives, its long-term cost-effectiveness becomes evident over time. The durability and resilience of limestone result in reduced maintenance costs and a prolonged lifespan, making it a financially sound choice for commercial real estate projects.
The combination of sustainability, low maintenance, and cost-effectiveness positions limestone as a strategic and impactful choice for developers seeking both aesthetic appeal and long-term value in their real estate investments.
ALSO READ: CHOICE HOME WARRANTY GEORGE FOREMAN: PROTECTING YOUR HOME WITH STRENGTH AND ASSURANCE
Popular Limestone Types in Commercial Real Estate
Cream-Colored Limestone
Cream-colored limestone stands out as a popular choice in commercial real estate for its warm and inviting appearance. The subtle tones and natural variations in color create a sense of elegance, making it well-suited for a range of applications. From corporate office buildings to upscale retail spaces, cream-colored limestone lends a touch of sophistication and timelessness.
Gray Limestone
The versatility of gray limestone makes it a go-to option for architects and designers. Its neutral color complements various architectural styles, allowing for seamless integration into both modern and traditional designs. Gray limestone is often chosen for its understated yet impactful aesthetic, making it suitable for diverse commercial settings.
Blue Limestone
For those seeking a distinctive and bold look, blue limestone is a captivating choice. The deep blue hues and unique patterns make it an attention-grabbing material, particularly when used as an accent in interior spaces or as a focal point in exterior landscaping. Blue limestone adds a touch of individuality and modernity to commercial real estate projects.
The availability of these diverse limestone types allows developers to tailor their material selection to the specific design vision and requirements of each project. The popularity of these variations underscores the adaptability and aesthetic richness that limestone brings to commercial real estate.
Case Studies: Successful Limestone Commercial Real Estate Projects
Highlighting Specific Projects and Their Success Stories
In this section, we’ll delve into real-world examples of how limestone has been successfully utilized in commercial real estate projects, showcasing its transformative impact.
Case Study 1: The Timeless Facade of Corporate Elegance
Location: Financial District, New York City
Project Type: Corporate Office Building
Architect: [Architectural Firm XYZ]
In the heart of the bustling Financial District, a corporate office building stands as a testament to the enduring allure of limestone. The exterior facade, adorned with cream-colored limestone panels, exudes elegance and sophistication. The choice of limestone not only elevated the building’s aesthetic appeal but also contributed to a sense of permanence and prestige, crucial in the competitive world of corporate real estate.
Client Testimonial:
The limestone facade has become a distinctive feature of our corporate identity. It not only sets us apart but also communicates a sense of reliability and longevity to our clients and employees.” – Brandi Mcdonald
Case Study 2: Retail Resplendence with Gray Limestone
Location: Luxury Shopping Center, Beverly Hills
Project Type: High-End Retail Complex
Architect: [Renowned Architect ABC]
In the world of luxury retail, first impressions are everything. This retail complex in Beverly Hills opted for gray limestone flooring, creating a seamless blend of opulence and durability. The natural patterns of the gray limestone not only added visual interest but also proved resilient against the high foot traffic typical in a bustling shopping environment.
Client Testimonial:
Our choice of gray limestone was strategic. Beyond its aesthetic appeal, it has proven to be a low-maintenance and durable solution for our high-end retail spaces, ensuring our stores always look impeccable.” – Brandi McDonald Sikes
Case Study 3: Blue Limestone in Contemporary Hospitality
Location: Boutique Hotel, Miami
Project Type: Boutique Hotel Renovation
Designer: [Interior Design Studio PQR]
In the competitive hospitality industry, creating a unique atmosphere is key. The renovation of this boutique hotel in Miami incorporated blue limestone accents in the lobby and common areas. The result was a contemporary and visually striking ambiance that resonated with modern travelers, setting the hotel apart from its competitors.
Client Testimonial:
The blue limestone elements have become a focal point of our hotel’s design. It’s a conversation starter and has significantly contributed to positive reviews and guest satisfaction.” – Brandi McDonald Sikes
These case studies exemplify the versatility and impact of limestone in diverse commercial real estate settings. From corporate offices to retail spaces and boutique hotels, limestone continues to shape the narrative of success in the world of architecture and design.
ALSO READ: EMPOWERING YOUR FINANCIAL JOURNEY: THE COMPREHENSIVE GUIDE TO IN HOUSE FINANCING
Challenges and Considerations
Potential Challenges in Using Limestone
While the success stories of limestone in commercial real estate are inspiring, it’s crucial to address potential challenges that may arise during its utilization.
Limestone, being a natural material, can be susceptible to certain acids found in rainwater or pollutants. This susceptibility may lead to erosion over time, affecting the appearance of the stone. Developers and architects need to be aware of these potential challenges to ensure the long-term integrity of their projects.
Strategies to Overcome Challenges
Understanding the challenges is only the first step; the next is implementing strategies to overcome them. Coating limestone surfaces with protective sealants is an effective preventive measure against acid-related erosion. Additionally, selecting appropriate cleaning agents and conducting regular inspections can help identify and address potential issues before they escalate.
Project teams need to collaborate with experienced geologists and stone experts to choose the right type of limestone for specific applications. This proactive approach ensures that the chosen limestone is well-suited to the environmental conditions of the project site, minimizing potential challenges.
Tips for Maintenance and Care
Regular Cleaning and Sealing
Limestone Commercial Real Estate Reviews: To maintain the pristine appearance of limestone in commercial real estate, regular cleaning is paramount. Using mild detergents and soft brushes removes accumulated dust and pollutants. Periodic sealing serves as a protective barrier, preventing stains and enhancing the stone’s longevity.
Addressing Common Issues like Stains and Discoloration
Despite preventative measures, occasional stains or discoloration may occur. Quick action is key in these situations. Employing gentle cleaning solutions specific to limestone and avoiding abrasive chemicals can help address stains without compromising the stone’s natural beauty.
In cases where stains prove challenging, seeking professional cleaning services specialized in natural stone maintenance is advisable. These professionals possess the expertise and tools to handle more complex issues, ensuring the continued elegance of limestone surfaces.
Future Trends in Limestone Commercial Real Estate
Emerging Design Trends
As the world of architecture evolves, so do the design trends associated with limestone in commercial real estate. Architects and developers are increasingly exploring innovative ways to incorporate limestone beyond traditional uses. From sculptural elements to intricate patterns, the versatility of limestone allows for unique and dynamic design expressions.
Moreover, there is a growing trend towards combining limestone with other materials, creating juxtapositions that highlight the stone’s natural beauty while embracing modern aesthetics. This fusion of traditional and contemporary design elements not only adds visual interest but also caters to diverse architectural preferences.
Sustainable and Eco-Friendly Innovations
Sustainability is at the forefront of design considerations, and limestone aligns seamlessly with eco-friendly initiatives. The industry is witnessing a surge in demand for locally sourced limestone, reducing transportation-related carbon emissions. Additionally, advancements in extraction techniques and waste reduction contribute to making limestone a more environmentally responsible choice in commercial real estate.
Innovations in sustainable construction practices, such as utilizing reclaimed limestone from existing structures, further emphasize the industry’s commitment to reducing its ecological footprint. As environmental awareness continues to grow, expect to see more commercial real estate projects adopting sustainable limestone solutions.
ALSO READ: THE ART OF BRAND COMMUNICATION: BUILDING STRONG CONNECTIONS
Client Testimonials
Real Experiences from Businesses Using Limestone in Real Estate
Incorporating client testimonials provides valuable insights into the real-world impact of limestone on commercial properties.
Testimonial 1:
“Our decision to use limestone in our office building not only met our aesthetic expectations but also proved to be a wise investment. The durability and timeless appeal have elevated our brand image, positively influencing clients and employees alike.” –
Testimonial 2:
“The choice of limestone flooring in our retail space has exceeded our expectations. It not only adds a touch of luxury but also requires minimal maintenance, ensuring our focus remains on delivering an exceptional shopping experience.” – Brandi McDonald Sikes.
Expert Opinions and Quotes
Insights from Architects and Designers
Limestone Commercial Real Estate Reviews: Engaging with architects and designers provides a deeper understanding of the thought processes behind the strategic use of limestone in commercial real estate.
Architect XYZ:
“Limestone’s versatility is unparalleled. It allows us to create seamless transitions between interior and exterior spaces, fostering a sense of continuity and harmony within the built environment. Its timeless aesthetic ensures that our designs stand the test of time.”
Designer ABC:
“Incorporating limestone into our projects goes beyond aesthetics; it’s about creating a sensory experience. The natural textures and variations add a tactile element, connecting occupants with the essence of the material. It’s a design choice that resonates on multiple levels.”
These expert insights underline the intentional and thoughtful approach architects and designers take when integrating limestone into commercial real estate projects. The emphasis on continuity, timelessness, and sensory experience showcases the depth of consideration given to the material’s impact on the overall design.
Comparative Analysis with Other Building Materials
Pros and Cons of Limestone Compared to Alternatives
Understanding how limestone stacks up against other building materials is crucial for informed decision-making in commercial real estate.
Pros of Limestone:
- Aesthetic Versatility: Limestone offers a broad spectrum of colors and textures, allowing for diverse design possibilities.
- Durability: Its natural strength ensures longevity, making it a reliable choice for high-traffic areas.
- Sustainability: Limestone’s natural composition and local sourcing options contribute to eco-friendly construction practices.
Cons of Limestone:
- Susceptibility to Acids: Acidic substances can impact limestone, necessitating proper maintenance.
- Initial Cost: While long-term cost-effective, the initial investment in limestone may be higher than some synthetic alternatives.
Comparing these aspects with alternatives such as marble or synthetic materials empowers developers to make choices aligned with their project goals and budget considerations.
ALSO READ: TOP SERVICES FOR BUILDERS TO SELL MORE HOMES
Limestone Real Estate Market Overview
Current Market Trends
Analyzing current market trends in limestone commercial real estate unveils dynamic shifts in consumer preferences and industry practices. The increasing demand for sustainable and locally sourced materials is reshaping the market landscape.
Projected Growth and Opportunities
Projections indicate a continued growth in the demand for limestone in commercial real estate. As sustainable practices gain traction, the market presents opportunities for businesses that prioritize environmentally responsible construction solutions.
Conclusion
In conclusion, the journey through the world of limestone in commercial real estate has been one of exploration and revelation. From its historical significance to its modern applications, limestone has proven to be more than just a building material—it’s a cornerstone for success in architectural design.
The case studies highlighted the transformative impact of limestone in diverse commercial projects, showcasing its adaptability and enduring charm. As we navigated through potential challenges, maintenance tips, and glimpses into the future trends, it became evident that limestone’s journey is an ongoing narrative of innovation and sustainability.
Expert opinions emphasized the thoughtful integration of limestone by architects and designers, acknowledging its unique ability to create both visual and sensory experiences. The comparative analysis shed light on the pros and cons, guiding developers towards informed decisions tailored to their specific project requirements.
The limestone real estate market overview revealed a promising future, with sustainability taking center stage. As businesses seek environmentally friendly solutions, limestone emerges as a key player, aligning with the growing demand for responsible construction practices.
In essence, limestone in commercial real estate is not just about structures; it’s about storytelling through architecture. It’s about creating spaces that stand as a testament to durability, aesthetics, and environmental consciousness. As the market continues to evolve, limestone remains a timeless choice, shaping the skylines of our cities and leaving an indelible mark on the landscape of commercial real estate.
ALSO READ: INDUSTRY TRENDS AND INNOVATIONS IN RV RENTAL MANAGEMENT
FAQs
Q: How does limestone enhance the value of commercial properties?
Limestone’s durability and timeless aesthetics contribute to an increased perceived value of commercial properties, attracting potential buyers and tenants.
Q: Are there any disadvantages of using limestone in real estate?
While rare, potential challenges include susceptibility to certain acids and the need for proper maintenance to preserve its appearance.
Q: What maintenance steps are essential for limestone in commercial real estate?
Regular cleaning and periodic sealing are crucial to maintain the pristine appearance of limestone surfaces in commercial real estate.
Q: How can businesses stay updated on the latest trends in limestone real estate?
Keeping abreast of architectural publications, attending industry events, and consulting with experienced designers can help businesses stay informed about the latest trends.
Q: Where can I find reliable suppliers for limestone in real estate projects?
Reputable stone suppliers, architectural firms, and industry trade shows are excellent sources for connecting with reliable limestone suppliers for real estate projects.
BUSINESS
10 Tips For Planning a Commercial Building Renovation
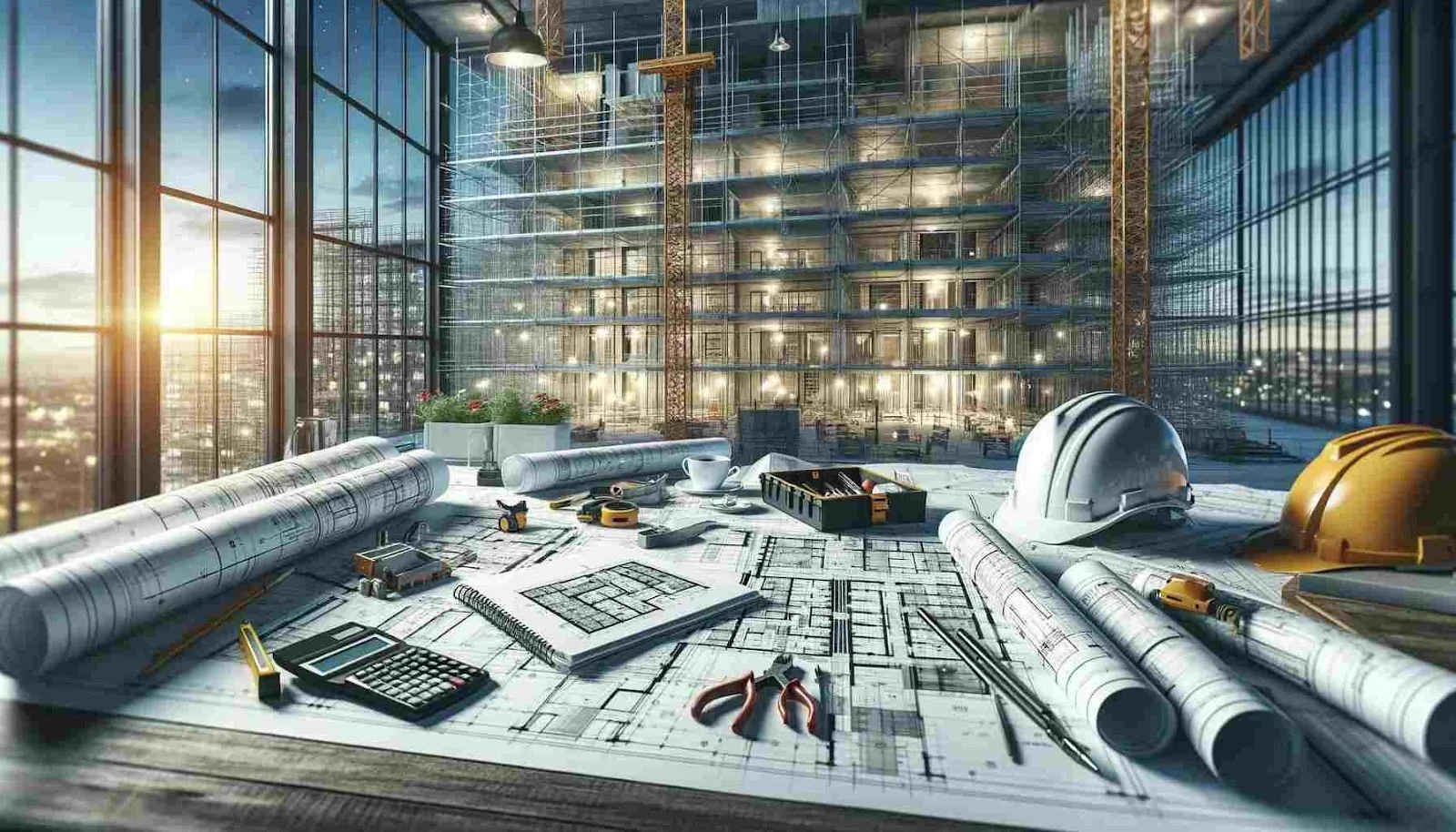
Introduction:
Starting to renovate a business building is like starting a journey: you need to carefully plan your route, have a clear idea of where you want to go, and have a reliable map to help you get there. It can be hard to figure out how to redesign an office, a store, or an industrial building. Don’t worry, though! This comprehensive guide is your reliable partner, giving you clear instructions and useful information to help you handle all the challenges of your Commercial Building Renovation project.
1. Assessing Needs and Goals
Before you start renovating a business building, you need to know why you’re doing it and what you want to achieve. In this case:
Understanding the Purpose of Renovation: Before making commercial building renovation plans, it’s important to know why the job is being done. Are you trying to bring the building up to date, make it more useful, or make it look better? Knowing the reason for the makeover will help you make decisions along the way.
Identifying Key Objectives and Priorities: After figuring out the renovation’s purpose, it’s time to set clear goals and order of importance. This could mean doing things like making better use of room, updating infrastructure, or meeting compliance standards. Setting these goals in order of importance makes sure that resources are used well.
2. Budgeting and Financing
To finance the renovation of a commercial building, you need to carefully weigh the costs and funding choices available:
Estimating Costs and Expenses: First, list all the costs and fees you expect to have for the renovation. This includes things like labor, supplies, permits, and fees for professionals. For making a reasonable budget, it’s important to get the costs right.
Exploring Financing Options: Once you know how much the renovations will cost, look into your choices for paying for the project. This could mean getting loans, looking for business partners, or using money from inside the company. Picking the right financing choice is important to make sure the project stays within its means.
3. Legal and Regulatory Considerations
To ensure compliance and avoid possible failures, it’s important to know how to navigate the legal and regulatory landscape:
Obtaining Necessary Permits and Approvals: Get all the permits and approvals you need from the local government before you start any renovations. This could include things like building permits, zoning approvals, and environmental clearances. Not getting the right licenses can cause delays and fines that cost a lot of money.
Compliance with Building Codes and Regulations: Make sure that the renovation job follows all applicable safety, building, and regulatory rules. This includes following the rules for structure, electricity, plumbing, and mobility. Working together with legal counsel and regulatory experts can make it easier to deal with tricky compliance problems.
4. Hiring Professionals
Building a skilled team of professionals is crucial for the success of a commercial renovation project:
Selecting an Architect and Design Team: Work with a skilled architect and design team to come up with ideas that match your goals and vision for the renovation. Pick professionals who have worked on business projects before and have a creative way of designing things.
Hiring Contractors and Subcontractors: Choose contractors and subcontractors with good reputations to do the remodeling work quickly and well. You should make sure that they have the skills and experience that are needed for your job. A relationship needs to be able to communicate clearly and trust each other.
If you live in Sacramento, CA, collaborating with Boulevard Construction for high-quality Commercial Building Renovation services is a wise decision. Boulevard Construction is known for its experience and dependability, and it provides customized refurbishment solutions.
Boulevard building works with Red Hawk, which specializes in 24/7 CCTV surveillance services for construction zones. Their innovative technology ensures continuous site surveillance, preventing theft, vandalism, and equipment idle concerns. Boulevard Construction and Red Hawk work together to ensure smooth project execution while effectively meeting the different needs of their customers. With this formidable cooperation, you can be confident that your Commercial Building Renovation project in Sacramento will be handled expertly.
5. Creating a Timeline
Making a realistic schedule is important for managing the renovation project well:
Establishing Milestones and Deadlines: Divide the remodeling project into manageable steps and give each one a reasonable due date. This gives a plan for how things will go and makes it easy to keep an eye on project deadlines. Demolition, building work, installations, and finishing touches are all examples of milestones.
Anticipating Potential Delays and Challenges: Renovation projects often have problems and delays that were not planned for, even when they are well thought out. Plan for problems that might come up, like bad weather, problems in the supply chain, or problems with the law, and include backup plans in the timeline. Being able to bend and change is important for getting past unexpected setbacks.
6. Structural Assessment
It is important to check the building’s structural stability in order to find any underlying problems:
Evaluating the Condition of the Building: Perform a thorough inspection of the building’s structural parts, such as the base, walls, roof, and support systems. Find any signs of damage, wear and tear, or structural problems that might need to be fixed during the makeover.
Addressing Structural Issues and Concerns: Once structural problems are found, work with engineers and building experts to come up with solutions and make any repairs or additions that are needed. To make the building safer and more stable, structural changes might include fixing the foundation, making the walls stronger, or replacing the roof.
7. Design and Layout
A good renovation starts with a design that is both useful and nice to look at:
Developing a Functional and Aesthetic Plan: Work with the design team to come up with a makeover plan that looks good and works well. Think about things like how you use the room, how well your workflow works, your brand, and how your customers feel. Try to come up with a design that makes the commercial area look better and be easier to use.
Incorporating Sustainable and Energy-Efficient Features: Adopt sustainable design principles and include energy-saving features in your plans for renovations. This could include lights, HVAC systems, insulation, and materials that can be used again and again. Sustainable design not only has less of an effect on the environment, but it also lowers prices and makes people more comfortable.
8. Material Selection
Choosing the right materials is essential for achieving durability, performance, and cost-effectiveness:
Choosing Durable and High-Quality Materials: Choose materials that will last, can handle being bent, and can be used in business settings. Take into account things like strength, durability, upkeep needs, and how it looks. Purchase high-quality materials that can stand up to daily use and help the renovated area last a long time.
Balancing Cost and Performance: Quality is important, but it’s also important to think about efficiency, budget, and the cost of the materials. Look into value engineering and other cost-effective options that will still meet the needs of the project without lowering the standard. Give priority to materials that are the best mix of long-lasting, useful, and affordable.
9. Communication and Collaboration
Communication and teamwork that work well are necessary for a project to go smoothly:
Maintaining Open Channels of Communication: Encourage everyone involved in the renovation job to talk to each other in an open and honest way. Set up regular ways to share comments, updates, and progress reports. Get everyone on the team to participate and give their opinion so that problems can be fixed quickly and the project stays on track.
Coordinating Efforts Amongst Team Members: Make sure that architects, contractors, subcontractors, suppliers, and other project players know what they need to do and how to do it. Make jobs, expectations, and deadlines clear so that everyone is on the same page with the project goals. Encourage people to work together and as a team to solve problems and achieve goals.
10. Safety and Risk Management
To protect workers, residents, and the project itself, safety must come first:
Implementing Safety Protocols and Procedures: To lower the chance of accidents and injuries on the job site, make and follow thorough safety rules and guidelines. Give all of your staff the right training, safety gear, and information about safety. Check the work spot often for possible dangers and take care of any safety issues right away.
Mitigating Risks During the Renovation Process: Find out what risks and dangers the renovation job might bring, like unstable structures, dangerous materials, or environmental issues. To deal with these problems before they happen, make risk reduction strategies and backup plans. Be alert and flexible to deal with risks you didn’t expect and make sure the makeover goes smoothly and safely.
Conclusion:
In conclusion, planning a renovation for a business building is a complicated process that needs careful thought, teamwork, and smart decisions. Project stakeholders can overcome problems and reach their renovation goals by figuring out their needs and goals, making a good budget, following the law, putting together a skilled team, setting a realistic timeline, checking the structure’s integrity, designing carefully, choosing the right materials, communicating well, and putting safety first. Commercial renovations can turn old areas into modern, useful, and environmentally friendly places that meet the needs of both the people who live there and the people who have a stake in the project.
ALSO READ: 25PR.COM
Frequently Asked Questions (FAQs):
1. Why should I renovate my commercial building?
Many good things can come from renovating a commercial building, such as bringing old areas up to date, making it more useful, making it look better, raising the property value, attracting tenants or customers, following the rules, and lowering costs by making energy-efficient improvements.
2. How do I determine if my commercial building needs renovation?
Outdated design or amenities, poor usefulness, inefficient use of space, structural problems, safety concerns, code violations, falling occupancy rates, or changes in business needs or industry standards are all signs that your commercial building may need to be renovated.
3. What factors should I consider when budgeting for a renovation?
When making a renovation budget, you should think about the amount of work that needs to be done, the cost of materials and labor, professional fees, permits and approvals, funding options, and emergency funds in case costs come up out of the blue, and the desired return on investment (ROI).
4. How can I finance a commercial building renovation?
You can use your own money, loans from banks or the Small Business Administration (SBA), business mortgages, investor partnerships, crowdfunding, or loans from banks or the SBA to fix up a commercial building.
5. What legal and regulatory considerations are involved in a commercial renovation?
For a commercial renovation, legal and regulatory issues to think about include getting the right permits and approvals, following building codes, zoning laws, environmental laws, accessibility standards, historic preservation rules, and contractual obligations with tenants or stakeholders.
6. How do I select the right professionals for a commercial renovation project?
When hiring professionals for a commercial renovation, look for architects, designers, engineers, contractors, subcontractors, and consultants who have worked on similar projects before, have the right licenses and certifications, and have good references or reviews.
7. How long does a commercial building renovation typically take?
How long it takes to renovate a commercial building relies on many things, including the size and complexity of the project, the amount of work that needs to be done, the availability of materials and labor, the weather, getting permission from the government, and any delays that were not planned for. It can take anywhere from a few months to over a year to do renovations.
8. How do I ensure safety during a commercial renovation?
To make sure everyone is safe during a commercial renovation, you should follow thorough safety protocols and procedures, give workers the right training and personal protective equipment (PPE), do regular safety checks, get rid of any potential dangers, and follow all occupational health and safety laws.
9. What are some common challenges faced during a commercial renovation?
Problems that often happen during business renovations include going over budget, being late, making changes to the design, finding unplanned structural problems, problems with the supply chain, government rules, trouble communicating, disagreements with stakeholders, and managing a lot of different contractors and subcontractors.
10. How can I maximize the ROI of my commercial building renovation?
To get the best return on investment (ROI) from a commercial building renovation, focus on making changes that raise the property value, bring in new tenants or customers, make the building more energy efficient, lower running costs, follow the rules, make the building look better from the street, and fit with long-term business goals and market trends.
- GENERAL1 month ago
5 Factors That Affect Tattoo Removal Success
- ENTERTAINMENT2 months ago
Exploring the Kristen Archives: A Treasure Trove of Erotica and More
- LIFESTYLE6 months ago
The Disciplinary Wives Club: Spanking for Love, Not Punishment
- TECHNOLOGY5 months ago
Blog Arcy Art: Where Architecture Meets Art
- LIFESTYLE2 days ago
Who Is Sandra Orlow?
- ENTERTAINMENT7 months ago
The Ultimate Guide to Shillong Teer Hit Number: How to Predict Your Next Win
- LIFESTYLE3 months ago
Berniece Julien: The Private Life of Tyson Beckford’s Partner
- GENERAL8 months ago
Worldwide Elephant List: Complete Reserves and Map 2024